3D Systems continues to improve the way users will leverage its Figure 4 platform. Today, the AM specialist unveils a new portfolio of plastic materials that will allow a broader range of applications: Figure 4® RUBBER-65A BLK, Accura® FidelityTM, Accura Bond, Accura Patch, and Figure 4 JEWEL MASTER GRY.
Compatible with the Figure 4 and Stereolithography (SLA) printing technologies, these materials would “deliver accurate, economical, and repeatable results” at the production level. Furthermore, to choose the ideal material for their applications, customers are given data sheets with key test results and performance specs of each material.
A close look at each material
Tested for UL 94 standards, the Figure 4 RUBBER-65A BLK delivers high elongation at break for flexibility and durability. The biocompatible material meets the ISO 10993-5 and ISO 10993-10 requirements.
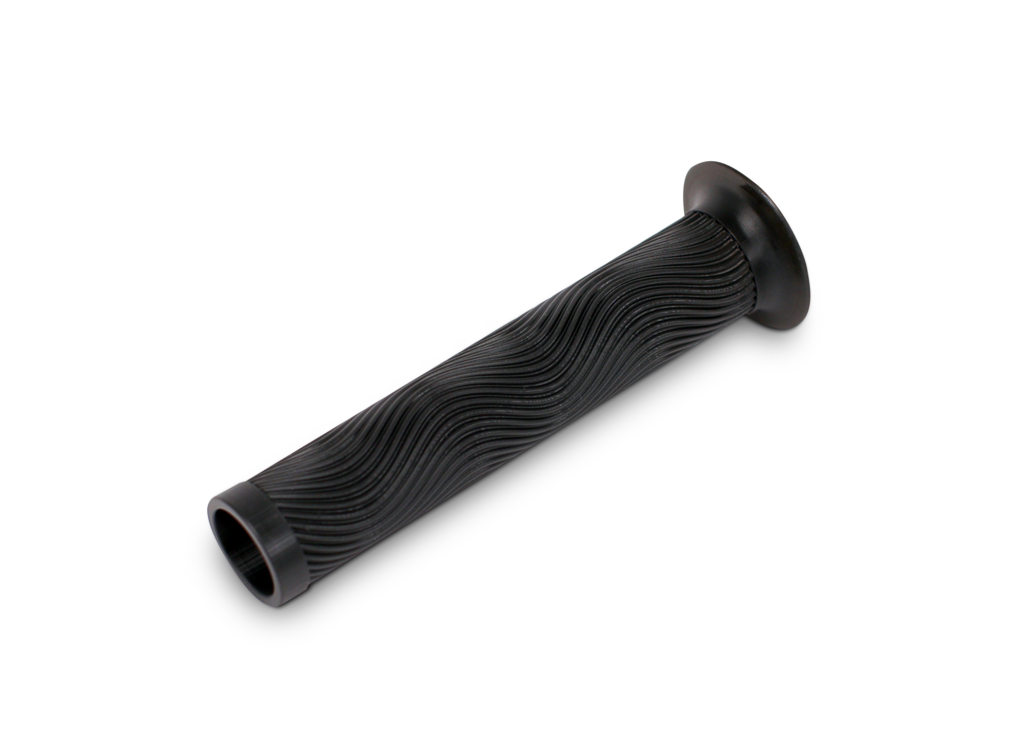
In this regard, it is a good choice for the fabrication of grips and handles as well as padding for splints and braces. It can also be used for the production of end-use elastomeric parts such as air/dust gaskets, seals for electronics, vibration dampeners and pipe spacers. 3D printed parts produced with this material deliver a high degree of accuracy and minimal scarring from supports and do not necessarily require a secondary thermal post-cure.
As far as casting materials are concerned, it should be noted that thirty years ago, 3D Systems unveiled the first 3D printed casting pattern. In the meantime, the materials producer learned from the experience of foundries and improved solutions that can ease direct production of medium to large size, high precision 3D printed investment casting patterns.
One of these solutions is the launch of the new casting material, Accura® FidelityTM, and two new post-processing materials (Accura Bond, Accura Patch), to enhance this trusted platform.
