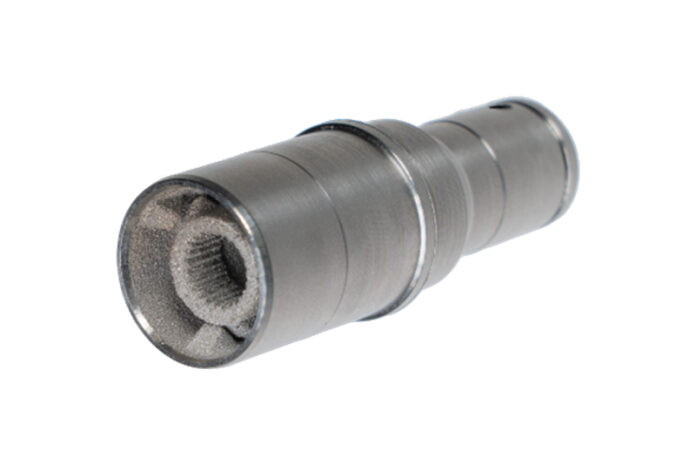
Liebherr-Aerospace, fournisseur de premier rang de pièces aérospatiales, a intégré un arbre flexible imprimé en 3D dans le système à grande levée de l’Airbus A350. L’unité a été approuvée par Airbus ainsi que par l’Agence européenne de la sécurité aérienne EASA pour la production en série.
(Pour ceux qui ne le savent pas, un arbre flexible permet de transmettre un mouvement de rotation entre deux éléments non alignés ou ayant des positions variables.)
Fabriqué à partir de poudre de titane à l’aide de la technologie ALM (Additive Layer Manufacturing), l’arbre flexible présente un degré de complexité accru au niveau de la conception et a pourtant réussi à s’imposer dans le secteur de l’aviation.
En effet, Liebherr a pu remplacer l’assemblage de sept pièces, auparavant fabriquées de manière conventionnelle, par un seul composant imprimé en 3D. La réduction du nombre de pièces permet d’améliorer la fiabilité et de réduire considérablement le poids. Par rapport aux pièces imprimées en 3D précédemment développées et fabriquées par Liebherr, l’arbre flexible est plus complexe et représente une nouvelle étape vers des applications dans des systèmes hautement intégrés.
L’arbre flexible fait partie du système d’hypersustentation de l’Airbus A350, où il sera intégré dans la boîte d’engrenage différentielle active du système de volets. L’arbre flexible transmet le mouvement rotatif à un capteur de position et compense ainsi les désalignements d’angle et d’axe entre la boîte de vitesses et le capteur.
Pour rappel, le fournisseur de solutions Liebherr-Aerospace peut d’ores et déjà se prévaloir d’un certain nombre de produits fabriqués par ALM. Début 2019, par exemple, Liebherr-Aerospace a commencé la production en série de pièces imprimées en 3D avec l’introduction d’un support de capteur de proximité imprimé pour le train d’atterrissage avant de l’A350. Ce support était la toute première pièce introduite du système Airbus qualifiée pour la fabrication additive par couche de titane.
N’oubliez pas que vous pouvez poster gratuitement les offres d’emploi de l’industrie de la FA sur 3D ADEPT Media ou rechercher un emploi via notre tableau d’offres d’emploi. N’hésitez pas à nous suivre sur nos réseaux sociaux et à vous inscrire à notre newsletter hebdomadaire : Facebook, Twitter, LinkedIn & Instagram !