Ideas are easy. Implementation is hard. In the manufacturing and technology industry, ideas are popping up every day. However, most of the founders choose to remain in stealth mode until they have a MVP (Minimum Viable Product) to introduce to the market – with good reason, given the risks that are often involved. Interestingly, this year, ten startups stood out from the crowd and introduced their products and services to the “glocal” (portmanteau that combines the words “global” and local”) AM industry. Here they are.
Q.big 3D GmbH
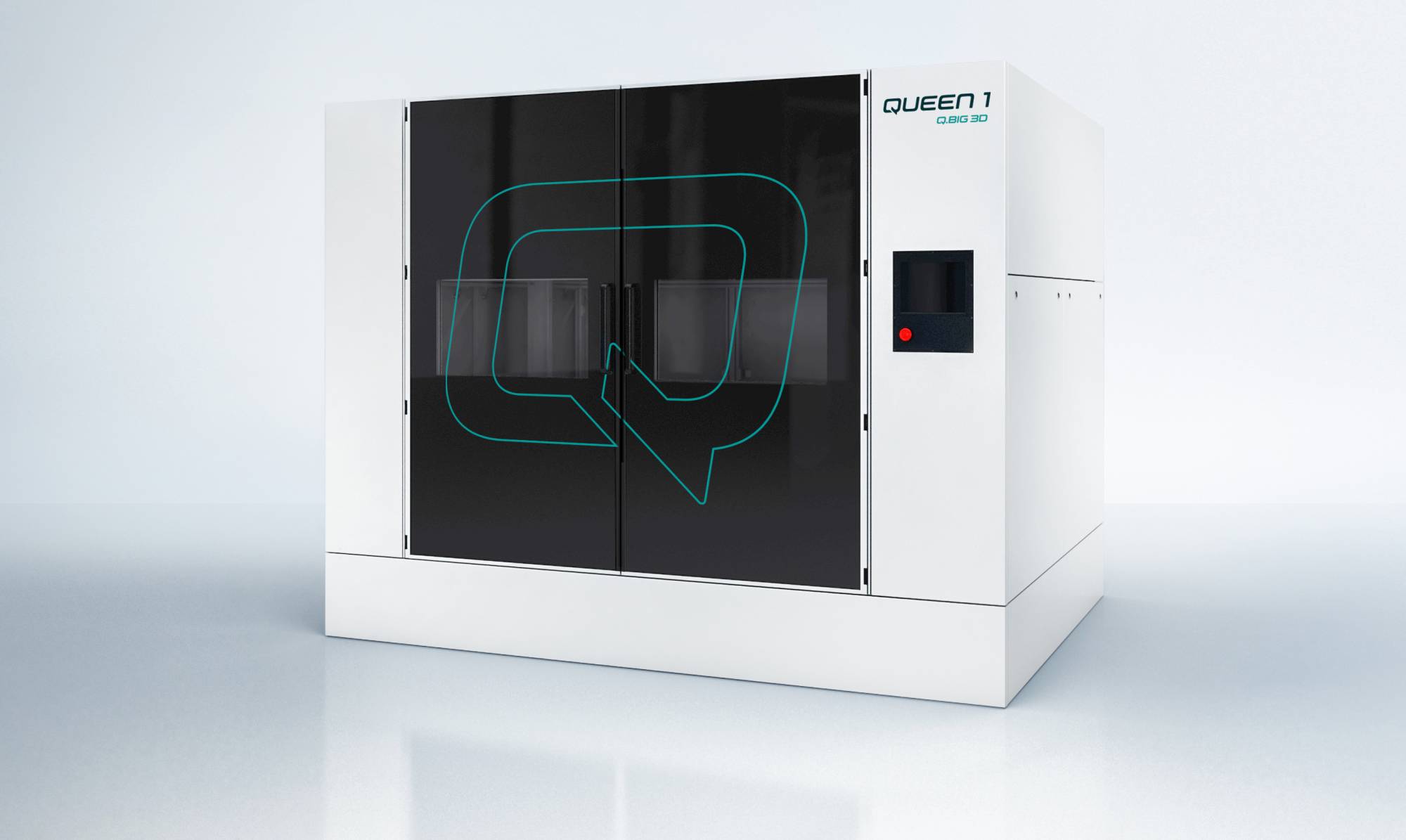
Founded in 2019, the Germany-based startup develops large scale 3D printers based on a process called VFGF (Variable Fused Granular Fabrication). I saw them for the first time at AM Forum Berlin. Their technology processes polymer (plastic) granulates into one single extruder. Variable because high-resolution printing is only used where the finest contours and good surface qualities are required. Everywhere else, the material throughput is much higher, the company says. Their flagship product is named Queen 1. I don’t know what inspired this name, but I like it. It’s easy to remember, and it implies something majestic – which is the feeling that big things should arouse. I now hope that their product is able to deliver on that feeling.
