With this new 3D printer, the OEM targets industrial applications such as repairing turbine blades and molds
With the acquisition of SLM Solutions by Nikon, we had almost forgotten that Nikon had decided to become a metal 3D printer manufacturer. The Japanese optics and photographic equipment manufacturer unveiled its first metal 3D printer in 2019 – only available on the Japanese market.
Today, the OEM announces another metal 3D printer in the Lasermeister series. Named Lasermeister LM300A, the new 3D printer is based on Directed Energy Deposition (DED) technology. Unlike the Lasermeister 100A that was designed for research purpose in mind, the new 3D printer is developed for industrial applications.
With an expanded build area, it is equipped with the newly developed 3D scanner, the SB100. This advanced 3D scanner supports factory automation by enabling users to scan each workpiece with the click of a button and then automatically generates the tool path data for the 3D printing process to begin. The successful pairing of the LM300A and SB100 deliver tremendous value to the industry, particularly for applications such as repairing turbine blades and molds, the company says.
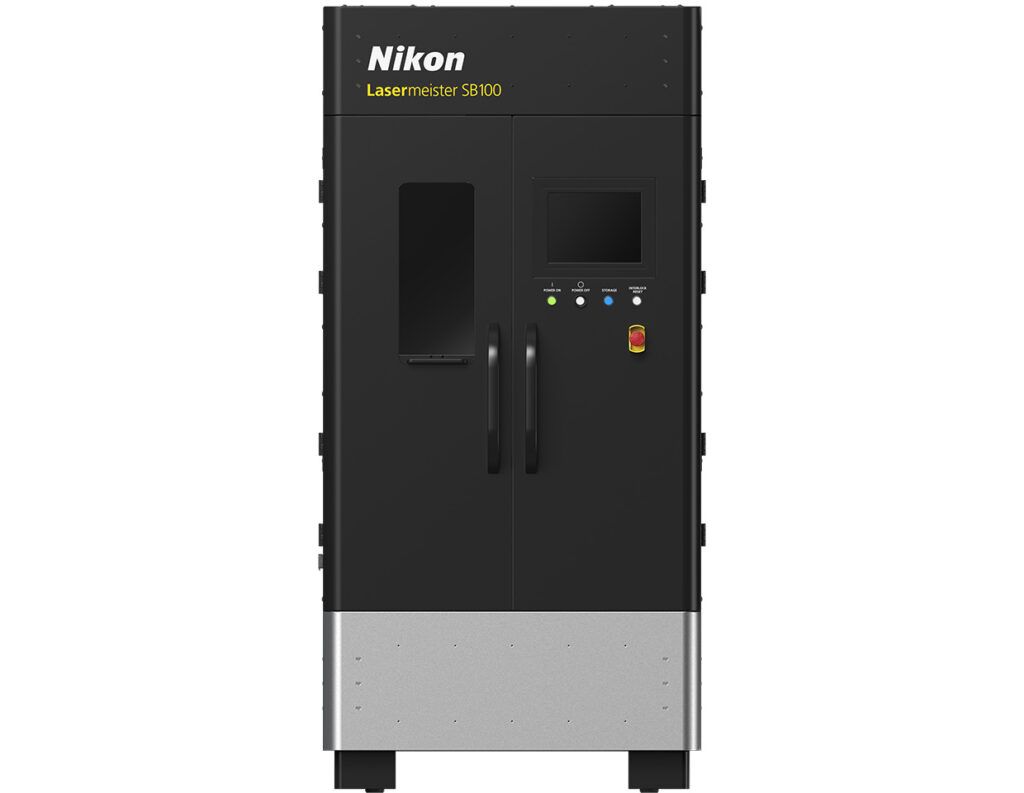
Why the focus on turbine blades?
Currently, turbine blades are used in aircraft engines and power generators to help extract energy from hot gas. However, due to exposure to harsh conditions, these turbine blades degrade over time and periodically the worn-out blades must be repaired to continue usage. The traditional turbine blade repair process involves cutting and scraping the worn area for each blade, which takes time and generates waste. The blade is then manually welded for repair and grinding is performed to restore the part to its ideal shape. This rigorous repair process introduces many challenges including difficulties in securing highly skilled welders, which can lead to quality consistency issues and long lead times.
With the LM300A and SB100, operators could reduce lead times up to 65%* of the conventional welding process and minimize post-processing requirements.
Apart from turbine blades, these solutions are also ideal for automobile, railway, machinery industry and other repair applications.
Key specifications of the LM300A
The 3D printer can support metal materials such as Nickel-based alloy (Ni625, Ni718), Stainless Steel (SUS316L), High-Speed Steel (SKH51/M2/HS6-5-2), and Titanium alloy (Ti64/Ti-6Al-4V), and it can be turned into an open system depending on customer requirements.
Thanks to real-time laser power control, the melt pool feedback system delivers smooth surface finishing and precise processing of parts, ultimately achieving crack-less repair with optimal quality and stability.
Dimensions (W x D x H) | 1800 mm x 1350 mm x 2085 mm |
Weight | 1350 kg |
Maximum processing range | X: 297 mm x Y: 210 mm x Z: 400 mm |
Powder provided by Nikon | Nickel based alloy (Ni625, Ni718), Stainless Steel (SUS316L), High Speed Steel (SKH51/M2/HS6-5-2), Titanium alloy (Ti64/Ti-6Al-4V) |
Axes | XYZ 3-axis |
Remember, you can post job opportunities in the AM Industry on 3D ADEPT Media free of charge or look for a job via our job board. Make sure to follow us on our social networks and subscribe to our weekly newsletter : Facebook, Twitter, LinkedIn & Instagram! If you want to be featured in the next issue of our digital magazine or if you hear a story that needs to be heard, make sure to send it to contact@3dadept.com