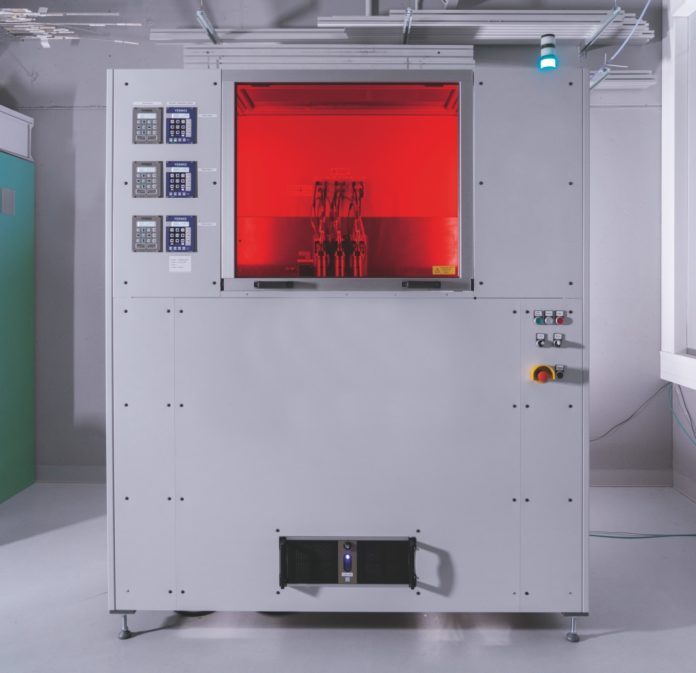
Researchers from the Fraunhofer Institute for Ceramic Technologies and Systems IKTS have developed a new AM technology that allows for the combination of several materials to form a 3D printed part.
The Multi Material Jetting system is based on thermoplastic binder systems. The focus on the development of this system has been made on improvements that were possible with metals and ceramic-based materials.
“Right now, we can process up to four different materials at a time,” says Uwe Scheithauer, a researcher at Fraunhofer IKTS.
Producing highly integrated multi-functional components with individually defined properties
Like in all AM processes, a continuous process is required to fabricate the part. However, researchers explain that the ceramic or metal powder from which the part will be made is distributed homogenously in a thermoplastic binder substance. The slurries produced in this way are loaded into micro-dosing systems (MDS) before the manufacturing process starts. These slurries are melted in the MDS at a temperature of around 100 degrees Celsius, creating a substance that can be released in very small droplets. The IKTS researchers also developed a corresponding software program to ensure precise positioning of the droplets during manufacturing. The micro-dosing systems operate in a high-precision, computer-controlled process, depositing the droplets one by one in exactly the right spot. This gradually builds up the part drop by drop at rates of up to 60 mm and 1,000 drops a second. The system works with droplet sizes of between 300 and 1000 μm, creating deposited layers with heights of between 100 and 200 μm. The maximum size of parts that can currently be manufactured is 20 × 20 × 18 centimeters.
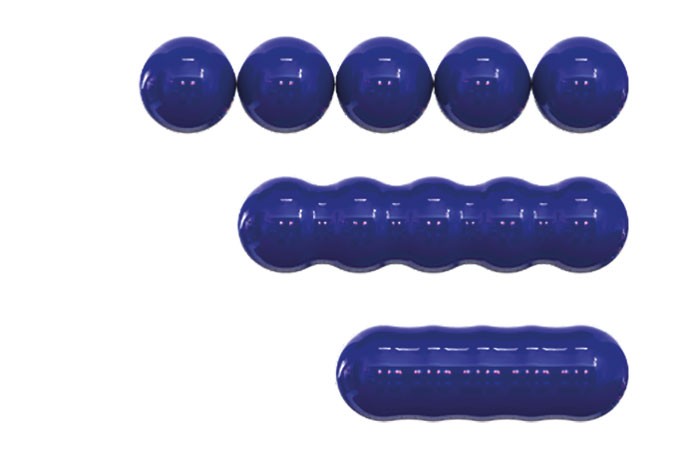
“The critical factor here is the custom dosing of the metal or ceramic slurries. Getting the dosing right is key to ensuring that the additively manufactured final product takes on the required properties and functions during subsequent sintering in the furnace, including properties such as strength, thermal conductivity and electrical conductivity,” says Scheithauer.
The new IKTS system can be used to make highly complex parts such as the ignition system in a satellite propulsion engine made of ceramics. Satellite engine combustion chambers reach extremely high temperatures, so the ability of ceramics to withstand heat makes them an ideal choice of material. MMJ can be used to produce an ignition system that is directly integrated within the engine. This ignition system combines electrically conductive and insulating areas in a single, extremely robust component.
