North America’s largest AM meetup, RAPID+TCT, happened last week in Chicago. Over 350 exhibitors and 10,000 industry professionals packed the nearly 125,000 square feet of McCormick Place, just south of the city’s center. When you cram that many AM nerds in one space, it’s hard to be surprised when big product releases come out, hot new tech appears around every corner, and business cards passing between hands plant the seeds for future partnerships and friendships to come.
Each of the three days of Rapid + TCT began on the mainstage. Todd Grimm of T. A. Grimm and Associates took the reins and gave the crowd a rundown of what to expect from each day. The morning huddles also included a keynote speaker. Day 1 was a standout, with Kevin Czinger taking the stage.
Czinger and an Ambitious Vision for AM Production
Kevin Czinger is the founder of Divergent Technologies and the CEO of Czinger Vehicles, the company that is using AM to make super cars that break speed records and look good while doing it. Czinger spoke about building and scaling an industrial digital manufacturing system, with a focus on reindustrialising the American Midwest and other areas throughout the globe. Czinger discussed “What happens when you design a complete digital manufacturing system, and not just a 3D printer in isolation?”
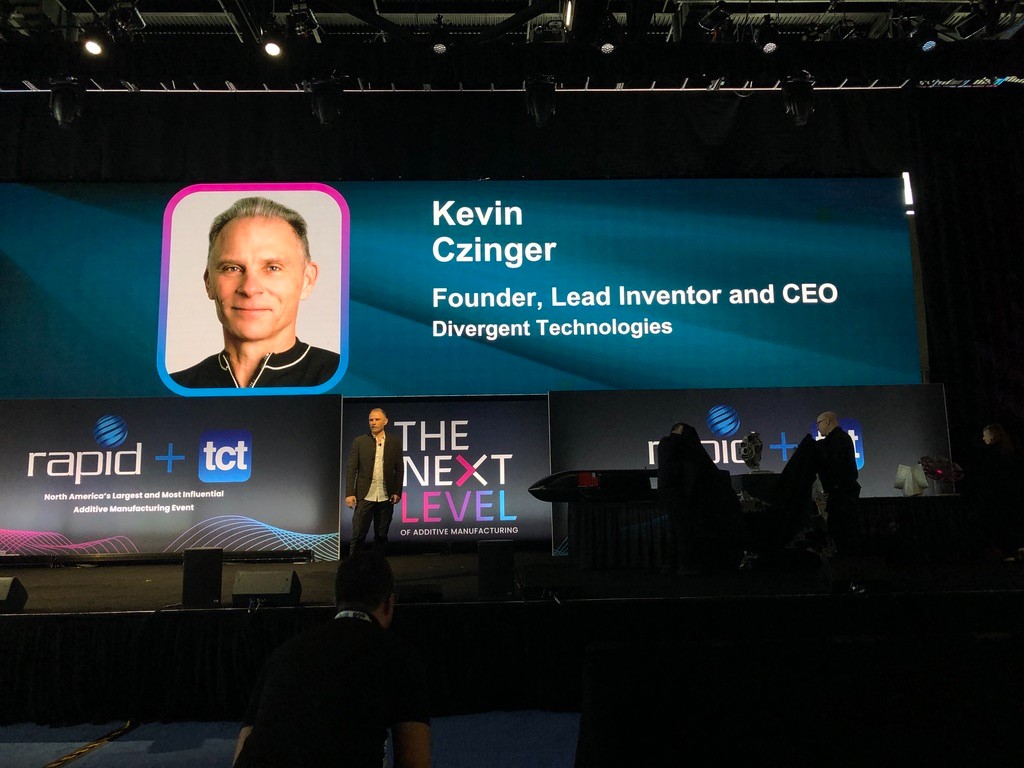
Called Divergent Adaptive Production System, or DAPS, the system includes an AI-assisted generative design stage, then additive production and robotics assisted assembly. Divergent no longer takes on customers looking for R&D and prototyping, only those looking to go into production. Czinger likens the system to the Amazon Web Services of manufacturing; companies buy-in to a service that helps them to design and manufacture without having to build and run a factory.
