“He didn’t have an answer to this basic question.” Jan De Pauw, CTO & Co-founder of ValCUN took 40 minutes of his Friday shift to share their company’s journey – and at some point, the way the company started is a fresh reminder that the only stupid question is the one that is never asked.
In 2014, when Jonas Galle, ValCUN’s other cofounder was designing a rocket engine for aerospace, he immediately thought of AM as a production method. While he understood the capabilities of metal 3D printing (LPBF) for this process, he quickly realized its expensive cost. The willingness to reduce costs for such production led Galle to consider FDM 3D printing as an option. The only thing is that FDM could not process aluminum or other metals. Why can FDM not process aluminum or other metals?
This question led to several other ones, an investigation that ambitions to explore how one can reduce the cost of a metal part with AM and in 2016 to ValCUN. Yet, it’s been 6 years and the Belgian startup remains intriguing, continuously raising interest from those outside its bubble.
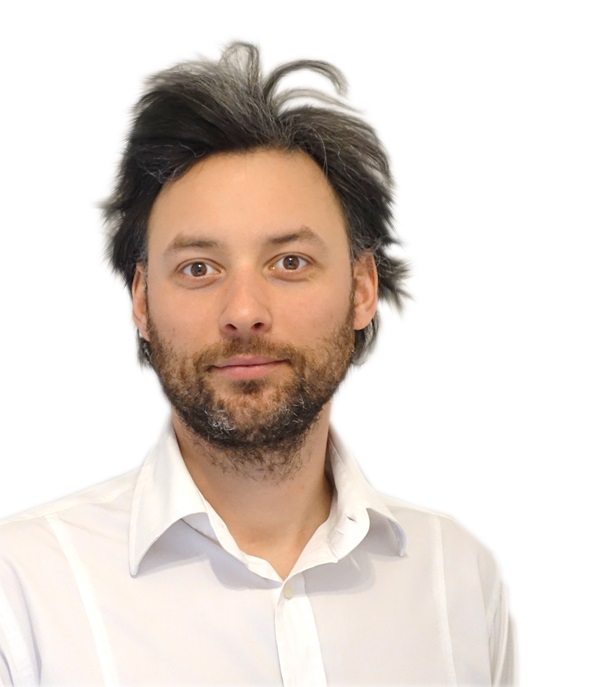
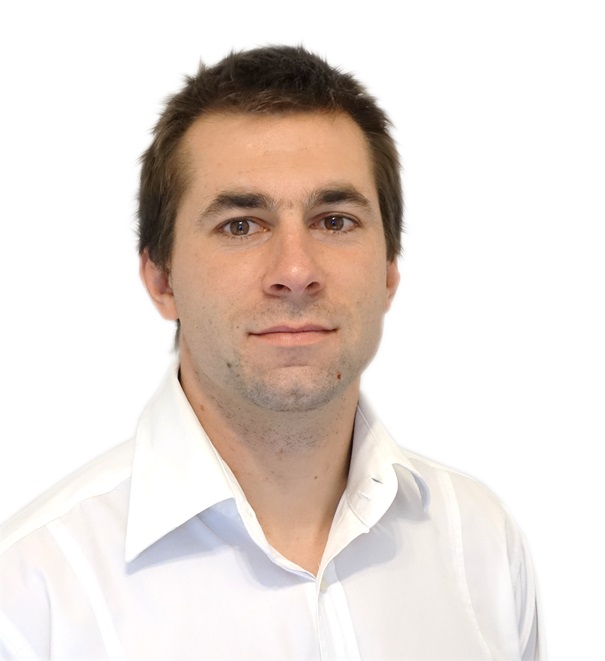
ValCUN’s will to operate in stealth mode is legitimate when we know that the less you say, the more you keep a competitive advantage over others; most importantly, when we know that hardware-tech companies do not benefit from the same “generosity” of investors to raise funds in Belgium as elsewhere. Here is the thing, this strategy can be a double-edged sword, because if you do not firmly define yourself, you let others define you.
That’s the reason why, in this Q&A series, De Pauw reveals some of the key capabilities of their technology – at least the key strengths that will make you knock on their door for a possible partnership.
3DA: What type of AM process does ValCUN develop? And how does it work?
We operate in the metal AM segment and we focus on aluminum. Not only is it a hard material that can be processed by various types of metal AM technologies (powder-bed fusion, binder jetting, etc.), but it’s also a very interesting material in terms of properties and applications.
We name our technology molten metal deposition (MMD). It’s an analogy to FDM but with molten metals. It’s easy to think that our technology is similar to Markforged’s desktop AM system but it’s not. The main difference is that in our case, all filaments are direct aluminum alloys wire while with other OEMs like Desktop Metal and Markforged are a mixture of metal and polymer. Furthermore, their process requires three steps to get to the final process (printing – debinding and sintering) while everything is performed in one step in our case. That’s the basic difference between the most known “metal FDM” technologies and our technology. So far, we believe we are the only OEM that develops a continuous extrusion-based method for metal 3D printed parts that processes molten metals. Few people did try this and stop their R&D activities as it is hard to get stable and reliable extrusion rates. We are aware of this and that is a reason why it took so much time for us to come with a solution. But as long as the physics make sense, perseverance always wins.
