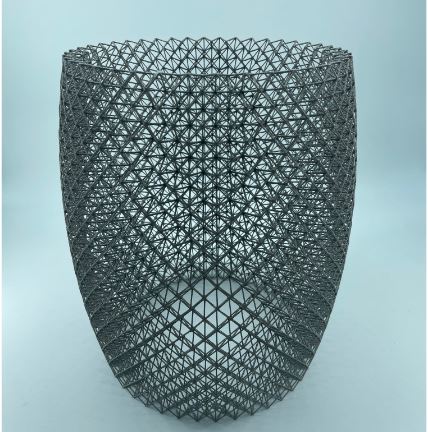
The last time we spoke of the Additive Manufacturing company Wayland Additive it had just launched its metal 3D printer Calibur3 and completed the first sale of the AM system. Now, the company is displaying 3D-printed parts made from difficult to process metals like titanium, carbon steel, and tungsten at Formnext 2023.
The company will be displaying its Calibur3 metal 3D printer in Booth B139 Hall 12 along with an array of 3D printed parts built from the machine.
The Calibur3 metal 3D printer is developed to address the bottlenecks of the metal AM industry. The system uses a metal electron beam (eBeam) powder bed fusion (PBF) technology which helps in the wider adoption of the 3D printer for creating 3D printed parts across sectors. Wayland Additive has developed a fully neutralized NeuBeam® process for the EBM charging along with the ability to process a wider palette of metal materials.
Speaking about NeuBeam®, the CEO of Wayland Additive Will Richardson said: “NeuBeam® unlocks a swathe of complex metal production opportunities that current metal AM processes struggle with. This is because the process is compatible with a much wider range of metal powders, including but not limited to refractory metals and highly reflective alloys”.
“NeuBeam really breaks new ground, with the ability to process existing metal materials, which reduces the pain burden when qualifying new parts”, Richardson added.
The NeuBeam process in Calibur3 3D printers eliminates the residual stress with alternative metal AM processes that can create fully dense AM parts having greater integral integrity. With NeuBeam in place, the entire sinter cake around 3D printed parts isn’t needed. This removes time-consuming and costly post-processing steps.
The company will be demonstrating this residual stress-eliminating hot bed process at Formnext. Incidentally, Wayland calls it a hot part process as high processing temperatures are applied to the AM parts and not the bed, reducing the energy consumption and ensuring free-flowing powder post-build (no sinter cake) and stress-free AM parts.
“On our booth at Formnext visitors will see intricate large parts made from titanium (which when processed using NeuBeam® require no post process heat treatment); carbon steels (the NeuBeam® process enabling the printing of alloys with higher carbon contents that would otherwise crack when printed using existing laser PBF techniques); and fully dense parts in Tungsten (a refractory metal that requires exceptionally high temperatures to melt and which his prone to cracking in any other metal AM process)”, said Wayland Additive CEO.
Remember, you can post job opportunities in the AM Industry on 3D ADEPT Media free of charge or look for a job via our job board. Make sure to follow us on our social networks and subscribe to our weekly newsletter : Facebook, Twitter, LinkedIn & Instagram ! If you want to be featured in the next issue of our digital magazine or if you hear a story that needs to be heard, make sure to send it to contact@3dadept.com