In the textile industry, dyeing is acknowledged as a pivotal process that provides colour to fabrics. In the additive manufacturing industry on the other hand, the ultimate goal remains the same: provide colour to ready-made 3D printed products but the technological process that enables to deliver these end-products is not always well depicted.
The truth is, for several decades, pot dyeing has been the standard for manufacturers who wanted to give a certain colour to parts. It requires the operator to have a basic pot, a textile dye and water. The textile dye is mixed with pre-heated water, and thereafter, the parts are immerged in the dyebath for a certain time. Despite its simplicity, the process started raising some concerns & questions:
- The fact that it is a manual operation means that operators often require more time and a lot of pots if they are dealing with a voluminous production batch, not to mention that this might lead in the end to a more expensive final product;
- Uncertain reproducibility. Complex geometries of parts, wall thicknesses or stirring tempo are some of the items that may affect the way dyes penetrate the 3D printed parts;
- What if the colour fades when exposed to UV light and heat?
- So far, we are yet to see a source that confirms that the textile dye used for pot dyeing is effectively appropriate for 3D printed parts. We haven’t seen any ISO certification yet that guarantees the safety of operators who use this process.
With a key focus on automated processes that have been certified by EU and US standards, this article aims to shed light on the different AM technologies where it can be leveraged, to describe the dyeing step of the post-processing stage, as well as a few examples of applications in the industry.
What AM technolog(y/ies) for dye colours?
Depending on the AM process leveraged and on the manufacturing goal of a given part, some post-processing tasks may be favoured over others.
As far as dyeing is concerned, the colouring process has always been considered as mostly problematic for parts manufactured via a sintering process (Selective Laser Sintering, Powder bed fusion). That’s why, 3D printed parts that have been produced via sintering are often mentioned as the main one that may require dyeing.
Associating dyeing exclusively to SLS can be explained by the fact that this manufacturing process is one of the most commonly used processes for industrial applications, namely for structural components. The other reason may be the fact that dyes are usually confined to their aesthetical purpose or their ability to enhance the objects’ resolution, while recent developments in the field reveal that they might also confer functional properties to 3D printed components.
“Modifying elastic moduli upon light irradiation, inducing optical and emitting properties in the matrices or conferring temperature responsivity are just few examples of innovative stimuli-responsive materials that can be produced by combining well-designed dyes with the appropriate 3DP printed matrices”, a research on “Functional Dyes in Polymeric 3D Printing” reads.
In this vein, dyes can deliver specific properties such as modification of mechanical behaviour, light emission, tunable permeability, controlled wettability or mechanochromic features depending on how they are utilized with photopolymerization techniques (SLA, DLP), Direct Ink Writing, SLS or FFF. To achieve such properties, dyes are generally used during the printing process which means that, with this method, they cannot be considered as a step of the post-processing stage.
-
Mixing colors examples – Image via 3D Systems -
Legend: 3D Printed bearing, threaded screw and mesh assembly Center, Rigid Clear M2R-CL, M2G-CL Armor and M2G-DUR ProFlex; Outer ring, M2R-CL dyed with 1% concentration (60C and 30min) – Image via 3D Systems.
As for the main goal of this article, which is to explore the direct colouring process of 3D printed parts after they come out of the 3D printing machine, one notes that companies that have been investing extra miles to automate this process include for instance, DyeMansion, CIPRES GmbH and Girbau. Moreover, although they are known for their ultrasonic cleaners, it should be noted that OmegaSonics has developed a dye tank specifically to dye parts from HP MJF’s technology or Stratasys’ technology.
DyeMansion, the youngest one in this list, was founded in 2013 and started its activities as Trindo, a 3D-printing agency that sold 3D-printed smartphone covers in the corporate design of large companies. In 2015, when the team developed their first industrial colouring solution – ending the smartphone journey -, Trindo became DyeMansion and since then, has been dedicating its core business to post-processing solutions of 3D printed parts.