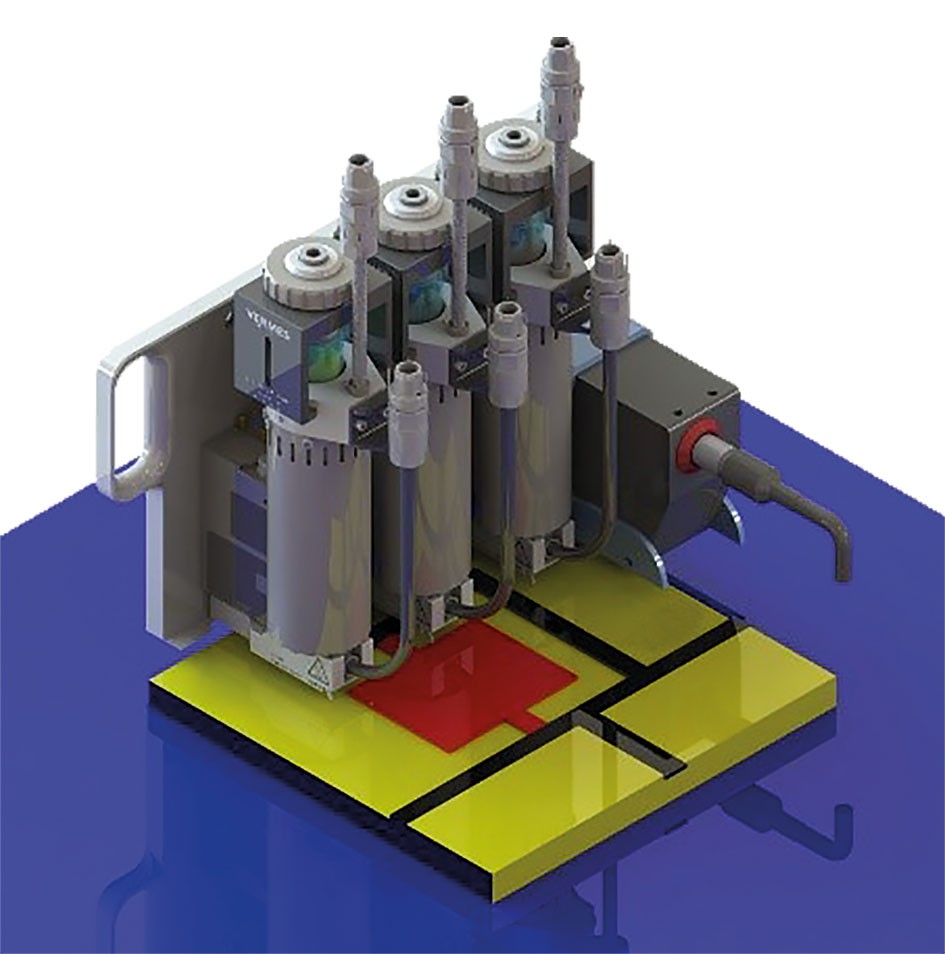
In this case, the MMJ process requires three dosing systems: one for a support material that disintegrates during heat treatment in the furnace, a second for the electrically conductive component, and a third for the electrically insulating component. MMJ also has plenty of conceivable applications in the consumer products market – for example, a two-tone ceramic watch bezel made for an individual customer as a one-off item.
Thanks to its high precision and flexibility, the MMJ system is suitable for more than just manufacturing multi-functional components.
“We could also use it to make blanks for carbide parts, for example. Thanks to the tremendous precision of the dosing systems, the contours of the blanks would already be very close to those of the end product. They would therefore require very little subsequent grinding as compared to conventional methods. That’s a big advantage when you are working with carbide,” says Scheithauer.
Validation and commercialization
The project at Fraunhofer IKTS has demonstrated that the technology also works in practice and is scalable. The next step is to validate the technology for industrial use. As well as supplying the hardware, Fraunhofer IKTS can also help industry customers develop the materials and software required for process monitoring and automation. Customers can therefore get everything from a single source, all tailored to their specific requirements.
Further information about this technology should sign up for the online AM Ceramics meets CERAMITEC Conference on September 16 and 17, 2020.
Remember, you can post AM job opportunities for free on 3D ADEPT Media or look for a job via our job board. Make sure to follow us on our social networks and subscribe to our weekly newsletter: Facebook, Twitter, LinkedIn & Instagram! If you want to be featured in the next issue of our digital magazine or if you hear a story that needs to be heard, make sure to send it to contact@3dadept.com