On the heels of a dossier that highlights “the current manufacturing landscape of Ceramic 3D printing and the business model that drives industrial applications” (March/April edition of 3D ADEPT Mag – pp 6-12), it feels right to focus on a vertical industry where there is still a long way to go for industry professionals to fully exploit the potential of ceramic 3D printing: the healthcare and medical industries.
There are dozens of publications and research that have analyzed and forecasted the growth rates of the use of additive manufacturing in the healthcare industry or the ceramic 3D printing market as a whole, but it’s hard to find the weight of ceramic additive manufacturing alone in the healthcare industry. Yet we know that ceramics are an integral part of the medical field, and given the range of applications and processes associated with custom-made medical products, they can be the best part of it.
Indeed, ceramics’ outstanding properties is ideal for a number of applications across the healthcare industry. A few examples of applications that have already been achieved, include but are not limited to medical implants (ear, femoral head implant for hip replacement, implants for neurology), CAT scans, pacemakers, components for cardiology, hand tools, valves and filters, pressure sensors, X-ray tubes, laser and reconstructive surgery and obviously, dental applications.
Moreover, ceramics are also ideal to help diagnose ailments. Medical centers and laboratories rely on ceramic and glass lab ware for chemical analyses and electronic components.
The truth is, the various uses of ceramics are evolving all the time as new technologies emerge. Furthermore, applications and advantages of ceramics are often more highlighted at the expense of their limitations and solutions to overcome them, most importantly, at the expense of key elements industry professionals should consider when leveraging ceramic AM for medical devices and healthcare applications. And these are some of the key areas this exclusive feature ambitions to address.
Use of AM in the healthcare industry: ceramic 3D printing vs other AM processes?
Most applications that are successfully completed via AM are usually described and highlighted through the lens of conventional manufacturing processes as the primary angle of comparison. Over time, with the advancements of AM technologies and their ability to meet the production requirements of several industries, we increasingly see the advantages of certain AM technologies more highlighted for certain applications. This can be seen in the healthcare industry as well, where we have seen applications made possible with various types of metal AM processes or polymer 3D printing.
“Usually, when we talk about ceramic 3D printing applications, the comparison is easily made with conventional manufacturing processes such as injection moulding and milling”, Dr. Daniel Bomze, Director Medical Solutions at Lithoz lays emphasis on, from the outset.
