All the memories and feelings linked to a specific event or person easily dredge to the surface when one listens to a piece of special music. We do not always realize that the most important part of this experience relies on an audio system, but not just any audio system. A high-performance speaker that creates or recreates an environment encompassing comfort, acoustics, and system performance – “as if the artist was in the room”.
Amid the high-performance speakers that might be found on the market, a new collection is increasingly drawing the attention of both music lovers and tech enthusiasts: the HYLIXA speakers. From our perspective, the reason seemed pretty simple: their manufacturing requires the utilization of additive manufacturing technologies but a conversation with David Evans, Director of Node, shows that it is more than that.
Node is a Cambridge-based company founded by Ashley May and David Evans with the ambition to push the boundaries of audio design. Both founders are industrial designers who have worked together in the past ten years in a product design consultancy called Studio 17.
“We’ve always wanted to design and develop our own products. We always thought about that from the start. The concept of the speakers came from my business partner’s passion for High Fidelity audio and our willingness as designers to understand the possibilities of AM. It’s almost like a blank piece of paper for a designer because you are used to manufacturing products in a particular way and suddenly, this process takes away all these restrictions while highlighting the benefits of doing them differently. That’s when the concept of what we could do with loudspeakers’ design came from”, Evans explains from the outset.
If their speakers require the use of AM in the manufacturing process, this was not the first time that Evans and May experienced the technology. They started using AM as part of some other projects for prototyping and production parts. However, the challenge with the HYLIXA speakers was quite different. It was not only about using AM, it was also about proving the feasibility of the concept at the audio level.
“So, three or four years ago, we approached a local acoustic engineer and we discussed the concept initially and our need to leverage AM technologies as part of the manufacturing. We saw an opportunity to do something that had not been done before; an opportunity to create the performance and quality of speakers that should normally be bigger than what we used to see on the market. But what we wanted to create was meant to be in a very smaller size and obviously, with a more attractive design”, the industrial designer adds.
The manufacturing perspective
A quick look at the design of the HYLIXA speakers reveals a unique form of sculptures that would reproduce vocals that sound true to life. In addition to acoustic engineering and design engineering, Evans outlines the crucial role of materials in the manufacturing process.
The team achieved the design phase through Solidworks and got access to a 3D Systems Pro 60 SLS printer that is onsite for the fabrication. “In the prototyping stage, we tested which material was more suitable for the closure. For the main part of the speakers, the main cabinet, we used a DuraForm GF Nylon material which does not only work well structurally, it also works well acoustically. Although the parts were mainly laser sintered, we did use other types of AM technologies. We also produced some Nylon parts on an HP machine for the base and the crossover. With every single component, there was a reason to use AM as in the end, we could testify that every 3D printed part could provide a new functional benefit” Node’s director points out.
Crossover
As far as the cabinet is concerned, we learned from Evans that the material used, enhanced the properties of the part and delivers a surface finish that is machinable and paintable. With its ceramic-like quality to the touch, it helped produce a 3D printed part that delivers a density and a high resonant frequency that enables to play the bass frequencies without they resonate at the operating band.
