Imagine ultra-lightweight components that are as strong as a reinforced concrete column.
Bugatti just gave us another reason to keep an eye on automotive innovations made possible using additive manufacturing.
VW’s hypercar brand recently releases further manufacturing details about their new Bolide, and it turns out that it reaches a new milestone in the manufacturing of a pivotal component.
Where it all started
Three years ago, the whole manufacturing industry remained speechless when the car manufacturer showed off the largest eight-piston titanium brake calipers 3D-printed for the Chiron, which measure 12.2-inches by more than eight inches (that translates to 30 cm by more than 20 cm).
Since then, the engineering team at Bugatti keeps experimenting new ideas to push the boundaries of this solution. Today, the technological concept of the Bugatti Bolide aims to answer a single question: “what if they built a radically light vehicle around its iconic 8.0-litre W16 engine?”
As part of his master’s thesis on a calculation methodology for the 3D-printed titanium brake caliper, Henrik Hoppe, a doctoral student who leads the selective laser melting project at Bugatti’s new technologies department worked on the manufacturing of both stiff and strong parts for the car.
“Through the process known as selective laser melting, commonly known as 3D printing, new, hollow, ultracomplex components that are stiffened from the inside can be produced which are very lightweight and yet extremely rigid and strong. We are utilising these benefits for an increasing number of components in our hyper sports cars,” explains Hoppe.
In his doctoral thesis, the industrial engineer goes one step further. Hoppe is pioneering a new system, owing to the cost- and time-intensivity involved with the complete cycle of the manufacturing process chain, from concept to delivery. Hoppe uses this system to identify the commercial and technological potential of functional 3D-printed metal components for automotive manufacture, and can enhance this potential with applied targeting at specific parts. Previously, these types of components were used predominantly in the aerospace sector.