Omar Mireles was the keynote speaker on Day Two. Mireles is an AM research and development engineer at NASA’s Marshall Space Flight Center, and highlighted for the audience some of the ways NASA is using AM at the moment, and plans to use it in the future. Mireles noted that 3D printing is already happening on the International Space Station, where crewmembers are able to print needed tools and parts, and can save space and money by leaving things on Earth that can be printed if needed while in orbit. Mireles pointed out that NASA is also factoring AM into permanent settlements on the Moon and Mars. He says AM will allow NASA to “live off the land” — by printing with elements found around the base, crews maximize the use of resources already on the celestial bodies we explore.
Solutions for AM users and solutions for AM companies
With over 350 exhibitors, conferences, keynote speeches and other sub-events, covering a massive event like Rapid+TCT often requires to juggle between several activities and conversations. Interestingly, while it’s easier to assume that all exhibiting companies target (potential) AM users, it turns out that some exhibitors were presenting solutions for AM companies looking to accelerate their go-to-market strategy.
In the first category of exhibitors:
DMG Mori is one of these large companies that have been slowly expanding into the additive sphere. I attended a press conference they hosted the first day. To a crowd of about 30 people all wearing conference-friendly headsets, Nils Niemeyer led the DMG Mori team in announcing the opening of a new factory in Davis, California, the first DMG Mori manufacturing facility in the US, as well as the new Lasertec 30 US SLM 3D Printer.
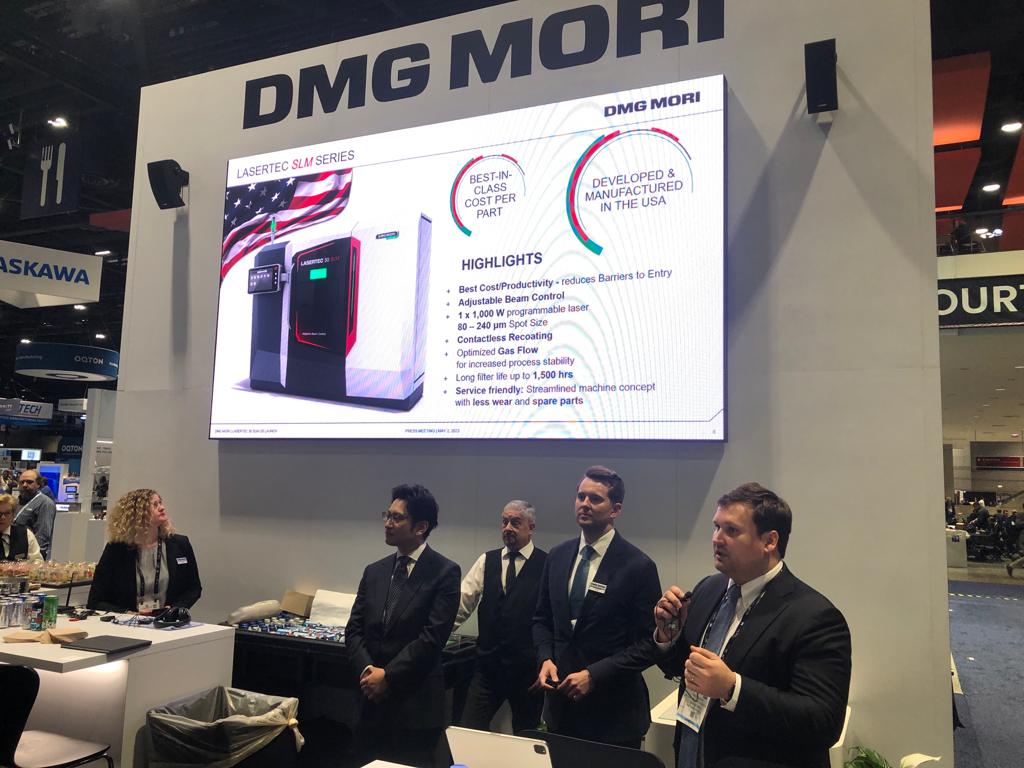
3D Systems had an exhibition, with a large space close to the main entrance. They showed off a new rapid material delivery system – the SLS Material Delivery Module and a module that enhances the use of their DMP Factory 500 system.
