Two days ago, the Maritime and Port Authority of Singapore (MPA) officially launched Singapore’s first Maritime Drone Estate (MDE), in conjunction with the 15th Singapore Maritime Week. While the MDE provides a conducive space to test bed and develop drone technologies for maritime applications (e.g.: shore-to-ship deliveries and remote ship inspections), it also allows companies such as Wilhelmsen and thyssenkrupp to showcase their additive manufacturing expertise.
What started as a collaboration in January 2020, for the production of 3D Printed parts for the maritime industry ended up in a 3D printing joint venture targeting the maritime industry in September 2020; a sign that both companies had understood the value they could bring to this vertical industry that has just started exploring the use of AM.
In this newly created joint venture, thyssenkrupp brings its expertise in additive manufacturing on the table while Wilhelmsen brings a long standing maritime service and supply know-how. Anyway, during the MDE day, the Wilhelmsen and thyssenkrupp joint venture successfully digitized, printed, tested, and delivered a cooling water pipe connector on behalf of Kawasaki Heavy Industries. In collaboration with Singaporean start-up, F-Drones, the part was delivered via drone to MMA Offshore’s vessel.
It should be noted that the part was developed as part of the Joint Industry Program on Additive Manufacturing in Singapore with the Wilhelmsen-led consortium awarded funding by the Maritime and Port Authority of Singapore (MPA) under its Maritime Innovation and Technology (MINT) Fund.
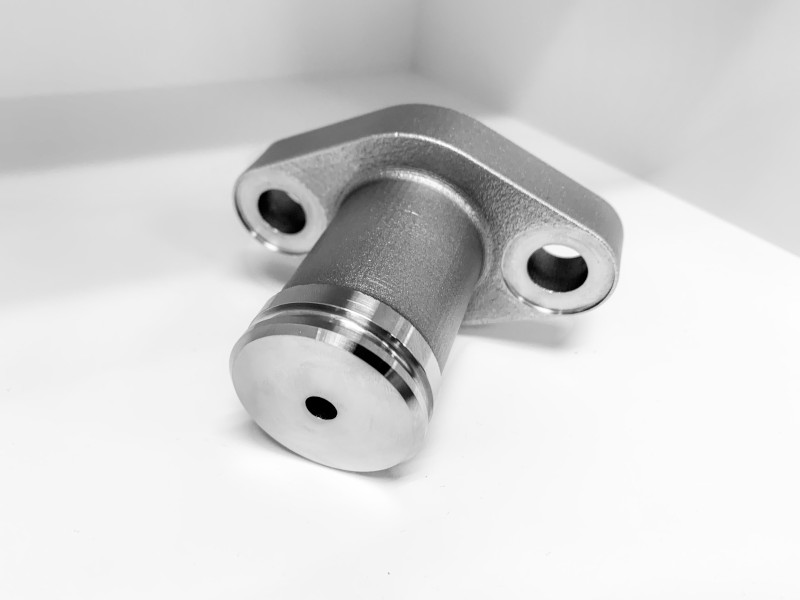
As a reminder, the consortium includes original equipment manufacturers Wärtsilä, Kawasaki Heavy Industries and Hamworthy pumps, independent assurance and risk management expert DNV, technology partners thyssenkrupp, Ivaldi Group and Tytus3D, and a number of forward leaning end users, already a part of Wilhelmsen’s 3D printing programs.
“We are honored to be on this journey with Kawasaki Heavy Industries who have entrusted us not only with their valuable IP, but the confidence for us to deliver successfully. We believe this is a true testament that the venture has the right ingredients for success. We will continue to provide this same level of accomplishment to our ever-expanding list of OEM partners,” says Kenlip Ong, Head of Additive Manufacturing Tech Centre, thyssenkrupp.
The Wilhelmsen thyssenkrupp company holds an “AM fulfillment platform” that currently serves over 3,000 vessels from key locations across the world. The companies explain that this platform aims to address and solve some of the biggest pain points such as, long lead time, part obsolescence, poor part performance and high carbon footprint, through on-demand manufacturing.
To this end, the collaboration with Original Equipment Manufacturers (OEMs) is inevitable as it is a pivotal step to help them reduce their supply chain costs and improve customer experience through increased serviceability, with shorter delivery times in key locations.
“We are excited to once again share an excellent use case presented by additive manufacturing, where OEMs and end users are experiencing a solution that is faster, better, and more sustainable – through on-demand manufacturing close to the point of need. The future of supply chain is now, and we are continuously expanding our service to key locations worldwide,” says Hakon Ellekjaer, Head of Venture, 3D Printing, Wilhelmsen.
Lastly, as the use of AM in the maritime industry is still nascent, this 3D printed cooling water pipe connector gives a first good idea of the way AM can impact production in this industry.
Remember, you can post job opportunities in the AM Industry on 3D ADEPT Media free of charge or look for a job via our job board. Make sure to follow us on our social networks and subscribe to our weekly newsletter : Facebook, Twitter, LinkedIn & Instagram ! If you want to be featured in the next issue of our digital magazine or if you hear a story that needs to be heard, make sure you send it to contact@3dadept.com