“However, when we look at the broad range of AM processes that can address the production requirements of various industries, ceramics are likely to compete with metals such as Titanium, cobalt chrome which is used in orthopedic and dental applications, and high-performance polymers like PEEK which can be 3D printed in different ways and resorbable materials. The choice of an additive manufacturing material will therefore depend on where we want to provide a solution. In resorbable applications for instance, metals will not be the ideal choice in terms of materials, while in the polymeric side of the business, there are already materials that are already resorbable”, he continues.
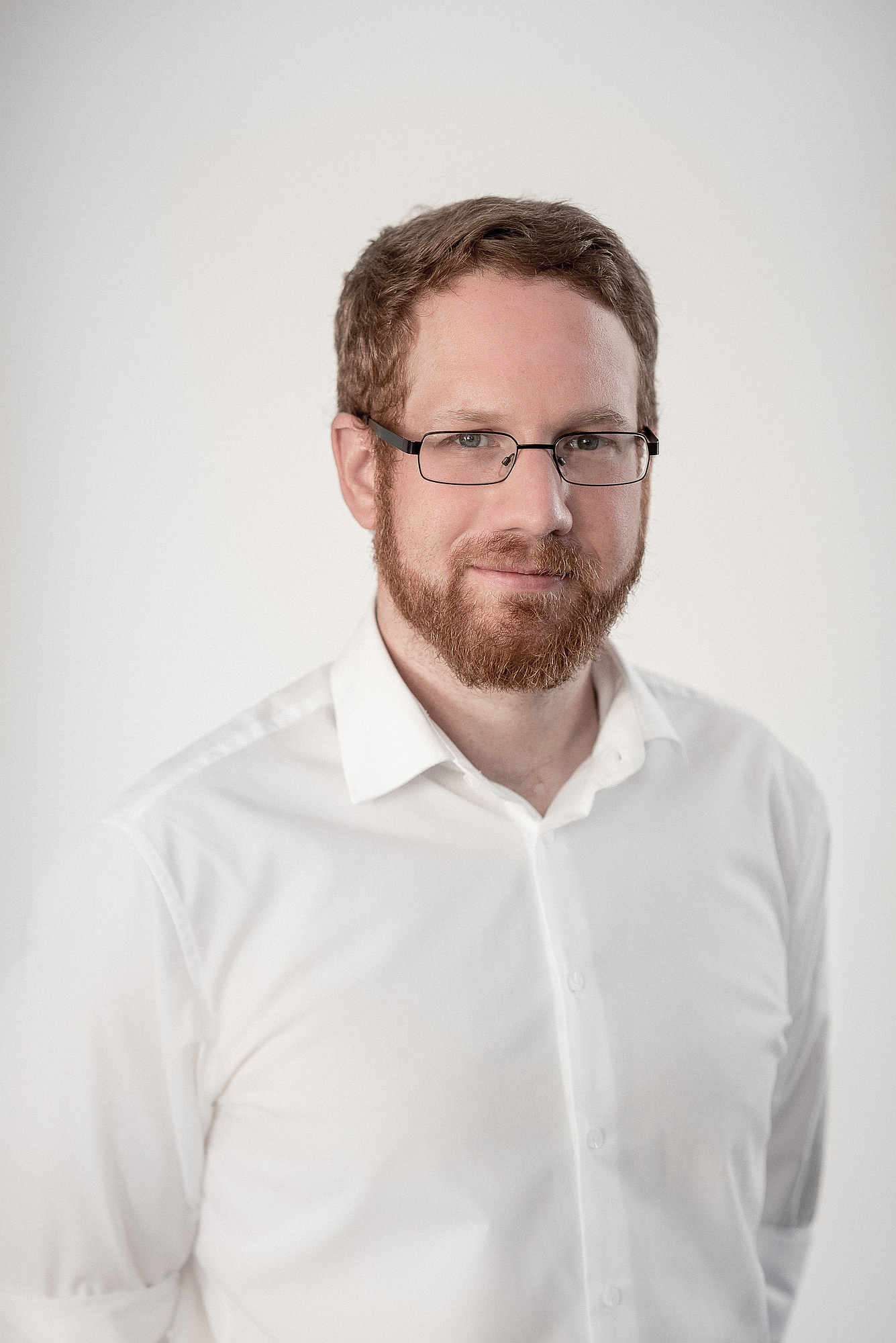
Lithoz is one of the companies you easily come across when you have a slight interest in ceramic 3D printing. The AM company headquartered in Austria is known for a comprehensive range of solutions (machines, software and materials) for 3D printing high-performance ceramics. At the heart of this expertise lies a proprietary lithography-based ceramic manufacturing process; a fabrication process where ceramic particles are dispersed in a photosensitive resin and this dispersion is thereafter solidified by light layer-by-layer to form a part. Then the part undergoes a sintering process to develop its ceramic properties and can be used for its final purpose.
As said during a conversation with Lithoz’ CEO & co-founder, Dr Johannes Homa, the company’s technology has been validated in three main vertical industries; medical, aerospace & space, and energy. However, the medical applications enabled by their ceramic 3D printing are the ones that have always struck my attention the most. And for good reasons, the use of ceramics in medical devices is changing rapidly as the development of this market is mainly linked to the development of technical ceramics. This urges healthcare professionals to pay more attention to changing factors that may influence their decision-making process when exploring ceramic AM for patient-specific applications.
Key factors to consider when exploring technical ceramics in medical 3D printing applications
The development of technical ceramics in both healthcare and medical applications is quite modern. To make it easy to understand for users, technical ceramics have been categorized into four main groups: oxide ceramics, non-oxide ceramics, bioceramics and other types of materials that are not found in the aforementioned three categories.
Oxide ceramics have popularized ceramic 3D printing thanks to their affordable cost and ability to be easily processed. Categorized as non-metallic mineral materials, they do not contain more than 15% silica with little or no glass phase. These binary oxides include for instance alumina and zirconia. Known for the applications they enable in medical implants and dentistry – outside of AM -, they have quickly become some of the most popular ceramic 3D printing materials available on the market.

