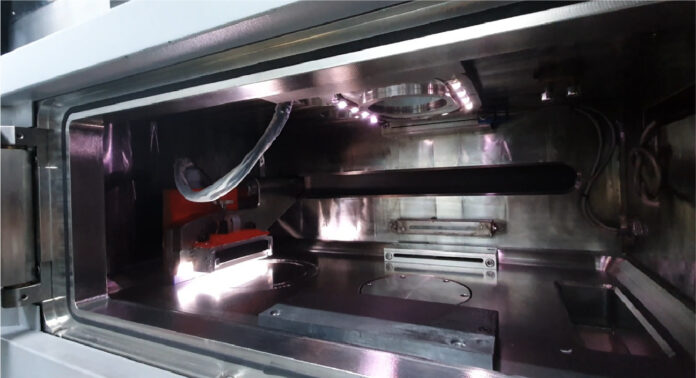
It might be easy for engineers or designers to think that, because they are not directly involved with the manufacturing of parts, they shouldn’t know about certain complexities surrounding the hands-on operation of machines. This is not true. Being aware of the variables and complexities related to the hands-on operation of machines helps to ensure clear communication with operators and most importantly, that design objectives perfectly meet manufacturing expectations. One of these complexities consists in understanding the importance of recoaters for metal Additive Manufacturing.
Put simply, a recoater is a horizontal bar that spreads and smooths material during the manufacturing process, to create a uniform and flat layer before the build material is solidified, sintered, melted, or bonded. As confirmed by Michael Wohlfart, AM Expert at EOS and Thomas Spears, PhD, Director of AAMT, there is a general understanding that only powder-based processes require a recoater.
Nevertheless, research shows that recoaters can also be used in VAT photopolymerization to spread liquid polymer. In such machines, the VAT photopolymerization machine consists of a resin vat, recoater blade, build platform, light source, and control systems. The liquid photopolymer resin is placed in the vat. The recoater is used to distribute and swipe the liquid resin when a layer is cured. The build platform attached to an elevator moves upside down and the part is built on it.
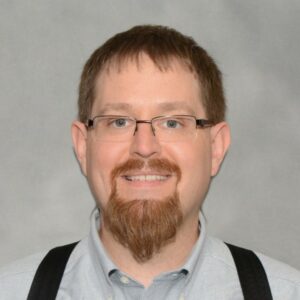
Speaking of examples of AM machines that integrate a recoater, Thomas Spears, Director of AAMT, said [they] “include Electron Beam Melting (such as Arcam) [or] binder jetting (such as ExOne).” “Newer modalities I saw at Rapid+TCT were spreading a ceramic matrix material, photolithography machines like those from 3D Systems, and plastic sintering machines like those from EOS,” he adds.
That said, this article will focus on the use of recoaters in laser powder bed fusion processes.
The importance of recoaters in laser powder bed fusion processes
In case you are new to AM, keep in mind that laser powder bed fusion processes (short for LPBF) work on a basic principle: the use of either a laser or electron beam to melt and fuse the material powder together. More specifically, a layer, typically 0.1mm thick of material is spread over the build platform. A laser fuses the first layer or first cross-section of the model. A new layer of powder is spread across the previous layer using a recoater or a roller. The process repeats until the entire part is fabricated.
Apart from the fact that it lays the powder down uniformly, a recoater helps control the thickness of the powder layer deposition. The recoating speed plays an important role in this process as it may influence the surface morphology of the powder bed which in turn might jeopardize the manufacturing success of the part and the production’s reliability.
The choice of the right recoater, therefore, becomes pivotal as operators may operate their LPBF machines 24/7, with layer changes each minute. That’s the reason why, machine manufacturers are increasingly making their recoating process a competitive advantage.
Types of recoater blades
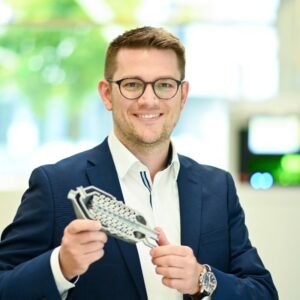
“There are multiple variants of technologies to spread powder in commercial powder-based systems but all of them are referred to as “recoaters”, Michael Wohlfart clarifies from the outset.
