Exclusive Interview with Johan-Till Broer, VP of Product Development at MakerBot, on the launch of the new MakerBot CloudPrint™ software
Remote working has become the new norm for several sectors of activity, but this new standard raises significant challenges for certain sectors such as the manufacturing industry. Indeed, manufacturing plants/production units greatly depend on operators to keep machines running and this simply makes remote working complicated to handle. To reduce operational impact, most companies need to rush to implement new processes.
The new MakerBot CloudPrint™ software is very timely as it is designed to deliver a seamless 3D printing workflow for teams to collaborate around the world. Stratasys’ subsidiary has been developing the free cloud-based 3D printing platform for a while but its release makes more sense today as the “physical constraint” in the manufacturing industry can impact productivity.
The constraints of production teams that use 3D printing/AM
The production of a part usually involves technical processes and materials, which ultimately lead to a collaboration in which different teams rapidly emerge and disband in real-time around objectives.
Furthermore, to work properly together, these teams often leverage several disconnected systems including email, excel sheets and enterprise systems like ERP, API, CRM to exchange data and to ensure good advancement of their project. At some point, these disconnected systems also require the need for in-person meetings, to ensure status updates and reviews.
To evaluate a new design for a new product, for instance, it’s crucial to ensure that every department involved in product development has the opportunity to look at the new design and gives its feedback. Therefore, the design file will be sent to all the 3D printers of each department at the same time.
Moreover, when several engineers have to share a single 3D printer, a queuing system becomes crucial to integrate, to manage the printing platform and the different projects of the teams.
This queuing system is even more important when there are several 3D printers in multiple locations and several administrators. Indeed, the more 3D printers there are, the more engineers will need to manage production capacity within the production workflow.
Not to mention that it may also happen that someone is not familiar with 3D printing. In this case, that person could just send the file to a more experienced-user in the office that will launch the print.
These situations are just a few examples of a non-exhaustive list that might lead to a disruption in work and, ultimately, a decrease in performance when they are not well coordinated.
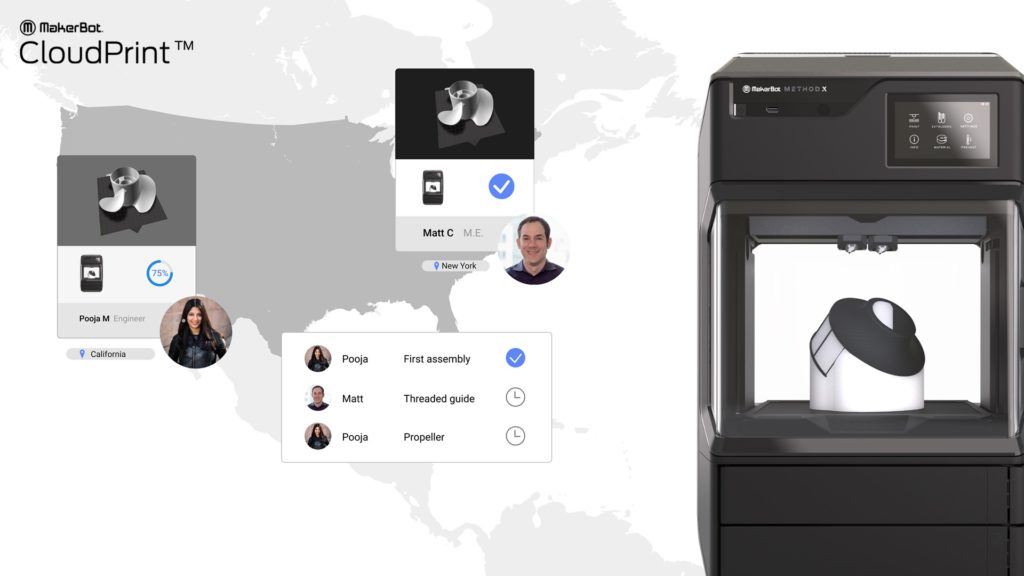
“With many people in our team working remotely, we’ve realized the importance of having a process that would have enabled both individuals and teams to continue collaborating or working on single projects from anywhere. The CloudPrint™ software has been in development for a while, but in today’s environment, it has become a necessity to give engineers and designers access to 3D printing platform(s) from within their browser and across any device. For MakerBot, this solution is another step to making 3D printing more accessible”, Johan-Till Broer states.
