Based on the principle of building up a structure layer-by-layer, selective laser sintering (SLS) has been an ideal manufacturing technology to benefit from the many qualities of polyamide 12 (PA12). PA12 powders specially designed for SLS have been on the market since 1996. Created by Evonik, PA12 3D printing powders have been setting new standards in quality and useful features – helping expand the applications and possibilities of industrial 3D printing at scale.
The latest features in PA12 for powder bed fusion technology are INFINAM® PA 6013 P and INFINAM® PA 6014 P. Developed by Evonik, the SLS powders possess a relatively substantial amount of carbon black embedded inside the core-shell particle. The production of these powders is an engineering feat.
A specially developed production process

To create these novel powders, Evonik uses a special precipitation process they engineered. This enables a substantial amount of carbon black to be added to the PA12 polymer core-shell particle. Contrary to other existing carbon black powders, in which carbon black is dry blended or compounded, the special precipitation process allows for encapsulation, and (subsequently) for the PA12 particle to contain a comparatively higher amount of carbon black while maintaining good processability in SLS.
Precipitation is generally considered the ideal production process for powders used in powder bed fusion techniques, like SLS. In addition to enabling encapsulation, the precipitation of PA12 yields particles with the most preferable shape, and high flowablility, which are ideal for even sintering.
As the resulting new product contains both a PA12 shell and carbon black core, the powder possesses an interesting combination of characteristics.
PA 12 – the gold standard of polymer powders for SLS
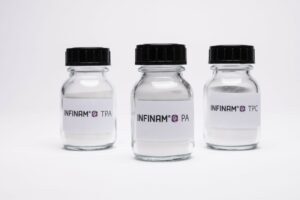
Pioneered by Evonik in the 1990s, polyamide 12, or PA12, has been continuously developed for the last 30 years to remain the ideal polymer-based SLS powder. A long-chain semicrystalline thermoplastic material, such as PA12 powders, is an ideal material for 3D printing elements used in prototypes, complex engineering projects, or low-volume customized applications. Taking it a step further, the material is also ideal for 3D printing made-to-measure medical devices for permanent or temporary body contact.
Key characteristics that make PA12 the ideal SLS polymer powder include:
- High mechanical resistance
- High chemical resistance, especially to oil, grease, and solvents
- Lower water intake
- Great impact strength
- Excellent surface resolution
- Easy processability
As such, the polymer performs well with applications in the aerospace, automotive, and medical industries.
Embedded with a significant amount of carbon black at the particle core, precipitated PA12 powders have an additional set of benefits.
Traditional PA12 powders are a neutral white, so the possibilities for further tinting are naturally infinite. This is typically done with a multi-step SLS printing, dyeing, and chemical smoothening to achieve the desired result.
When the desired color is black or a darker tone, 3D printing with carbon black encapsulated powders naturally eliminates the step of dyeing to achieve the final product. There are other benefits, however, that are due to the high ratio of carbon black at each tiny particle’s core:
- True pigmentation uniformity, for small and very large parts
- Minimized visibility of surface scratches, abrasion, and wear
- Elevated resistance to ultraviolet rays
- More isotropic performance (optimized elongation in z-direction)
These additional properties serve well in products that are destined for use outdoors – those needing to withstand an elevated amount of exposure to heat and light, such as certain applications in the automotive and aerospace industries.
A look at future developments in SLS polymers
The carbon black encapsulated INFINAM® PA 6013 P and INFINAM® PA 6014 P powders are just the latest features available for 3D printing polymers. In fact, with existing properties ranging from excellent surface finishing to food contact compliance and high processability, INFINAM® is found in virtually all PA12-based 3D printing processes. Regarding sustainability, all INFINAM ® products have a reduced carbon-emission footprint, as indicated by the RFP labeling in the product name.
Looking to the future, new developments in PA12 for SLS and other additive manufacturing technologies are currently in the works.
From 19-22 November in Frankfurt, Germany, Evonik’s experts will be on-site at Formnext 2024, the additive manufacturing world’s hub for networking and information sharing among production professionals.
At the event, Evonik’s top experts will present the latest details on the new carbon black encapsulated INFINAM® PA 6013 P and INFINAM® PA 6014 P powders, as well as showcase additional innovations and solutions for industrial 3D printing at scale (in Hall 12.1 C39).
Branded content | Remember, you can post free-of-charge job opportunities in the AM Industry on 3D ADEPT Media or look for a job via our job board. Make sure to follow us on our social networks and subscribe to our weekly newsletter: Facebook, Twitter, LinkedIn & Instagram! If you want to be featured in the next issue of our digital magazine or if you hear a story that needs to be heard, make sure to send it to contact@3dadept.com.