Autodesk’s Netfabb will soon make its generative design accessible to the 3D printing industry with a new software tool.
The generative design aims at helping the engineer/designer to discover a wide range of functional and manufacturing design options. It consists in using algorithms based on machine learning and advanced simulation to obtain smart design solutions.
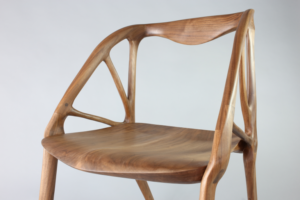
The user sets goals regarding size, weight, strength, style, materials, cost, and any number of other criteria. Thereafter, he/she makes use of cloud computing to create as many solutions as possible.
Stanley Black & Decker experienced the super power of generative design
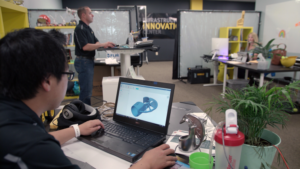
Through a pilot project, the Innovation group aims at making a hydraulic crimper better (better = lighter). Used about a hundred times in a work shift, a normal crimper weighs 15.4lbs (6,98 kg).
Simulations demonstrate the tool maintained its original strength features. Furthermore, Netfabb users can create an additive manufacturing strategy to make a new attachment.
By using generative design and additive manufacturing technologies, the Breakthrough Innovation team was able to shave more than three pounds off the crimping tool attachment, reducing the weight by more than 60%.
When Frank DeSantis, Vice President of the Breakthrough Innovation group, was asked his feelings, he declares:
“The generative design capabilities we can access with Netfabb are almost magical. It’s not brute force engineering. It’s elegant. You define a problem and you get a solution set unlike anything you’d predict. The results of the wire crimper project ensure we’re going to be applying the incredible combination of generative design and additive manufacturing that Netfabb offers to an array of other products we have in development. This is clearly the future and that’s what our Breakthrough Innovation group is all about.”
//pagead2.googlesyndication.com/pagead/js/adsbygoogle.js
(adsbygoogle = window.adsbygoogle || []).push({});