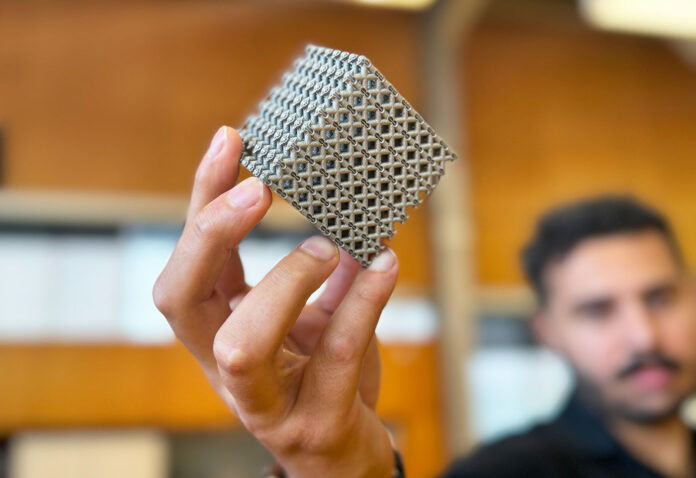
This title looks like the beginning of a Sci-Fi book but it is not. Researchers from Australia-based RMIT have developed a new metamaterial – a term used to describe an artificial material with unique properties not observed in nature – from common titanium alloy.
Tests show it’s 50% stronger than the next strongest alloy of similar density used in aerospace applications.
The key is the material’s unique lattice structure design
This development is a great reminder of how nature can inspire 3D printing advancement. In this specific case, lattice structures made from hollow struts were originally inspired by strong hollow-stemmed plants like the Victoria water lily or the hardy organ pipe coral (Tubipora musica) which combine lightness and strength.
To adapt this material to AM, the challenge lied in replicating these hollow ‘cellular structures’ in metals. RMIT’s Distinguished Professor Ma Qian explains that the stress in all complex cellular materials should be evenly spread. “However, for most topologies, it is common for less than half of the material to mainly bear the compressive load, while the larger volume of material is structurally insignificant.”
That’s where metal 3D printing comes in.
“We designed a hollow tubular lattice structure that has a thin band running inside it. These two elements together show strength and lightness never before seen together in nature,” said Qian. “By effectively merging two complementary lattice structures to evenly distribute stress, we avoid the weak points where stress normally concentrates.”
They 3D printed a cube using laser powder bed fusion. Testing showed the printed design – a titanium lattice cube – was 50% stronger than cast magnesium alloy WE54, the strongest alloy of similar density used in aerospace applications. The new structure had effectively halved the amount of stress concentrated on the lattice’s infamous weak points. The double lattice design also means any cracks are deflected along the structure, further enhancing the toughness.
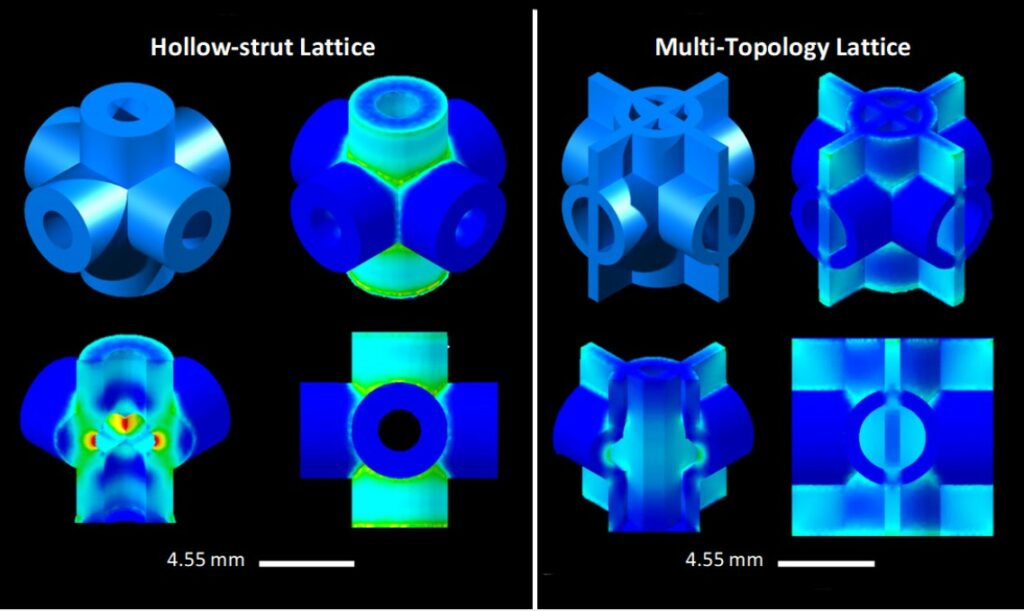
Credit: RMIT
The team plans to further refine the material for maximum efficiency and explore applications in higher-temperature environments.
While currently resistant to temperatures as high as 350 °C, they believe it could be made to withstand temperatures up to 600 °C using more heat-resistant titanium alloys, for applications in aerospace or firefighting drones. As the technology to make this new material is not yet widely available, its adoption by industry might take some time, RMIT concludes.
Remember, you can post job opportunities in the AM Industry on 3D ADEPT Media free of charge or look for a job via our job board. Make sure to follow us on our social networks and subscribe to our weekly newsletter : Facebook, Twitter, LinkedIn! If you want to be featured in the next issue of our digital magazine or if you hear a story that needs to be heard, make sure to send it to contact@3dadept.com