Needless to say, peculiarities of some 3D printers may appear as different tools used to spread layers of powder evenly for each layer of a build. “Some manufacturers use a roller to help compact the powder and create a denser and more consistent packing density on the active surface. Velo3D uses a non-contact recoater where they use a vacuum to ensure proper layer thickness,” Spears explains.
One can identify four main types of recoaters. According to Wohlfart, there are:
- Hard recoaters: HSS (high speed steel), ceramic blades
- Soft recoaters: Different types of brushes (carbon fiber, metal), different types of polymer blades (silicone, NBR rubber, other types of polymers)
- Roller recoaters: Primarily used in polymer LPBF but also a niche technology in metal LPBF, especially for fine powders that are difficult to spread.
Contactless recoaters: Niche technology in metal LPBF that allows out-of-plane growth of the application without build interruption but it is typically slow and limited in flexibility (e.g. only one specific layer height). Furthermore, allowing out-of-plane growth is not acceptable for a lot of applications due to tight dimensional tolerances.
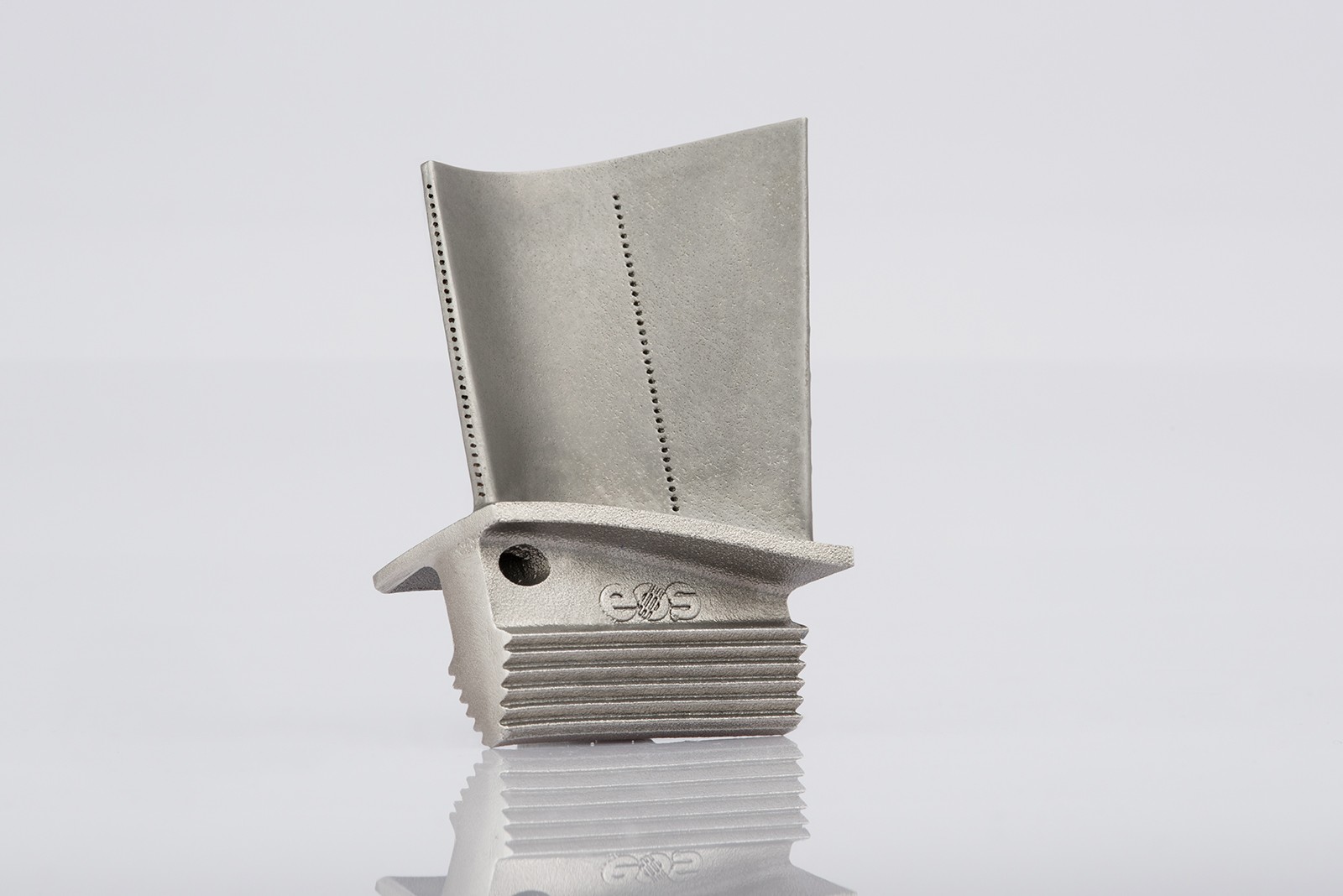
As you will realize in the industry, hard recoaters and soft recoaters are often mentioned as the main types of recoaters. That’s the reason why EOS’ AM expert refers to the two others as niche technology.
