X-plorer is the result of a project developed by JetX, a team of aerospace engineering students from the University of Glasgow working with Rolls Royce.
Rolls Royce helped with the technical side of things. Finalists of the 3D Hubs Student Grant challenge, their aim was to create a very functional 3D printed jet engine model that would provide instant design feedback on the one hand, on the other hand, to enable engineering students to be immersed in practical aspects of their training.
X-plorer
X-plorer 1 model is an engine of 75 cm long, with span diameter of 27 cm and weighs in at 8.1 kg. To achieve this reactor, students developed over 965 3D printed parts, 300 fasteners and 10 integrated sensors into one high-bypass turbofan model.
Every piece was modeled in line with current aero-propulsion theories. Chris Triantafyllou, the President and Founder of JetX explained the considerations that needed to be taken into account while manufacturing the engine:
“The first step in optimizing the design is to perform computational analyses to investigate how the flow changes throughout the engine, as well as the effect that specific forces and loading conditions have on the parts. When several designs are available for one part, CFD analyses are performed with tools that include Solidworks Flow Simulation, ANSYS Fluent & Star CCM+ on single stators, rotors or multi-stage segments to assess which one performs the best.”
The importance of 3D printing in the project
The model was made exclusively from FDM printed parts, with the shortest print lasting just 7 minutes and longest being over 58 hours for the main PCU casing. The team used materials such as PLA, ABS, Nylon, PETG and more for testing.
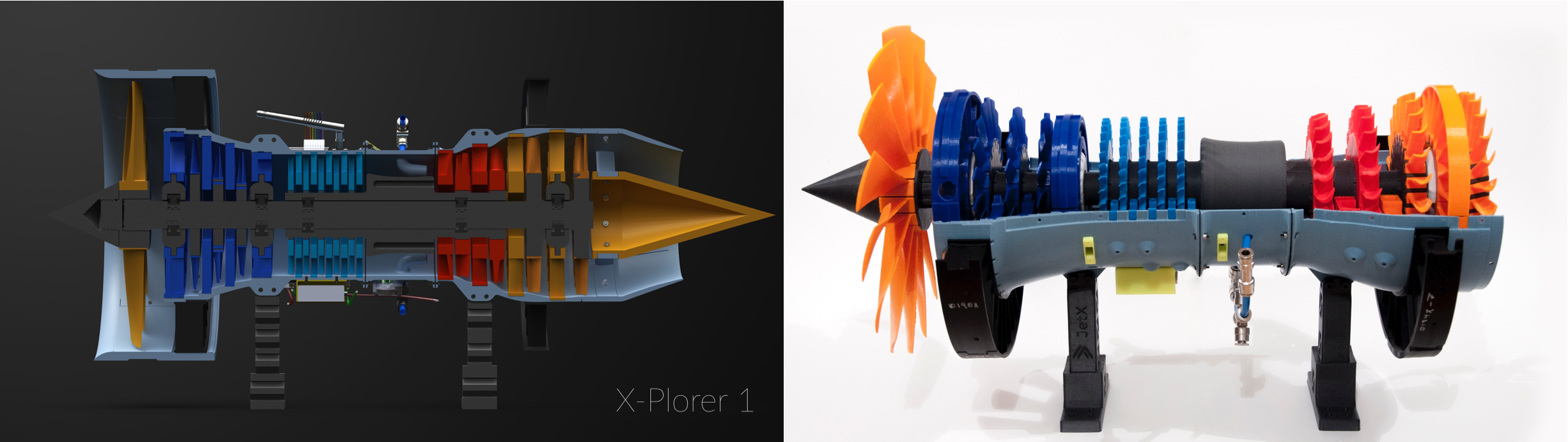
It must be said that additive manufacturing was used as an alternative method of manufacturing to enable the team to facilitate the transition from CAD to part. Furthermore, using another technology such as CNC would have been very expensive.
Moreover, 3D printing was faster and more efficient to change parts when there were new optimizations with the testing.
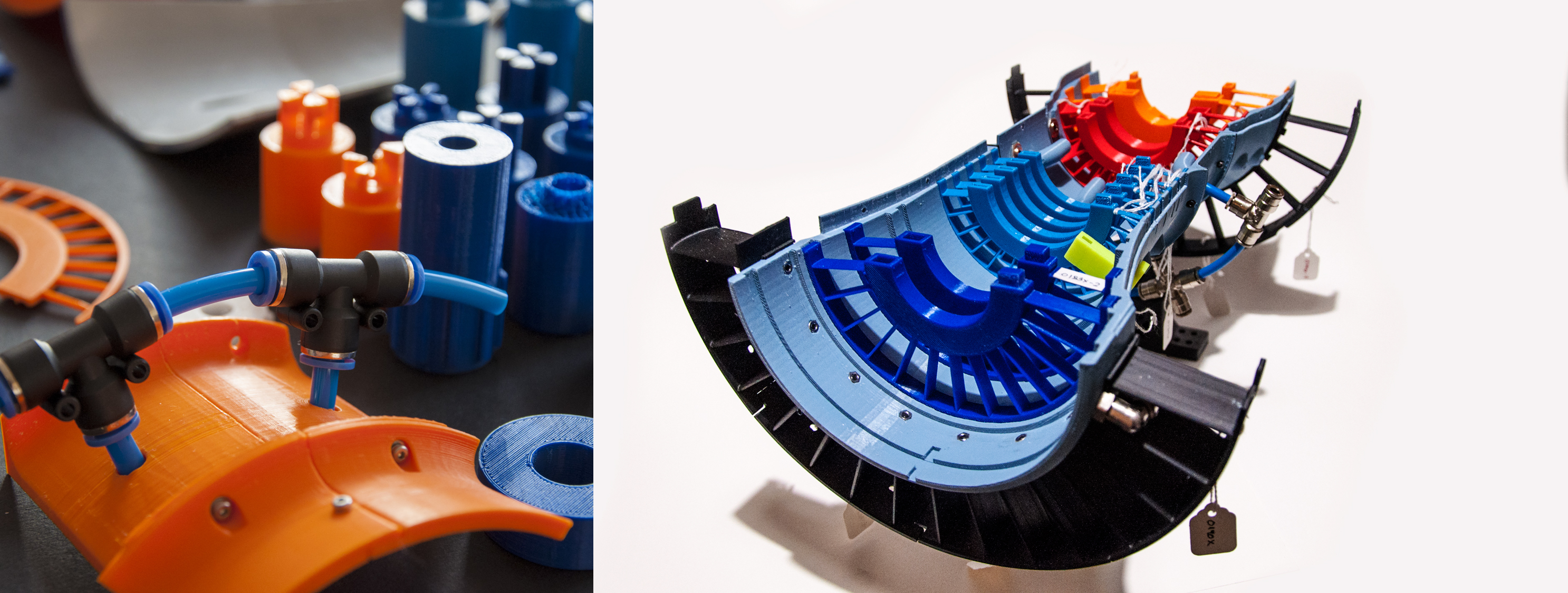
What’s next?
Efforts are still to be made to improve the engine. The project will look to further its engagement in STEM fields, encouraging students to get outside of the lecture environment and to apply their learning.
For further information about 3D Printing, follow us on our social networks and subscribe to our newsletter!
//pagead2.googlesyndication.com/pagead/js/adsbygoogle.js
(adsbygoogle = window.adsbygoogle || []).push({});