Inutile de rappeler les changements monumentaux qui ont aidé de nombreuses industries à apprécier et à considérer le potentiel de la fabrication additive. Avec plus de 300 systèmes de fabrication additive (FA) métallique disponibles sur le marché actuel, dont la plupart sont des systèmes fermés et propriétaires, nous ne pouvons pas nous empêcher de penser au long chemin à parcourir et aux défis qui restent à relever. Comment les opérateurs peuvent-ils accéder aux connaissances sur les procédés de fabrication additive ? Comment peuvent-ils faire face aux limitations en termes de matériaux et obtenir davantage d’applications ? Comment peuvent-ils avoir un plus grand contrôle sur le processus de fabrication ? Pour une niche d’experts sur le marché de la FA, la réponse à ces questions est de « s’appuyer sur des plates-formes ouvertes de fabrication additive ».
Ce dossier traite de l’essor et des raisons qui amènent les entreprises à considérer les plateformes de « fabrication ouverte ». Plus important encore, il vise à donner aux fabricants de diverses industries une autre option à envisager lorsqu’il s’agit d’investir dans les technologies de fabrication additive métallique.
Le concept de « fabrication ouverte » n’est pas nouveau. Au contraire, il est relativement simple à comprendre. Le terme est lié à l’idée de démocratisation de la technologie telle qu’elle s’incarne dans la culture des fabricants et dans d’autres domaines d’innovation de base tels que les hackerspaces. Il consiste à combiner de nouveaux outils de production, de nouveaux processus (imprimante 3D) et de nouveaux protocoles de fabrication.
En ce qui concerne la FA, les fabricants ont du mal à la comprendre et à l’appliquer à l’environnement industriel actuel. POURQUOI ? Pour répondre à cette question, nous avons invité deux entreprises « incontournables » dans ce milieu. Elles ouvrent actuellement la voie à une plus grande « ouverture » dans la fabrication additive : Dyndrite et Open Additive.
Dyndrite™ a pour mission de fournir une technologie avancée pour l’avenir de la fabrication numérique. Fondée en 2016, la société a développé le Dyndrite Kernel, un noyau à géométrie accélérée qui permet aux entreprises de construire la prochaine génération de logiciels ou de matériel de fabrication additive plus facilement et plus rapidement que jamais. Outre ce produit phare, la société a été reconnue pour son Dyndrite Developer Council, élément central du Dyndrite Developer Program qui fournit des outils, des ressources et une communauté aux équipementiers (OEM), aux éditeurs de logiciels indépendants (ISV), aux fournisseurs de services et aux éducateurs.
Open Additive est une autre société à surveiller lorsqu’il s’agit de systèmes de fabrication additive ouverts. Dans le but de fournir des systèmes de FA métalliques abordables, Open Additive se démarque en offrant des solutions personnalisables à l’industrie de la fabrication additive.
Harshil Goel, fondateur et CEO de Dyndrite™ et Ty Pollak, président et CEO d’Open Additive partagent leurs points de vue sur ce sujet.
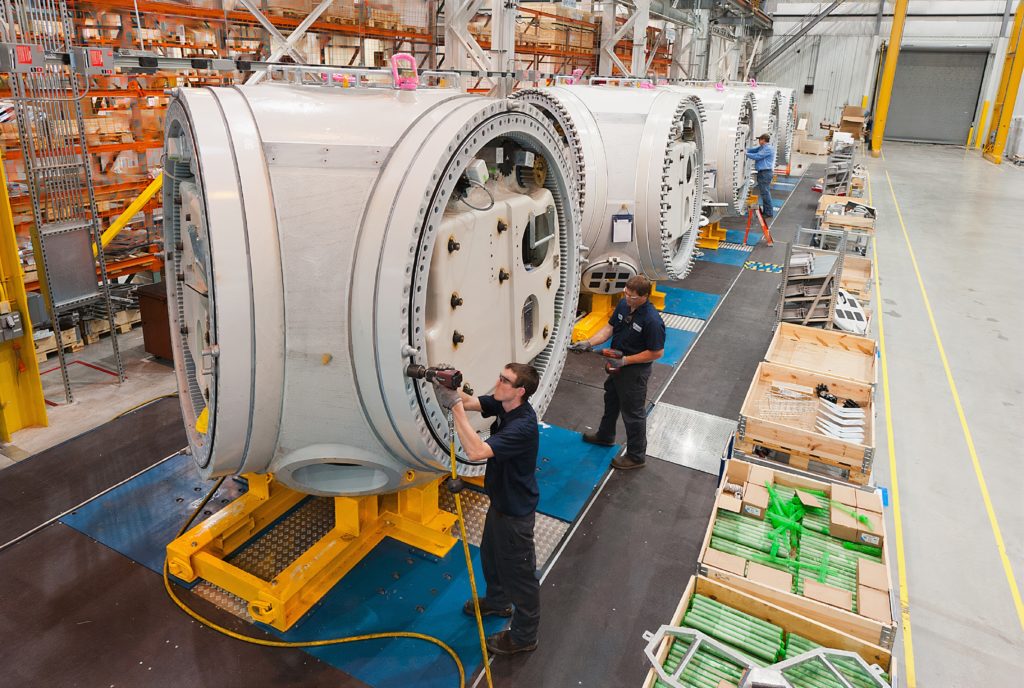
Comment reconnaître une plate-forme « ouverte » de fabrication additive ?
