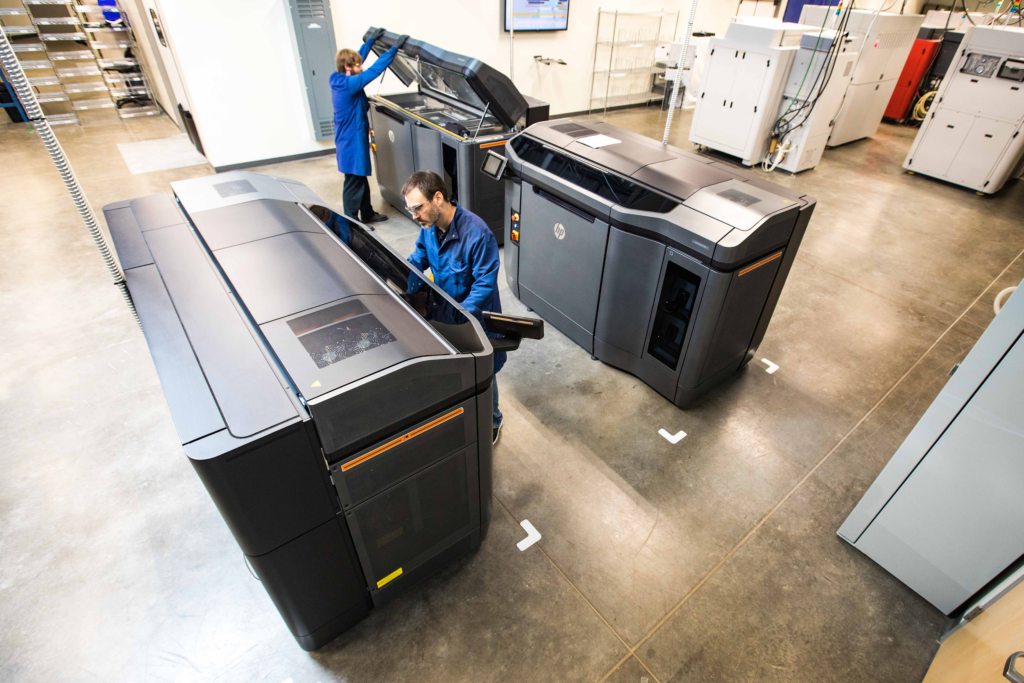
Multi-jet Fusion and Selective Laser Sintering are two of the most commonly used 3D printing processes around, but if you are considering employing one of these for your fabrication, rapid prototyping, or production runs, which is the best? Well, a lot of that depends upon your circumstances, so let’s consider these two processes, and their pros and cons.
Multi-Jet Fusion
The Multi-Jet Fusion process is a 3D printing technology which is fairly similar in operation to the Binder Jetting operation and produces similar types of components. It uses a liquid binding agent in order to build-up the different layers of the 3D printed part. Once this material is deposited on the powder bed, a detailing agent is also deposited in order to get the finest details and a smooth surface. Because the powders are fine, highly detailed components can be made.
The Multi Jet Fusion equipment uses heads akin to an inkjet array to selectively apply fusing and detailing agents across a bed of nylon powder, which are then fused by heating elements into a solid layer. After each layer, a powder is distributed on top of the bed and the process repeats until the part is complete.
When the build finishes, the entire powder bed with the encapsulated part is moved to a processing station where a majority of the loose powder is removed by an integrated vacuum. Parts are then bead blasted to remove any of the remaining residual powder before ultimately reaching the finishing department where they are dyed black to improve cosmetic appearance.
This 3D printing process needs less heat to fuse the powder than SLS. It still needs to cool once the part is ready, but it goes much faster. At that point, the building box is placed into the post-processing station which cools the parts and makes them ready for cleaning. Once de-powdering is done, your object is ready.
One of the main selling points of multi-jet printing is that it could produce the same, highly detailed and good quality components as the laser sintering process, but it’s cheaper and around ten times faster! However, being only able to use polymeric materials, it is limited in what it can construct in terms of functional or hard-wearing components.
However, if you require high strength along with your precision, then you might want to consider Selective Laser Sintering as an alternative process.