As part of this project, the luxury brand decided to apply principles from the field of bionics to give the printed components a bone-like structure. : featuring thin walls, a hollow interior, and fine branching. And this is precisely how the components obtain their remarkable rigidity despite their low weight – with wall thicknesses of up to just 0.4 millimetres.
The manufacturing of the pushrods
A number of specific parts, and especially suspension components like brackets and springs have been 3D printed in metal and optimized for the Bolide, but the components they really take pride in are the pushrods.
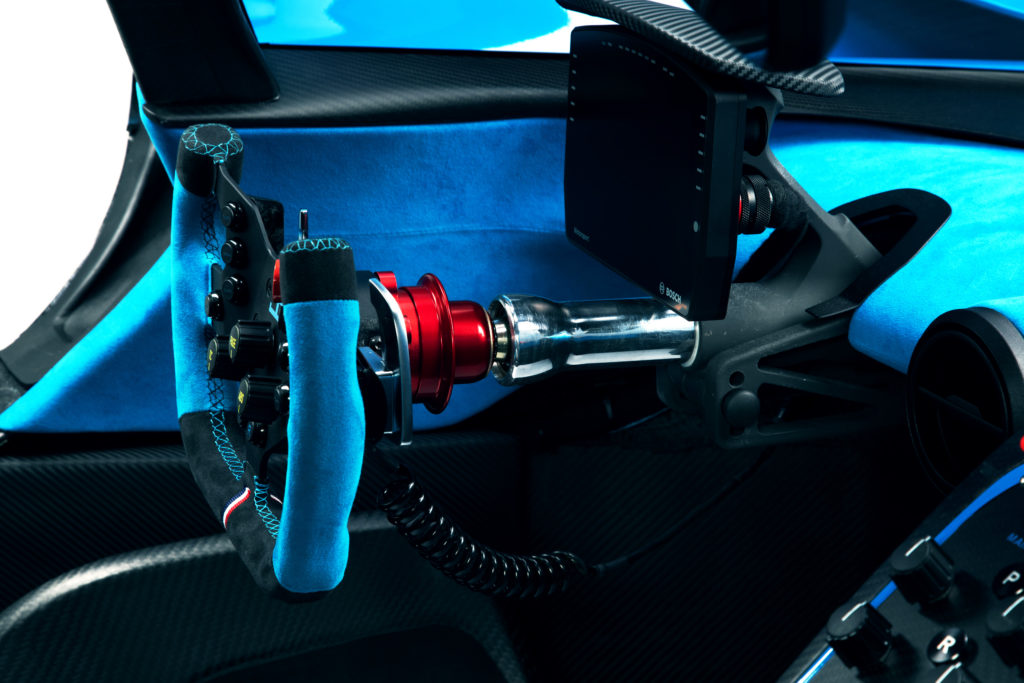
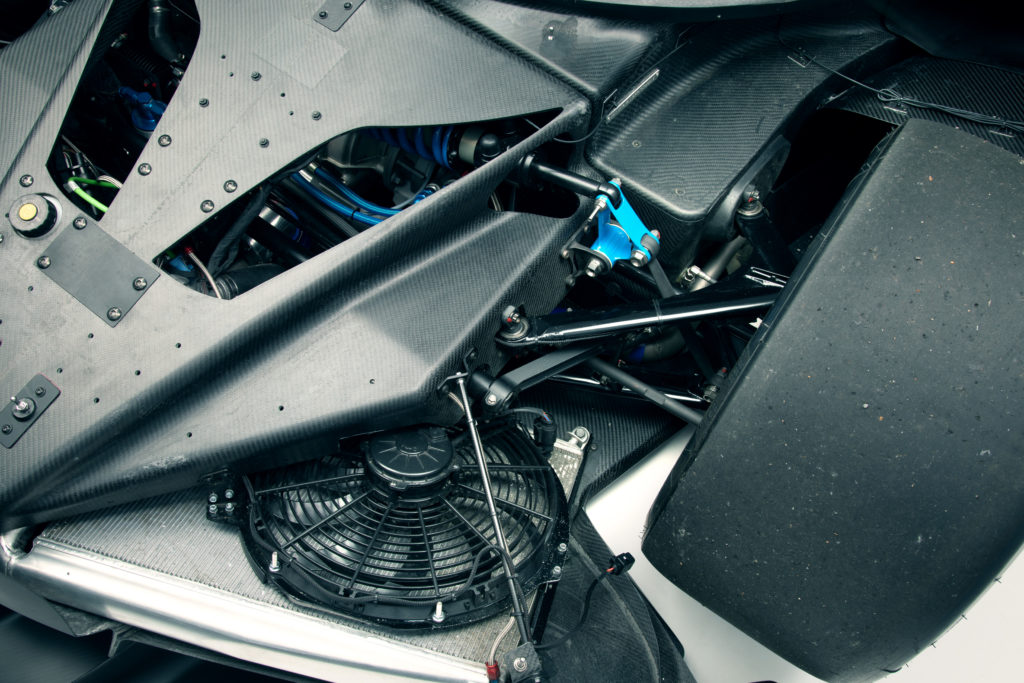
“They transfer a force into the rockers which, depending on the driving manoeuvre, is equivalent to a weight of up to 3.5 tonnes. Nevertheless, thanks to the implementation of multiple ideas, they only weigh as much as a bar of chocolate, in other words 100 grams each,” explains Henrik Hoppe. For the first time, the Bugatti developers varied the wall thickness of the thin-walled, hollow rods. They become thicker towards the centre and then thinner again, meaning that they are optimally adapted to localised stress. Similar to a human bone, the component has an internal structure. This special structure was also recently registered as a patent.
The manufacturing of the tailpipe trim cover
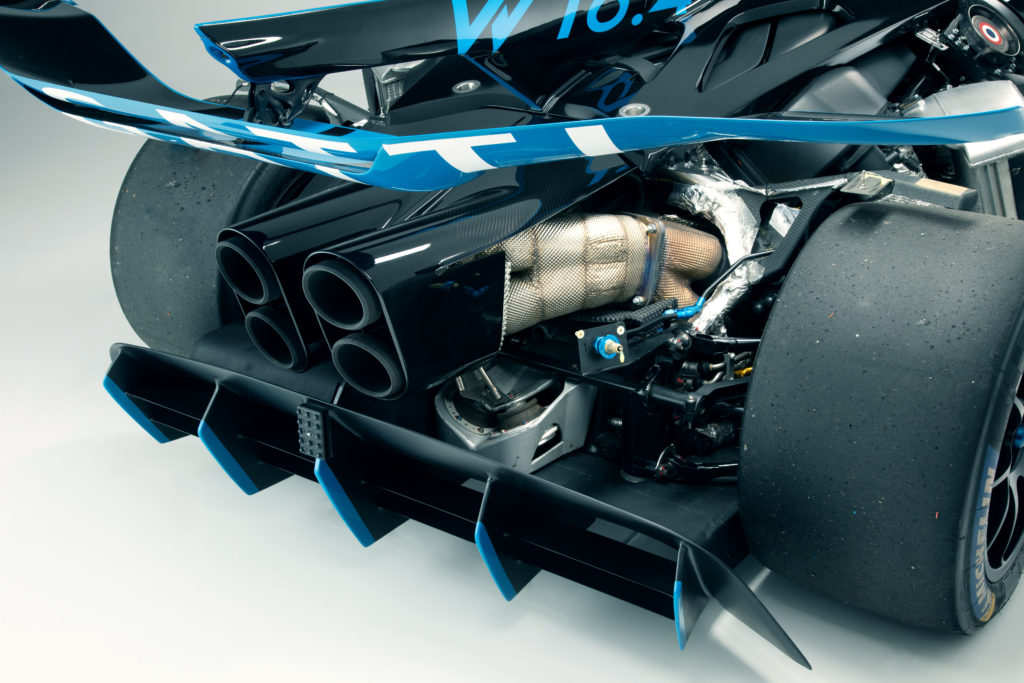
In the tailpipe trim cover, a hybrid component made of 3D-printed titanium and ceramic, Bugatti reduced the weight by around half compared to the already weight-optimised titanium tailpipe trim covers well known from series production. The component, which measures more than 280 millimetres in length and has a consistent wall thickness of just 0.5 millimetres, therefore weighs less than 750 grams.