The team seems to be open to have commercial relationships with all companies across the world, but its deeds show that their main area of focus is the DACH region, as communication is mainly done in German.
Additive Assurance
I have good feelings about these guys. The team is experienced and interesting. Marten Jurg and Associate Professor Andrey Molotnikov, the founding team behind the Australia-based company spun out of Monash University in 2019; they have developed an in-process quality assurance solution for laser powder bed fusion (LPBF). Named AMiRIS, it enables manufacturers to ensure the structural integrity of components as they are being made and correct any anomalies when they occur.
They said they already work with a couple of customers in the aerospace and advanced manufacturing industries to enable the use of 3D-printed parts in serial production. And they end up their year on a successful note by securing a $4.1 million funding round to push forward their research and development activities and hire international business development teams.
AM Extrusion GmbH
Based in Radebeul, Germany, the idea of AM Extrusion became reality in early 2021 when Felix Alber, Aljoscha Roch and Sven Halank joined forces to develop a range of metal and ceramic filaments for 3D printing.
“Material availability is a high threshold for the industrial use of the otherwise so advantageous fused deposition modelling. With our unique AM-Xcomp binder system, we are able to lower this threshold and to process almost any available metal or ceramic powder into sinterable materials for 3D printing. Our patent pending AM-X thermoplastic filaments feature unprecedented powder enrichment rates, excellent printing properties and easy applicability at nearly room temperature. Warping issues in the workpieces, high occupational safety standards, the disposal of excess toxic material, and other disadvantages of conventional AM processes are now a thing of the past”, the company says.