From our understanding, hard recoaters are a good deal when fabricating identical parts on the same build platform. They often lead to little part deformation. Obviously, if one part in the build deforms, there are great chances that other parts will deform as well.
On another note, if you’re rather fabricating delicate or different parts at once, you might want to choose a soft recoater. It seems obvious, right? In this specific case, if you are handling a batch of different parts, the deformation of one part does not necessarily lead to the deformation of others – therefore, the build will not pause.
Interestingly, sometimes, these differences are not enough to choose between a hard recoater and a soft recoater.
Some manufacturers will recommend the hard recoater for parts with highest demands given their ability to achieve repeatable quality whereas they will opt for a soft recoater for parts with high aspect ratios and for productions where lead time is more crucial than the risk of imperfections.
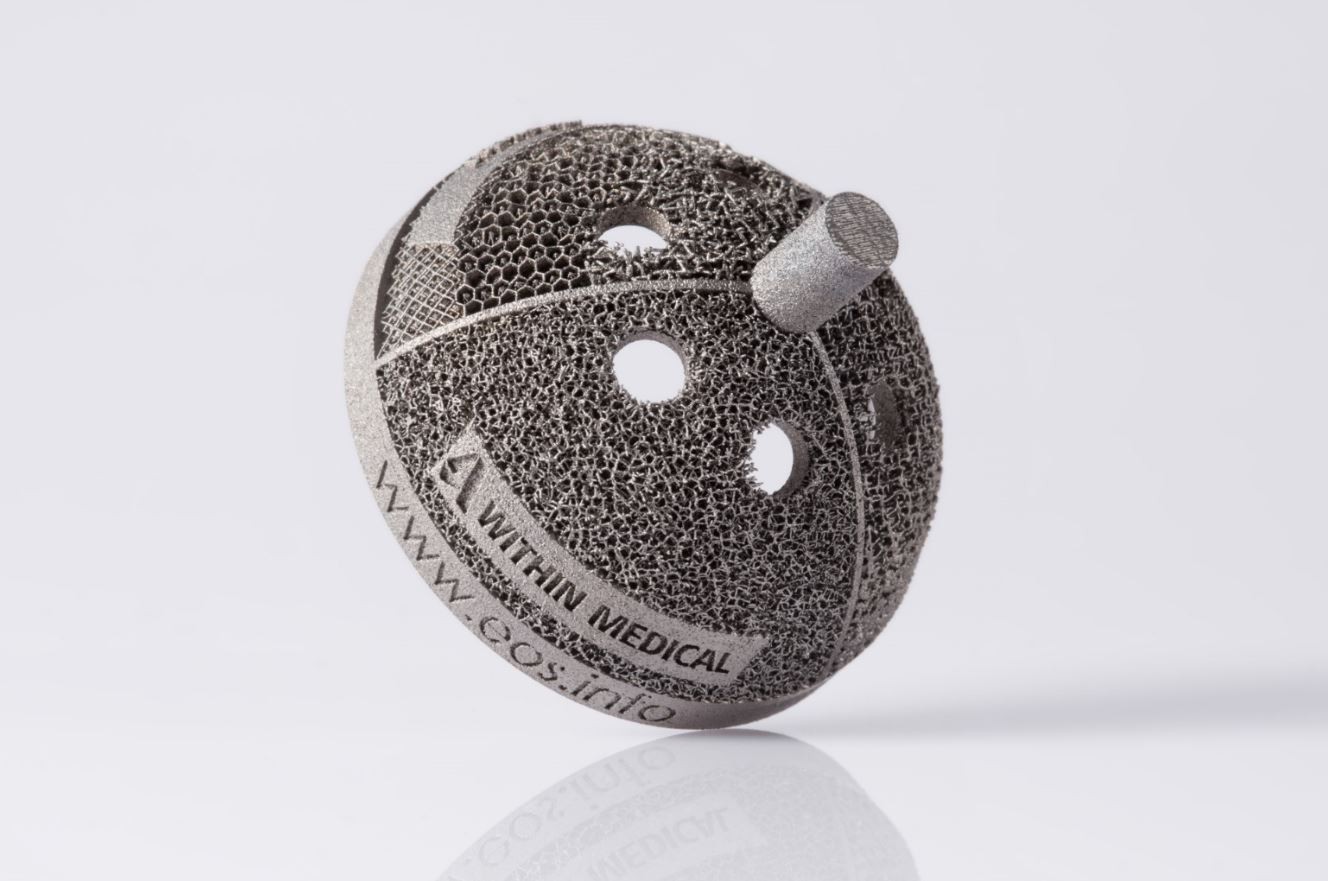
While the machines they build are compatible with both hard and soft recoaters, the Director of AAMT recognizes that “there is an element of subjectivity [when it comes to choosing the ideal recoater]. Some users prefer the forgiveness of the soft recoater while others prefer the consistency of the hard recoater despite its stronger likelihood of crashing due to top surface anomalies or part peel-up. Other process considerations can also dictate recoater type as silicone, carbon fiber brushes, and metal rakes are more appropriate for applications where very fine features are required that may be physically destroyed by a hard recoater making even modest contact with it.”
Wohlfart on the other hand, brings further clarification on the topic:
“The processes for metal and polymer LPBF are fundamentally different and there are no machines on the market that could process both materials in the same system. However, there are still differences between the recoater systems than can be explained by the different material/process requirements but also the geometry to be printed may have an influence on the recoater type.