Since ceramic material is a significantly less effective heat conductor than titanium, Bugatti introduced special ceramic elements that are built into the titanium housing and centre the cover with respect to the carbon outer skin, so that the outer skin is not damaged even at high exhaust gas temperatures.
This thermal shield is also supported by a built-in Venturi nozzle: when hot exhaust gas enters the tailpipe trim cover, fresh air is drawn in, thereby creating a jacket of cool air around the hot exhaust gas flow. In its entirety, this is an invention for which Bugatti has submitted a patent application.
Finally?
Although it is named “a road-ready extract”, it should be noted that the real Bolide drives, but it’s hard to determine how far the manufacturer would push it outside the digital space.
In the meantime, the experimental study of the Bugatti Bolide shows that the hyper sports vehicle features a W16 engine derived from series production as powertrain combined with a minimal body for maximum downforce. It therefore promises to offer the ultimate Bugatti performance kick. (8.0-litre W16 engine, with up to 1,850 PS˚ and a car that theoretically 1,240 kilograms, which translated to a weight-to-power ratio of 0.67 kg/PS, a top speed of over 500 km/h).
According to Frank Götzke, Head of New Technologies at Bugatti, these can also be transferred to production vehicles. Although this might raise speculations, while looking at the Bolide, we are ready to take his word for it.
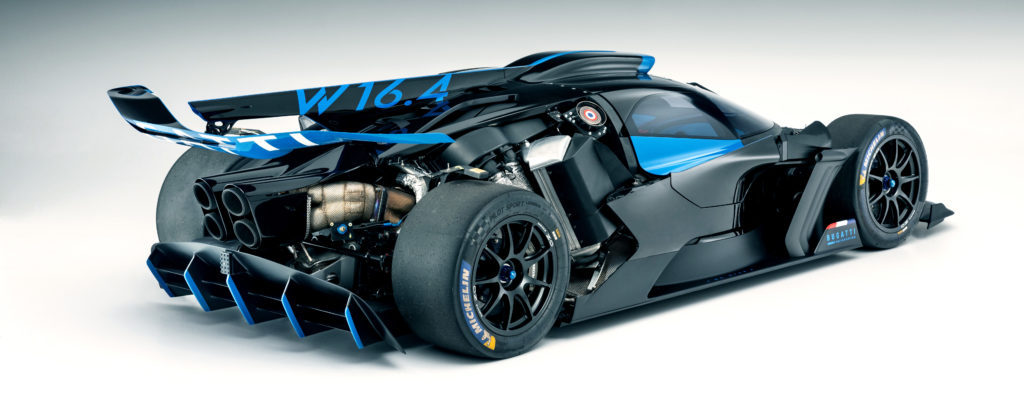
Remember, you can post free of charge job opportunities in the AM Industry on 3D ADEPT Media or look for a job via our job board. Make sure to follow us on our social networks and subscribe to our weekly newsletter : Facebook, Twitter, LinkedIn & Instagram ! If you want to be featured in the next issue of our digital magazine or if you hear a story that needs to be heard, make sure to send it to contact@3dadept.com