Concrete is so widely used in the building industry that sometimes, one of its key ingredients is missing: sand.
To address this issue, scientists are exploring the possibility of replacing sand with recycled glass in 3D printing – a material that would otherwise end up in landfills if it is not used.
Glass is a material that can be entirely recycled with no reduction in quality, yet it is one of the least recycled waste types. It is made up of silicon dioxide, or silica, which is a major component of sand, and therefore delivers significant untapped potential to be recycled into other products.
That’s the reason why the research team from Nanyang Technological University, Singapore (NTU Singapore) is looking for ways to recycle glass by 3D printing it into items for everyday use.
A new route for recycling glass
For this specific study, glass waste has been fragmented into five different sizes: – coarse, medium, fine, super fine and "moondust". The goal was to replace the sand and gravel which ordinarily serve as aggregate in concrete. That ground glass was then combined with concrete's other two ingredients: cement and water.
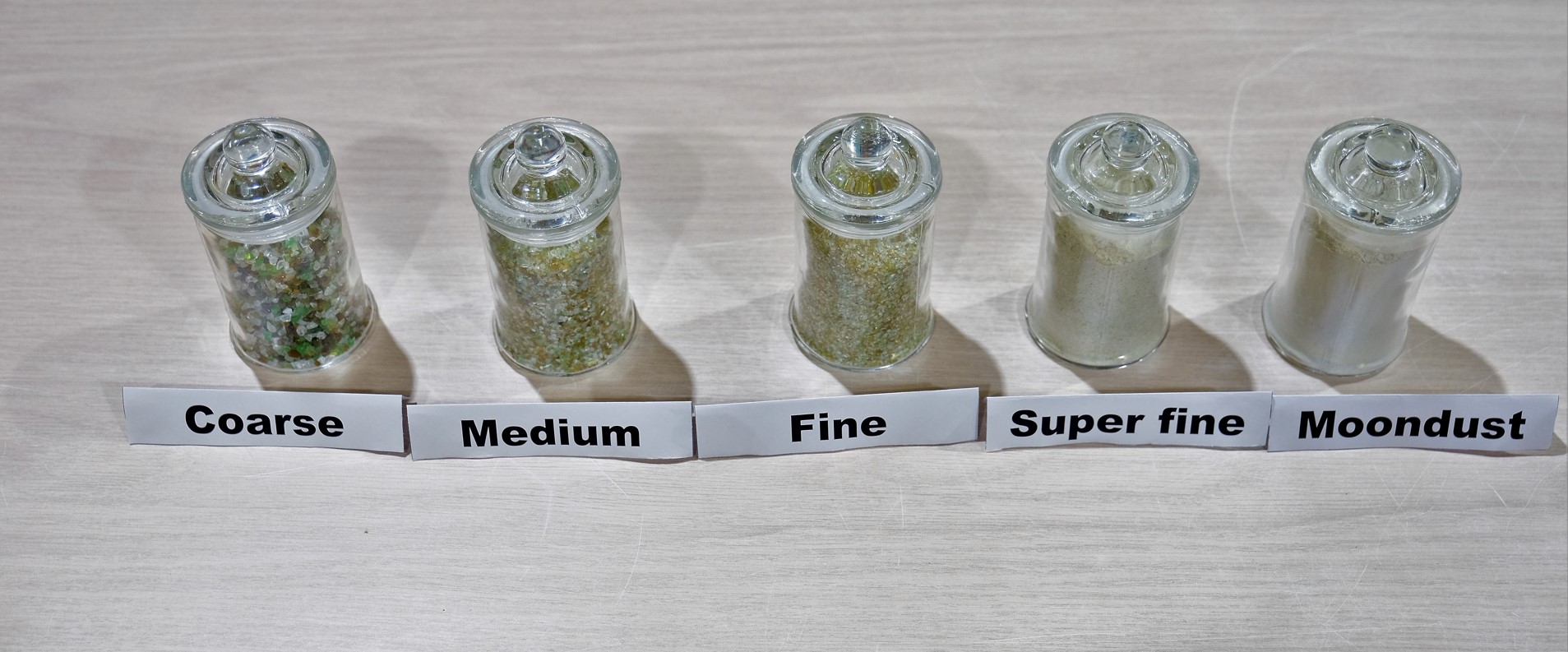
By figuring out the optimal concrete formulation, the NTU research team was able to successfully 3D-print a 40cm tall L-shaped bench as a proof of concept that their material could be 3D printed into an everyday structural (weight-bearing) product.
In lab compression tests and filament quality (strength) tests, the 3D printed structure showed excellent buildability – the printed concrete does not deform or collapse before the concrete cures – and extrudability, meaning the special concrete mix is fluid enough to flow through the hoses and print nozzle.
The printing was then carried out in a single build using a 4-axis gantry robotic printer which has a print volume of 1.2 metre x 1.2 metre x 1 metre. The specially designed concrete mixture was fed to a pump and transported to a nozzle mounted on the robotic arm, depositing the material layer by layer according to the digital blueprint.
