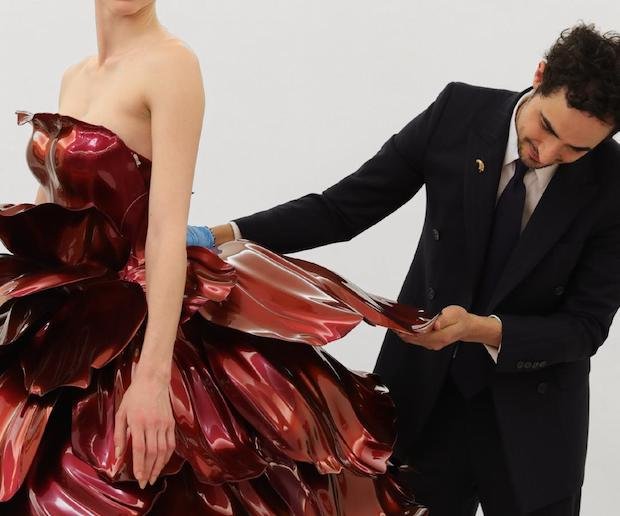
A line of 3D printed sculptural garments and accessories showcased at fashion’s ‘biggest night out’.
“The Met Gala is special for designers because it’s the biggest fashion event in the world”, said Zac Posen, acknowledged fashion designer. This year, it has become even special for the additive manufacturing industry because of 3D Printing’s input in the creation of an eye-catching 3D printed clear bustier and other original outfits.
Zac Prosen worked with GE Additive & Protolabs to create a wide range of 3D printed garments and accessories inspired by the concept of freezing natural objects in motion. A 6 month-collaboration that required over 1500 hours to produce creations that should meet the theme ‘Camp: Notes On Fashion‘.
The team finally unveiled four gowns, a headdress and a number of structural elements worn by Jourdan Dunn, Nina Dobrev, Katie Holmes, Julia Garner and Deepika Padukone.
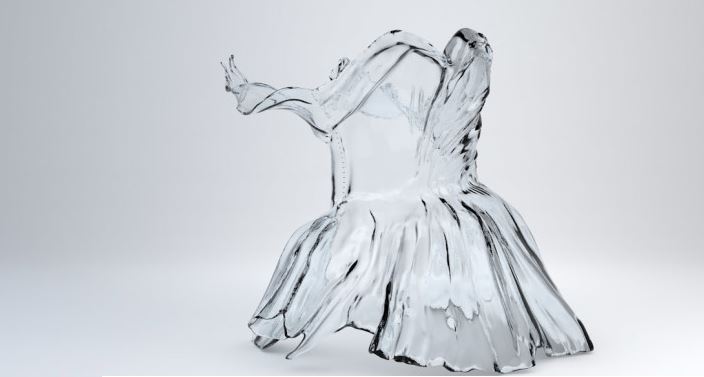
For those who are looking for technical specificities, please note that the rose gown features 21 unique 20-inch plastic petals printed with stereolithography (SLA) finished with primer and bold colour shifting red automotive paint.
As for the petals, it should be noted that each petal weighs 0.45 kg and was attached to a Titanium cage additively manufactured using GE Additive Arcam EBM system.
Moreover, another gown that requires the use of 3D printing technology is the 408 complex embroidery pieces for a metallic pink gown. The piece has been 3D printed in plastic; vacuum metalized before painting. Other 3D printed accessories include brooches and cufflinks.
“For me, science, engineering and art all work together. That’s why standing at the forefront of 3D printing is so important”, explained the fashion designer.
Daniel Cohn, General Manager of Protolabs, added his support: “In a fashion project like this, 3D printing gives designers almost complete creative freedom.
“Designers are no longer limited by traditional manufacturing processes, where a project would be curtailed by questions like ‘can a part be cut to this shape’ or ‘can it suspend itself under its own weight’. What we have here is a very pure design process, from concept to physical part.”
For further information about 3D Printing, follow us on our social networks and subscribe to our newsletter! Source : Bdaily News
Would you like to be featured in the next issue of our digital magazine? Send us an email at contact@3dadept.com
//pagead2.googlesyndication.com/pagead/js/adsbygoogle.js (adsbygoogle = window.adsbygoogle || []).push({});