The SLS Material Delivery Module is a new accessory for the SLS 380 platform that allows users to use multiple materials on a single platform. Materials are stored in a portable cart that can be rolled up to the machine and attached to run a new material. Furthermore, the ability to utilize a broader range of materials with the printer maximizes the value of the platform for end users to expand the applications they can address. In addition to being compatible with SLS 380, the SLS Material Delivery Module also enables multiple material functionality on 3D Systems’ ProX® SLS 6100 and ProX SLS 500. This product is planned to be available for ordering in the second half of 2023.
3D Systems’ DMP Build Changeover Station is a standalone module that facilitates the use of the DMP Factory 500 system. The DMP Build Changeover Station allows the user to depowder a finished build, remove the base plate with a printed part, add fresh powder, install a new base plate, and prepare a removable print module to launch the next job. Changing materials on the DMP Build Changeover Station proper can be achieved in a matter of minutes, and thus it can serve multiple printers running different materials in parallel. The Build Changeover Station is a lower-cost accessory as compared to 3D Systems’ full peripheral chain thus making metal AM more accessible to a broader range of customers. As production demands increase in an organization, customers are able to move to the full peripheral chain. The DMP Build Changeover Station is currently available for ordering.
Nearby on the floor was EOS, whose booth included a mini basketball court where attendees could test out the airless, 3D printed basketball made by Wilson in partnership with EOS. John Walker with EOS says the ball passed the roundness test, roll test and a rebound test when compared to a regulation basketball.
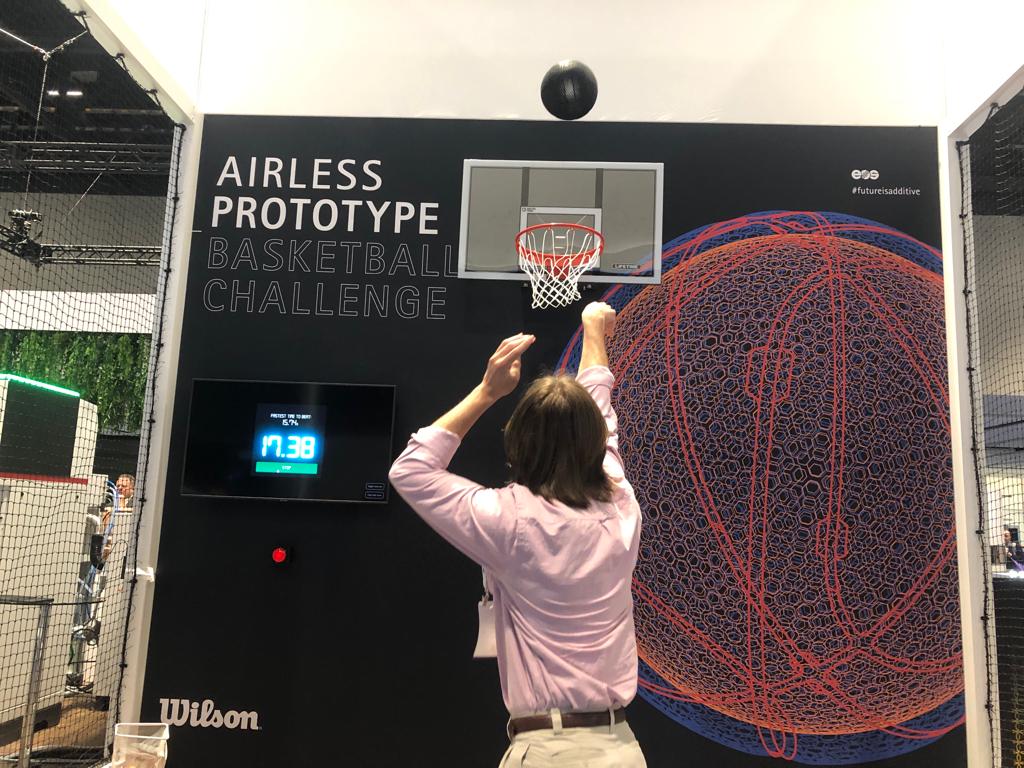
I also caught up with Marina Haugg at Solukon, a German company specializing in depowdering machinery. The company showed off their SFM-AT 1000-S depowdering machine, which features a pneumatic opening roof to allow users to depowder extra-large parts, up to 600x600x1000 mm.
