By the end of this summer, Protolabs customers will benefit from large format metal 3D printed parts produced on GE Additive Concept Laser X Line 2000R machine.
With a build volume of 31.5 in. x 15.7 in. x 19.7 in. (800mm x 400mm x 500mm), metal parts produced on this DMLM (direct metal laser melting) machine can be produced in a single piece.
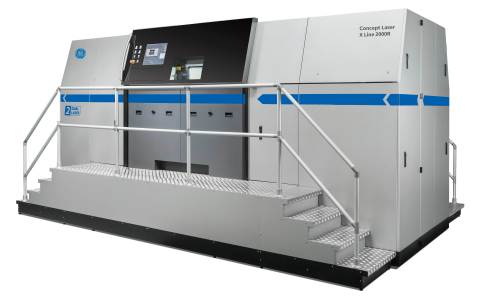
“Our customers, especially in the aerospace industry, have told us they need the ability to create larger parts with complex geometries,” said Vicki Holt, president and CEO at Protolabs. “Through our partnership with GE Additive, we are responding by scaling up use of its cutting-edge equipment to further support our customers’ metal production needs.”
At the technical level, the dual 1000W lasers of the 3D printer make it an ideal candidate to achieve serialized production volumes. Furthermore, its two build modules enable the operator to save time by allowing one build to take place while another is being set-up.
At the beginning, the contract manufacturer will first utilize Inconel 718 for the rapid production of aerospace parts. Acknowledged for its high strength and corrosion resistant properties, Inconel 718 has proven itself in the development of turbojet engines for aircraft, among a variety of other applications. The nickel-based heat resistant alloy has been added last year to Protolabs’s portoflio of Direct Metal Laser Sintering (DMLS) materials.
The material is more and more demanded by aerospace specialists as it was also the first material to be leveraged as part of the qualification process of Velo3D’s Sapphire by Honeywell Aerospace.
To date, Protolabs integrates four more GE Additive Concept Laser M2 printers, which can produce parts up to 9.8 in. x 9.8 in. x 13.8 in. (250mm x 250mm x 350mm). The company therefore counts more than 30 metal additive machines, all capable of producing AS9100-production parts.
As additive manufacturing machines now go hand in hand with post-processing, Protolabs has also invested in new equipment for this stage of manufacturing. The Additive Manufacturing Service provider has chosen Solukon’s powder removal system. Indeed, Solukon’s powder removal systems are increasingly acknowledged in the aerospace and space industries as “the batch number of aerospace parts perfectly matches with automated depowdering”, which makes it easy to remove trapped powder from internal cavities and complex geometries.
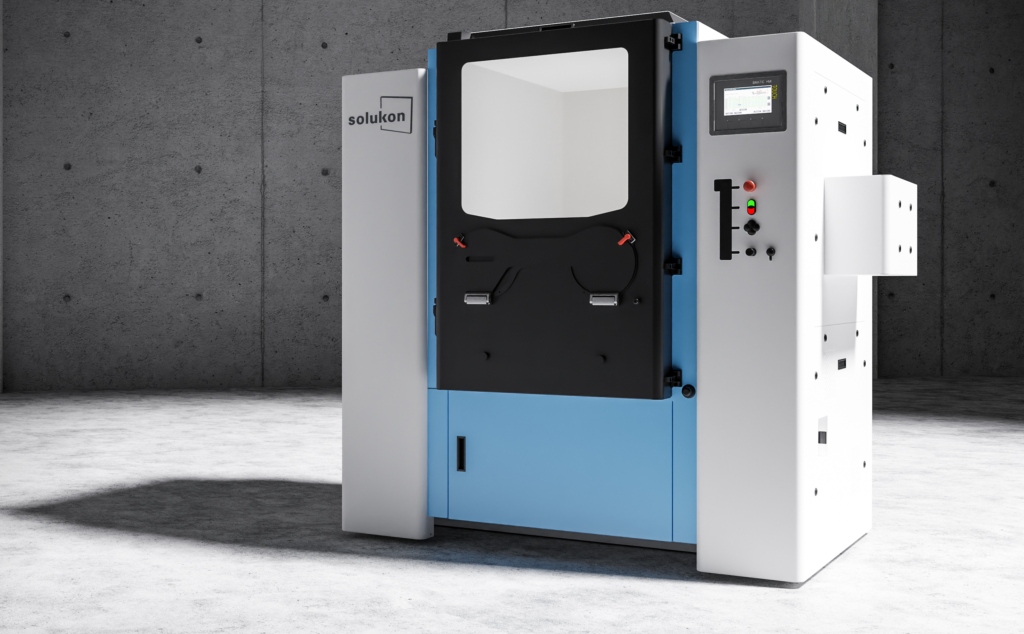
Last but not least, a new Ipsen vacuum heat-treat furnace will enable more in-house heat treatment. This will improve the consistency of mechanical properties of manufactured parts.