MakerBot CloudPrint™, the transition from a physical location to a digital one
Right now, the advantages of a cloud-based 3D printing platform, seem more blatant as most professionals are working from different locations. However, even though they work in the same environment, they will still have to follow some basic steps to ensure a fluent production workflow and minimize printer downtime between projects.
No matter what the case is, the CloudPrint™ software helps ensure these basic steps. First steps usually include print preparation and printer management. Directly from their browser, engineers can edit, preview and find the ideal positioning of their print file. Using optimized print modes, and advanced settings of the MakerBot METHOD platform, they can easily follow the print jobs progress on connected printers. The live camera on the METHOD platform can provide the printing updates but to add, monitor and control access to the 3D printers, a dedicated dashboard can help track and view prints while creating reports to assess the printers’ performance.
“Downloadable analytics will help the engineer to know which department is in charge of what. Moreover, since the platform is cloud-based, it makes it easier to integrate with other solutions. The integration with Google products, for instance, guarantees access to MakerBot applications with other tools,” the VP of Product Development adds.
“Another main feature for remote team members is queuing as it helps improve the printer’s performance. Indeed, when there are several users, several 3D printers or when there are several projects to achieve, the queuing feature provides key insights into each print job and trace each project from its beginning to the end”, Johan-Till Broer continues.
In this vein, the queuing feature also enables collaborative processes. Indeed, be it from a user point of view or a printer’s perspective, there is no limit when it comes to the number of users or machines that can be connected at the same time on the platform. Classrooms, engineering teams in labs, in SMEs or large companies can leverage MakerBot CloudPrint™ with one 3D printer or several 3D printers. To mitigate risks due to multiple printers’ management, MakerBot’s VP of Product Development explains that those 3D printers can be disposed into workspaces. Team members will, therefore, receive permission to better control and access the workplace. In this case, each team leader will approve the print jobs submitted by the rest of the team.
Lastly, “one advantage of our METHOD platform is that its settings can always be extended to achieve advanced capabilities of the printing process”, Johan-Till Broer points out.
As a reminder, the 3D printer manufacturer has recently unveiled a new extruder that can turn its 3D Printer into an open materials platform. With a modified hot end, the MakerBot LABS™ includes interchangeable nozzle assemblies and broadens print settings in MakerBot’s print preparation software, MakerBot Print. Not only can it reach up to 300°C, but it also includes sensors that track temperature, materials, and extruder jams.
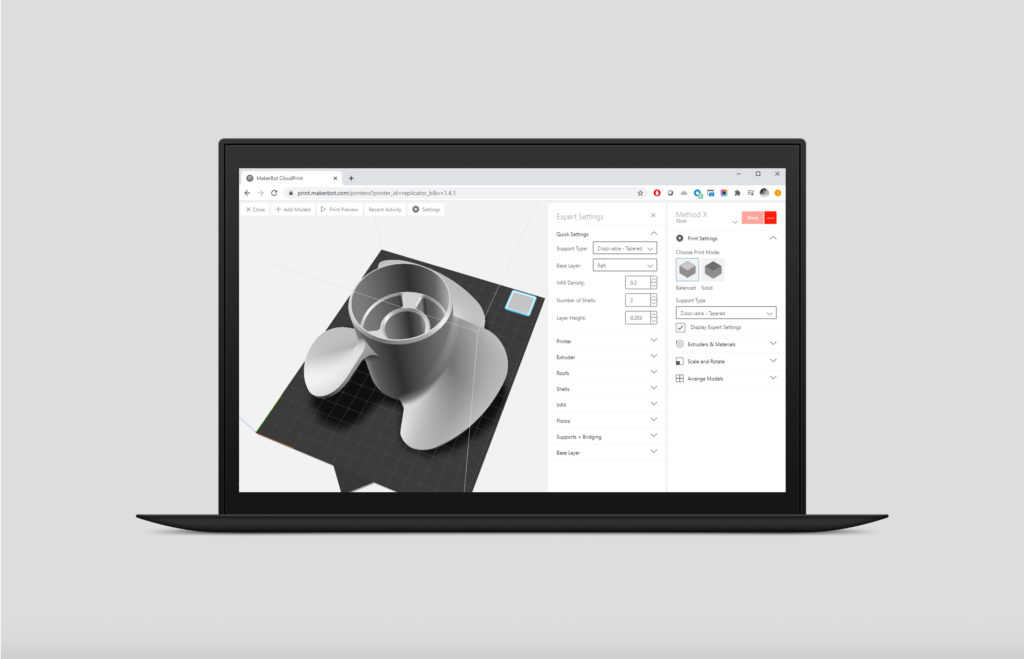
Enhanced accessibility for filament suppliers
MakerBot’s commitment to advancing innovators and institutions involves its partnerships with material suppliers. Since the launch of its materials development program, the company has been partnering with well-established filament suppliers including Polymaker, ARMOR, Mitsubishi Chemical and Jabil, to bring additional materials to the METHOD platform. As Broer explains : “these partners are qualifying their materials for the METHOD platform and tuning their materials requires the use of several settings. With the CloudPrint™ software, we are also giving them more flexibility and advanced tools so that they continue to develop materials for our platform.”