ZEISS was there as well, offering another angle to the post-processing world. I spoke with Paul Brackman, one of their AM Managers, about what they call the “Blue Line” for AM, that includes quality control from ZEISS at every stage of the AM process. This includes powder analysis, imaging and analysis during printing, and post-print quality assurance.
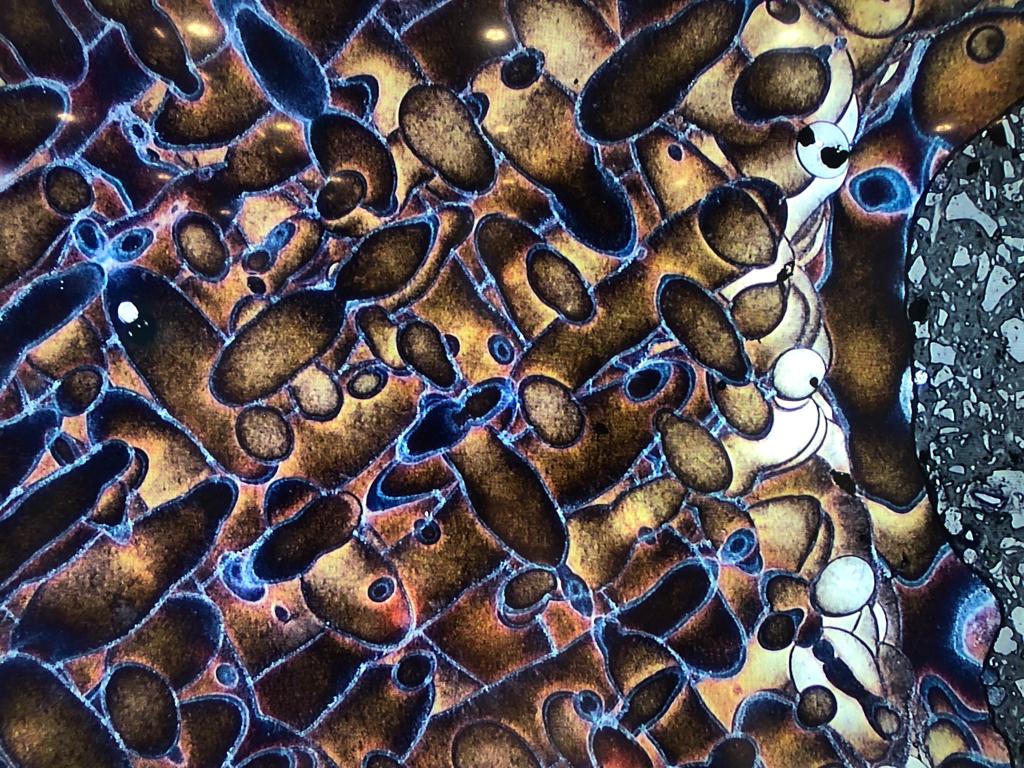
While the big names in AM crowded the middle of the floor with large displays, some of the more innovative and exciting technologies were with the start-ups, many of whom were in smaller spaces on the periphery.