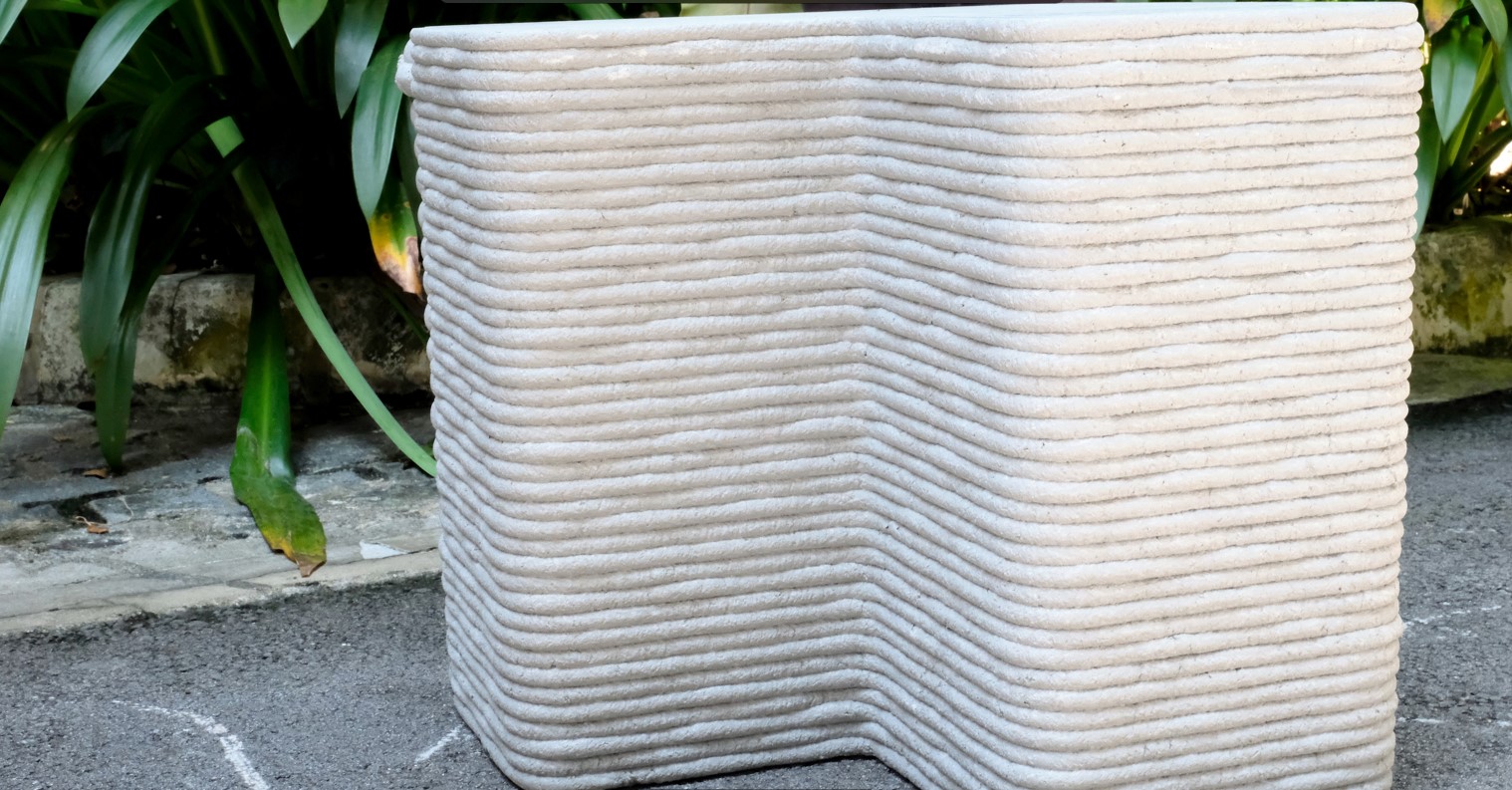
According to the principal investigator of the study Professor Tan Ming Jen of the NTU School of Mechanical and Aerospace Engineering (MAE), “the main challenge in formulating 3D-printable concrete mixtures is to figure out just how much of each component to add to obtain a structurally sound structure with minimal defects.”
However, one of the advantages of using glass is that it doesn't absorb as much water as sand, and less water was required to make the concrete.
"Our research has shown that recycled glass can be used to replace up to 100 percent of the sand in concrete for 3D printing," said the lead scientist, Andrew Ting. "The result is a concrete bench with a mechanical strength that meets acceptable industrial standards. Given that sand is being exploited at a rate much quicker than it can be replenished naturally, the prospect of using recycled glass in building and construction is becoming more attractive."
Moving forward, the NTU research team, in collaboration with Singapore start-up company Soda Lemon, will look at 3D printing larger scale and more diverse structures using the recycled glass concrete mix, and to optimise the printing algorithm for consistent performance.
Remember, you can post job opportunities in the AM Industry on 3D ADEPT Media free of charge or look for a job via our job board. Make sure to follow us on our social networks and subscribe to our weekly newsletter : Facebook, Twitter, LinkedIn & Instagram ! If you want to be featured in the next issue of our digital magazine or if you hear a story that needs to be heard, make sure to send it to contact@3dadept.com