
Machine manufacturer 3D Systems drew attention with its new SLS 3D printing solutions including 3D printing materials.
The 3D printer maker launched the Accura® AMX High Temp 300C resin, SLS 300 printing system, a new professional service for C-103 3D printing materials, and the DMP Flex 350 Triple laser printer at the Frankfurt event.
Vice President of 3D System Martin Johnson said: “The latest additions we’re introducing at Formnext are expanding the capabilities of our plastic and metal solution portfolios to enable manufacturers to produce high-quality parts more efficiently. It has been a privilege to see our AIG specialists work closely with our aerospace and defense customers on the most challenging applications in difficult materials for extreme environments”.
All these new additions are designed to meet the customers’ needs of producing high-quality end-use 3D printed parts across industries like consumer goods, space, medical, automotive and semiconductor. Recently, European Hospitals have performed cranial surgeries using cranial 3D printed parts made with 3D systems printers.
Accura AMX High Temp 300C resin
The Accura AMX High Temp 300C resin has a heat deflection temperature of 300°C, doubling the HDT of 3D Systems’ present unfilled material. The ultra-high temperature SLA resin eliminates post-thermal cure steps, fulfilling the demand of HDT temperature of 300°C required in 3D printed parts produced for HVAC and consumer appliances like stators and motor enclosures.
Justin Pringle, the managing director of Prototype Projects has lauded the material as “next level of SLA performance for high-temperature resistance”.
“The material surpasses any other SLA material with its unique HDT above 300C without the need for any thermal postcuring. The synergy between this material and its Figure 4 equivalent allows Prototype Projects to offer larger format parts to fulfill new and innovative applications to our customers”, said Pringle.
3D Systems will make the material available for all from the fourth quarter of 2023.
SLS 300 3D printing system and Powder Recycling Station
The company introduced the SLS 300 3D printing sytem (earlier known as Wematter Gravity) at Formnext. As a reminder, Wematter was acquired by 3D Systems last year. Formnext is the first show where we can the see the Swedish 3D printer rebranded.
The SLS 300 Powder Recycling Station (PRS) showcased by the company at Formnext was a fully automated unit that works in tandem with the SLS 300 to recycle and mix the unused material currently in the system with fresh material.
This maximises material usage and eliminates wastage of it, ultimately leading to a reduction in human intervention and low production costs.
The HEPA filters fitted PRS system will be available for commercial use from 2024 while the SLS 300 3D printer is already available. The HEPA filters adjust the machine to dampening, making it suitable for use in many environments.
This coupled with the C-103 Niobium alloy makes it suitable for producing 3D printed parts for space, aerospace and defense industry as it can withstand high temperatures and stresses. The C-103 refractory material has a service temperature between 1200°C and 1400°C along with a low ductile-to-brittle transition temperature. This 3D printing material is resistant to high vibrations, chemical attack, heat and pressure, making it ideal for producing 3D printed parts for rockets, spacecraft, launch vehicles, satellites etc.
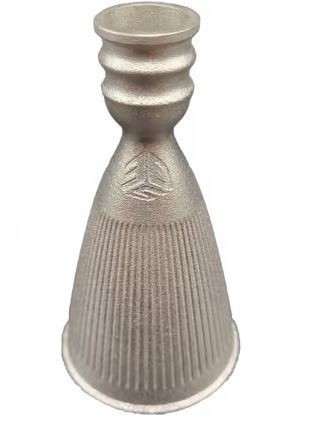
3D Systems is building on the success of recently launched NASA’s new GRX-810 super alloy by introducing the C-103 material which is very sensitive to O2 exposure maintained by the DMP vacuum technology of the company. Both the materials are available at the company’s Professional Services delivered by the Application Innovation Group (AIG) but GRX-810 is only available for US customers.
New DMP Flex 350 laser printing platform
At Formnext, the company also showcased the latest DMP Flex 350 platform, called DMP Flex 350 Triple which has an enhanced vacuum chamber design with better Removable Print Modules or RPMs with different build volumes.
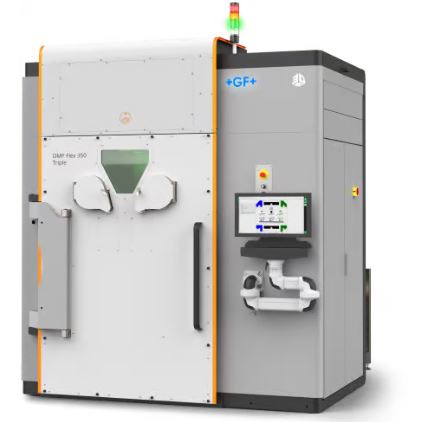
The new DMP Flex 350 Triple 3D printer has a larger build capacity in the same footprint having features like:
- RPM with a larger build of 350mm x 350mm x 350mm and
- the standard RPM with a build volume of 275mm x 275mm x 420mm.
The RPMs can also be swapped for increased application flexibility and the laser system offers multi-laser load balancing and seamless surface quality scan strategies. This eradicated the problem of roughness in zones where multiple lasers work together.
The new DMP Flex 350 Triple 3D printing platform is compatible with eight different 3D printing materials including aluminum alloys like AlSi10Mg, AlSi7Mg0.6, high-strength aluminum alloys like A6061-RAM2, and high-conductivity aluminum CP1 which are good for thermal resistant applications. In addition to that nickel-based alloys such as Ni718, Ni625, and HX are available for high-temperature corrosion-resistant applications. Lastly, it works with 316L stainless steel used for creating 3D printed parts in the (petro)chemical, food, and pharmaceutical industries.
While the DMP Flex 350 Triple is open for commercial use, the new RPM will be available from July 2024.
Apart from these new products, 3D Systems also gave a sneak peek to its PSLA 270 3D printing platform which would be useful to generate 3D printed parts for healthcare applications.
Remember, you can post job opportunities in the AM Industry on 3D ADEPT Media free of charge or look for a job via our job board. Make sure to follow us on our social networks and subscribe to our weekly newsletter : Facebook, Twitter, LinkedIn & Instagram ! If you want to be featured in the next issue of our digital magazine or if you hear a story that needs to be heard, make sure to send it to contact@3dadept.com