While FDM 3D printing is one of the most affordable processes used for the production of parts, its utilization often comes with a number of challenges related to the filament, and the ideal temperature it should have in order to ensure reliable printing. Machine manufacturers who have understood it, have developed an additional equipment that can be used with their 3D printer. That’s anyway what we saw with BCN3D’s smart cabinet, BigRep’s dry cabinet or even MakerBot’s smart Hepa filtration system. Another crucial challenge faced with filaments is related to its diameter. Sometimes, as the filament diameter varies, it makes it difficult to ensure quality assurance and repeatability of the print.
That’s an issue that French 3D printer manufacturer QUALUP SAS has decided to address in the development of its latest 3D printer. Named Qu3-HT, the high temperature 3D printer is equipped with a filament diameter control and print flow monitoring system that ensures the material flow rate during the printing process, while delivering the expected quality assurance and repeatability of the print.
“The filament control, integrated into the printer, continuously measures the diameter and ovality of the filament with an accuracy of 0.8µm”, declared Myriam BOICHUT, President of QUALUP SAS. “The triple objective of this instrument is to continuously compensate for variations in filament diameter in order to have a constant flow rate, the same as that calculated by the Slicer, to guarantee the repeatability and the quality of the parts by means of a print report supplied with each part.”

A press release from the company explains that filament manufacturing tolerances generally vary by +/-0.05mm, which in reality gives a 12% variation in volume between the maximum and minimum tolerances. For technical filaments: PEEK, PEKK, PEI, PPSU… Some manufacturers even announce tolerances of +/- 0.10mm, the filament can therefore vary by 24% in volume. These volume variations are generally well supported when using standard filaments (PLA, ABS, PETG,…), but pose major problems with technical filaments (Hi-polymers, Metal…). All filament extruders control the flow rate in “mm equivalent”, so it is impossible to achieve consistent quality and reproducible prints with such volume variations.
This issue ultimately gives rise to a domino effect on the rest of the manufacturing process, since the variation of the printed volume causes under-extrusions or over-extrusions systematically degrading the inter-layer bonds, and thus the strength of the parts. Other aspects of the manufacturing process that are affected include for instance, the dimensions of the part, filling rates, surface conditions, or even the mass of the part.
“We decided to develop this feature a little over two years ago when one of our customers asked us to print stainless steel parts using a process similar to BASF’s Utrafuse 17-4®, he absolutely wanted to get 100% filling of the parts”, explains Myriam BOICHUT. “It was impossible to print correctly with 100% filling, the filament, highly charged with metal 85/15 ratio, did not tolerate any over or under-extrusion, either there were gaps and porosity, or the nozzle became fouled and caused marks on the part. This innovation has profoundly improved the quality and repeatability of Qu3- HT printed parts, with all materials, especially Hi-Temperature polymers. It is now possible to certify the quality of Filament Fusion printed parts and that two same parts are identical.”
In practice, what does the operation look like?
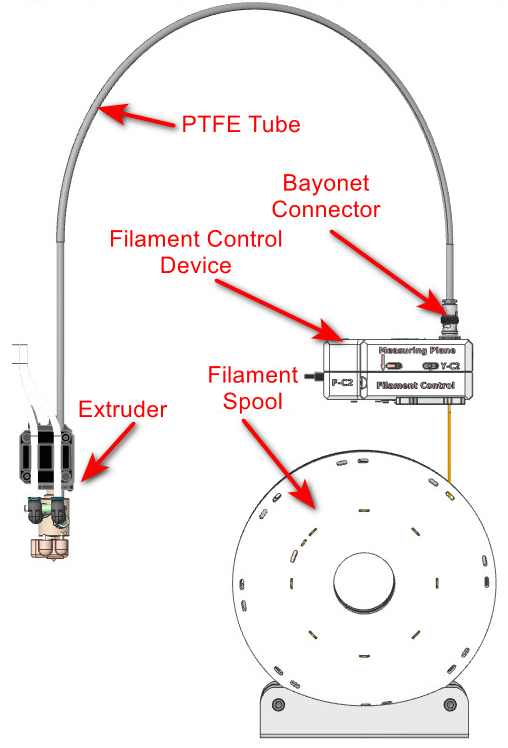
Every second the Filament Control takes diameter measurements in two perpendicular planes and calculates the ovality and average cross-section of the filament. Simultaneously with the diameter measurements, it queries the Qu3-HT’s Motherboard to find out what the extruded length was when the diameter was measured. It then calculates the volume compensation to be sent to the Qu3-HT and at what extruded length it should send this compensation (depending on the distance between the measurement point and the extruder drive rollers). When the extruded length reaches this value, it sends the compensation which is executed immediately by the machine. The measurements are carried out on 2 perpendicular axes at a frequency of 500 Hz with an accuracy of 0.8µm (0.0008mm), with measurement of diameters, ovality, average section and calculation of the volume compensation to send to the machine.
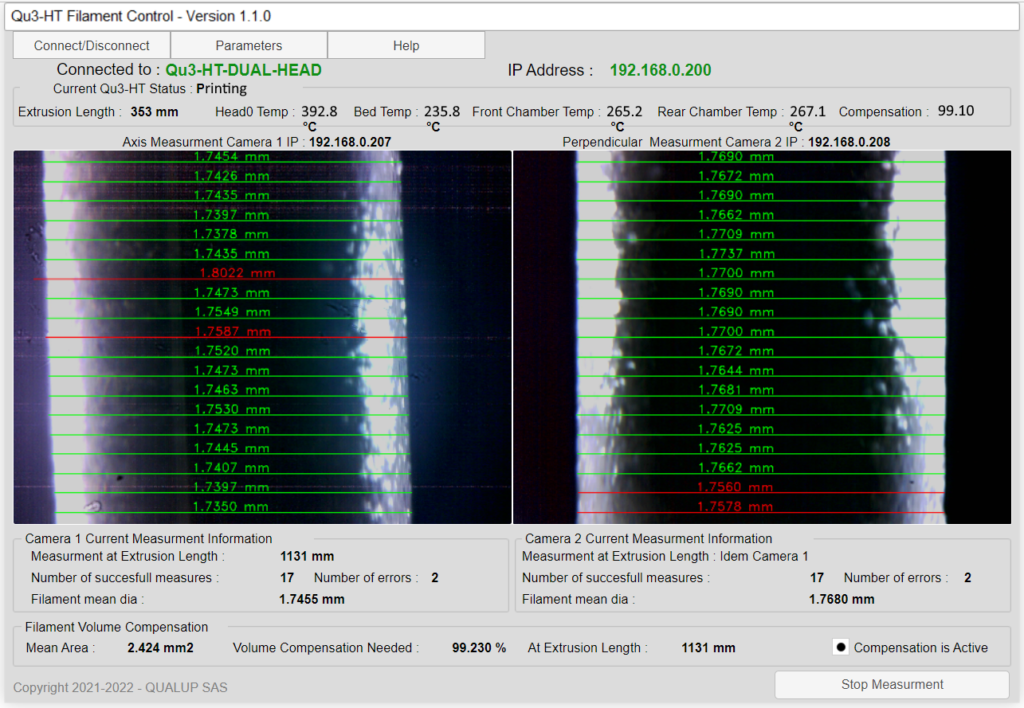
Remember, you can post job opportunities in the AM Industry on 3D ADEPT Media free of charge or look for a job via our job board. Make sure to follow us on our social networks and subscribe to our weekly newsletter : Facebook, Twitter, LinkedIn & Instagram ! If you want to be featured in the next issue of our digital magazine or if you hear a story that needs to be heard, make sure you send it to contact@3dadept.com.