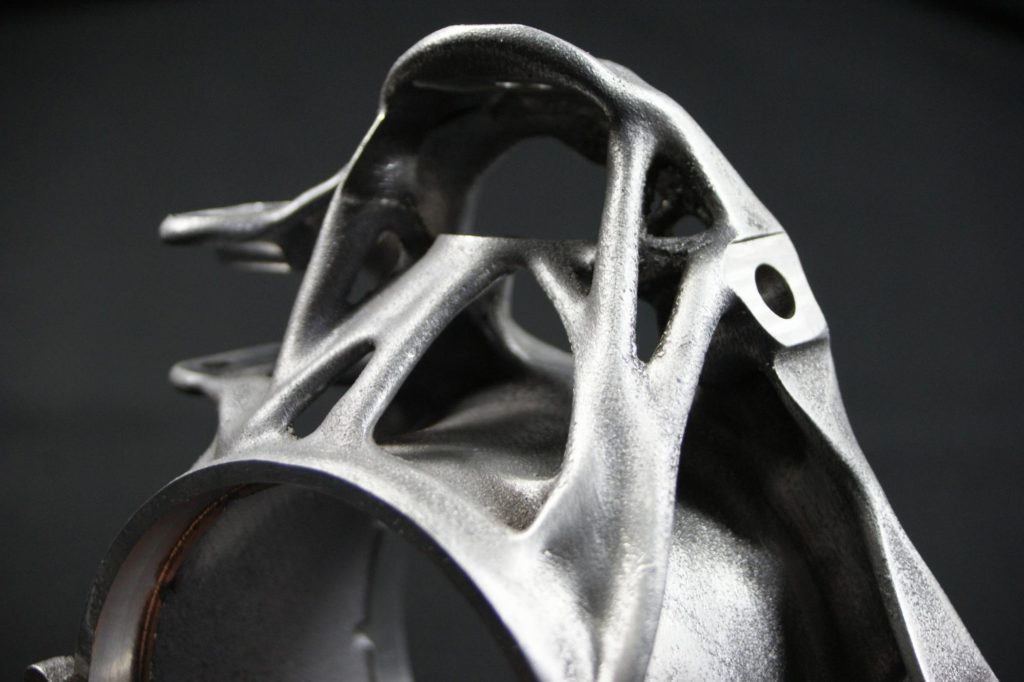
As manufacturers more and more recognize additive manufacturing (AM) as a viable production alternative, they find themselves facing new challenges in informatics or systems integration. Every day, operators answer and raise several questions related to platforms interoperability. Today, we seize the opportunity to complement existing efforts in current digital solutions. Experts from Authentise, AMendate and Volume Graphics share their expertise in this topic.
Interoperability refers to the ability of computer systems or software to exchange and make use of information. In other terms, different manufacturers can connect their devices in order to leverage specific data for a given process. In a manufacturing process, designers need to master several things to design the part in the right way. In additive manufacturing especially, the design process is quite different from other manufacturing methods. That’s why we first need to understand, what additive manufacturing interoperability is; at least at what level, one can talk about interoperability in an additive manufacturing process.
Philip Sperling, Product manager Additive Manufacturing at Volume Graphics defines interoperability in AM as “the connection between different hardware and software components of the AM process chain.” “If you are looking at the complete AM process chain, e.g., for the powder bed fusion technologies, you will find a lot of equipment and software necessary to get to the finished part”, adds Philip Sterling.
In this vein, issues related to platform interoperability can be observed from and between design, manufacture, and post-process. An assertion that Dr Thomas Reiher, CEO and Co-Founder of AMendate GmbH confirms:
“Additive Manufacturing (AM) enables a digital process chain and thus fosters smart manufacturing. To be successful, the interoperability of AM is a fundamental factor. Consequently, the digital creation process has to be combined with actual manufacturing. There has to be an integrated process from and between design, manufacture, and post-processing.”
For Andre Wegner, Founder & CEO at Authentise, we speak most frequently about interoperability of data. For example, interoperability of design files, interoperability of machine data, etc. However, as we have seen in the literal definition, he laid emphasis on the fact that the term goes beyond the software level and can be studied in other fields.
Interoperability at the software level: Dependencies and related standards
Andre Wegner said that we mostly speak about interoperability of data. Several cases can describe dependencies that might explain the need for an interoperability process in a manufacturing environment.

