Most applications of additive manufacturing in the food industry reveal several alternatives to food products such as milk, meat or even fish, that all aim to protect animals. Interestingly, at the manufacturing level, there are also interesting applications to discover, applications that show that innovation in the food industry can go beyond flavour.
Loctite, the additive manufacturing brand of Henkel, has recently supported a startup confectionary company in the production of personalized candies for a variety of purposes such as special events or corporate outings.
The challenge was enormous for the confectionary company that wanted to bring a new product to the market. As a startup, such product development requires money and resources and in their specific case, the ability to demonstrate traction. Among other upfront costs, the manufacturing process for such production implies a big investment in tooling, especially moulds for silicone casting. They are traditionally machined from aluminum and then nickel plated to meet the U.S. Food and Drug (FDA) standards for food safe materials. Silicone is then poured into the tool to form the final mould.
That’s where Henkel comes into play. The AM team of the German chemical and consumer goods company wanted to show the startup that AM might might improve their workflow while being cost-efficient. Interestingly, the issue they addressed, goes beyond the simple use of the technology.
“For many entrepreneurs, the cost of tooling is a dead stop,” says David Brady, European Business Development Manager for Henkel AM Services. “With the help of our Open Materials Platform partners, we engineered a cohesive solution. Beyond just 3D printing a tool, we were able to develop an end to end manufacturing process for the food industry. Normally, the time to produce a complex machined tool can take at least four weeks. While they can be made with aluminum, more often the tools are machined in steel, polished and then nickel plated, which usually makes them even more expensive. In the confectionary industry, even a relatively simple molding tool would typically cost over 10,000 Euro. By reducing the cost and time involved with mold making, we’re fulfilling the promise of additive manufacturing and leveling the playing field for a new market innovator.”
How to meet the stringent requirements of food manufacturing
In terms of regulations, the need to approve Nickel plated coatings is due to the fact that they deliver corrosion prevention and easy cleanup. Furthermore, thank to Nickel plating, products can easily withstand the extreme hot and cold temperatures that are usually observed in food processing.
The experts at Henkel explain that Nickel plating also offers a nonstick coating that is resistant to water, oils, fats and steam, making it ideal for molding silicone. However, this time, rather than machining the molds from aluminum or steel, they 3D printed them and then coated with an FDA approved nickel plating.
Henkel’s materials expertise was crucial to this project as the latter requires a hard and tough resin; a resin that would have provided a surface finish suitable for electroplating. The team utilized then the LOCTITE 3843 resin and processed it on a RapidShape i30+ DLP 3D Printer.
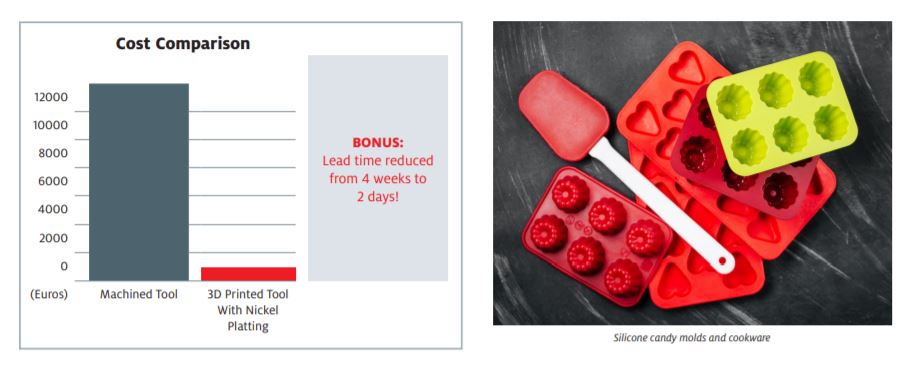
As a reminder, Henkel has recently added Rapid Shape to its production portfolio. And this project demonstrates that Rapid Shape DLP Technology is not only meant for dental applications.
“After the test tools were printed, they went on to be electroplated in nickel. Then, silicone was poured into the nickel-plated test tool. Finally, the complete silicone mold is released, and the candies are manufactured”, Henkel concludes.
Remember, you can post free of charge job opportunities in the AM Industry on 3D ADEPT Media or look for a job via our job board. Make sure to follow us on our social networks and subscribe to our weekly newsletter : Facebook, Twitter, LinkedIn & Instagram ! If you want to be featured in the next issue of our digital magazine or if you hear a story that needs to be heard, make sure to send it to contact@3dadept.com