Deux (anciens) cyclistes de compétition, Jules de Cock et Noah van Horen ont toujours été intrigués par les facteurs qui influencent une course cycliste. Ils ont fondé SPEECO pour explorer des solutions qui amélioreront l’expérience cycliste des professionnels et des passionnés du domaine. Au cœur de SPEECO, il y a la production de guidons de vélo personnalisés à l’aide d’imprimantes 3D. Dans cette chronique invitée, Noah van Horen et Thom Spermon, ingénieur en fabrication mécanique, relatent cette expérience vécue par les cyclistes, les raisons pour lesquelles l’impression 3D entre en jeu, les avantages mais aussi ce qu’ils souhaitent améliorer.
Les produits personnalisés sont courants dans le cyclisme sur route depuis les premiers jours. Pendant de nombreuses années, les coureurs professionnels avaient leur fabricant de cadres préféré qui soudait quelques cadres pour eux chaque année, qui étaient ensuite repeints aux couleurs et aux autocollants du sponsor de l’équipe.
Pour empêcher les coureurs de bénéficier d’avantages injustes grâce à des composants personnalisés inaccessibles, l’Union cycliste internationale (UCI) a introduit en 1997 des règles sur la commercialisation obligatoire des composants et l’homologation supplémentaire des cadres et des roues. Cela signifie que tous les composants utilisés dans une course doivent être disponibles pour un client dans un délai de 3 mois, et que les cadres et les roues doivent avoir toutes les tailles et variations autorisées par l’UCI.
Les produits personnalisés ont disparu et des percées ont été réalisées dans la production en série de cadres composites qui s’adaptent à un éventail aussi large que possible de personnes, en réduisant au minimum le nombre de moules et de processus différents. Jusqu’en 2015, lorsque l’équipe Sky a fourni à Bradley Wiggins (cycliste professionnel) un ensemble d’extensions de contre-la-montre en titane, imprimées en 3D, qui soutiennent et enferment ses avant-bras dans une position aérodynamique, pour sa tentative de record de l’heure.
En 2017, l’ensemble de l’équipe sponsorisée par Sky a roulé sur des extensions de chrono imprimées en 3D personnalisées, et bientôt le reste du peloton n’a pas pu rester derrière.
La société néerlandaise qui fournit des barres d’accélérateur Speedbar™ a ensuite suivi la même voie, en fabriquant à la main des extensions de chrono personnalisées pour la tentative de record du monde du cycliste belge Victor Campenaerts, puis en les fournissant pour les « courses normales » par la suite.
L’unicité de Speedbar™ réside toutefois dans l’utilisation d’un matériau relativement moins cher, la fibre de carbone, mais d’un processus beaucoup plus laborieux impliquant des moules faits à la main. Il en résulte que les options en titane et en fibre de carbone ne sont pas à la portée de la plupart des coureurs (4 500 à 8 000 euros).
Nous pensons qu’il existe un juste milieu. Lorsque Jules de Cock, le cofondateur de SPEECO, a réalisé son projet de fin d’études dans le domaine de la fabrication de composites « standard », il a pu commencer à concevoir et à tester différents processus. Après quelques mois, nous avons été en mesure de fabriquer un produit final en fibre de carbone à partir de simples moules imprimés par FDM.
Pour réduire davantage la main-d’œuvre, nous avons pris deux nouveaux coureurs et examiné les variations possibles entre leurs besoins individuels, puis nous avons développé une conception paramétrique pour les extensions d’essai. Il était désormais possible d’obtenir les dimensions de coureurs qui n’étaient pas près de nous ou même sur le continent, de les entrer dans le modèle, de leur envoyer un simple échantillon imprimé en FDM PLA pour qu’ils l’examinent et donnent leur avis, puis de leur fabriquer un produit final en fibre de carbone, tout en réduisant la main-d’œuvre au minimum.
Ce processus a maintenant été étendu à trois produits différents, et d’autres produits seront lancés cet été. Pour les nouveaux produits, nous collaborons avec un pionnier de la discipline pour développer un produit parfaitement adapté, puis nous paramétrons le modèle et le vendrons dans le monde entier.
Images via Speeco
Bien que cela fonctionne, il est encore possible d’améliorer et de mettre en œuvre davantage de technologies additives.
Ce que nous voulons réaliser à l’avenir
Nous avons déjà parlé du travail accompli, mais nous voulons aussi regarder vers l’avenir. Tout en perfectionnant nos processus actuels, nous recherchons et développons également de nouveaux produits. Dans le processus de production actuel, la main-d’œuvre est encore très présente.