The use of new features in software
Data interoperability between CAD systems remains a significant hurdle in information integration and exchange in a collaborative engineering environment. The use of CAD data exchange standards causes the loss of design intent such as construction history, features, parameters and constraints.
Such hurdle often results from the migration of some functions generally found in AM specific software to CAD software. Those functions might be “part placement in the build environment, design of support structures, or setting a build orientation.”
These functions are still a part of the AM process, but eventually will become a CAD design function. So, CAD software companies now develop those capabilities or integrate existing AM software into their software. “There is a need to capture the information associated with those functions in a [single] file for interoperability and long-term archiving and retrieval.”
The use of several tools/ software during the design process
While the first dependency laid emphasis on the confusion created by the migration of specific features into a given software, another dependency might occur during the design process of complex parts. This dependency occurs when the design of a part requires the use of different software solutions.
“For highly complex parts, you have to make a lot of considerations when designing your part regarding the function and how to make it “printable”. During this process, you have to use different software solutions that cover single design steps, e.g., the topology optimization, the lattice design, positioning of support structures, force and build simulation, as well as build preparation. These different solutions may not integrate properly to convey original design intent”, explains Volume Graphics Product Manager Additive Manufacturing.
The integration of AM has certainly the potential to reduce time and cost during the production process. However, “it’s currently still too cumbersome to move a part from idea through design, through manufacturing preparation and production. Multiple tools are involved [and] interoperability allows us to reduce the number of tools, the number of steps and effort required”, adds the founder & CEO of Authentise.
In this specific case though, manufacturers still have a long way to go before reaching stable compatibility between all processes. For AMendate GmbH’s CEO, the understanding of the issue seems clear in theory but, in practice, “continuous and thorough integration is usually more difficult than expected to implement and many small details cause major problems. However, compatibility [between solutions] is only really interesting and seamless if we also embrace the physical level of production and post-processing. On the one hand, data must arrive at the machine entirely and correctly and [must] be processed. On the other hand, though, it is also important to ensure that findings from production flow back into the software. When we have a constant flow of information back here and [when we will] continuously adapt and align the software [for] production, we will have a stable compatibility in the future.
Nowadays, compatibility is more important than ever. Intensive cooperation takes place at various levels. Data, processes and products must be exchanged efficiently to carry out this cooperation effectively and quickly. Compatibility is the lubricant of a well-functioning system. [A few years ago, the improvements were not as significant as expected on the compatibility of different machines, software and companies]. Nowadays, in terms of Industry 4.0 and smart factory, this is a significant advancement. Companies such as Hexagon are working on a broad basis for interoperability of software and machines and thus guide the engineers in their daily business.”
The ideal way to have interoperable manufacturing
Today, we do not question the importance of interoperable manufacturing anymore. Its importance seems justified, especially in a manufacturing environment that is increasingly digitalized, and that frequently requires new tools to achieve complex tasks.
We question its real feasibility because so far, operators still seem to face a range of challenges that seem difficult to explain when delving into technical aspects of the manufacturing process.
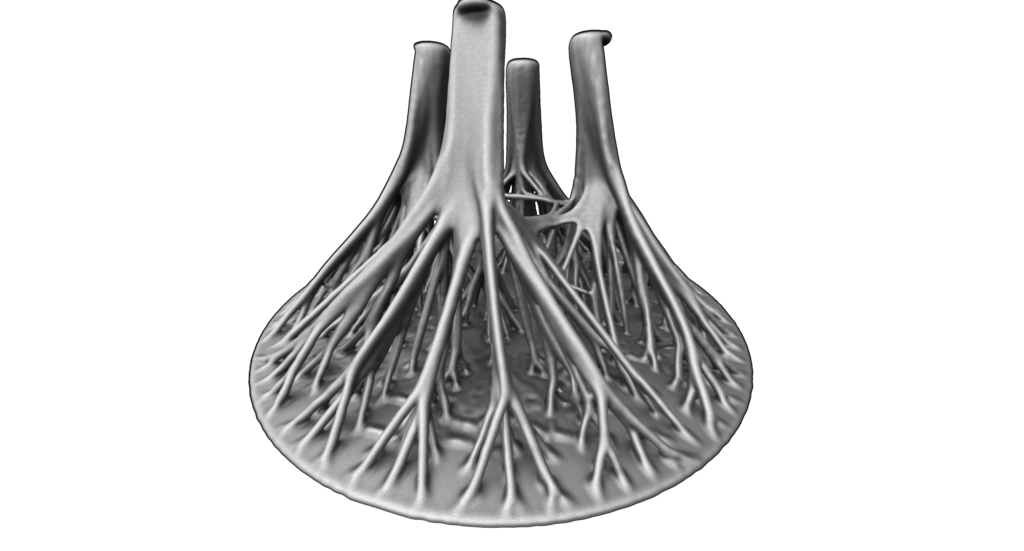
In the range of possible solutions that we can explore, experts share their opinion on the idea:
From our analysis, Authentise and Volume Graphics would obtain the “same result” at the end of a given manufacturing process using “almost different approaches”:
While Authentise’ Andre Wegner uses the words “Open Standards” to talk about the ideal way to reach interoperable manufacturing, Philip Sterling, on the other hand, talks about “a standardized, scalable file format for AM that enables interoperability through all the different process steps—design, printing, post processing, and inspection.”