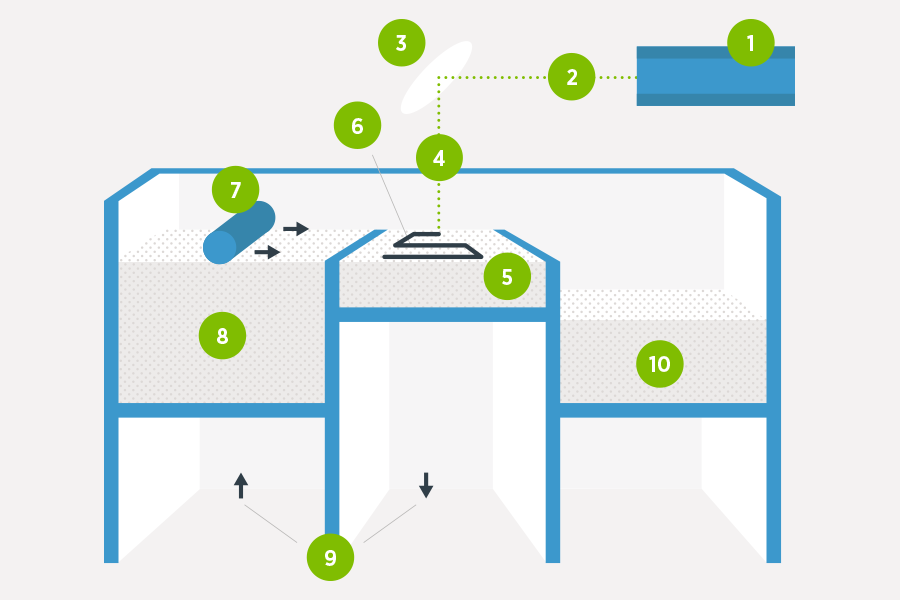
Selective Laser Sintering.
The highly flexible Selective Laser Sintering (SLS) process has become a very popular method of manufacture for product designers and engineers, thanks to its ability to rapidly convert complex CAD geometries into physical working models via CAM. With SLS capable of producing parts from easy to produce, commercially available materials such as Nylon there has also been significant growth in the number of companies turning to Selective Laser Sintering to meet prototyping needs and limited run manufacturing requirements. Selective Laser Sintering is a Powder Bed Fusion (PBF) process wherein a bed of powder polymer is either sintered by a high-power directional heating source such as a laser that results in a solidified layer of fused powder.
How does it work?
The SLS process begins with the conversion of customer-generated 3D CAD data into a sliced STL file using proprietary software designed for the job. Once created the STL file is then sent to print on the SLS machine for printing to begin. The printable material is heated to just below its melting point prior to the feed bed rising by a small increment (usually in the order of <0.1mm) and the levelling roller pushes fresh powder across the build platform/part bed.
The first layer is then traced out by a CO2 laser which melts and fuses the material as it makes contact. Once the first layer has completed the build platform/part bed drops by a pre-set amount, while the feeder bed rises and a fresh layer of powder is swept along the build platform. The next layer is then traced out and the process repeats layer by layer until the model has been completed. Once finished, the model is left to cool before being removed and any loose material brushed away to leave the final part.
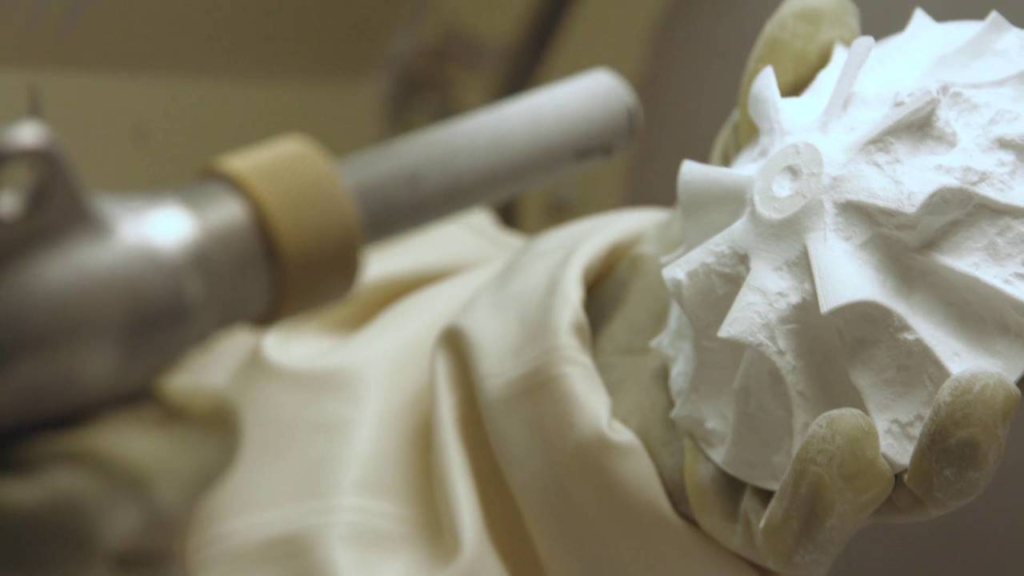
What’s Best?
It depends on the application and the materials that you require. Essentially, the main difference between MJF and SLS is the heat source used. SLS uses a CO2 laser to scan and sinter each cross-section, while in MJF an ink mixed with a fusing agent, which is dispensed on the powder and promotes the absorption of infrared light. An infrared energy source then passes over the building platform and fuses the inked areas. Because of its power, SLS can handle many different materials while MJF is really restricted to polymeric powders to create the final product.
SLS can be stronger components, but MJF is substantially quicker.
//pagead2.googlesyndication.com/pagead/js/adsbygoogle.js (adsbygoogle = window.adsbygoogle || []).push({});