Premièrement, il n’existe pas encore de définition standard des « plates-formes ouvertes de fabrication additive ». Les fabricants d’imprimantes 3D qui développent et fournissent actuellement des plates-formes de fabrication additive ouvertes visent à répondre premièrement à la demande de matériaux de meilleure qualité, d’applications plus nombreuses, et donc de personnalisation. Cette question est devenue inhérente pour de nombreux fabricants, dont Origin, Arburg ou encore Freemelt.
Prenons l’exemple de l’impression 3D polymère. Les fabricants d’imprimantes 3D Origin et Arburg ont ouvert les portes à des entreprises de matériaux qui adaptent désormais une large gamme de matériaux habituellement utilisés dans le moulage par injection. Les opérateurs peuvent par exemple choisir entre différents granulés amorphes pour le moulage par injection afin de produire non seulement des maquettes, mais aussi de véritables composants fonctionnels.
Dans la même veine, pour élargir le portefeuille de matériaux et les domaines d’application de la fusion par lit de poudre d’électrons (PBF-EB), le fabricant suédois Freemelt AB développe un système de développement de matériaux à source ouverte qui permet aux opérateurs d’essayer de nouveaux matériaux et des stratégies innovantes de numérisation de faisceau. C’est une stratégie judicieuse, surtout dans le domaine de la fusion par lit de poudre d’électrons où le plus grand obstacle qui freine l’adoption plus large de ce procédé est le développement de matériaux.
En réalité, contrairement aux imprimantes 3D à base de polymères, qui nécessitent essentiellement le développement de toute une gamme de matériaux, les imprimantes 3D à base de métaux sont connues pour l’utilisation de fils (poudres métalliques) et de matières premières provenant d’industries qui existaient déjà. En fait, selon la règle, si un métal se soude ou se coule bien, il doit aussi pouvoir être adaptable à la fabrication additive. Toutefois, cette règle ne tient pas compte du cycle vertueux de l’industrie de la FA. Ce cycle vertueux stipule que « plus les concepteurs concevront de produits, plus nous aurons d’applications. Plus il y aura d’applications, plus de matériaux seront développés, et plus d’imprimantes évolueront ou seront introduites sur le marché ». En fin de compte, ce cycle renforce la croissance de l’industrie, mais il soulève également nombre de ses défis.
Si on examine le développement des systèmes de FA métal, une partie de ces défis montre que les matériaux ne peuvent pas être le seul facteur à prendre en compte pour qualifier un système de fabrication additive ouvert.
Autres caractéristiques clés d’une plate-forme ouverte de fabrication additive
En plus d’une plateforme ouverte de matériaux, il faut garder à l’esprit d’autres éléments lors de la recherche d’une plate-forme de FA ouverte, éléments qui ont de forts contre-arguments soulevés par les fabricants d’imprimantes 3D industrielles bien établies.
Architecture ouverte VS Architecture fermée.
Les systèmes fermés ont été la norme dans la fabrication additive industrielle. Seul bémol ? Cette option enferme souvent les fabricants dans le matériel, les processus et les matériaux d’un seul fournisseur. Pour parler simplement, l’architecture ouverte et l’architecture fermée peuvent être considérées comme les deux faces d’une même pièce.
Il est compréhensible que les entreprises qui ont été à la pointe de la technologie de FA protègent la propriété intellectuelle qu’elles ont développée au cours des dernières années. Elles sont également dans une position unique pour capitaliser sur ce marché.
« L’argument de la propriété intellectuelle » est parfaitement logique ; sans parler du fait que les systèmes propriétaires sont connus pour leur capacité à fournir une stabilité, une répétabilité et une traçabilité qui donnent aux fabricants industriels confiance dans les choix qu’ils effectuent.
