Arash Motor Company, un constructeur britannique d’hypercars et de voitures de sport, utilise l’impression 3D dans le cycle de développement de son véhicule de prochaine génération.
Dirigée par Arash Farboud, fondateur et concepteur principal, l’entreprise est reconnue pour ses voitures de sport, légères et très puissantes, telles que la voiture de sport AF8 Cassini et l’hybride électrique-essence AF10. Avec une production à faible volume, Farboud peut offrir à chaque conducteur une expérience de conduite holistique et l’un des outils de production forts qui aident à réaliser cette vision est l’impression 3D.
Le designer utilise l’impression 3D depuis plusieurs années déjà. Si nous ne connaissons pas toutes les technologies dont il dispose en interne, nous savons qu’il est un défenseur de la technologie MakerBot, puisque les imprimantes 3D MakerBot Replicator 2, Replicator Z18 et METHOD X sont utiliséEs pour divers projets qu’il a réalisés.
D’autre part, la présence de la technologie de MakerBot dans cette installation automobile n’est pas si surprenante quand on connaît les diverses applications que cette technologie a permis de réaliser au milieu de nulle part, ou même pour des marques automobiles et de style de vie de luxe.
Dans ce cas précis, Farboud et son équipe ont utilisé les trois imprimantes 3D MakerBot pour toute une série d’applications destinées au dernier projet d’hypercar électrique de la société. Construite dans un souci de performance ultime, la nouvelle hypercar est équipée d’une cartouche de moteur en carbone, de plusieurs moteurs électriques, d’un pack de batteries avancé et d’un design aérodynamique élégant.
Le processus de fabrication
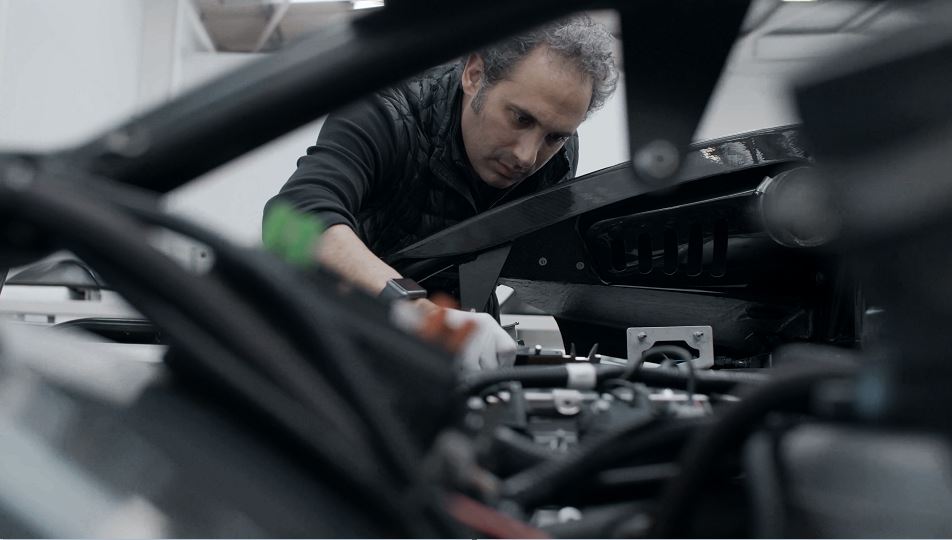
Tout d’abord, il convient de noter que leur première voie de fabrication nécessitait de passer par le processus long et fastidieux du prototypage avec de l’aluminium – de la fabrication, du pliage, du soudage, du façonnage, etc.
« La quantité de ressources nécessaires pour effectuer ces étapes est éprouvante. Une fois que vous disposez d’une imprimante 3D pour éliminer une grande partie de ces étapes, alors vous permettez à vos ressources d’être utilisées sur des choses qui comptent vraiment pour vous », explique le fondateur.
L’équipe a donc commencé par un modèle à l’échelle réelle produit à l’aide de la Replicator 2, puis a commencé à concevoir la structure complexe du châssis et la structure aérodynamique à l’aide de la Replicator Z18. Cela comprenait de nouvelles techniques telles que la conception de la suspension et des ailes, la vérification des suspensions à triangles, le montage des moyeux et du verrouillage central, et des modèles réduits pour montrer les pièces structurelles.
En utilisant une gamme de matériaux sur la MakerBot METHOD X, y compris la fibre de carbone MakerBot Nylon et l’ABS, l’équipe a imprimé en 3D des pièces de production à utiliser directement sur le véhicule. Le METHOD X a produit des pièces sous une forme réelle, ce qui a permis à l’équipe d’utiliser les pièces pour des tests de résistance, des supports, des engrenages et d’autres composants pour la voiture.
L’hypercar comporte de nombreuses pièces complexes à l’intérieur, comme l’aile arrière et l’aile inférieure arrière, et l’équipe a donc dû trouver un moyen de réduire le poids de l’usinage de l’aluminium. Pour ce faire, ils ont plutôt utilisé des pièces en carbone nylon imprimées en 3D.
