Every year a range of new companies venture into the Additive Manufacturing industry. In the list of 2023’s newcomers, one notices that the growing trend around companies that focus on AM-dedicated applications continues. While services target the entire value additive manufacturing chain (from software to post-processing), it is interesting to see how companies provide solutions in new vertical industries that could adopt AM on a broader scale.
Here are 12 newcomers that turned stealth mode off in 2023.
1. ECL
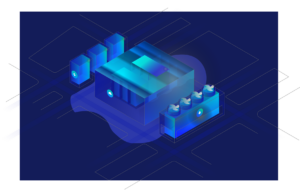
At the beginning of 2023, in January a new company EdgeCloudLink (ECL) was started by former Microsoft data center employee Yuval Bachar to make data centers zero emission with the help of 3D printed hydrogen power grid.
The California-based company raised $7m in funding from Hyperwise and Molex with its modular net zero proposal of making Data center-as-a service through which they planned to build 1MW units of hydrogen-powered off-grid data centers.
The company built the first zero-emission data center in Mountain View, California using a locally powered hydrogen source and a construction 3D printer. The data center was built with the help of a proprietary liquid cooling design and didn’t require any diesel generators.
ECL made the design available in the second quarter of 2023, offering services to create zero-emission data centers within 6 months at half the price of building data centers in the conventional way (half of $12-15 million per MW). The data centers built in this process are equipped with hydrogen fuel cell tanks and connected to the local grids for added reliability which can be operated by the customers all by themselves or can be run jointly with ECL.
The company also provided ECL construction 3D printer services which can used by customers for making data centers or other 3D construction buildings.
2. Outokumpu
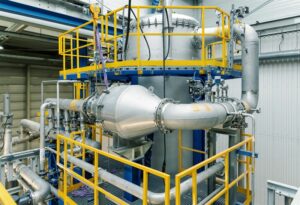
In April this year, the Finnish stainless steel manufacturer Outokumpu entered the metal AM industry with metal powder solutions. The company introduced a range of stainless steel powders which were manufactured at their new atomization plant in Krefeld, Germany.
The stainless steel powders introduced by Outokumpu can be used in various 3D printing processes like Metal Injection Moulding (MIM), Binder Jetting (BJ). Beyond powder manufacturing, the company seeks to create a viable AM ecosystem to support its customers in producing customizable 3D printed parts.
3. Evove
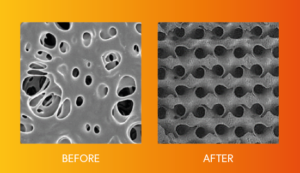
Another company trying to solve net zero problems is the UK-based startup Evove. The company operates in the field of filtration technology; it is on a mission to reduce the cost and environmental impact of the filtration and separation of fluids in a variety of sectors. By filtering the unfilterable, the team leverages nanotechnology and additive manufacturing processes to deliver advanced membrane technology that could reduce the impact of water filtration.
Water filtration systems affect the environment through production, testing and transport. These issues are present in any product that’s manufactured and shipped to customers. Manufacturing of water purification systems requires a lot of material and water from a wide variety of different sources. Depending on the specific types of materials that are used, the degree of the impact on the environment varies, one learns from a source.
On another note, industrial process water is not (that) easy to recycle; not to mention that there is often waste in wastewater, and cleaning up heavy industry wastewater lakes is not that simple. Evove has taken note of all these challenges and now ambitions to address them by targeting the lithium, green hydrogen, desalination, food and beverage, and water and wastewater industries.
More specifically, the company’s technology harnesses graphene oxide-based coatings and a variety of 3D printed enhancements to boost the performance of conventional membranes. Separonics® are Evove’s precision-engineered membranes, providing transformational productivity gains in selectivity and flux, operational efficiency, energy consumption and equipment lifetime.
4. JPB Système
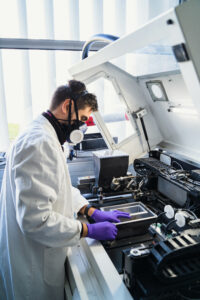
The French KeyProd production monitoring solution provider JPB Système ventured into the AM industry this year to offer metal binder jetting services for making complex 3D printed parts, especially those used in the aerospace industry.
Through the acquisition of a stake in France-based 3D printer manufacturer start-up, Addimetal, JPB Système will be involved in the development of Addimetal’s innovative open hardware platform, technology and associated process to ensure both existing and future application needs are met.