L’argument des entreprises qui développent un système à architecture ouverte est de fournir « un outil permettant non seulement de fabriquer des pièces, mais aussi de faire des progrès dans l’industrie ».
Cet argument pourrait certainement être plus attrayant non seulement pour les fabricants mais aussi pour les chercheurs, car un tel système permet une plus grande flexibilité. Les opérateurs qui utilisent ces systèmes ont plus de liberté pour modifier, développer et/ou intégrer des composants matériels ou logiciels.
« Idéalement, la plate-forme devrait être conçue dans un esprit d’ouverture dès le départ, avec un espace physique adéquat, des informations disponibles sur la configuration et la possibilité d’accéder aux données du système », explique Open Additive. En outre, les systèmes de fabrication additive ouverts permettent aux utilisateurs d’intégrer leur propre technologie propriétaire, qui n’a rien à voir avec « des matériaux ou des paramètres ouverts ».
Configuration ouverte ou configuration fermée ?
Concentrons-nous sur les systèmes à lit de poudre par exemple. En fonction du projet réalisé, les opérateurs peuvent avoir besoin d’atteindre une certaine performance avec le(s) laser(s), l’optique, la plaque de construction, le dépôt de poudre ou les capteurs.
Ces caractéristiques sont généralement configurées avant la vente et ne peuvent pas toujours être modifiées dans les systèmes de FA à architecture fermée. Pour optimiser le processus de fabrication industrielle, les opérateurs règlent souvent les paramètres des machines en s’appuyant sur la simulation – ce qui, en fin de compte, conduit à un meilleur contrôle du processus de fabrication.
En réalité, que ce soit dans les systèmes de FA ouverts ou fermés, la liste des facteurs qui peuvent avoir un impact sur la qualité d’une pièce finale est longue et ces variables de processus doivent être strictement définies et contrôlées pour permettre une impression réussie à chaque fois, quelle que soit la machine.
Cependant, une chose que tout le monde devrait apprécier dans les systèmes de FA ouverts est la flexibilité. En effet, on ne peut pas prévoir tous les types de projets qui pourraient être réalisés avec une machine et la capacité d’adapter la machine avant ou après la vente est certainement précieuse.
Cette liste de pour et de contre n’est certainement pas exhaustive, car le débat ne fait que commencer. Cependant, le principal acteur qui mène la conversation est le client.
Que veut le client ?
Le client veut des options. Dans une enquête réalisée en 2018 par le fabricant d’imprimantes 3D Essentium, 162 directeurs et cadres d’entreprises manufacturières du monde entier ont partagé leurs expériences, défis et tendances actuels en matière d’impression 3D pour la fabrication de produits.
L’enquête révèle que malgré l’optimisme quant à l’utilisation de la technologie de FA, certaines entreprises se heurtent encore à des obstacles, notamment le coût élevé des matériaux d’impression 3D (51 %), le matériel d’impression 3D coûteux (38 %) et le fait que la technologie d’impression 3D actuelle n’est pas évolutive (31 %).
Pour surmonter l’inflexibilité du système et utiliser les matériaux de leur choix, les fabricants exigent des écosystèmes ouverts. 50 % des personnes interrogées déclarent avoir besoin de matériaux de haute qualité et abordables pour répondre à la demande croissante de pièces industrielles imprimées en 3D. D’autre part, pour 85 % des fabricants, la fabrication additive à l’échelle industrielle a le potentiel d’augmenter les revenus de leur entreprise, 22 % déclarent que le verrouillage des fournisseurs a entravé la flexibilité nécessaire.
Harshil Goel et Ty Pollak ne peuvent pas être plus d’accord, car ils croient fermement que le moment est venu d’accélérer le passage à des systèmes de FA métallique plus ouverts.
Pourquoi les systèmes ouverts et les logiciels avancés sont-ils l’avenir de l’industrie ? – Les points de vue de Harshil Goel et Ty Pollak
Harshil Goel, CEO de Dyndrite™ Ty Pollak, CEO de Open Additive
Si les modèles commerciaux traditionnels ont permis de maintenir la croissance du secteur dans son état actuel, ils ne sont pas adaptés pour propulser et soutenir le secteur dans l’environnement actuel, dans lequel des dizaines de fournisseurs sont désormais en concurrence, offrant des centaines d’options matérielles et logicielles à optimiser pour un éventail étourdissant d’applications par une base d’utilisateurs beaucoup plus sophistiquée. Dans ce nouveau climat, le modèle de solutions de FA métal fermées et hautement propriétaires limite la promesse ultime de la FA à ses utilisateurs finaux : une plus grande liberté de conception, des coûts réduits et une meilleure qualité des pièces. Ainsi, des solutions matérielles et logicielles plus ouvertes sont la clé de la croissance future du secteur.
