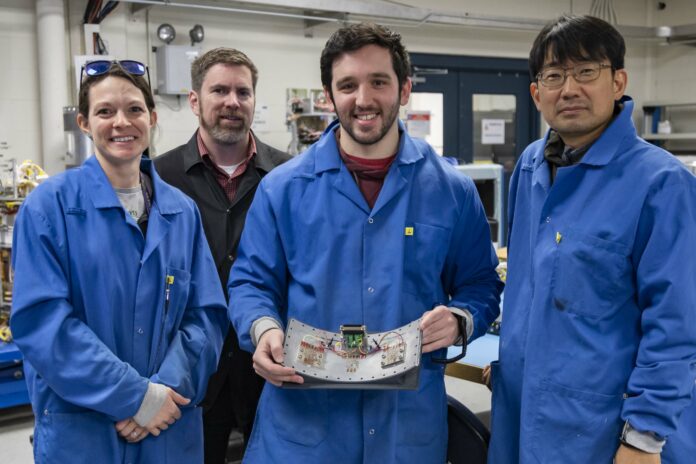
Engineers successfully tested hybrid printed circuits at the edge of space in an April 25 sounding rocket flight from NASA’s Wallops Flight Facility near Chincoteague, Virginia. Electronic temperature and humidity sensors printed onto the payload bay door and onto two attached panels monitored the entire SubTEC-9 sounding rocket mission, recording data that was beamed to the ground.
While the experiment sought to prove the space-readiness of printed electronics technology, it attracted the attention of engineer Ryan McClelland at NASA’s Goddard Space Flight Center in Greenbelt, Maryland. McClelland pioneered NASA’s use of Evolved Structures, spacecraft parts designed by artificial intelligence. He believes one “could use their printed electronics to add functionality to parts that may have been designed by AI and 3D printed themselves or even manufactured in orbit.”
The experiment
Aerospace engineer Beth Paquette and electronics engineer Margaret Samuels of NASA’s Goddard Space Flight Center in Greenbelt, Maryland worked with colleagues at NASA’s Marshall Space Flight Center in Huntsville, Alabama, who developed the humidity-sensing ink. Partners from the University of Maryland’s Laboratory for Physical Sciences (LPS) created the circuits.
Printed circuits allow a new level of functionality for smaller spacecraft, ever more common for both near-Earth and deep space missions, said Wallops electronics engineer Brian Banks. “The hybrid technology allows for circuits to be fabricated in locations that would typically not be available for conventional electronics modules,” Banks said. “Printing on curved surfaces could also be helpful for small, deployable sub-payloads where space is very limited.”
LPS engineer Jason Fleischer designed and printed the circuits for the April flight using printers capable of producing electronic traces thinner than the human eye can see. The SubTEC-9 launch marked a turning point in LPS’s development and validation of printed-circuit technology, he said.
“Every part needs to work throughout the flight,” Fleischer said, “and a successful data return means all the circuits were up and working. I’m excited for this success as well as getting on another rocket and having more successes.”
The team has printed electronic circuits on a variety of materials, including around curves and corners and on flexible parts. In another investigation, they printed X-ray instruments on flexible strips of Kapton plastic. The team is developing guidelines to make it easier for mission and instrument engineers to adopt these circuits.
Printed circuits provide a significant advantage in predictability and stability in antenna connections and design, Samuels said. “We can print the antenna on a curved surface like the outside of a rocket or spacecraft, increasing the angles at which it can send and receive signals in space.”
Remember, you can post job opportunities in the AM Industry on 3D ADEPT Media free of charge or look for a job via our job board. Make sure to follow us on our social networks and subscribe to our weekly newsletter: Facebook, Twitter, LinkedIn & Instagram ! If you want to be featured in the next issue of our digital magazine or if you hear a story that needs to be heard, make sure you send it to contact@3dadept.com