With production capacities that range from 500 g to several 100 kg, their portfolio of filaments currently includes light or hard metal, copper, stainless steel or ceramics; it can be customized if there are special requirements for a filament to meet.
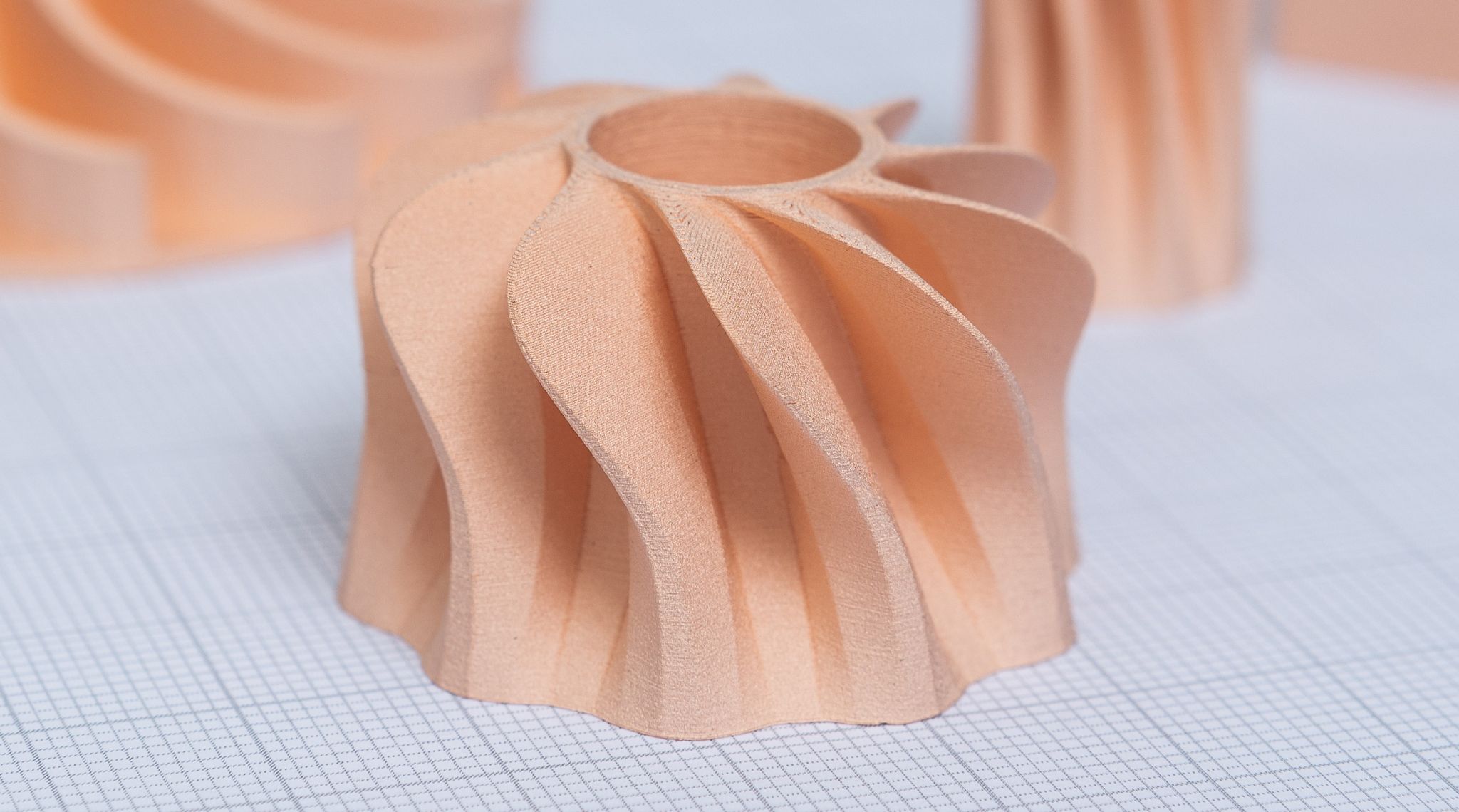
AM Extrusion invented a tool for printing copper easily. No airborne powder, no high safety requirements for the employees, and no personal protection equipment. Their special copper filament is fed in a print head of a 3D printer. The printer melts the filament and extrudes the material onto a building platform. “For 3D printing of pure copper parts, we invented the AM-X Cu 99,97% filament that contains a polymer filled with a high-purity copper powder at high volume fraction. The uniqueness of our material is that the polymer can be fully removed after printing and the copper powder can be sintered easily in a furnace. That enables a 100 % material consumption for getting copper parts. We avoid any material waste and have a resource-saving manufacturing process. The material is used additively, exactly where it is needed”, they explain.
Namma
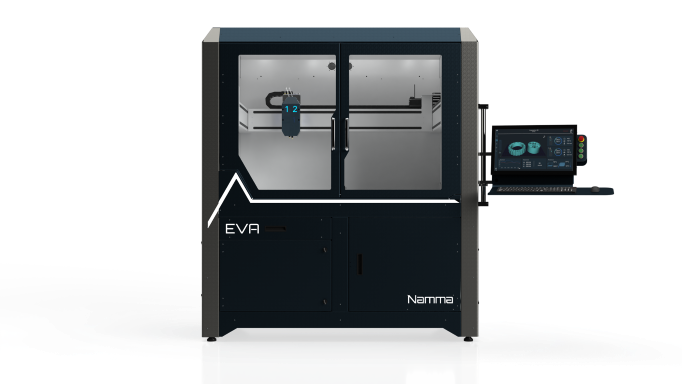
Namma is another startup that we failed to mention last year in our list of 3D Printing startups created in a post-COVID-19 era. Based in France, the engineers behind Namma believe in the best of both additive manufacturing and subtractive manufacturing worlds. Their flagship product is EVA, a hybrid 3D printer that combines 3D printing, CNC machining and laser engraving on one platform. Their machine integrates two separate heads that can function simultaneously – one can be a printing head, and the other, a milling or laser printhead; or you can have two unique printheads working at the same time. EVA comes with N-Center, its own software suite to enable its users to optimize their production at every step of the manufacturing process.