Andre Wegner first explains his point:
“In the absence of open standards for machine data (or, rather, standards still being established), Authentise is working on interoperability by providing a connector to different machine data types. Currently, Authentise already integrates data from HP, EOS, SLM, Carbon, Stratasys, 3D Systems and many others.

In addition, Authentise’s open, modular infrastructure allows integration into existing IT systems as well as the integration of 3rd party modules, such as mesh healing and support algorithms. This means that users no longer have to interface with different systems, but can manage the pre-production processing for various machines in one, seamless interface.
Finally, the integrations Authentise has built into other 3rd party systems enable further interoperability. One example is the integration with Autodesk Netfabb, which allows users to switch seamlessly between CAD and production planning. Another example is our integration with Microsoft Flows, which enables additive interoperability between hundreds of different online services to empower operators to create their workflows.”
Philip Sterling clarifies his assertion:

“Since users have to work with different programs, they also have to work with different file formats and interfaces with many constraints between them – not to mention the added challenges of varying interfaces and workflows, and even interpretation of data and results.
As we are offering [a] software solution [that analyzes] industrial CT data sets, we get a lot of requests from the Additive Manufacturing industry. Sometimes we encounter some of the consequences of missing interoperability as users send us different files for the nominal-actual comparison with CT data. We then receive single files for the part, the lattice design and the support structures—all of which makes our process for completing the analysis more complicated.
We try to make our customers’ lives easier by supporting a lot of data formats to import and export in our software solution.”

Dr Thomas Reiher, on the other hand, still lays emphasis on the “compatibility” argument:
“The lack of compatibility was one of the triggers for the foundation of our company. When optimizing components, the conventional process is characterized by the fact that different software solutions are necessary to achieve a result with a lot of manual work. Data exchange between these programs, however, led to information losses due to data conversions, [which] degraded data situation.
With AMendate these conversions are no longer necessary. The software integrates all relevant steps in one software and automates them. The result is a fully integrated, automated optimization process in which compatibility for previous and subsequent operations plays a crucial role.
This considerably simplifies the work process. In the next step, we are working on integrating Simufact’ s production simulation into our design process. Once this implemented, AMendate will foster the integration with other MSC products to enable a consistent data workflow with down- and upstream applications such as MSC Adams (multibody simulation), MSC Nastran (high detail FEM-Simulation) and CNC-machining.
In the end, our solution can be optimally leveraged directly on the selected machine, without any significant intermediate steps in a single, continuous digital chain.”
In a nutshell ?
AM interoperability focuses on simplifying the additive process and enabling an interoperable workflow. Its vision is to create a collective experience through a secure, intuitive tool that reduces design iterations and speeds up the time to print a good part, according to the design intent.
AM interoperability can happen in different situations: while using new software that integrates several tools, or while using several tools to achieve the design of a ready-to-print part. Furthermore, AM interoperability can be observed at different levels of the production process.
However, whatever the situation is, when we look at the experts’ points of view, we can see that even though the “final goal is the same”, roads that lead to it vary from one company to another.
A few words on the participating companies:
Founded by Andre Wegner, Authentise provides the additive manufacturing industry with process automation software. Its tool automatically monitors active prints and identifies Key Performance Indicators in the production environment.
AMendate aims to create a better way for optimizing parts. Founded by Thomas Reiher, Steffen Vogelsang, Anne Düchting & Gereon Deppe, the company has recently been acquired by Hexagon. AMendate’s strength relies on its ability to decrease time-to-print for Additive Manufacturing significantly.
Volume Graphics develops software for the analysis and visualization of industrial computed tomography (CT) data. The software company ensures quality control in AM using industrial computed tomography.