5. SAEKI
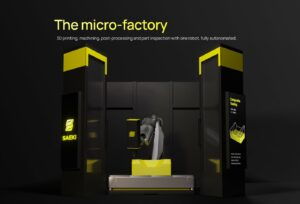
The Swiss robotics company Saeki started by Andrea Perissinotto, Oliver Harley and Matthias Leschok started its journey to automate factories this year by building a production unit that will support manufacturing in both the construction and other industrial sectors.
Their solution combines 3D printing, and milling, with large industrial robots that can print formwork up to many meters in length.
The Swiss company offers Robotics as a service for end-to-end automation for 3D printing, machining and inspecting of functional parts to fully automate factories.
6. 3D BioFibR
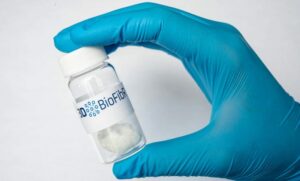
3D BioFibR, a company that specializes in biomaterials for tissue engineering, is the latest to penetrate the 3D bioprinting market. The company focuses on collagen products that can serve 3D cell culture and tissue engineering applications, especially the cellular scaffolds segment. Using its fully automated and proprietary dry spinning process, 3D BioFibR could produce “high quality, diameter-controlled collagen fibers at commercial scale.”
The machine can process μCollaFibR™, a proprietary bio-ink additive for use in 3D bioprinting of tissue and organ models in a laboratory setting.
The company says CollaFibR™ helps to make more durable 3D printed tissues as they can assemble multiple types of cells layer-by-layer. This helped them to produce a more natural collagen fiber matrix with cellular movements and biochemical properties of the naturally occurring fiber.
7. flō optics
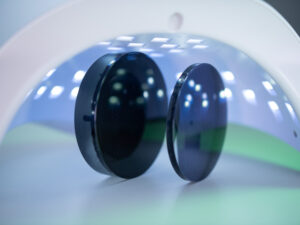
The Israel-based company flō optics has recently made it possible for 3D printing to find applications in the ophthalmic industry through its advanced lens coatings solutions.
At the heart of the manufacturing process, one finds an inkjet-based 3D printing technology that applies unique, multi-material, multi-layer coatings to lenses. This proprietary deposition technology is built on a rich expertise in digital printing.
Coatings range in function and vary according to customer needs. And these specific needs often come from the ophthalmic labs that fulfill the opticians’ requests. flō’s platform will serve this audience by providing manufacturing hubs that could generate thousands of customized lenses daily.
8. Additive Appearance
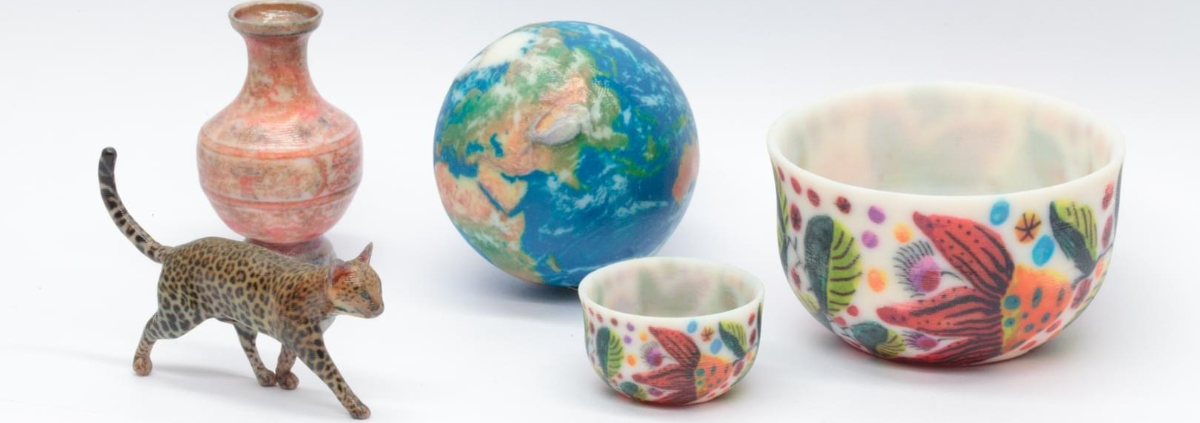
Years of research into simulation software for 3D printing by a spin-off company from Charles University in Prague led to a software simulation solution that could enhance the sharpness and quality of 3D printed parts.