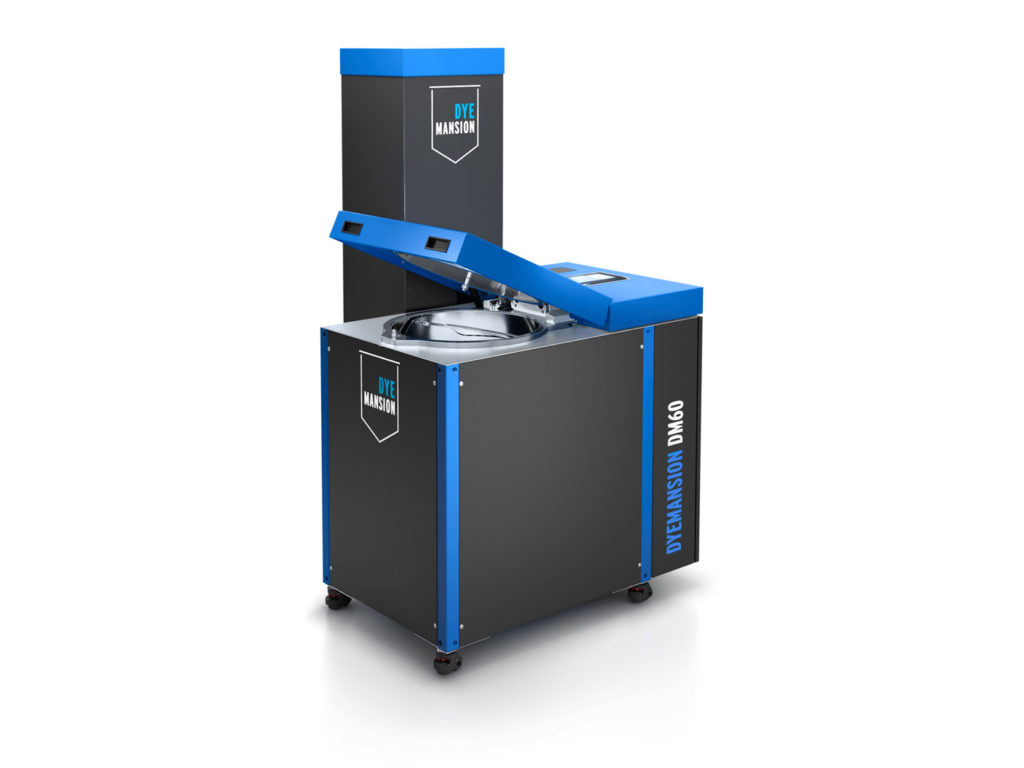
In 2004 when it was founded, CIPRES was a manufacturer of laser sintering prototypes. In 2006, the company has decided to deliver serial production of 3D printed parts, and since then, has also been focusing its activities on the development of colour techniques, colour units and solutions for surface finishing.
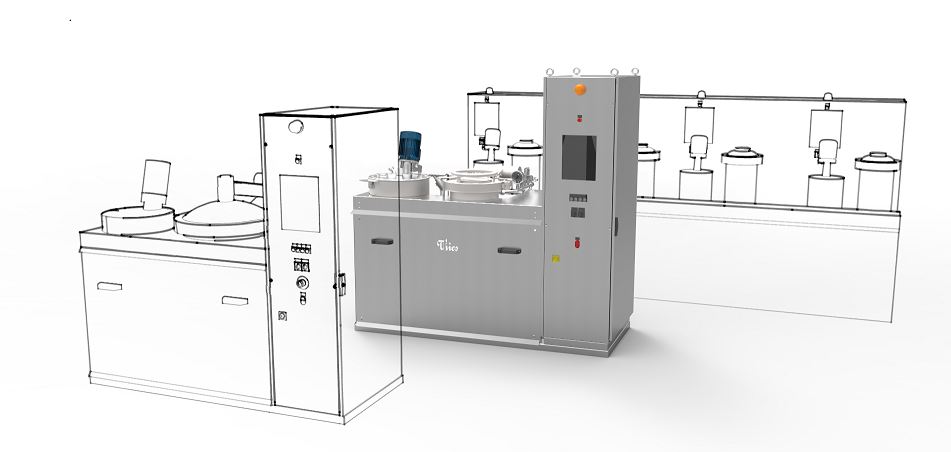
Girbau is the company that raises our interest the most in this short list. Very little communication is done about its 3D printing activities. The company is acknowledged for the manufacture and sales of industrial laundry equipment as well as its expertise in water management and temperature control. Headquartered in Vic, Spain, the company was founded in 1960, and is still managed by the Girbau family. With an annual turnover of €185 million, Girbau employs over 1 000 staff today, holds 15 subsidiaries across the world and is backed by 80 resellers.