TriTech Titanium Parts
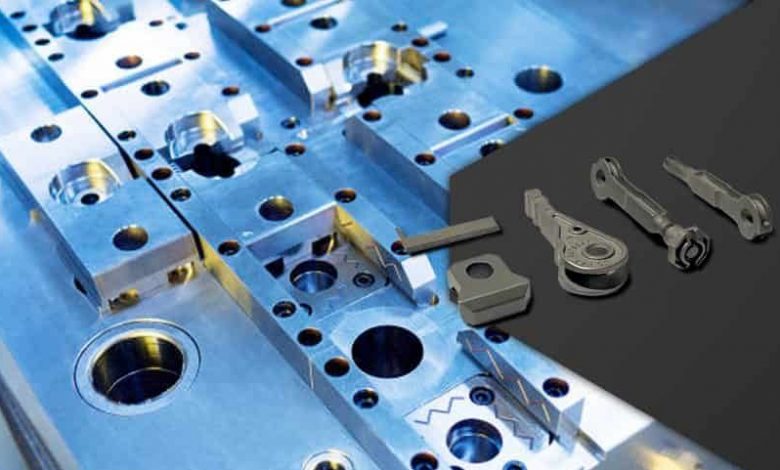
Manufacturers that have 3D binder jet printing, metal injection molding and investment casting in their production environment have understood the power of their complementarity. For me, they can only be up to something interesting and worthwhile following.
TriTech Titanium Parts, a newcomer on the market combines these technologies in its production environment. Launched on April 5, 2022, the company is a spin-off of its President’s former company, AmeriTi Manufacturing. The latter was sold to Kymera International, also on April 5, 2022.
Organized in response to market needs, TriTech produces net shape titanium parts using the most appropriate technology for the part and the customer. TriTech’s unique array of three production technologies includes 3D binder jet printing, metal injection molding and investment casting. The 3D printing is the latest addition, and the binder jet process is a unique cutting-edge manufacturing process for producing complex titanium parts.
Fractal Additive
Founded this year by Olivia Krueger, this US-based start-up provides two main services: Contract Design Engineering Services and Fractal Infill. My curiosity is aroused for this latter one: a solution that creates adaptive structures that are optimized for each part that goes through the slicer. Material savings increase as part scale increases, without the compromise of overall part strength. Why do I find it interesting? Because it’s hard to innovate in the material extrusion field (FDM 3D printing) and I am very keen to discover where Krueger can go with this solution…Hopefully, very far away.
Filaret
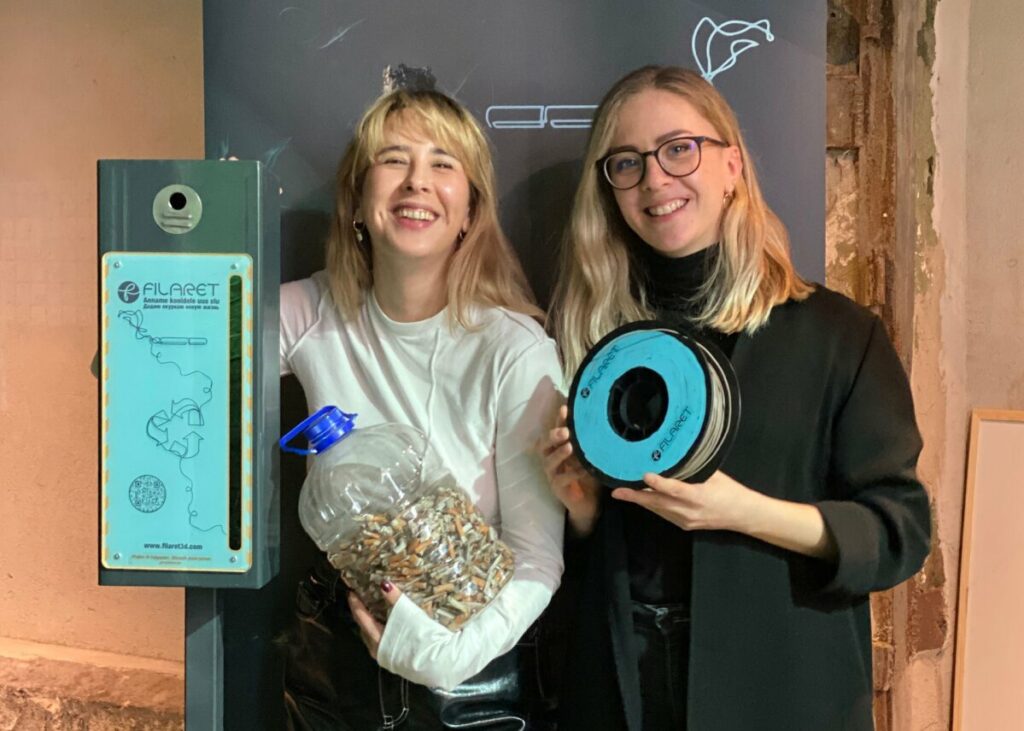
Did you know that cigarette butts are one of the most common types of marine litter in the Baltic Sea? In addition to plastic, most of the waste found in the Baltic Sea and in coastal areas is cigarette butts and cigarette filters, which are toxic and non-biodegradable. A single cigarette butt can pollute up to 1,000 litres of water, and toxins released from the filter into the water can persist for up to 10 years, becoming lethal to aquatic life.
