Two years ago, when we first sat down with industry insiders from Oak Ridge National Laboratory and Burloak Technologies to discuss the use of Additive Manufacturing in the nuclear industry (Additive Talks, season 2, episode 4), the market was still very nascent (- the very first use cases being recorded in 2017). Opinions were very divergent and the pragmatic use of AM was still limited to a few materials and processes as well as to a few applications.
Today, AM is going nuclear, and as this sector is increasingly seen as a potential solution to CO2 reduction in energy generation, it is crucial to keep track of what’s happening in this specific field.
With a key focus on the practical use of AM across nuclear plants, the next Additive Talks session will gather industry experts who have already made AM a key strength within their operations. Unlike the very first panel that was a bit theoretical, the upcoming Additive Talks session aims to provide insights into hidden complexities when using AM across nuclear power plants.
Set to take place on Thursday, June 13th from 3:30 pm to 4:30 pm Central European Time (9:30 am to 10:30 am New York Time), it will gather:
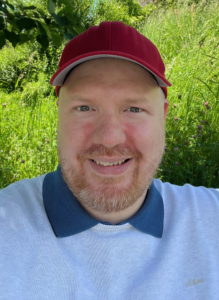
Benjamin Regener, Team Head, Project & Innovation Leader and Subject Matter Expert at the nuclear power plant Kernkraftwerk Leibstadt AG. Regener is a hands-on innovator in the nuclear energy sector. His deep expertise in integrating diverse technological fields, such as advanced manufacturing, robotics, automation, sensors, IT/OT integration, system health monitoring, calculation, simulation, and more, is a result of his extensive hands-on experience.
Kernkraftwerk Leibstadt AG (KKL) plays a vital role in Switzerland’s energy mix with high significance of nuclear power. Operational since 1984, KKL is Switzerland’s largest power plant with a net capacity of 1,233 MWe, supplying electricity to approximately two million households and contributing about one-third of the country’s nuclear power. Regener has built and led both small, focused teams on-site and coordinated large-scale project teams involving external contractors across various disciplines worldwide, using cutting-edge solutions such as Additive Manufacturing.
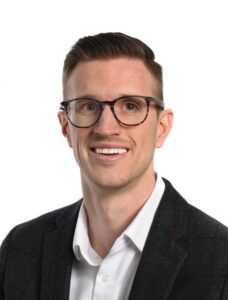
Adam Travis is the other innovator you will hear around this virtual table. The Global AM Program Leader at Westinghouse Electric Company runs the Westinghouse Additive Manufacturing Center of Excellence. In his role, he combines his experience in AM materials, powders, processing, and supply chain to set and execute Westinghouse’s global AM strategy and get qualified parts into serial production. He has worked in the AM industry for 10 years, developing a passion for leveraging AM to enable novel applications. In that time, he’s led AM R&D and operations, developed new alloys, commercialized new products, and built out the Digital Thread.
Westinghouse Electric Company is shaping the future of carbon-free energy by providing safe, innovative nuclear and other clean power technologies and services globally. The company supplied the world’s first commercial pressurized water reactor in 1957 and its technology is the basis for nearly one-half of the world’s operating nuclear plants. Over 135 years of innovation make Westinghouse the preferred partner for advanced technologies covering the complete nuclear energy life cycle.
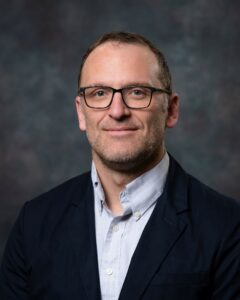
Dr. Ryan Dehoff, Director of the Manufacturing Demonstration Facility at Oak Ridge National Laboratory and the Technical Area Lead for Advanced Manufacturing under the Nuclear Energy AMMT Program. His focus of research includes understanding correlations between process conditions of advanced manufacturing processes materials microstructure and mechanical performance. His research expertise lies in the field of Additive Manufacturing with a particular focus on metals and alloys. He has worked on multiple additive manufacturing technologies including electron beam and laser powder bed, large-scale directed energy deposition technology, and solid state-based AM processes. He is working to integrate the digital thread into manufacturing for the certification and qualification of advanced manufactured components. His work at ORNL has been instrumental in pushing the boundaries of additive manufacturing, particularly in metal additive manufacturing, where he has developed innovative techniques to improve the properties, performance, and scalability of printed materials.
Nuclear energy found a home at ORNL 80 years ago and never left. The premier research institution represents nearly 250 researchers and scientists from across the globe, focused on delivering nuclear science and technology breakthroughs. The Nuclear Energy and Fuel Cycle Division is the heart of ORNL’s nuclear energy research capacity—and a haven for big thinkers, international expertise, and technical prowess. As it refines concepts and components to extend the life of current nuclear plants, ORNL pioneers advanced reactor concepts and explores novel energy conversion methods. Its approach incorporates all aspects of the fuel cycle, from fuel development and transportation to reprocessing, waste reduction, and secure fuel storage.
Does this look like a conversation that you do not want to miss?