Rösler, a machine manufacturer that specializes in surface preparation and surface finishing, recently launched a programme aimed at improving the performance, efficiency, and longevity of existing shot blasting and mass finishing systems.
What does the process look like?
The process begins with a thorough inspection of the equipment and an evaluation of the production process. In-depth consultations with the client follow this assessment to identify enhancements tailored to their specific operational needs.
Several factors influence the approval decision, including the overall condition of the equipment. If a machine is in poor condition, a full replacement may be the better option. The availability of replacement components is another consideration, as some obsolete parts may be difficult to source, making retrofitting less viable. Finally, the potential for performance gains plays a crucial role. If significant enhancements can be achieved, retrofitting becomes an attractive and practical solution.
Once the proposal is approved, the necessary components are designed, manufactured, and installed by Rösler’s skilled engineers. Finally, the upgraded system is fine-tuned for optimal performance during the commissioning phase, and operators receive training to ensure seamless integration. As Chris Kershaw, Digitisation and Automation Manager (Service) at Rösler UK describes, “After an initial discussion, a site visit and equipment evaluation will be undertaken, followed by an open discussion around the options available and the benefits that could be delivered.”
Advantages of retrofitting over a new purchase of equipment
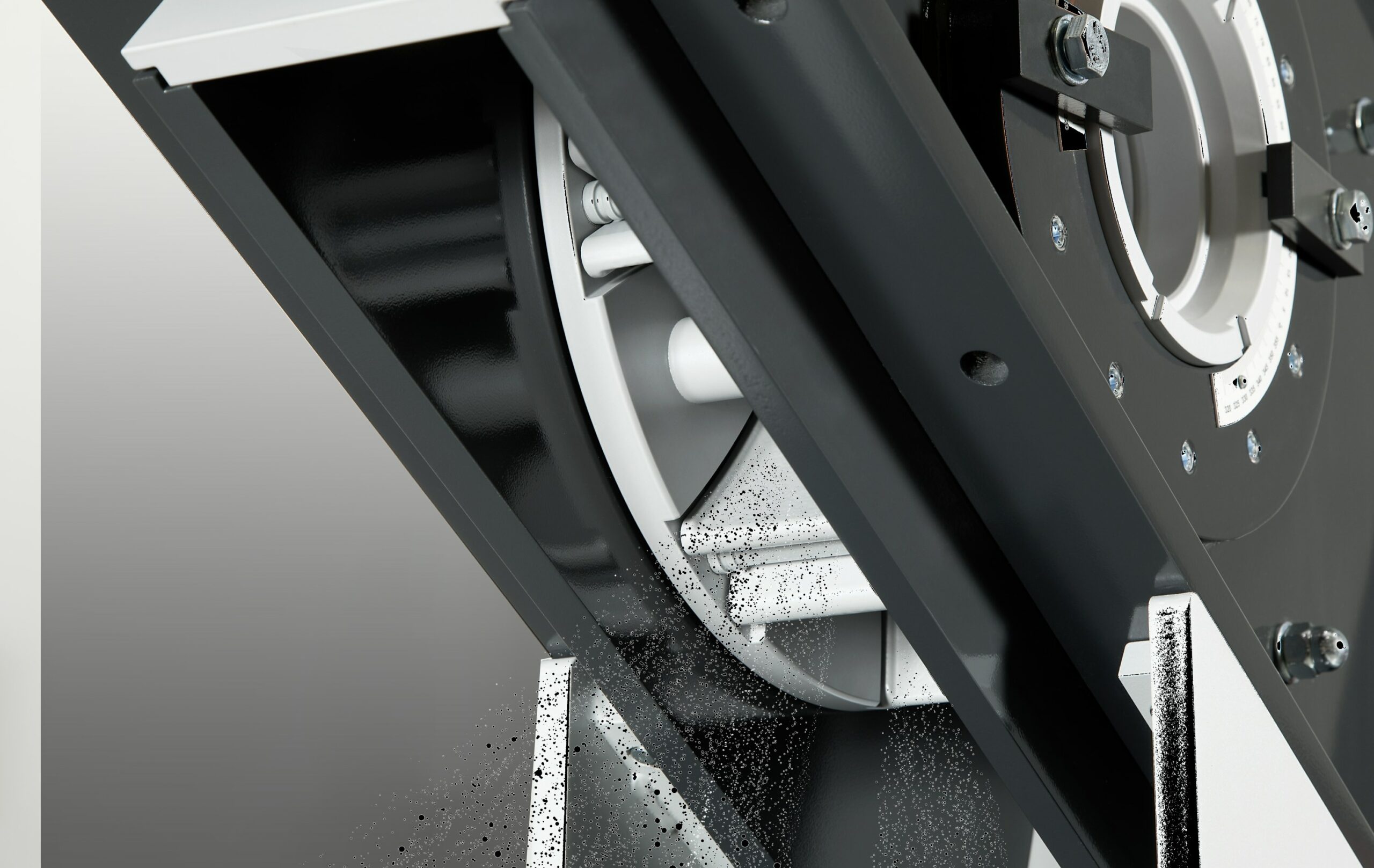
One of the most significant benefits is cost savings, as retrofitting often costs significantly less than acquiring new equipment.
Minimized disruption: replacing large shot blasting installations can be costly and disruptive. Many older machines still in operation can benefit from control system enhancements, such as replacing outdated PLCs and HMIs with modern alternatives that improve usability and reliability.
Enhanced performance: Advanced blast wheels and modern control systems can greatly boost equipment productivity. Rösler’s Gamma blast wheels, for example, provide energy savings between 10% and 25% while increasing blasting performance by up to 77%, leading to reduced cycle times.
Reduced downtime and maintenance costs: Obsolete components can be a major source of unexpected breakdowns, but modernizing control systems and upgrading core components significantly enhance reliability.
Common technological upgrades
One of the most impactful improvements is blast wheel enhancement, where outdated blast wheels are replaced with high-performance models like the Gamma series, which improve energy efficiency and processing speeds. Control system modernisation is another critical upgrade, with modern PLCs and HMIs enhancing usability and reducing the risks associated with obsolete components. The integration of automation into existing systems is increasingly popular, as it minimizes manual intervention, enhances efficiency, and allows skilled labor to be used in other key functions.
Words: Colin Spellacy, Head of Sales, Rösler UK / AM Solutions – Images credit: Rösler.
Remember, you can post job opportunities in the AM Industry on 3D ADEPT Media free of charge or look for a job via our job board. Make sure to follow us on our social networks and subscribe to our weekly newsletter : Facebook, Twitter, LinkedIn & Instagram ! If you want to be featured in the next issue of our digital magazine or if you hear a story that needs to be heard, make sure to send it to contact@3dadept.com