La primauté du parcours d’outil
À son niveau le plus élémentaire, l’impression 3D se résume à tracer un chemin (par exemple, une ligne ou une zone) avec un outil actif (par exemple, une tête d’impression, un laser, etc.) pour joindre des morceaux de matière en une pièce solide. Aujourd’hui, l’industrie de la FA métallique dispose de plus de 300 systèmes métalliques, dont la plupart sont des systèmes fermés et propriétaires, avec leurs propres stratégies de traçage d’outil uniques qui sont généralement difficiles à comprendre, sans parler du contrôle. Cela signifie que même si vous pouvez faire fonctionner les mêmes paramètres de processus sur les machines de différents fournisseurs, cela produira trop souvent des pièces nettement différentes tant du point de vue métallurgique que géométrique, ce qui rendra les normes et le contrôle des processus difficiles et coûteux. Comparez cela aux outils d’usinage traditionnels qui peuvent exécuter le même parcours sur différentes machines, ce qui donne des pièces similaires. Des systèmes matériels/logiciels plus ouverts permettant la compréhension et le contrôle du parcours d’outil sont donc essentiels à l’accélération de la FA pour améliorer la qualité et réduire les coûts.
Les pièces métalliques imprimées en 3D sont bien au-delà des « supports de tondeuse à gazon ».
Nous sommes coincés dans une situation sans issue : Les vendeurs de systèmes de machines développent chaque année de nouveaux matériaux et paramètres de traitement tout en liant ce développement à leur stratégie de propriété intellectuelle. Les fabricants de systèmes de machines et leurs équipes de logiciels et d’ingénieurs sont poussés à bout pour développer ces paramètres. Mais ils utilisent des pièces génériques/représentatives pour tester et valider. Cependant, les utilisateurs finaux repoussent les limites de ces imprimantes en produisant une géométrie de plus en plus complexe et sophistiquée qui exploite le véritable mandat de l’impression 3D : avec une géométrie nettement plus exotique que les pièces génériques. Les utilisateurs finaux considèrent ces nouvelles pièces avancées comme un élément essentiel de leur stratégie de propriété intellectuelle, et ne sont donc pas disposés à partager cette géométrie avec qui que ce soit.
Ainsi, l’industrie de la FA métallique est maintenant coincée dans un scénario où les intentions des vendeurs de systèmes et de leurs clients sont en désaccord. Très franchement, il faut que quelque chose donne. Le fabricant de systèmes a besoin de meilleurs outils pour développer de meilleures machines. L’utilisateur final a besoin de solutions qui répondent à l’évolution de ses besoins, une architecture ouverte est l’un des principaux moyens de sortir de cette situation difficile.
Réduire le risque d’obsolescence
Si les systèmes ouverts ont été jusqu’à présent principalement bénéfiques pour la communauté de la R&D, ils permettent également aux producteurs, des grands fournisseurs au petit atelier d’usinage, de modifier la configuration de leur système en fonction de l’évolution des besoins et de la technologie. En conséquence, le risque d’obsolescence diminue et un plus large éventail d’applications futures peut être pris en charge. Cela peut inciter les organisations à s’engager à entrer dans le jeu plus tôt, sachant qu’elles peuvent commencer à développer des compétences et des cas d’utilisation, mais sans s’enfermer dans les capacités existantes. Ainsi, les systèmes à architecture ouverte peuvent réduire l’un des principaux obstacles à adopter la FA en métal, à savoir la crainte d’effectuer un investissement majeur qui verrouille les capacités futures dans un secteur qui évolue rapidement.
Vers des systèmes plus intelligents
Un élément clé dans le développement des normes de FA et des stratégies améliorées de contrôle des processus est l’intégration de divers capteurs et analyses pour surveiller, et même modifier, le processus de construction. Pour développer et utiliser au mieux ces capacités, les utilisateurs doivent pouvoir accéder aux données brutes et traitées des capteurs, comprendre toutes les analyses disponibles ou créer leurs propres analyses. Cela permet d’informer l’opérateur et de contrôler la machine afin de prendre des mesures sur la base des informations obtenues. Les architectures fermées font obstacle à chacune de ces étapes, d’où le manque d’informations utiles sur les processus disponibles sur les machines AM métalliques actuelles. Au contraire, les systèmes matériels et logiciels ouverts sont essentiels pour réaliser l’état futur de l’industrie, dans lequel les plates-formes de FA métallique deviennent des outils de production plus intelligents.