Bioceramics are a class of advanced ceramics that increasingly raise the interest of healthcare professionals due to their ability to be used within the body. They are often employed in medical and dental applications, mainly as implants and replacements. Not only for their biocompatibility, but also for their ability to help the body repair itself. Promising applications of bioceramics are therefore seen in reconstructive surgery. According to Bomze, one of their biggest advantage is their unlimited availability. For reconstructive surgeries where bone graft is needed, it may happen that the surgeon requires a large area of extraction to achieve better results. In that case, the bone tissue might require a separate procedure, which means double surgery, and increased risks of complications for both the patient and the surgeon. Whereas artificial bones created using bioceramics may lead to patient-specific 3D printed solutions while “removing the need for further surgeries.” Although they might lead to more brittleness as they do not have the elasticity of bone tissues, Bomze outlines that “with artificial bones, the chemical composition is exactly the same than the mineral fraction of the bone.” Lastly, their utilization also reduces “the surgery time in the operating room and a better patient experience.”
Although they will not raise our interest that much in this feature, let’s note that non-oxide ceramics, such as silicon nitride (available for the LCM technology) and aluminum nitride, are useful in extreme environments given their high heat and corrosion resistance. However, compared to oxide ceramics, they are quite expensive and difficult to print.
Interestingly, Lithoz has built up extensive expertise in the development of materials for these three categories. For the Director Medical Solutions at Lithoz, the first criteria that should be assessed when exploring technical ceramics in medical 3D printing, is the properties of the selected material for a given application.
“Ceramics have outstanding properties and in some cases, they can be the only option for specific applications and requirements. However, as all materials, they cannot be the solution for all issues. What’s really important here is to understand first the customer requirements and to select the materials that best meet these requirements. In industrial applications for instance, aluminum nitride may be the ideal ceramic to go with, but you won’t probably use it to create a crown – dental part – because it’s more brittle than zirconia.
And if you do not look at the materials side first when you explore ceramic 3D printing, then I would recommend to assess other details. Almost all technologies’ providers are looking to print the part that looks at first glance to the geometry that the customer requests – This part is often called ‘green part’. However, it’s only after sintering that you will be able to tell if you can rely on the part’s properties, or if the machine you invested in, can produce green parts, you will never be able to manufacture ceramic parts because there will be cracks, and other issues related to size and dimensions.
Therefore, before investing in a production technology, it’s important to understand all the consequences that may result from every type of production and the details that are often least highlighted.”
Bomze’s statement is quite interesting to the extent that it brings forward the fact that we do not talk enough about the limitations of AM technologies and/or materials and how they can be addressed in manufacturing. This applies to technical ceramics that are usually highlighted for their ability to deliver performance that other materials simply cannot, which is true. As a matter of fact, they are robust, and can survive extreme stresses, temperatures, nuclear radiation or highly aggressive chemicals. But that is not all because most ceramics are generally brittle. That’s why they are not always self-sufficient.
“The original fact of ceramics’ brittleness, in my opinion, can be directly addressed by developing new types of ceramics. At Lithoz, we have developed a solid area of expertise in the development of new types of printable ceramic materials which led our customers to develop various forms of 3D objects. Also Lithoz works very closely with ceramic powder manufacturers to offer newly developed ceramic materials for additive manufacturing on the market. Furthermore, with the advancements we made in multi-material 3D printing, we came to realize that combining different kinds of materials enable to address most of the disadvantages raised by technical ceramics.
Let’s take the example of two kinds of ceramics: bioresorbable materials – osseoconductive materials that facilitate bone regeneration – and zirconia oxide, a high-performance ceramic. The combination of these materials allows to fulfill the requirements of a critical size-effect in load-bearing body implants.
In certain applications for instance, you might want to combine zirconia with some types of metals in order to have the elastic properties of a metal with for example, some wear resistance properties of ceramics. Ceramics could be used as a cover to protect the part and metals as a electrical conductive element. At the end, the part created, benefits from the combination of each material selected.
