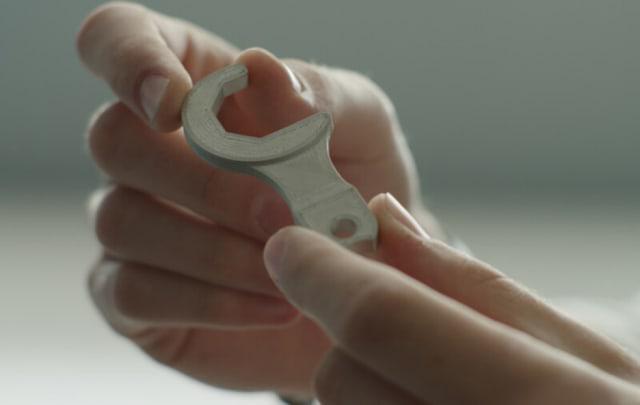
Overcoming global supply chain challenges, increasing production speed in metal 3D printing, and achieving new high performance parts in high-temperature thermoplastics reinforced with continuous fiber
Ever since they have unveiled their AI-powered software Blacksmith, the Markforged team has gone through a lot of changes. The machine manufacturer has signed a distribution partnership with Phillips Corporation and has made some changes to its management team. I have to say, that the updates that raise my interest the most are those achieved at the technical level: the new 3D printers, and software updates.
If you are a regular reader of 3D ADEPT Media, then you certainly know that the company headquartered in the US, develops metal and carbon fiber additive manufacturing platforms that are connected through its Digital Forge.
With the goal of addressing global supply chain challenges by producing parts where and when needed, the recent additions Markforged has added two new hardware and one software to its cloud-based platform: the Metal X Gen 2, Next Day Metal, and the X7 Field Edition.
Based on the development of the well-known Metal X System, the Metal X Gen 2 includes new features such as an external seven-inch touchscreen, door position sensors, and additional chamber insulation, all of them making metal printing easier, while saving energy and time.
Next Day Metal is the software option that completes the introduction of this new metal 3D printer. It aims to increase production speed of users and is compatible with the manufacturer’s entire global fleet of metal printers.
Markforged explains that the wash and dry times are now more accurate for smaller parts, shortening the required debind cycle time. These factors, combined with an approximately 17-hour small parts express run on the Sinter-2 post-processing oven, can give manufacturers the parts they need more quickly and — thanks to increased capacity on each printer — allows them to scale their additive manufacturing operation.
The X7 FE on the other hand, is a ruggedized, field-deployable industrial 3D printer for tactical response to inventory challenges in remote locations, as utilized by the U.S. Marine Corps XFAB program. The X7 FE is equipped with a rotomolded high-impact polyethylene Pelican case to protect it during transportation through harsh environments. The case contains all the tools, spare parts, and materials required for maintenance and repair operations in the field. Customers can drop the unit directly into harsh environments like combat zones and exploration sites and be printing in less than two minutes.
“Manufacturers are up against many challenges in today’s market — from supply chain challenges like rising supply costs and shipping delays to increased pressure from the market to innovate faster and stay ahead of the competition,” said Shai Terem, President and CEO of Markforged. “Since Markforged shipped our first printer, we’ve been committed to quality and continuous improvement, always looking for simpler, smarter, and more robust ways to empower our customers to build anything they can imagine. The addition of the Metal X (Gen 2), Next Day Metal, and the X7 FE to our Digital Forge are important steps towards reinventing manufacturing today so that we are all more resilient tomorrow anywhere in the world.”
Last but not least, given the fast pace at which the market advances, Markforged can’t legitimately improve its metal 3D printing portfolio without any considerations for its composites 3D printing portfolio.
In this vein, the manufacturer plans to unveil its latest 3D printer at Formnext. Named FX20, the 3D printer is described as the “most sophisticated 3D printer Markforged has ever produced”.
Designed to meet the needs of industries, such as aerospace, defense, automotive and oil & gas by printing high-strength, more accurate and higher performance parts, “the FX20 is a beast of a machine and represents our commitment to providing innovative solutions to our customers to empower them to build anything they can imagine. The addition of the FX20 to the Digital Forge strengthens our leading position in the additive manufacturing market by enabling the robust production of lightweight, advanced composite parts. With this combination of hardware and software, our customers will be able to count on Markforged for production of the end-use, mission critical parts that are required to overcome the limitations of traditional manufacturing. This builds resilient and sustainable supply chains that extend directly to the point-of-need,” said Shai Terem.
While many are expecting the first shipments of this FX20 in the first half of 2022, we can’t wait to see this new beast at the leading AM show of the year in November.
Remember, you can post job opportunities in the AM Industry on 3D ADEPT Media free of charge or look for a job via our job board. Make sure to follow us on our social networks and subscribe to our weekly newsletter : Facebook, Twitter, LinkedIn & Instagram ! If you want to be featured in the next issue of our digital magazine or if you hear a story that needs to be heard, make sure to send it to contact@3dadept.com