With a market size of 1.5 trillion U.S. dollars, Fashion is one of the biggest industries in the world. However, the sector is currently facing hard times due to the COVID-19 crisis, as we all are. The pandemic has raised attention to underlying issues that were not previously considered before. Those issues include but are not limited to the delicate and intricate supply chains, the increment of brands’ digital presence, as well as the experimentation with new technologies such as 3D Printing and materials – mainly bioplastics or recycled materials. The article below will discuss the use of 3D printable materials in the fashion industry and this sector’s approach to sustainability concerns.
Enabling wearability and comfort with appropriate materials Fashion is about the joy of self-expression; something that 3D printing users easily understand as the technology enables the freedom of design. By integrating 3D printing into their creative process, fashion designers can create products that enable them to express their mood, interests, and beliefs. To do so, they rely on Computer-Aided Design (CAD) to develop intricate designs that can translate beautifully into a piece that is unique and customizable.
However, one of the biggest concerns raised by 3D Printed Fashion is wearability and comfort. One simply cannot find joy in fashion if an apparel is uncomfortable for the wearer. There are, at least, three paths to 3D Printed Fashion I can identify related to comfort: – Rigidity and structure: The use of materials such as Polylactic acid (PLA), Acrylonitrile butadiene styrene (ABS), and Polyethylene terephthalate (PET) used in Fused Deposition Modeling (FDM) Printing, do not deliver comfort to the wearer, but one can still use them to create interesting wearable pieces. We only need to turn our heads to Cosplay, in which fans usually use these materials to recreate garments from their favourite characters from video games, anime, comics, and more. Another possibility is to use these rigid materials to create, precisely, structure in a garment like a corset. Nevertheless, those rigid materials are not always very comfortable to wear. Another idea is to create other accessories like buttons, embellishments, and trimmings. The following image highlights a corset made by Raquel Banegil mixing bioplastics with PLA boning, as part of her research in the field.
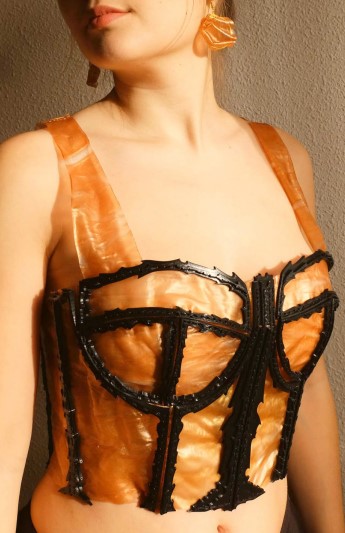
– Concerning flexibility and fluidity. Thermoplastic Polyurethanes (TPU) can play a key role here. Recreus’ FilaFlex, an example of such materials, is a filament used by Danit Peleg in her 3D Printed Fashion collection. This material is easy to work with, can look like fabric and can be breathable for the skin if you control the infill in each piece. Nevertheless, it can feel like plastic to the skin; that is why designers generally use organic fiber textiles like cotton, silk among others, to create linings. A large number of fashion designers and entrepreneurs, including myself, are used to experimenting with this material in the design and manufacture of garments, as seen in the picture.
– Concerning the mix of materials with fabric: This path consists in depositing materials directly to a fabric, like tulle, cotton, or even woven fabrics, to take advantage of both worlds. Fashion designer Julie Daviy’s approach is quite interesting here as she prints in fabrics which, when shrunk allow for incredible volumes in a garment. People and designers are using these three methods to create garments. As materials and technology evolve, there will surely emerge various paths to 3D Printed Fashion.
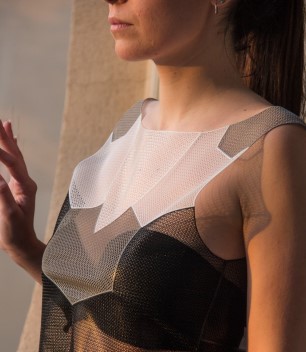
New materials for new needs
3D printing materials are continuously developing, but none of them are specifically designed for the fashion industry, as suggested in the aforementioned three paths that should be taken into account to enable wearability and comfort in 3D Printed Fashion.
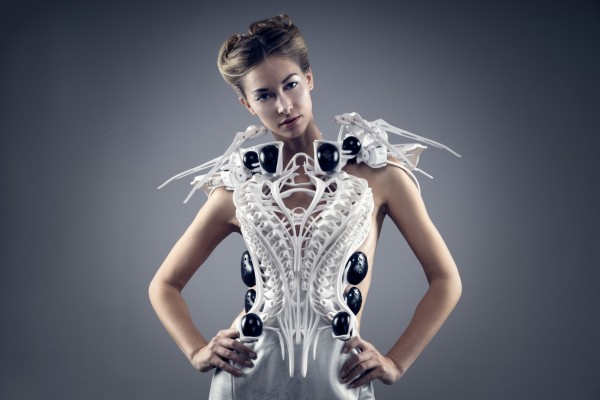
As Susana Marques, fashion designer and researcher in 3D printed textiles, said to an interview for Women in 3D Printing in 2020: “we do not have technology aimed at our industry, materials, printers, software … nothing is developed taking into account the specific needs of fashion, but it is already possible to find very functional solutions”.