Another solution that is worth mentioning might be to go with non-sintered ceramics. If you use for example, a highly-filled resorbable polymer material with a certain ceramic, you would not come up with a pure ceramic in the end, but rather a composite material that could address the brittleness of ceramics.
At Lithoz, we have also tried the combination of glass fiber and carbon fiber which works well. However, it might come with some limitations and our R&D team is currently working on them” Bomze explains.
Lithoz’s representative also raised our attention on the fact that limitations of technical ceramics may also depend on the manufacturing technology you use to process them.
“For every manufacturing process used for medical devices, you need to adapt your processes. At first glance, this might sound like extra work but if it allows you to benefit from the design freedom of AM, then you should do it properly. In this case for instance, it’s crucial to understand the design rules in ceramic AM to know exactly all the advantages that may result from a given application versus the disadvantages. I believe that understanding these design rules are essential to get out the most of the technology”, he adds

Focus on applications: digital dentistry
Lithoz’ technology may have proven itself in various fields of the medical and healthcare industries, but the most prominent advancements are currently seen in dental applications. As a reminder, it’s been a while that the company has been working on the development of 3D printed ceramic dental implants alongside Dr. Jens Tartsch, the founder and president of the European Society for Ceramic Implantology (ESCI) and Metoxit, a Swiss high-tech ceramics company that develops oxide ceramics.
Today, the company prides itself on the ability to deliver mass production of complex shaped implants based on patient-specific designs using Lithography-based Ceramic Manufacturing (LCM) technology. Currently in its portfolio, materials that can enable dental 3D printed productions include Zirconia, ATZ and ZTA.
“Zirconia (3 mol% yttria partially-stabilized) offers excellent strength without having to make major compromises on aesthetics. Another newly emerged material in this context is silicon nitride. It provides an exceptional combination of biocompatibility, antibacterial and high-mechanical performances. Another advantage of using silicon nitride for implants is the good nano-roughness of the surface, which strongly facilitates bone attachment. By processing this material with the LCM technology, the micro-roughness can be varied by using different layer heights and helping to produce an implant on which bone cells can anchor and grow on. Materials such as ATZ (alumina toughened zirconia) and ZTA (zirconia toughened alumina) are also suitable for dental applications. Unlike metals, there is no debate around ion release or corrosion and they have long-term stability both in soft and in hard tissue”, the company points out.