Polymer systems typically use hard recoaters or roller recoaters, because of the elevated temperature of the powder bed and the different nature of the processes. The shape of the hard recoater blade is typically also different compared to metal recoaters because compaction of the powder bed is more essential for the process.
Regarding hard recoaters for metal LPBF systems, a ceramic blade is required if the material is easily magnetizable (for example maraging steels) otherwise, HSS blades are used. While hard recoaters assure the best repeatability in layer height, soft recoaters are recommended for parts with a high aspect ratio.”
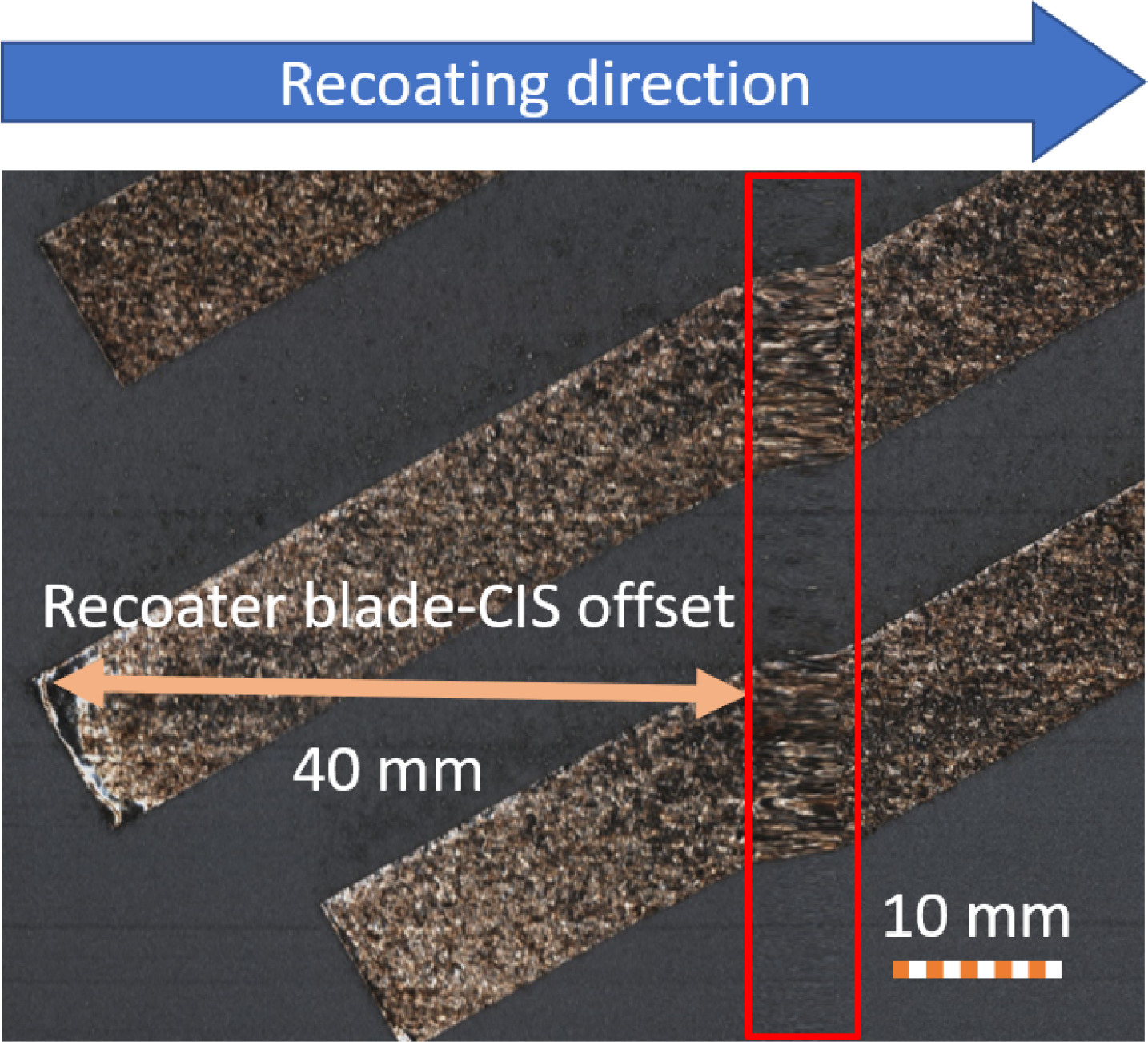
A couple of tips on part positioning
To minimize distortion or failed builds, and to a certain extent, ensure the efficiency of the recoater blade in the long run, the operator should pay attention to part positioning.
In an ideal world, once the recoater has spread a layer of powder, the area of the component built should not move. In practice, depending on many variables, the part could move, leading to a distortion that may apply pressure on the recoater. That pressure could bend or break the component, – or worst scenario, damage the recoater blade.
A correct part positioning may help prevent these issues. For instance, one may avoid having the recoater make simultaneous contact with several 3D printed components at once. The operator can stagger the parts on the build platform to mitigate this risk.
Another example may be to place the tallest parts closest to the recoater. The reason for this is that some 3D printers may require to pause the build, and add powder to build large parts.
On another note, you may not want to place your 3D-printed components directly behind one another. The reason for this is to enable the build to continue if the part or the recoater is damaged.
Last but not least, some part manufacturers increasingly explore the idea of in-situ monitoring of geometric and surface defects in powder bed fusion to monitor the recoating process and prevent issues that may cause a failed build.