Additive Appearance’s software is focused on the visual appearance of the resulting 3D prints and will not only achieve high color accuracy but also the best texture sharpness, which has been very difficult to achieve with existing technologies. The team is building the software with components from artificial intelligence to form a multi-step virtual optimization that is running before the printing. By using this software in combination with PolyJet 3D printers, the resulting physical prototypes will provide designers with a unique opportunity to communicate their vision to clients on prototypes as believable as the intended final product
9. Pelagus 3D
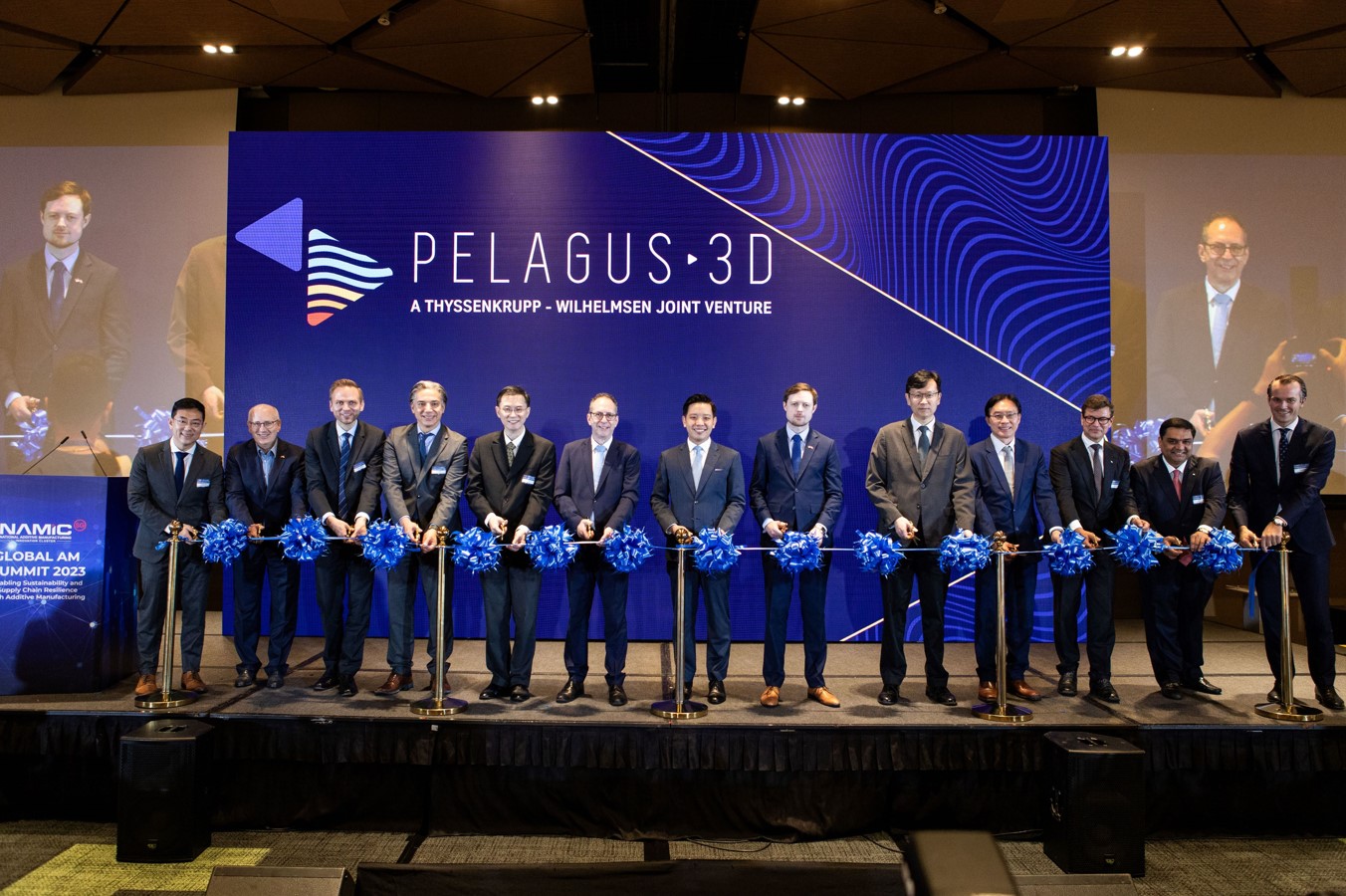
1. Kenlip Ong, Chief Executive Officer, Pelagus 3D; 3. Dr. Sebastian Smerat, Head of Customer Innovation of thyssenkrupp Materials Services and Member of the Board of Directors, Pelagus 3D; 4. Dr. Cetin Nazikkol, CEO Asia Pacific Africa and Chief Transformation Officer of thyssenkrupp and Member of the Board of Directors, Pelagus 3D; 6. H.E. Dr. Norbert Riedel, Ambassador, German Embassy Singapore; 7. Alvin Tan, Minister of State, Ministry of Trade and Industry; 11. Kjell Andre Engen, Chief Executive Officer & President, Wilhelmsen Ships Service and Member of the Board of Directors, Pelagus 3D; 12. Nakul Malhotra, Vice President, Emerging Opportunities Portfolio, Wilhelmsen Maritime Services and Member of the Board of Directors, Pelagus 3D; 13. Hakon Ellekjaer, Chief Commercial Officer, Pelagus 3D. Credit: thyssenkrupp
This is one of the developments in the AM industry that caught my eye as it is likely to have an impact on the maritime industry. Industrial companies thyssenkrupp and Wilhelmsen joined forces to launch Pelagus 3D, which will manufacture 3D printed maritime spare parts using 3D printing technology.
The aim here is to democratize and streamline access to 3D printed maritime parts and OEMs. The Singapore-based Pelagus 3D is offering a range of fleet optimization and vessel optimization through its OEMs and the AM platform also delivers 3D printed maritime spare parts on-demand, reducing vessel downtime and costs.
10. ArcelorMittal Powders
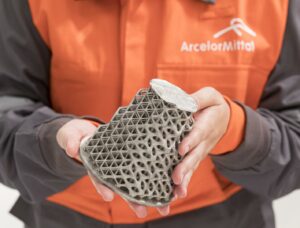