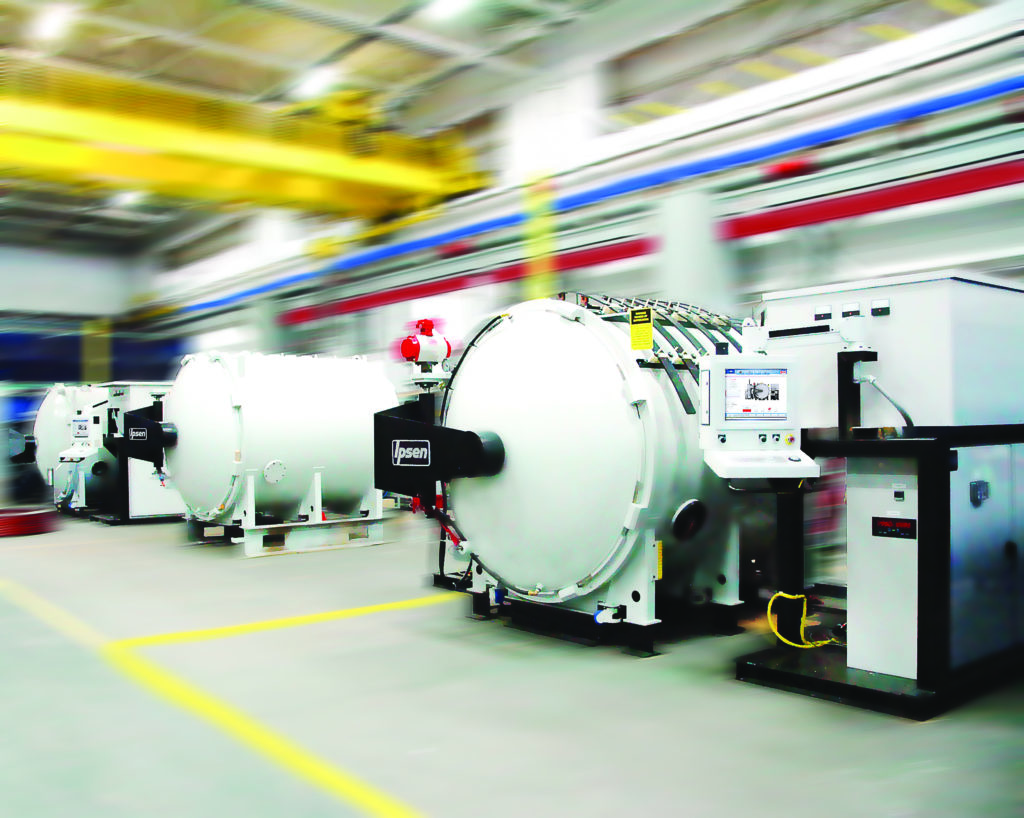
Remember, you can post free of charge job opportunities in the AM Industry on 3D ADEPT Media or look for a job via our job board. Make sure to follow us on our social networks and subscribe to our weekly newsletter : Facebook, Twitter, LinkedIn & Instagram ! If you want to be featured in the next issue of our digital magazine or if you hear a story that needs to be heard, make sure to send it to contact@3dadept.com