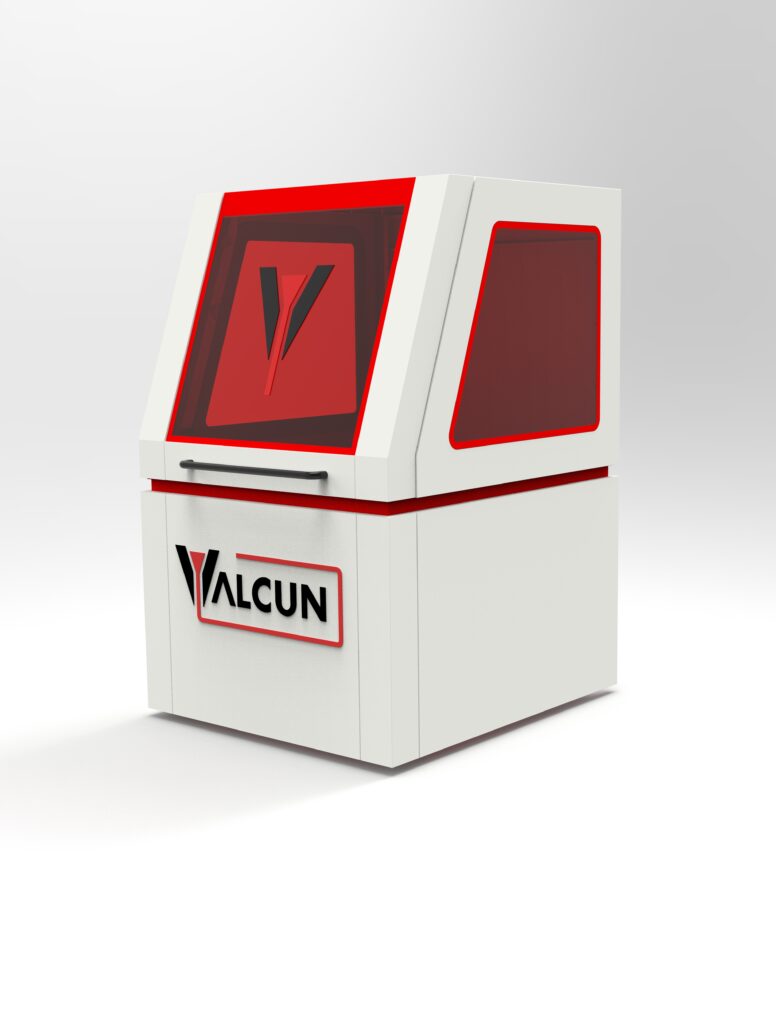
3DA: Materials are often highlighted as a key challenge to achieve repeatable and industrial production parts. Do you face the same challenge with your technology?
The short answer is NO. 🙂
The long one requires to compare the process with other processes. For the LPBF process for instance, experts change the alloys, the ones that are mostly frequently used today in the industry (AA6061 – AA7075). Everybody likes them in the industry except one has difficulties printing with LPBF. By changing the alloys, industrials get suspicious and are not willing to explore applications with them. That’s the reason why, aluminum AM is not widespread yet.
With our technology, you can take any aluminum alloy and process it. The main reasons are the nature of the physics in our process that are significantly different from powder based technologies. This means that, all aluminum alloys that have been used during the last decade on conventional manufacturing processes, can now be made available in AM. This is a game-changer for the industry.
3DA: Let’s focus on automotive. ValCUN could be a supplier for the electric vehicles’ market. What challenges can your technology address in this specific vertical?
We are focusing on heat exchangers. Electricity or power electronics tends to be seen as one of the main challenges in the production of electric vehicles but it is not. It is the heat that is generated by electricity and the drain of this heat that is the technological limitation in such production. AM has already proven to be an excellent tool to address this limitation. In our case, we can print very large overhangs and bridging, similar to FDM. The fact that we only focus on aluminum printing plays to our strengths. First of all, aluminum delivers properties that are ideal for heat exchangers. Furthermore, since metal powders are used with SLM, it can be tricky to produce heat exchangers with internal channels as it might not be 100% free of metal powder or due to half adhered particles. That’s the reason why operators would rather choose to explore WAAM, binder jetting , MMD or any other AM process that does not use powders for this application.
3DA: Are there any examples of applications that you can mention in this vertical?
Our technology can also be a good production candidate for heat exchangers in ICT centers. Another category that is raising our interest is near-net-shape production. With such manufacturing, we can easily achieve the desired production results with post-processing. In the long-run, we would focus on everything from hundred to thousand parts.
3DA: ValCUN has secured 1.5 million euros in fund raising. What happened since this fund raising?
We expanded our team, from 3 FTEs to 5 FTEs. We expanded our machines. We acquire a new patent and we developed a new extruder.
3DA: What are the next urgent steps the company ambitions to achieve?
This is the period of pilot projects for our technology. We are willing to demonstrate the capabilities of our technology and we absolutely need to do so – as you may know any new technology is suspicious, so industries need to know and feel what they can perform with MMD. At the moment, projects that fit with our roadmap are those related with aluminum parts, thin-wall structures…We therefore welcome any company that is interested in exploring some applications to reach out to us.
In the long-run, we will secure another funding round and hopefully will announce it in Q1 next year.
This feature has first been published in the March/April edition of 3D ADEPT Mag.
Remember, you can post job opportunities in the AM Industry on 3D ADEPT Media free of charge or look for a job via our job board. Make sure to follow us on our social networks and subscribe to our weekly newsletter : Facebook, Twitter, LinkedIn & Instagram ! If you want to be featured in the next issue of our digital magazine or if you hear a story that needs to be heard, make sure you send it to contact@3dadept.com