Over a decade of experience in the steel industry led Indian steel giant ArcelorMittal to steel powder manufacturing for the AM industry. The Belgian subsidiary has been working behind the scenes on a pilot application in the steel industry with Guaranteed, a 3D printing service provider where it’s also a shareholder.
Now, the company is building an inert gas atomizer in Aviles, Spain to manufacture steel powders for the AM industry which will be available for use in processes like laser powder bed fusion (LPBF), binder jetting (BJ) and direct energy deposition (DED) from January 2024. The company will have an annual capacity of 1,000 tonnes which can supply steel powders in batch sizes of 3 tonnes to the AM industry.
11. Forivory
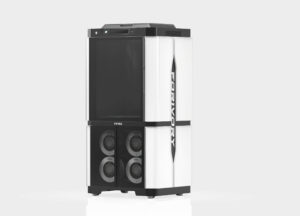
As we near the end of 2023, we came across a new 3D printer manufacturer from South Korea Forivory which has enhanced 3D printing with its FT400 3D printer. The new company Forivory has been launched by the South Korean 3D printing brand Jelect.
According to the R&D team of Forivory which built the FT400 3D printer based on the ‘high performance, high efficiency, stability’ characteristics, Forivory’s XTC (X-axis gantry toolchanger) technology solves the problem of slow output speed due to large and heavy head. This would place it ahead of other multi-nozzle 3D printers in the market. The company is offering its new 3D printer (globally from April next year) which comes equipped with Maker Station software to monitor the process.
12. Metafold
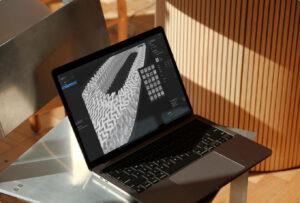
Metafold, a newcomer in Design for Additive Manufacturing, develops an “ultra-precise, lightning-speed geometry computation engine for outputting accurate designs for 3D printing complex parts”. Metafold explains that its cloud-based SaaS platform is accessible on any device, making it fast and easy for design and engineering teams to produce optimized parts with the Metafold web application or leverage the Metafold Engine API to build their own custom tools and integrations. Through this advanced geometry support, Metafold enables manufacturers to use less raw material and produce lighter, more efficient parts that use less energy, both of which contribute to helping customers achieve their sustainability goals.
This articles has first been published in the November/December edition of 3D ADEPT Mag.