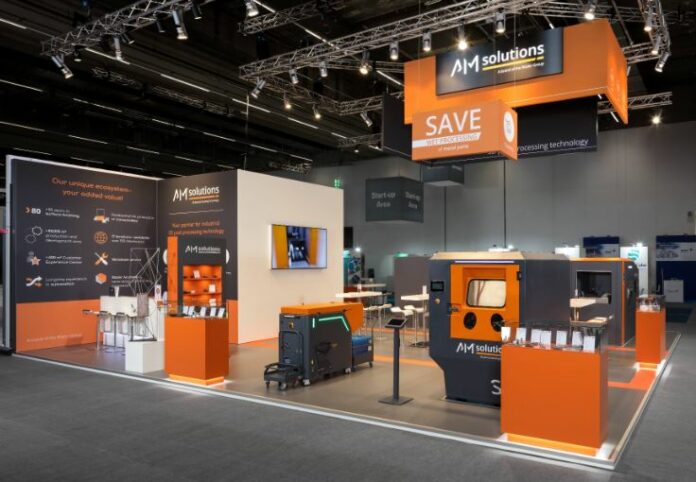
Automation drives innovation in the 3D printing industry and the post-processing company AM Solutions – which is part of the Rösler Oberflächentechnik GmbH – is showing how the latest advancements in automated post-processing can make this industry more cost-efficient, allowing high volumes of 3D printed parts production at Formnext 2023.
As you may know, Formnext, is an international platform where the who’s who of the AM industry unite to showcase their potential and AM Solutions will be there at stand D59 in hall 12.0.
AM Solutions will showcase its new C2 automated post-processing system at this year’s Formnext event along with the already-used automated post-processing systems S1, S2, S1 Wet and C1. The company has improved the C1 system launched last year.
While the S1 automated post-processing AM system is pitted as the most cost-efficient and productive 2-in-1 system for surface finishing 3D polymer parts, S1 Wet is a wet blasting solution for surface finishing 3D printed metal parts.
The S2 automated post-processing system, on the other hand, is for surface finishing of high-volume 3D printed plastic parts. The C1 system with its improved thermal and mechanical effects removes any support/resin from photopolymers at a faster rate and more efficiently than currently available machines on the market.
The C2 automated post-processing system of AM Solutions is also a 2-in-1 process that lets the chemical smoothing and the dyeing step of 3D printed plastic parts happen in one step.
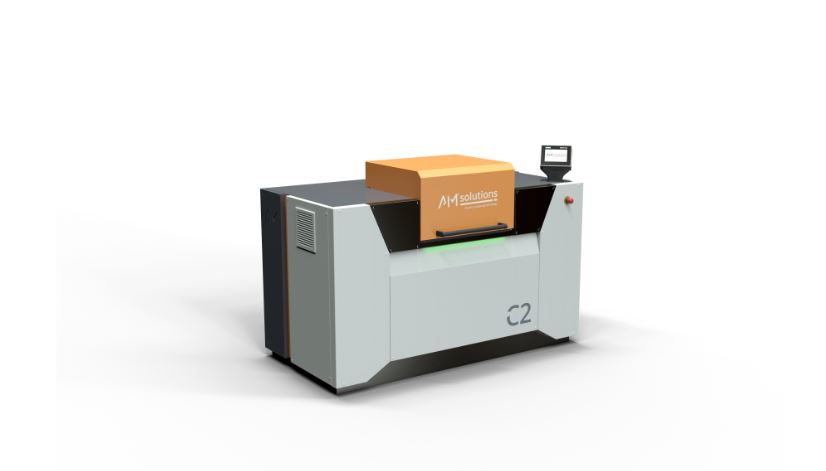
According to David Soldan, the Head of AM Solutions, the company is determined to increase the production of 3D printed parts with the new improved 2-in-1 solutions in automated 3D printing as it can simultaneously run two post-processing steps in a single machine.
Soldan further elaborated on how this “higher degree of automation” streamlines the entire chain of production and reduces the per-piece cost.
“Such an approach allows us to perfectly fulfill the requirements of customers who are looking for high-volume production with 3D printing technologies. One good example is the Italian job shop company Weerg. With the S1 system, this company saved not only money by not having to invest in additional equipment but also saved valuable manufacturing space. Above all, the processing time for 3D-printed parts could be reduced by over 60%. In the past, most of the post-processing of delicate, large and geometrically complex components had to be done manually. Thanks to the S1 system, these manual operations could be drastically reduced. The share of mechanically processed components increased from 60 to 90%. These impressive statistics show that with our unique technological approach, we are on the right path and can consistently assist our customers in meeting the additive manufacturing challenges they are facing every day”, said David Soldan.
Soldan explained how the C2 automated post-processing system added “substantial value” to the existing post-processing system and will help customers in streamlining the production chain.
“We have taken enough time to develop the best possible process for our customers and make sure that the C2 is productive, cost-efficient, has a small footprint and consistently produces high-quality results”, said Soldan.
The C2 system also has a compact M4 which provides better surface finishing including grinding, smoothing and polishing of small to midsize 3D printed metal and plastic parts. It operates in a plug-and-play principle, bypassing the time-consuming assembly on site. The C2 system has the processing unit and the process water treatment combined in one system for optimum ease of operation including machine control. With the help of the system’s integrated water cleaning and recycling system along with the cleaning centrifuge which is compatible with both dirty and clean water tanks, one can do post-processing without any wastewater connection or freshwater addition. The water recycling aspect of M4 makes it more eco-friendly and cost-effective.
Remember, you can post job opportunities in the AM Industry on 3D ADEPT Media free of charge or look for a job via our job board. Make sure to follow us on our social networks and subscribe to our weekly newsletter: Facebook, Twitter, LinkedIn & Instagram! If you want to be featured in the next issue of our digital magazine or if you hear a story that needs to be heard, make sure to send it to contact@3dadept.com