When it comes to fashion design using 3D printing, designers have to use their creativity and knowledge to translate materials, software, and printers that are specifically conceived for industries as different as automotive, aeronautics or others, to create solutions that are sustainable, relevant yet fashionable. An interesting branch of fashion is the use of technology and textile to enhance physical capabilities or diminishing them.
Now imagine mixing that branch with Additive Manufacturing. An example of that is the work that Marques is doing on the research of 3D printed textile surfaces for unsighted individuals, in which she is experimenting with tactile and olfactive materials for clothing to reduce the gap between people with disabilities and fashion brands. Biopolymers are another material taking over the fashion industry. Experiments in this area start to question how we consume and produce objects and how we close the loop in the circular economy.
These materials made with alginate, sodium chloride, or gelatine, are under research for many purposes like packaging for example, but in fashion, a great example is Charlotte McCurdy, who created a water-resistant jacket from plastic made of algae. In Spain, Mariel Díaz, CEO of Triditive and Women in 3D Printing’s Ambassador for Asturias, is investigating the use of apple waste in the cider manufacturing process for the creation of 3D printing materials.
According to Mariel in an interview for the newspaper La Nueva España this year: «We have to analyse what type of pieces can be printed with this technique, but it is feasible and we understand that it can be a solution for all this material that is discarded and with which the cider makers may not know very well what to do», with the advantage that those biopolymers are biodegradable synthetic substances. In the same vein, there are already filaments that are compostable, meaning that with the action of certain agents like water, oxygen, microbes, a piece can disintegrate in a short time. As for the combination of bioplastics and Additive Manufacturing, there is still work to be done and research to be made, but a new way of doing Fashion is emerging and surely, we can benefit from a solution that is sustainable and waste-free.
Fashion and Sustainability One of the biggest problems in the Fashion Industry is the pollution created by overconsumption and overproduction. According to McKinsey and Global Fashion Agenda in their report: “The fashion industry accounts for around 4% of emissions globally, equivalent to the combined annual Green House Gases (GHG) emissions of France, Germany, and the United Kingdom. (…) Under its current trajectory, the fashion industry will miss the 1.5-degree pathway by 50%”. We have created a monster that is devouring our planet. Sustainability is surely permeating brands as we as consumers gain awareness of the problem we are generating. Sustainability is now a need more than a trend and more and more brands are taking into consideration the three big pillars in sustainability: people, the planet and profit.
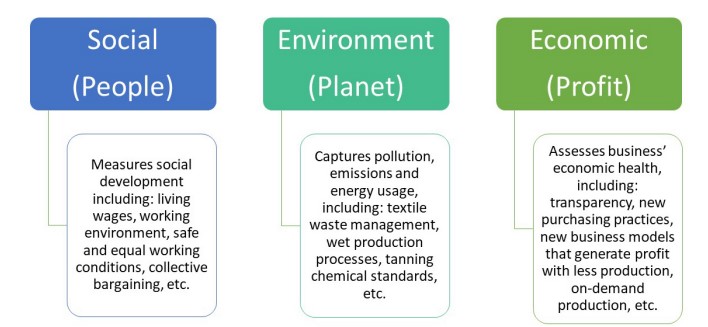
In 2020, Julia Daviy won the gold prize of the Edison Awards with the Organic Skirt Project, defined as “A digitally created and deeply customizable in more than 1,000 variants 3D-printable skirt is the first project uniting different worlds – digital and physical, non-organic and organic, additive manufacturing, and traditional craftsmanship.”
Using a large-format industrial 3D printer, Julia created impressive collections that are similar to traditionally made clothes and with sustainability in mind : a zero-waste approach in the design and printing, an intensive and ongoing research on new materials and processes. Nowadays, in the fashion industry, a brand must be sustainable and all efforts should be made to enhance the way clothing is produced, from the materials we source, to the people that work in our brand. And us as clients, reduce the quantity of clothing we discard.
And…now?
The fashion industry is experiencing structural changes to transform the production processes, the materials sourcing, and the important role workers play in the production of a garment. It is not a mystery that we wear the same clothes as we did centuries ago. Have a look at what you are wearing right now, you can see that little has changed over the years, yet we are still putting the Earth in danger as well as endangering ourselves in the (not-so-)long run.
Technology is here to help us create new paths to change and improve the way we do what we do, and the fashion industry is a major player in our lives, for better or worse. New materials and new technologies such as AM in the fashion industry could and must be the answer to climate change and sustainability concerns.
They should lead to a new set of values revolving around the beauty and joy of self-expression. Now that we’ve gone through the state of 3D printed fashion, let your mind wander about the possibilities of merging Additive Manufacturing and fashion.
This article has first been published in the 2021 September/October edition of 3D ADEPT Mag. It has been written by Andreina Martinez Tancredi; a Women in 3D Printing’s Ambassador for Valladolid, Spain, and a Master Degree candidate in Innovation and Technology in Fashion Design by the Polytechnic University of Madrid, Spain. She has a Degree in Aeronautical Engineering with a focus on Project Management, with more than 6 years of experience in different areas in the civil aviation and automotive industries, such as Risk, Operations, Quality, and Project Management. Currently, she is interested in the mix between Fashion and Technology and their possible contribution to the Aerospace Industry, as well as how Additive Manufacturing can help tackle major issues in the fashion industry.