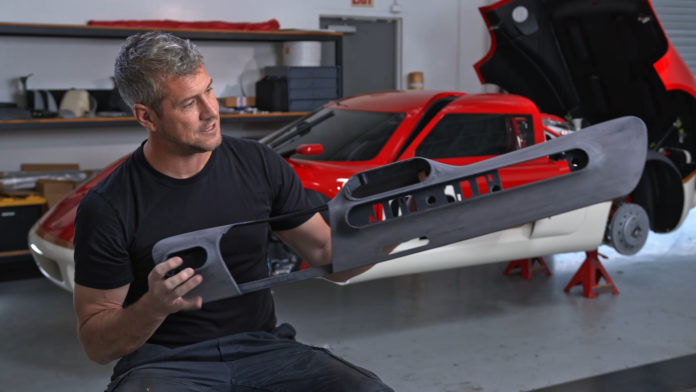
L’équipe de Radford a programmé et suivi ses impressions 3D sur cinq sites internationaux, en utilisant simultanément un parc de 20 imprimantes 3D Stratasys différentes.
Pour le lancement de la voiture de sport carrossée Lotus Type 62-2, la marque mondiale d’automobiles de luxe Radford utilise différentes technologies d’impression 3D de Stratasys. En utilisant les technologies FDM®, PolyJet™ et la stéréolithographie, le constructeur automobile a produit 500 pièces imprimées en 3D.
Selon un communiqué de presse, pour produire les deux premières voitures, plus de 500 pièces ont été imprimées en 3D au Radford Studio, à la société de conception et d’ingénierie automobile Aria Group et à Stratasys Direct Manufacturing. À l’aide du logiciel de flux de travail GrabCAD Shop™ de Stratasys, l’équipe de Radford a programmé et suivi ses impressions 3D sur cinq sites internationaux, en utilisant simultanément un parc de 20 imprimantes 3D Stratasys différentes – une véritable démonstration de fabrication distribuée. L’éventail d’imprimantes Stratasys comprenait les imprimantes 3D F900®, F770™, Fortus 450mc™, F370® et J55™, chacune étant utilisée pour obtenir différents résultats souhaités pour chaque pièce.
L’utilisation de diverses technologies permet à l’équipe de Radford de mieux évaluer les différences entre chaque type de technologie ainsi que les avantages qu’elles peuvent apporter pour telle ou telle pièce.
Un grand noyau sandwich de pare-feu en composite solide, par exemple, a été imprimé en 3D en deux moitiés sur l’imprimante Stratasys F900 en résine ULTEM™ 1010. La pièce a été collée en une seule pièce, puis enveloppée de fibres de carbone sans l’utilisation d’un outil de stratification. La conception de la cloison pare-feu comprenait des caractéristiques de montage complexes pour les haut-parleurs intérieurs, un support de remplissage de carburant et le compartiment à bagages. En outre, de nombreux éléments extérieurs tels que les boîtiers de rétroviseurs latéraux, les conduits de radiateur et les évents de carrosserie ont été imprimés en fibre de carbone FDM® Nylon 12 et en matériaux ASA. De nombreux supports de montage répartis sur l’ensemble de la voiture ont été imprimés en FDM Nylon 12 CF en raison de nombreux facteurs, notamment les exigences de résistance, le calendrier serré du projet et la liberté totale de conception.
« En intégrant la technologie d’impression 3D dans son atelier, Radford a pu faire entrer la fabrication de « supercars » inspirées du style des années 1960 dans le XXIe siècle avec le style et les caractéristiques haut de gamme et hyper-personnalisées que leurs clients attendent d’un véhicule de ce standing », a déclaré Pat Carey, vice-président principal de la croissance stratégique chez Stratasys. « C’est un exemple extrême d’une chose que nous constatons tous les jours dans le secteur automobile. Tous ceux qui investissent dans de nouveaux véhicules veulent bénéficier d’un niveau plus élevé de personnalisation, ce que l’impression 3D contribue à rendre possible. »
Vous pouvez maintenant poster vos offres d’emploi sur 3D ADEPT Media. Pour des informations exclusives sur l’impression 3D, abonnez-vous à notre newsletter et suivez-nous sur les réseaux sociaux : Facebook, Twitter, LinkedIn & Instagram ! Vous souhaitez-vous abonner à 3D ADEPT Mag ? Ou vous voulez figurer dans le prochain numéro de notre magazine numérique ? Envoyez-nous un email à contact@3dadept.com