One that jumped out to me was Grid Logic. The company was started by two brothers, Matt and Jim Holcomb, in a small town north of Detroit, Michigan. Matt has a PhD from Stanford and has experience with cryogenics and quantum fluids, as well as chemical engineering. Jim has decades of industry experience at General Motors. Together they’ve developed a multi-material binderless printing system that can mix metals and ceramic materials. The machine simply deposits layers of powder on top of each other, with a zirconium support powder around the powders that will make up the part. Then it all gets sintered together, and the zirconium substrate falls away, leaving the user with the part, bound without lasers or resins or beams.
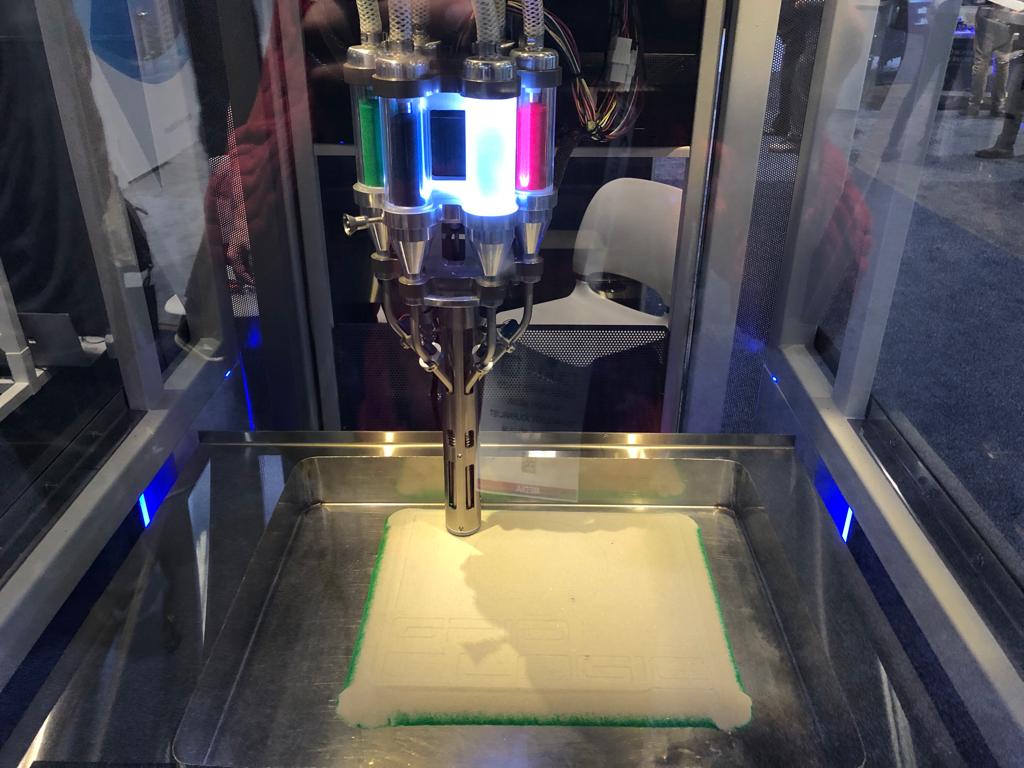
Another company closer to the wall was the Austrian firm Incus, which is innovating in Lithography based metal AM. Incus is a spin-off of the ceramic AM company Lithoz. Head of Application Engineering Denise Mödder says Incus is doing metal SLA printing using a photo-reactive binder filled with metal powders that allows for sintering. The technique apparently allows them to bind “unweldable” materials, and eliminate support material.