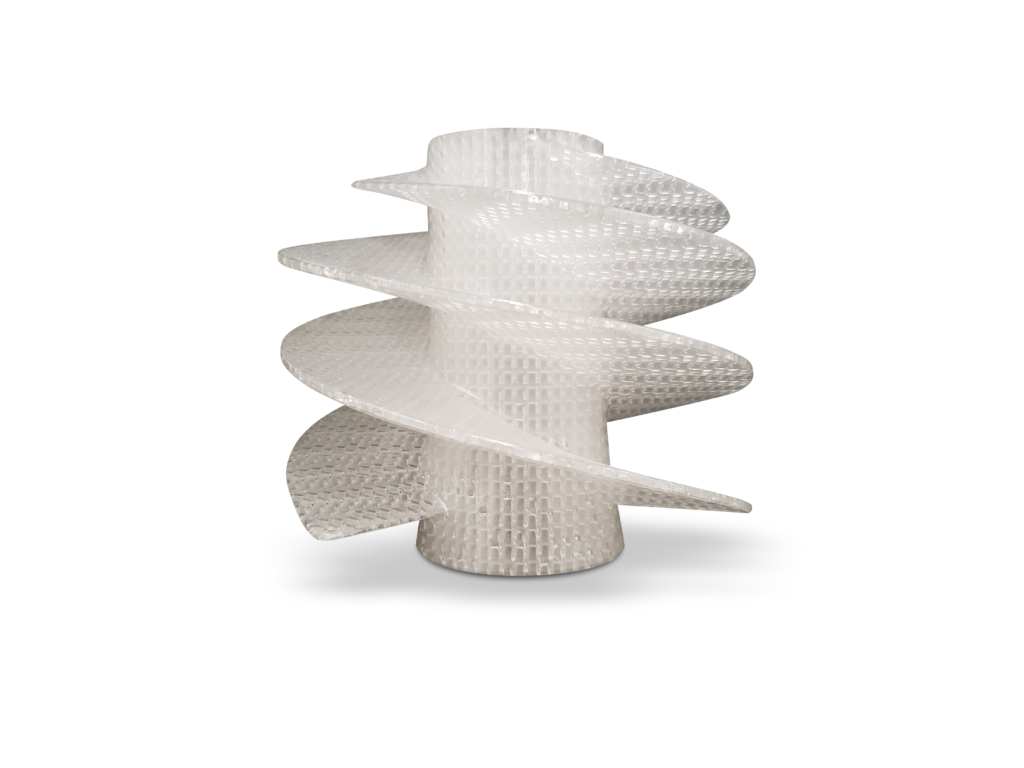
“The new Accura Fidelity material for Stereolithography printing has improved the post-processing of our QuickCast investment casting patterns,” said Nancy Holt, director of operations, 3D Systems On Demand. “The low viscosity of this material facilitates better drainage and faster cleaning of the patterns, resulting in an expected increase in throughput by up to 30% as we move into full production with this material. The ultimate test is in its castability, and our foundry customers are providing very positive feedback. One customer, SeaCast, said the QuickCast pattern with Accura Fidelity casted extremely well with their process and they were very pleased with the final metal part.”
As for the Figure 4 JEWEL MASTER GRY, it comes in line with the company’s desire to push jewelry applications forward. Indeed, as a reminder, early at the beginning of the year, the company launched its Figure 4 production solution for jewelry applications.
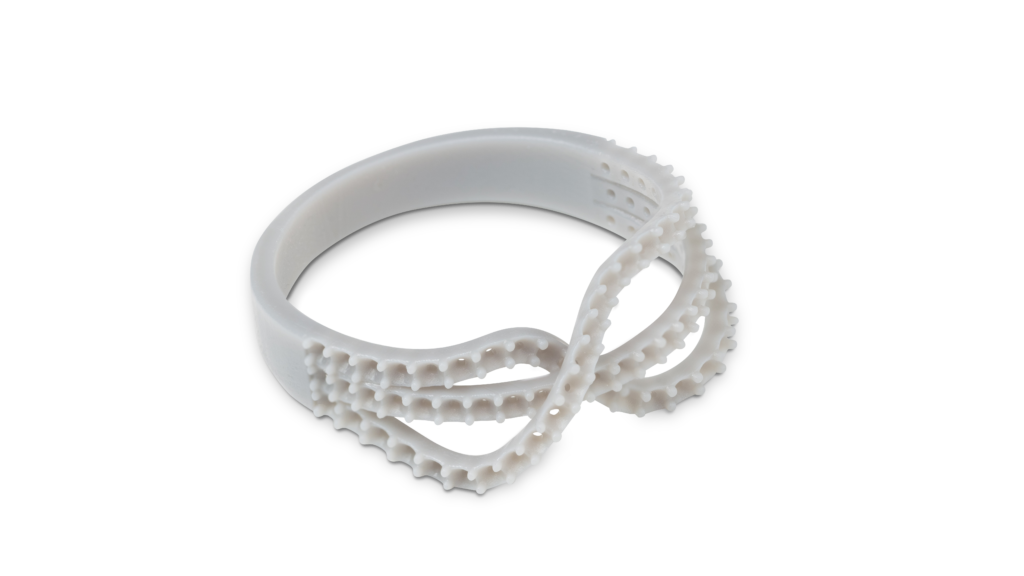
Compatible with this platform, this material allows for the manufacturing of high-volume jewelry silicone molds and prototype/fit models. It integrates high heat deflection temperature properties and delivers exceptional precise surface quality for design and functional prototyping, as well as snap-fit and stone-in-place testing. Moreover, it meets biocompatibility standard ISO 10933-5 for cytotoxicity, making it safe for try-ons and fittings.
It’s been two years now that 3D Systems has been developing a wide range of solutions for its Figure 4 platforms and it looks like the company has not finished to surprise us.
Remember, you can post free of charge job opportunities in the AM Industry on 3D ADEPT Media or look for a job via our job board. Make sure to follow us on our social networks and subscribe to our weekly newsletter : Facebook, Twitter, LinkedIn & Instagram ! If you want to be featured in the next issue of our digital magazine or if you hear a story that needs to be heard, make sure to send it to contact@3dadept.com