In dental applications especially, LCM makes it easy to scale up the production compared to milling, not to mention that the fact that the platform uses 95% of the material used, does not prevent the reproducibility of the layers.
CF System S65 | 4 x CF System S65 | |
Implants per run | 153 | 612 |
Production time | 5,6 hours | 5,6 |
Building time per implant | 3 min | 0,5 min |
Implants produced in 24h | 656 | 2624 |
Table: the table below reveals the productivity of CeraFab System S65 (103x64x320 mm³) (standalone and modular) for the production of dental implants and how the shift can easily be made from prototyping to serial production.
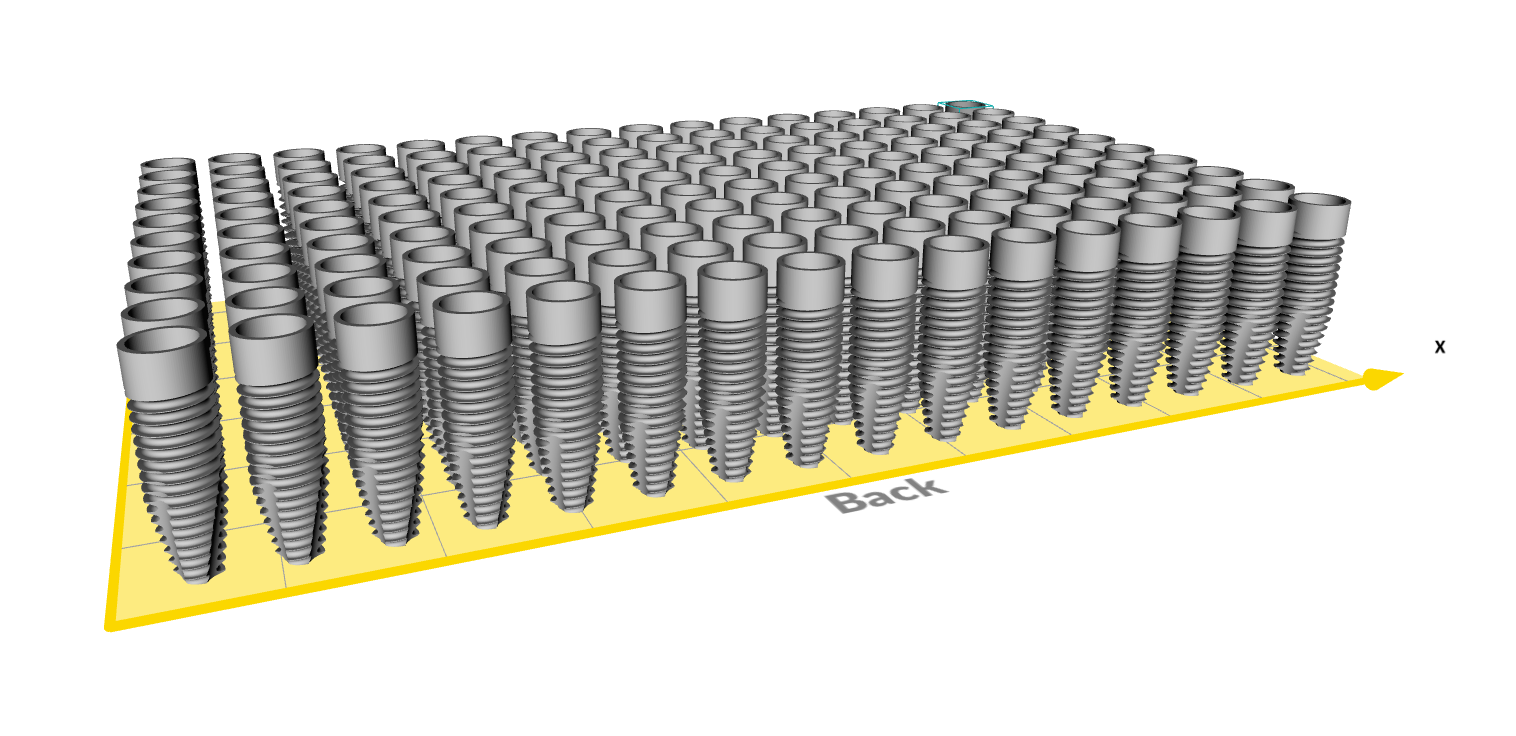
That being said, dental implants may be the most highlighted applications in digital dentistry, but it should be noted that LCM can also be a great fit for dental restorations (Bruxism, a medical term that describes a condition in which somebody grinds, gnashes or clenches his/her teeth.).
In this case, unlike conventional manufacturing processes, AM has the unique advantage to achieve thin, ‘tabletop’ veneers, with unprecedented accuracy.
“The process starts with a scan of the tooth, from which a digital model is created. This model is then accurately and efficiently 3D printed, minimizing material consumption compared to milling or heat pressing. Once debinded and sintered, the restoration is ready to be fitted, avoiding the removal of the healthy tooth material and therefore fulfilling the principles of minimal invasive treatment and maximum patient satisfaction”, a Lithoz report reads.
And right now…?
The use of technical ceramics in medical additive manufacturing applications is quite fascinating. As a ceramic 3D printing technology company that has built its success on its close collaborations with academics, I am not surprised to hear Lithoz genuinely talks about the pros and cons of using technical ceramics and most importantly, how the limitations could be addressed. Nonetheless, what I would like to keep in mind is the various ways this conversation has shed light on the ability of LCM to deliver patient-specific solutions.
Be it through the combination of LCM and dual-material implants in bone regeneration applications or through the use of LCM for dental implants and dental restorations, Lithoz has ticked the right boxes by addressing the most significant hurdles that were slowing down the use of technical ceramics in the healthcare field, thus opened up possibilities that led to a confident use of this technology. While advancements will surely continue to be made in the field, the next urgent step might be on the side of medical and healthcare professionals. A step that consists in extensively experiencing the capabilities of these processes in order to testify to their veracity.
This content has been created in collaboration with Lithoz.