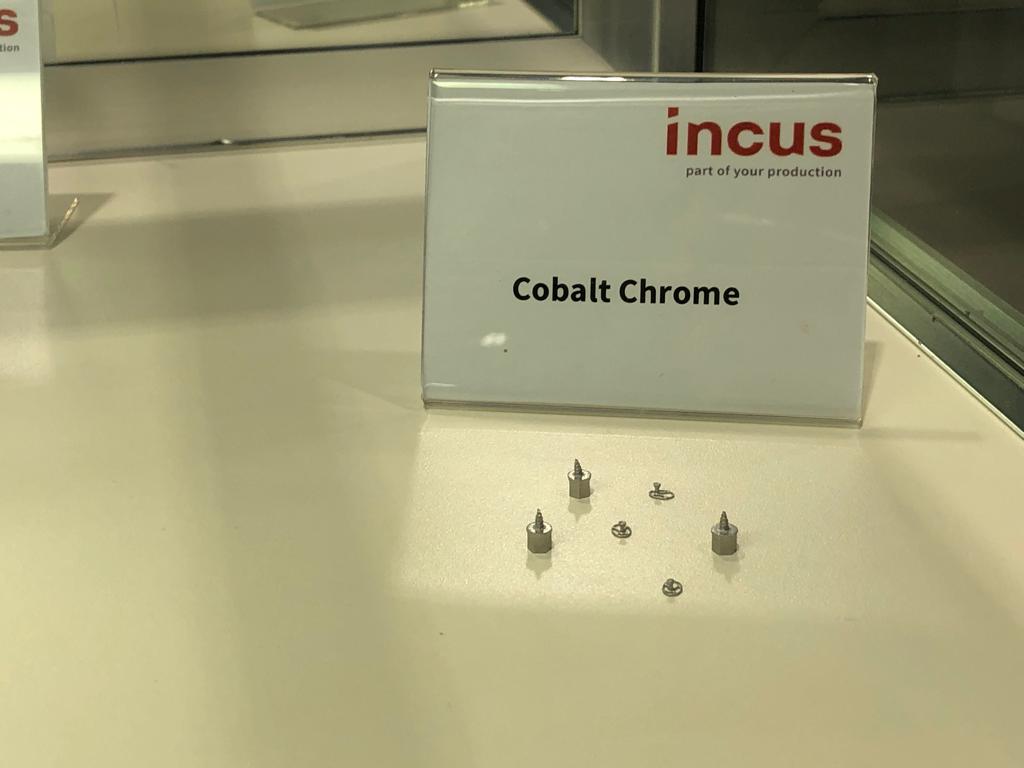
In the second category of exhibitors…
In the spirit of commercialization, I talked to a few more firms that were focused not on materials or machines, but with helping businesses implement additive manufacturing.
One of them was Fittle, a financial services subsidiary of Xerox. Fittle has been in the business of helping customers finance large manufacturing equipment and is expanding into additive. Fittle allows companies to enter the additive world without having to shell out tens of thousands for equipment that might not be the ideal solution for them. Instead, Fittle will buy the equipment, and a business can enter a contract with Fittle to perhaps just rent the machine until a new model comes out, or to pay off the machine over time.
While I was walking away from the Fittle booth, a man approached me and said “You seem like the kind of guy that likes whiskey.” I did a double-take, then told him “Sure!” He was Frank Meskowsky from Profitkey, a company brand new to RAPID+TCT. Profitkey has experience in manufacturing, and is bursting into the AM sphere to help companies using AM for production. Profitkey has a software that can help companies with scheduling when running multiple printers at once.
Last but not least, conferences
Aside from the exhibition floor, RAPID+TCT also featured some lectures/conferences, with topics ranging from “Use of Carbon Nanotubes to Address Thermal Cracking in 6061 Aluminum and Haynes 230” to “Additive Manufacturing – How to Build a Business Case”. I attended two conference sessions, and I liked them but they didn’t feel essential to the RAPID+TCT experience. Not all attendees had permission to see these sessions, which might be why the ones I went to were sparsely attended and kind of quiet.
For those who are still looking to assess the latest solutions unveiled during the show, to see what would work best for their production, I would recommend to stay tuned on the latest announcements that we will continue to be released here on 3D Adept Media.