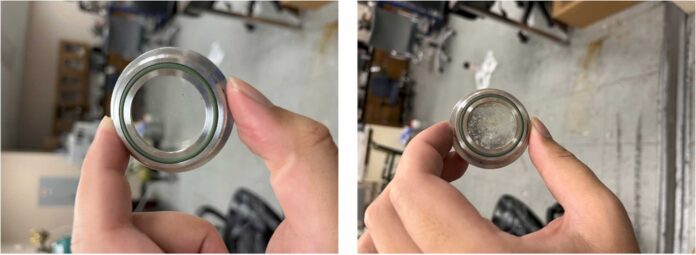
The research has been conducted by Yehong Chen, Congyuan Zeng, Huan Ding, Selami Emanet, Paul R. Gradl, David L. Ellis, Shengmin Guo affiliated to Louisiana State University, Southern University and A&M College, NASA Marshall Space Flight Center & NASA Glenn Research Center.
Remember the copper alloys GRCop-84 (Cu-8Cr-4 Nb at%) and GRCop-42 (Cu-4Cr-2 Nb at%) developed by NASA? The materials recognized for their high thermal conductivity and high mechanical properties at elevated operating temperatures have recently been studied as part of a research project.
Due to the fact that L-PBF parameters and resulting microstructures do not always translate well into a production environment, it is crucial to understand the variations across multiple machines and powder chemistries to achieve industrial 3D printing applications for highly-regulated sectors. The research study therefore focuses on thermophysical property variations that can be used to establish process capabilities and design guidelines for ongoing commercial use and further research.
GRCop-84 and GRCop-42
Designed to achieve regeneratively cooled rocket engine combustion chamber liners, the matrix of these alloys is nearly pure copper, hence the electrical and thermal conductivity. GRCop-84 particularly, can deliver microstructural stability, creep resistance, good thermal conductivity, good low cycle fatigue life, and high tensile strength that are optimized for 500–800 °C.
The problem is, since most materials expand upon heating, this thermal expansion can cause three issues for rocket engine liners:
- Thermally induced stresses: the liner is typically constrained by a high-strength jacket that remains relatively cool. The liner cannot expand freely and the thermal expansion results in thermally induced stresses.
- The permanent deformation of the material from these thermal stresses that can permanently change the shape of the liner. This can include the so-called “doghouse” effect [28] that can contribute to failure in the hot wall within a cooling channel.
- Low cycle fatigue (LCF), where a combustion chamber liner is repeatedly cycled for qualification or operation. The liner will be subjected to repeated strains locally from thermal expansion that can exceed 1%. This is one of the major contributors to liner failure
To achieve the desired microstructure, thermophysical properties, and mechanical properties, GRCop alloys require high cooling rates during solidification.
In this study, GRCop-42 and GRCop-84 copper-alloy feature build plates were produced by eight different vendors utilizing the Laser Powder Bed Fusion (L-PBF) process. Each vendor employed their specific L-PBF machines and slightly different parameters, often considered proprietary, to manufacture the plates. Equations were therefore developed over the temperature range of 25–700 °C to predict thermal conductivity and 20–1000 °C for CTE (average and instantaneous).
Key takeaways
With different powder sources and different L-PBF systems/parameters, the variations of GRCop thermal conductivities are up to about + /- 4% of the mean value, which is slightly higher than the equipment uncertainty associated with the thermal conductivity measurements (+/- 3%). These small variations could be explained partially by the difference in contents of alloying elements.
The results for thermal expansion, average CTE, and instantaneous CTE all show excellent agreement between samples with very small variations in the values as exemplified by the small standard error of estimate. Based upon these results, the thermal expansion properties of AM GRCop-42 and GRCop-84 have excellent reproducibility regardless of starting powder, parameters, or machine.
The results demonstrated that thermophysical properties of GRCop-42 and GRCop-84 alloys produced with L-PBF demonstrate highly repeatable results independent of processing parameters, powder feedstock differences, and machine type. This implies consistency within parts and between parts and provides designers higher confidence in meeting design minimum values during the manufacturing process, which means increased reliability and risk reduction.
The thermal conductivities of the GRCop-42 samples exhibited a variation of ± 4%, which marginally surpasses the inherent instrument variability of ± 3%. This additional variation between samples, exceeding the known instrument variability, could potentially be associated with the amounts of solute atoms dissolved in the Cu matrix. While no explicit correlation was identified, it was demonstrated that these elements could be significant factors. Further research, employing comprehensive atomic-scale and micro-scale studies, is required in the future to fully elucidate the variations in thermal conductivity.
For the AM GRCop-42 and GRCop-84 thermal expansion samples, the AM L-PBF thermal expansion behavior was statistically significantly different from the extruded material but was consistent for each alloy. The mostly lower thermal expansion would result in lower thermally induced stresses, less permanent deformation from thermally induced strains, and longer LCF lives.
It is important to recognize that while L-PBF parts can be successfully built in a controlled laboratory setting, the translation to a production environment is not always seamless. The presence of variations across many machines and powder lots necessitates a comprehensive understanding of the variability of properties across multiple vendors operating independent of each other. The repeatability and reproducibility throughout the commercial supply chain holds paramount significance for designers aiming to ensure that parts align with expected properties and operational requirements. Specifically, the thermal conductivity and thermal expansion emerge as crucial in the design process. By leveraging the knowledge of variations in thermal properties, it becomes possible to establish process capabilities and design guidelines that facilitate ongoing commercial utilization and further research endeavors.
You can read the entire research here.
Remember, you can post job opportunities in the AM Industry on 3D ADEPT Media free of charge or look for a job via our job board. Make sure to follow us on our social networks and subscribe to our weekly newsletter : Facebook, Twitter, LinkedIn & Instagram ! If you want to be featured in the next issue of our digital magazine or if you hear a story that needs to be heard, make sure to send it to contact@3dadept.com