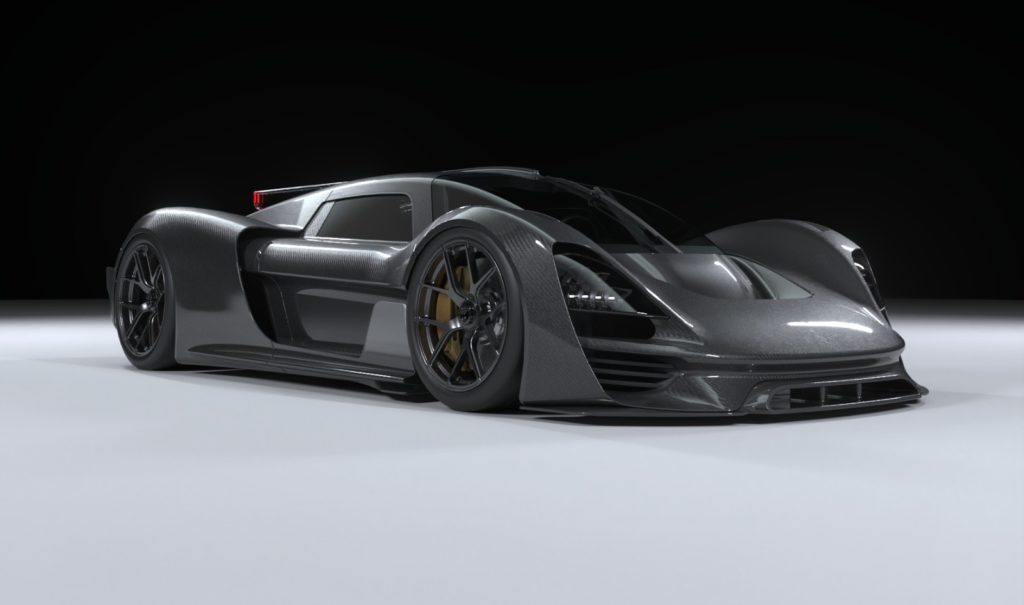
« Nous utilisons beaucoup de supports, de points d’ancrage et de points de fixation autour de la voiture en fibre de carbone nylon imprimée en 3D. Nous utilisons également beaucoup de structures intérieures en ABS et en fibre de carbone nylon parce que c’est plus rapide et plus facile à fabriquer. Nous essayons d’obtenir 95+% de la voiture dans un matériau composite pour être encore plus performants, et nous essayons également de réduire la complexité de la fabrication à l’impression 3D. Nous nous concentrons uniquement sur les pièces qui comptent vraiment dans la fabrication en composite – châssis, panneaux de carrosserie, certaines structures intérieures. Nous déqualifions une grande partie des processus à certains égards et nous nous perfectionnons à d’autres égards pour la complexité et la précision« , a déclaré Farboud.
L’équipe avait l’habitude d’envoyer les pièces pour qu’elles soient usinées localement ou à l’étranger, ce qui était coûteux et prenait du temps. Mais désormais, elle peut envoyer sa conception CAO directement à la MÉTHODE X pour fabriquer une pièce, la vérifier et la tester.
« L’impression 3D en interne signifie également que vous pouvez faire les choses rapidement, immédiatement et au coût le plus bas possible. Cela signifie que vous êtes en mesure d’expérimenter sans trop de crainte et d’inquiétude quant aux dépenses. Vous ne dépensez de l’argent que pour votre filament et votre temps, ce qui vous permet d’essayer des choses sans crainte« , poursuit-il.
Avec trois conceptions, de l’esquisse à la modélisation à l’échelle, en passant par la modélisation CAO, les accessoires, l’entretien et les intérieurs, l’équipe a pu raccourcir ses délais, qui peuvent atteindre plusieurs années, à 12 mois. À partir de là, elle a pu créer quelques prototypes et véhicules d’essai, avant de passer à la production complète.
« La série d’imprimantes 3D MakerBot réduit le temps entre un fichier sur l’écran de l’ordinateur, le prototypage et la vérification du toucher et de la sensation. C’est un élément important. Il arrive que l’on rate un trou ou une fixation, mais on peut le faire sur un modèle CAO. Ensuite, une fois qu’il est imprimé, vous pouvez le vérifier physiquement. La METHOD X a l’avantage d’avoir une chambre chauffée, ce qui est essentiel pour nous car cela permet une précision dimensionnelle. Pendant la fabrication de la pièce, la base ne bouge pas et il n’y a pas de déformation. Cela permet une grande précision pour une imprimante 3D aux normes actuelles. Nous avons effectué plusieurs tests et elle s’est avérée très précise à chaque fois« , conclut Farboud.
N’oubliez pas que vous pouvez poster gratuitement les offres d’emploi de l’industrie de la FA sur 3D ADEPT Media ou rechercher un emploi via notre tableau d’offres d’emploi. N’hésitez pas à nous suivre sur nos réseaux sociaux et à vous inscrire à notre newsletter hebdomadaire : Facebook, Twitter, LinkedIn & Instagram !