Additive manufacturing companies as well as industrials in general are increasingly trying to overcome the issue of lightweighting in their manufacturing process. It is a true paradox because this issue has led to uncertainty but also a wide range of opportunities for companies using materials such as Magnesium and CFRP within the industry.
In a market research entitled Composites 2017-2027: Innovations, Opportunities, Market Forecasts and Lightweight Metals 2018-2028: Forecasts, Developments, Players, IDTechEx brings out the good and the bad of these materials and presents the challenges faced by the market .
The advantages
If you are a professional that has already exploits both materials, then you will certainly agree with the fact that both materials provide very good lightweight options. Furthermore, due to regulations and performance drivers, they are increasingly used by the industry.
CFRP integrates anisotropic properties because of the use of a fiber which leads to unparalleled tensile strength and stiffness to weight. The material also enables provides good corrosion resistance and is versatile through the choice of polymer, fiber content and orientation. However, a closer look should be taken at the growing use of thermoplastics, robotic automation, and multifunctionality.
Magnesium on its side is 33% lighter than aluminium. “Although the stiffness-to-weight ratio for steel, aluminium, and magnesium are the same this does not scale linearly with thickness.” The material is interesting because of its abundance of metal. Plus, it is recyclable, integrates good NVH properties and a very good fluidity in casting.
The disadvantages
The disadvantages of CFRP show up when it comes to repair, reuse and recyclability of parts on the one hand, on the other hand, the costs and challenges in volume manufacturing.
As for magnesium, have a look at the table below which presents the main difficulties in its use:
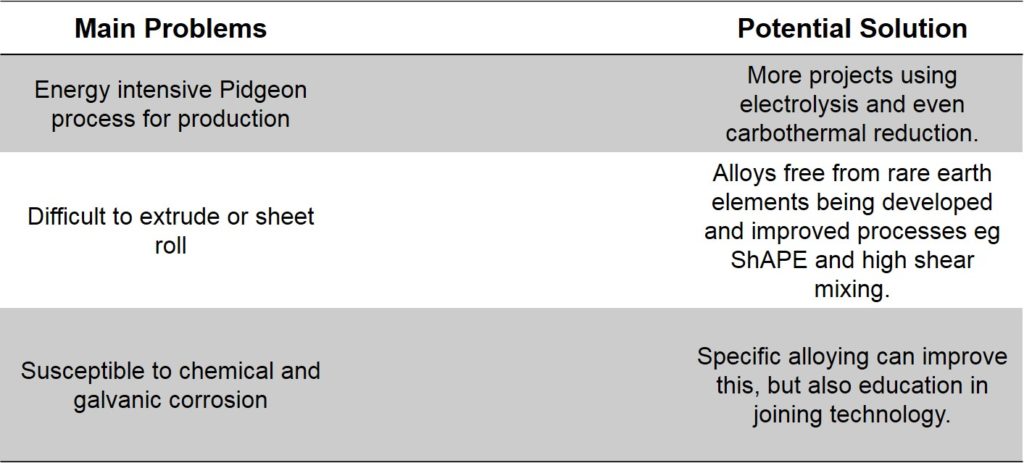
The market
The truth is that CFRP has the healthier growth rate and its increasing use is driving capacity expansions. Aerospace is obviously a key sector for this material, but other areas are starting exploiting it including automotive, energy, and infrastructure applications.
Magnesium is still dominated by die casting applications and predominant use in the automotive sector. As the graph shows the capacity still significant outstrips demand, but this gap will narrow over the next 10-year period.
The whole report can be found on IDTechnEx’ website.
For further information about 3D Printing, follow us on our social networks and subscribe to our newsletter!
Would you like to be featured in the next issue of our digital magazine? Send us an email at contact@3dadept.com
//pagead2.googlesyndication.com/pagead/js/adsbygoogle.js
(adsbygoogle = window.adsbygoogle || []).push({});