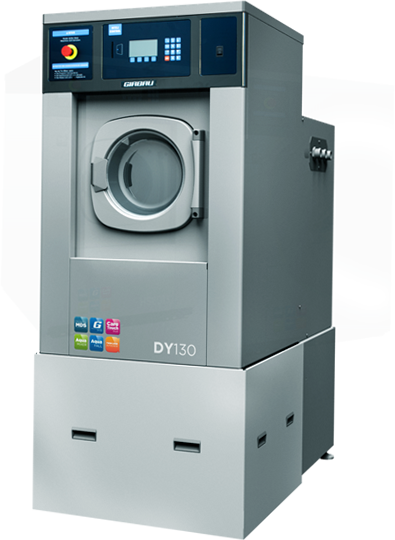
Colouring solution of Girbau – Image via Girbau
An exchange with José Maria Maristany, responsible for the Girbau program in the AM industry, enabled us to discover that the company started developing a dyeing solution for AM in 2018, thanks to a partnership project between Girbau lab (Girbau open innovation platform) and Hewlett Packard (HP).
The project gave life to DY130, primarily intended for HP Jet Fusion 3D 4210/4200 Printing Solutions, an only dyeing solution dedicated to AM in the company’s portfolio. “We have decided to focus on dyeing solution because of the synergies between Girbau traditional know-how in [water management and temperature control]. We are currently working on adjacent products and services to complete our dyeing solution and enhance our value proposition”, Maristany told 3D ADEPT Media.
The automated dyeing step of the post-processing stage
As often mentioned in our dossiers, the post-processing stage is a long phase that comprises many different tasks that operators can perform to deliver the desired end-product.
If you are familiar with 3D printing production, then you probably know that the first step in the 3D printing post-processing workflow is cleaning. It appears right after the part has been cooled and uncaked. This stage remains of paramount importance prior to performing dyeing to avoid stains that could be left by white powder and to obtain a very functional part.
(Nonetheless, if some stains do appear after the dyeing process, then a bead blast or shot peening post-process step is required. A shot peening after the dyeing process might help to improve the aesthetic appearance of the parts.)
So, normally, right after the cleaning phase, the dyeing process is relatively simple to achieve and consists of two main phases. “In the first phase, parts are immersed into a dyeing bath with specific temperature conditions for a prescribed period of time. In the second phase, [the operator] rinses parts with water”, Maristany explains.
