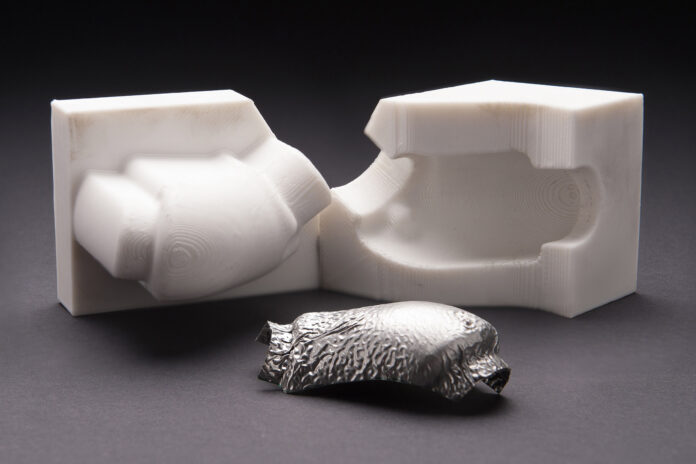
Reichenbacher Hamuel and Multec joined forces to develop the M1000, an industrial 3D printer to meet the demand for large high-performance thermoplastic components.
Reichenbacher Hamuel has made its name for itself as a manufacturer of CNC milling machines whereas Multec is a manufacturer of 3D printers powered by FDM.
What sets the M1000 apart is its ability to print high-performance plastics like ULTEM and PEEK. These materials have mechanical properties including high impact strength and good chemical resistance. This will mainly help industries that need components with high-temperature resistance and good mechanical properties, such as wheel housings and air ducts.
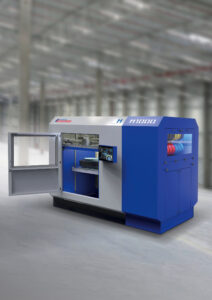
Credit: Multec
The key to the success of the M1000 can be found in the combination of Multec’s patented HexaMove 6-fold printing head with a CNC device from Reichenbacher. This was the only way to realize such extreme precision, flexibility, and efficiency in 3D printing – according to the company.
The HexaMove printing head is equipped with an automatically operating filament change via a magazine allowing seamless changeover between different materials and nozzle types without interrupting the printing process. In this development, time-consuming cleaning cycles are circumvented, and productivity is boosted while reducing downtimes.
Advanced systems for heating and cooling are also incorporated into the design of the M1000. While the building chamber can reach temperatures of up to 350°C to ensure the optimum bonding of the first layer and stress-free printed materials a temperature range of 250°C can be supplied to the building platform.
The cooling system overheads the temperature operations for the printing head, axes, and electronic components to help ensure continuous machine use at high temperatures without degrading its performance and reliability.
Within a 1,000×1,000×1,000 mm building space, the M1000 can create large-sized components in a single print, saving a huge amount of post-production assembly. This makes it especially interesting for industries needing large single-piece components, such as orthopedics, aeronautics, and rail vehicle manufacturing.
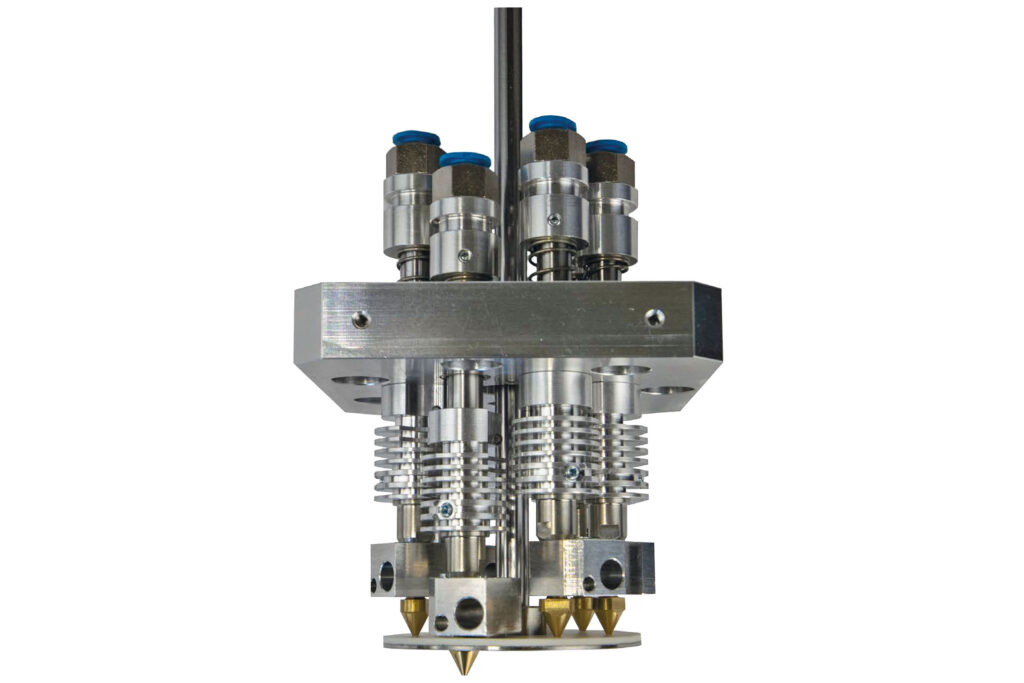
Credit: Multec
Because of the high-speed printing head with 6 hotends, volume flows three to five times higher than traditional systems are realized, allowing fast production of massive components.
Due to the high degree of automation, the M1000 provides flexibility in production, a short lead time, and low investment costs. As this machine can work 24/7, it is optimized to meet prototyping needs and a small series of large parts. Other important factors are its energy efficiency and, therefore, low costs for its acquisition and, as a consequence, operations.
The new 3D printer aims to enable applications across the aerospace, medical engineering, railroad, and military manufacturing industries.
Author: Nagarjun M. Remember, you can post free-of-charge job opportunities in the AM Industry on 3D ADEPT Media or look for a job via our job board. Make sure to follow us on our social networks and subscribe to our weekly newsletter: Facebook, Twitter, LinkedIn & Instagram! If you want to be featured in the next issue of our digital magazine or if you hear a story that needs to be heard, make sure to send it to contact@3dadept.com.