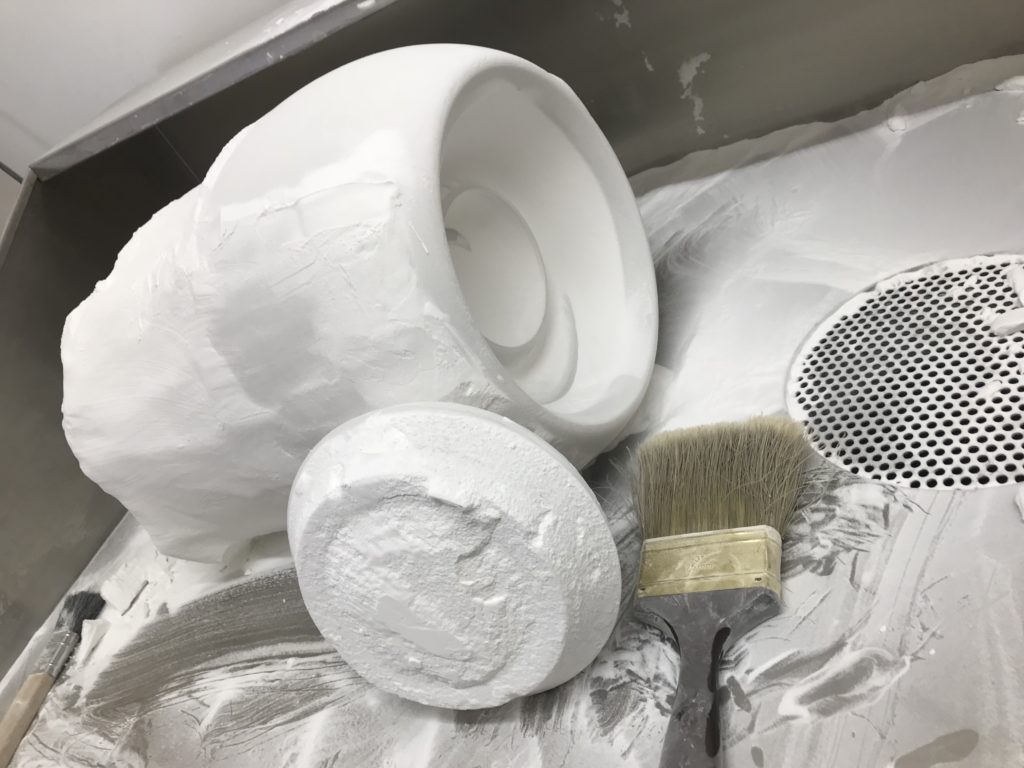
While the laser sintering process highlights the complex geometries of the design, it should be noted that the rounded cabinet has been produced in a single piece, therefore, there is no disruption to sound accuracy.
However, one of the main important challenges the team encountered during the fabrication was the post-processing stage, and that’s an area they would like to see manufacturers of AM technologies and related equipment improve in the long-run.
For the helix of the HYLIXA speakers for instance, when the part came out of the 3D printer, they needed to ensure that no unsintered powder was left inside. “To make sure that we had removed all powders of certain parts, we used an endoscopic camera to inspect all angles of the inner part and [performed a well thought out post-processing job] in order to prepare the surfaces for the desire finishing stage”, Evans notes.
On the other hand, the industrial designer notes that the use of appropriate and custom materials played an important role in the development of their product, yet they “remain quite expensive; which in the end, drives the cost of the final product.”
The market perspective
So far, reviews on many HiFi music gear sites we have checked acknowledged HYLIXA as an aesthetically unique compact system that might change the way one enjoys music but the best experience is certainly the holistic one. In this vein, prior to receiving their products, customers are most welcome to take a tour of the company’s site in Cambridge – or in Shanghai and Tokyo via their partners to either see the production process they go through or experience the HYLIXA uniqueness.
This makes more sense when we know that the speakers are only produced on-demand and for “a new business, it is the most cost-effective way to produce and proceed, not to mention it opens up more possibilities for the customization of the surface finishing.”
Available at a starting price of £30,000 (approximately $39,000 = €32135) – metallic and paint finishes being customizable based on the customer’s preferences, we will not doubt the competitive edge of the HYLIXA made possible through the use of additive manufacturing technologies.
Both founders have distinguished themselves from what we used to see in the standard HiFi industry by delivering “performance in a smaller tailor-made device”.
Main specifications of the HYLIXA speakers
- Type: 3-way transmission line loaded, floorstanding loudspeaker
- Tweeter: 19mm ring radiator
- Midrange driver: 46mm BMR
- Bass driver: 140mm cone
- Recommended amplifier power: 50W – 150W
- Sensitivity: 82.4dB
- Nominal impedance: 6Ω (2.6Ω minimum)
- Frequency response (-6dB): 39Hz-25kHz in room
- Connectors: silver-plated copper binding posts / 4mm banana plugs
- Dimensions (HxWxD): 960 x 433 x 278mm
- Weight: 15 kg including stand
Remember, you can post job opportunities in the AM Industry on 3D ADEPT Media free of charge or look for a job via our job board. Make sure to follow us on our social networks and subscribe to our weekly newsletter : Facebook, Twitter, LinkedIn & Instagram ! If you want to be featured in the next issue of our digital magazine or if you hear a story that needs to be heard, make sure to send it to contact@3dadept.com