Connecter l’écosystème numérique
Aujourd’hui, les machines de FA métal font de plus en plus partie d’un écosystème numérique, qui ne fera que s’interconnecter de plus en plus. Alors que le logiciel de la machine contrôle tout ce qui concerne le processus de construction – les paramètres, les contrôles de processus, la résolution, la vitesse, les flux, etc. – il doit être intégré à d’autres outils qui permettent la configuration et l’optimisation avant la construction, l’utilisation efficace des actifs disponibles, la collecte et l’analyse des données en temps réel et après la construction, etc. La machine doit donc être capable d’accepter et de produire une variété de formats standards, compatibles avec les différents outils logiciels utilisés dans ce paysage numérique. Il faut donc des cadres logiciels qui acceptent à la fois des normes ouvertes et des normes propriétaires, et qui offrent à l’utilisateur une plus grande souplesse pour contrôler la machine au moyen de plug-ins logiciels et d’API personnalisés selon les besoins. Les cadres logiciels ouverts avec des API accessibles à d’autres personnes que les développeurs de logiciels internes sont la clé de la croissance future.
Construire des ponts grâce aux normes et aux nouveaux noyaux de géométrie
« Nous ne pouvons pas avoir 30, 40 ou 100 imprimeries différentes, toutes avec des normes concurrentes différentes ». Harshil Goel, lors de l’événement Dyndrite Developer Council 2020 en avril.
Tous les participants étaient d’accord. Les normes sont un sujet central pour la croissance future de l’industrie de la FA métal. Sans normes applicables à l’ensemble du secteur, la croissance collective de l’industrie est freinée, ce qui affecte chaque OEM individuellement. Dyndrite s’efforce d’aborder la question des normes par le développement du noyau géométrique central visant à faire avancer l’industrie de la FA et à développer des écosystèmes intégrés critiques qui alimentent la fabrication numérique. En outre, la société a également lancé le Dyndrite Developer Council pour travailler avec les fournisseurs de l’industrie afin de développer des normes que tous peuvent utiliser et aider à développer le noyau Dyndrite pour répondre aux besoins collectifs. Une des tâches clés et essentielles dont s’occupe actuellement le conseil des développeurs est le développement d’une API standard de parcours d’outils pour aider à résoudre les problèmes de parcours d’outils décrits précédemment. Les membres du conseil couvrent l’ensemble du secteur, des entreprises établies telles que 3D Systems, EOS, SLM, Renishaw et ANSYS, aux nouveaux acteurs du marché, notamment Open Additive, Aconity3D et Impossible Objects. L’intérêt pour des systèmes plus ouverts s’accroît dans tout le Conseil, y compris chez SLM et EOS.
Le Conseil compte désormais 20 membres et continue de se développer car les fournisseurs prennent conscience de la nécessité de collaborer, même lorsqu’ils sont en concurrence. Aux côtés de Dyndrite, Open Additive est un champion de l’accélération de l’innovation grâce à des solutions plus ouvertes, et cherche à étendre le développement et l’application des normes de FA à ses stratégies de contrôle des machines de FA métallique ainsi qu’à ses outils de collecte et d’analyse de données multi-capteurs.
Conclusion
Certaines entreprises de la FA ont commencé à reconnaître la nécessité de disposer de machines ouvertes et indépendantes. Cependant, malgré les prévisions, le marché ne semble pas prêt à abandonner le paradigme de la propriété intellectuelle. À l’heure actuelle, plusieurs facteurs jouent en faveur des forces des systèmes ouverts. Si Harshil Goel et Ty Pollak ont raison, ce n’est qu’une question de temps avant que les industries ne suivent ce mouvement.
Ce dossier a été initialement publié dans le numéro de Septembre – Octobre de 3D ADEPT Mag.
N’oubliez pas que vous pouvez poster gratuitement les offres d’emploi de l’industrie de la FA sur 3D ADEPT Media ou rechercher un emploi via notre tableau d’offres d’emploi. N’hésitez pas à nous suivre sur nos réseaux sociaux et à vous inscrire à notre newsletter hebdomadaire : Facebook, Twitter, LinkedIn & Instagram ! Si vous avez une innovation à partager pour le prochain numéro de notre magazine numérique ou si vous avez un article à faire connaître, n’hésitez pas à nous envoyer un email à contact@3dadept.com.