Une façon de surmonter ce problème serait d’automatiser davantage de parties du processus en intégrant différentes parties du produit final dans une impression plus grande et en gagnant du temps sur l’alignement. En raison de la complexité des pièces, cela nécessiterait une nouvelle approche du processus FDM, une approche dans laquelle le processus est élevé à un véritable processus 3D dans lequel la tête d’impression se déplace sur tous les axes en même temps, ce qui garantit une meilleure finition dans laquelle l’étagement ne sera pas aussi présent. Ce procédé pourrait être réalisé avec une configuration similaire à celle de la plupart des imprimantes 3D actuellement sur le marché, ce qui le rend accessible dans un avenir proche.
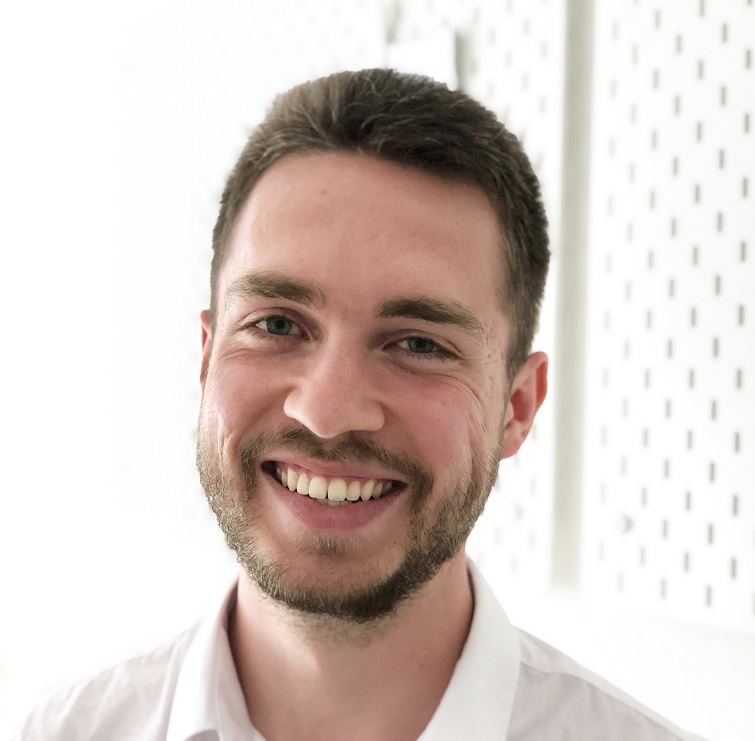
Une autre approche pourrait être d’utiliser un bras de robot d’une manière similaire à WAAM, avec un refroidissement adéquat, ce qui permettrait d’imprimer des formes très complexes. Dans une telle configuration, il serait également possible d’intégrer un processus multi-matériaux qui permettrait d’imprimer du TPU dans le guidon, ouvrant ainsi un nouveau champ de possibilités pour la personnalisation des produits.
Une autre solution qui nous vient à l’esprit pourrait être d’utiliser un matériau chargé qui permettrait d’éviter la stratification du carbone ou du moins une partie du processus de stratification. Il existe déjà un grand nombre de matériaux chargés en carbone et en kevlar sur le marché, avec toutes sortes de matériaux de base différents pour l’impression. Ces matériaux permettent de produire des pièces très durables dans différentes applications (industrielles), mais l’un de leurs inconvénients est qu’ils nécessitent généralement un remplissage important, voire une impression solide, pour garantir leur rigidité et leur résistance. Les produits que nous fabriquons actuellement exigent un certain degré de légèreté et, dans la plupart des cas, un moyen de faire passer les câbles à l’intérieur. Ces deux exigences rendent plus difficile la fabrication de pièces d’utilisation finale par impression.
Un autre point crucial est la résistance des pièces imprimées par FDM en fonction de l’orientation, même s’il existe des moyens d’améliorer ce point, il est difficile de le surmonter. La charge dynamique produite par le coureur sur les pièces, surtout pendant une course, peut être très dure. Lors d’une course, il arrive souvent que les coureurs roulent ensemble à grande vitesse, les conséquences d’une chute dans un tel moment sont énormes. Cela signifie qu’il est de la plus haute priorité que les pièces soient capables de supporter ces charges.
La structure de la fibre de carbone et celle des tapis de kevlar assurent la minimisation du risque d’une défaillance du produit mais une telle structure et assurance est difficile à reproduire avec la seule impression 3D.
L’innovation dans l’industrie de l’impression 3D est si rapide que les possibilités de produire des pièces de cyclisme à usage final se rapprochent chaque jour.
Nous nous concentrons actuellement sur la production de guidons et d’extensions de guidon, mais l’impression 3D offre bien d’autres possibilités.
Trop d’équipements sportifs ont été standardisés au fil des ans, créant des produits qui conviennent presque à tout le monde, mais qui en réalité ne conviennent à personne. L’utilisation des technologies additives offre la possibilité de changer radicalement cette situation et nous sommes impatients de voir où cela nous mènera.
Par Noah van Horen et Thom Spermon
Cet article a premièrement été publié dans le numéro de Mars/Avril 2021 de 3D ADEPT Mag.