That’s the reason why Ines-Issa Villido and Kristina Jacqueline Leon, the badass ladies behind Filaret – based in Estonia – embarked on a noble mission: making recycled waste materials a norm in the 3D printing industry by collecting and upcycling cigarette butt waste into a sustainable, compostable and nature friendly 3D printing filament. To do so, they installed special litter bins on the beaches of the Põhja-Tallinn district to prevent cigarette butts from ending up in the sea. For now, no information has been given on the transformation of these cigarette butts into filament. Furthermore, we do not know if the filament could be used for prototyping or production purpose. Hopefully, this information will be shared at the end of this pilot project by Filaret or one of its partners (the Port of Tallinn and the Tallinn Airport).
DUPLEX
Just when you think that there is not a lot to expect from FFF 3D printing anymore, a company comes to prove you wrong. A very intriguing manufacturing trend in this segment comes from a new entrant: DUPLEX. The pink brand introduces MAP™ (multi-dimensional additive production), a technology that enables multi-directional printing. Not only does this speed up the fabrication process, but this two-directional process also reduces or eliminates the use of support materials, and makes it easy to print organic geometries. Amid the wide range of FDM 3D printer manufacturers that are present on the market, I think DUPLEX is the one that could make a big impact.
Sinterjet
Based in Turkey, Sinterjet has been operating for a couple of years on the market but made their premiere this year at Formnext. The company wants to position itself on the market of affordable metal 3D printers. Priced at €65,000 (US$68,000), their flagship product is the Sinterjet M60, an industrial metal 3D printer with a build volume of 160 x 60 x 60 mm that uses Binder Jetting 3D printing technology, a process where a liquid binder solution is selectively deposited on powder layers until a complete object is created.
As you may guess, no support materials are required here, as the surrounding loose powder provides support for overhangs. With a resolution of 1200 x 1200 dpi, the machine can build at a rate of 50 cc per hour. This is quite fast for this type of volume, right? The machine is compatible with an in-house developed software solution which would be easy to use according to Sinterjet.
The Industry Sweden AB
This is one of the companies we met on the last edition of Formnext. (As we said in the “EVENT” segment, always leave room for wandering). They have actually been on the market for a while. You may have known them as BLB Industries – developing 3D printers for doors; they went on quiet mode and we lost track of their activity, then rebranded as “Industry” last year with the goal of adopting a new strategy. To be honest, it’s hard to say if one should still consider the company as a new start-up in the industry – given the fact that they now operate with a different name and category of products. Anyway, what you should keep in mind is that The Industry Sweden AB currently develops FGF systems (fused granule fabrication), which use thermoplastic granules rather than filament to print 3D plastic parts.
With a build area of 1500x1200x1200 mm, the FGF system is ideal for the use of recycled plastics, as the number of processing steps is reduced in converting raw material into feedstock when compared to filaments. It will also be capable of printing rubbers and certain biofibers fillers such as wood, hemp and flax.
The company says their rebranding is the start of a new scalable business model that will focus on developing strong brand recognition, with new products and strategies to fight plastic pollution.
Disclaimer: A number of big corporations also decided to create their AM division this year, they have purposely been excluded from this article to highlight SMEs and founders who are building their company from scratch.
This article has first been published in the 2022 November/December edition of 3D ADEPT Mag.