A few words on the contributing companies
Open Additive is a manufacturer of metal additive manufacturing (AM) systems, process monitoring solutions, and related products and services. The company is part of the Arctos Group, a premiere applied R&D firm that is setting the flight path for the next generation of aerospace and defense technologies. The company has recently released AMSENSE Chimera with Recoat+ to address recoater issues during the manufacturing process. The new AMSENSE Chimera with Recoat+ offering is specifically designed and tuned to identify recoat process issues common on EOS M400 and M290 machines, providing an affordable 3rd party sensing platform that will increase throughput and decrease build failures on the most critical and widespread LPBF machines in the aerospace market.
EOS is a manufacturing of polymer and metal AM systems. The company provides a wide range of hard and soft recoaters. Depending on the magnetizability, an HSS (standard) or ceramic blade (magnetizable powders) would be used. While they provide their customers with maximum flexibility and openness, the company said the hard recoater configuration is in most cases the preferred option. Their soft recoater types include:
- Two types of polymer blade recoaters: Silicone and NBR for different temperature ranges and stiffness requirements.
- A carbon fiber brush, which is even more forgiving for fragile and high aspect ratio parts than a polymer blade soft recoater. However, if damage to the brush recoater occurs in case of rising edges or out-of-plane growth due to internal stress, it is also more costly to replace this kind of recoater type.
Based on detailed investigations of different recoater types, the company recommends the right configuration based on their use case.
Other references:
The intelligent recoater: A new solution for in-situ monitoring of geometric and surface defects in powder bed fusion; an article written by Matteo Bugatti, Bianca Maria Colosimo.