Productivity & versatility
While it addresses the current productivity challenges in the manufacturing industry, the MakerBot CloudPrint™ softwaredelivers the perfect combination of theMakerBot Print™ features and the scalability of the cloud.
In addition to the METHOD 3D printers, other solutions from the company that can be used with the cloud-based platform include the MakerBot SKETCH Classroom™ bundle and the MakerBot Replicator® 3D printer series.
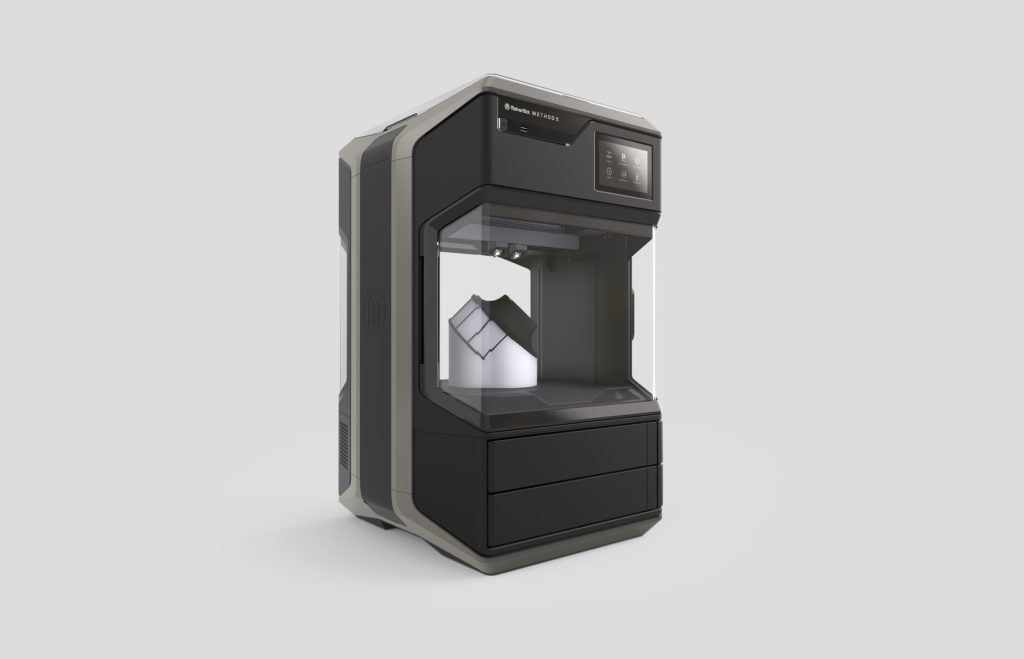
“Our users understand how our work is automated and one of our biggest strengths in every solution that we deliver is that we ensure a user-friendly experience. This is true for our 3D printers and it is true for our software solutions as well. A FAQ segment has been established to help engineers that would encounter any issues while using the CloudPrint™software. This release is a very first and big step for MakerBot. We plan to launch additional features for the software, in the long run, to ensure a continuous support for remote workforces and collaborative processes”, Johan-Till Broer enthuses.
As 3D printing/additive manufacturing matures, the technology’s advancement finds itself impacted by the uncertainty of the current socio-economic environment, an environment in which connected solutions have proved out their efficiency, an environment in which the MakerBot CloudPrint™ perfectly fits.
Remember, you can post AM job opportunities for free on 3D ADEPT Media or look for a job via our job board. Make sure to follow us on our social networks and subscribe to our weekly newsletter: Facebook, Twitter, LinkedIn & Instagram! If you want to be featured in the next issue of our digital magazine or if you hear a story that needs to be heard, make sure to send it to contact@3dadept.com