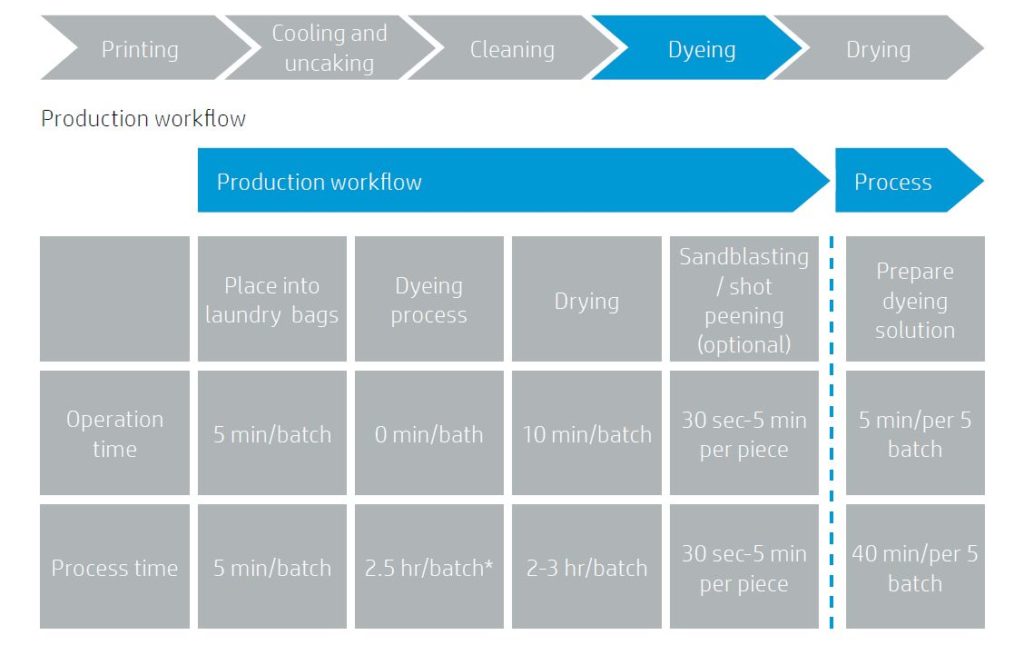
* If there is a hot water supply installation, the process times shown here will be faster, reducing the
processing time to approximately 45 minutes. Source: Girbau.
The teams of Girbau and HP that have worked on the development of the Girbau DY130 explained in a report that, to achieve colour uniformity for parts through this process, all details and cavities of the parts are reached. Not only is the process repeatable, but the operator is not limited by the size of a small pot as it is the case with pot dyeing. Therefore, many parts can by dyed at the same time.
However, two main recommendations are worth noting:
The first one is that “to avoid the physical marks produced by movement of the pieces during the drying process, the use of laundry bags to separate pieces (with different weights) in the same batch is strongly recommended. And, “as the process takes place in water, it is important to keep in mind that, as parts absorb some water during the process, their dimensional and mechanical properties may change slightly. Warpage of thin and flexible parts could be affected.”
A closer look at the DY130 dyeing solution from Girbau reveals that the solution’s predefined programs include Dye bath mixing, Dye bath conditioning, Dyeing 60° C, Dye bath disposal and Cleaning.
Speaking of materials their solution can process, Girbau’s expert states that “HP has validated [their] solution for PA11 and PA12 materials. DY130 could be used to dye parts produced with similar Industrial 3D printing solutions such as SLS.” Although the information has not been confirmed yet, the solution could also be compatible with the recently launched Stratasys SAF technology.
Lastly, operators might need a dedicated machine by colour, but colour change remains feasible using recommended detergent and some operational activities.
Applications and Outlooks
-
3D printed parts produced on MJF – Coloured by Girbau – Courtesy of Girbau -
Dyeing for 3D printed parts has proven its relevance in applications where a pleasant look is crucial. Consumer products like eyewear, watches, or figurines, some medical parts used for training, as well as some automotive and industrial parts are a few examples of applications that may require this (optional) process of the post-processing stage.
Although automated dyeing seems to present a lot of advantages, operators should always be careful when it comes to using it for parts that require a long-term contact with skin. Lastly, those who were used to conventional pot dyeing often depict the fact that with such technological advances, some human touch is lost. Whether it is true or not, in the end, they should not forget that it’s up to them to decide whether they want to go for an automated dyeing process or continue with a traditional pot dyeing process.
This exclusive feature has first been published in the May/June edition of 3D ADEPT Mag. Featured image: 3D Printed bracelets – coloured by CIPRES GmbH – Courtesy of CIPRES GmbH.