The rail industry is often seen as more “traditional” than automotive and aerospace sectors when it comes to adopting new technologies in manufacturing. With the increasing need to facilitate production and maintenance work, companies gradually turn to additive manufacturing.
The choice for this technology comes with its array of challenges that transport companies need to address. These challenges vary from one country to another, and sometimes, from one company to another as they require a thorough understanding of the stakeholder’s roles: operators, maintenance companies and rolling stock providers.
“Across Germany, train operators handle the trains’ day-to-day operations and act as caretakers of public transportation. Maintenance companies ensure the availability and sometimes the attractiveness of the trains, while I would define rolling stock providers as suppliers of railroad vehicles and infrastructure to the owner – which could be the operators or a rental company. With reference to Siemens, we can fulfil each of these roles, so that we are able to support our customers with a complete portfolio, depending on the set-up and the demand”, states Michael Kuczmik, Head of Additive Manufacturing/Mobility Customer Services –Siemens Mobility.
“We operate in a similar way at Bombardier. Sometimes we are the sole rolling stock supplier, as well as being responsible for maintenance and the effective running of rail networks. It all depends on our customers’ business model”, completes André Bialoscek, Head of Vehicle Physical Integration, Hennigsdorf – Bombardier Transportation.
“In theUK, it is somewhat fragmented. We have the rolling stock providers who finance the trains and lease them to the train operators. The train operators run the daily train services and undertake basic maintenance. Then we have maintenance and overhaul companies who deliver the large vehicle refurbishment and overhaul works, and finally we have engineering support companies such as DB ESG who deliver technical services to the industry”, explains Martin Stevens, Mechanical Engineering Manager – Deutsche Bahn ESG. Bombardier Transportation, Deutsche Bahn ESG and Siemens Mobility are Europe-based transport companies that share together the willingness to use digital manufacturing technologies to move production forward in the rail industry. However, the use of these technologies comes with its challenges in terms of speed and costs. Kuczmik, Bialoscek and Stevens share key insights into how their company overcomes these challenges.
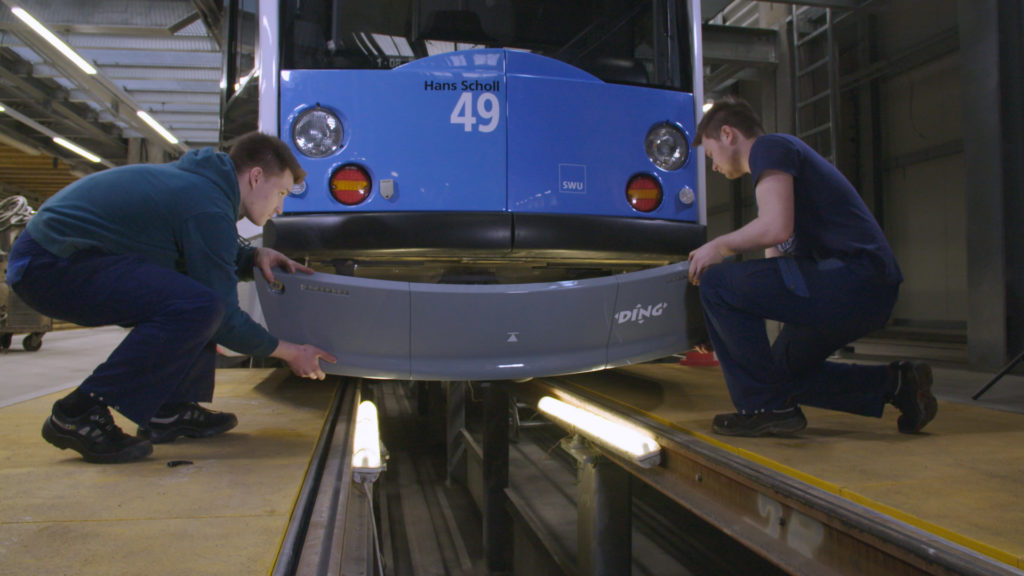
Reaching low production volumes while maintaining low costs
A single train can operate for more than three decades before it is removed from the market. Over time, this train might necessarily need maintenance and repair of spare parts. The only thing is that these spare parts cannot always be mass produced as all trains do not require the same spare parts, not to mention that manufacturers always develop different train designs, which brings further complexity at the production level.
In this regard, low production volumes are proving to be a viable solution to meet maintenance requirements and that’s where AM comes into play.
“We need to deliver trains significantly faster than three to five years ago. This increases the general pressure on all facets of our operations, including engineering, procurement, manufacturing and testing/homologation. We’re constantly having to quickly adapt to the ever-changing market, and this can often mean challenging ourselves as a company to stay ahead of the curve. This is where additive manufacturing comes in”, explains Bialoscek. A few applications of AM in the rail industry includes air vents, front casing parts (streetcars) or even interior grab handles.
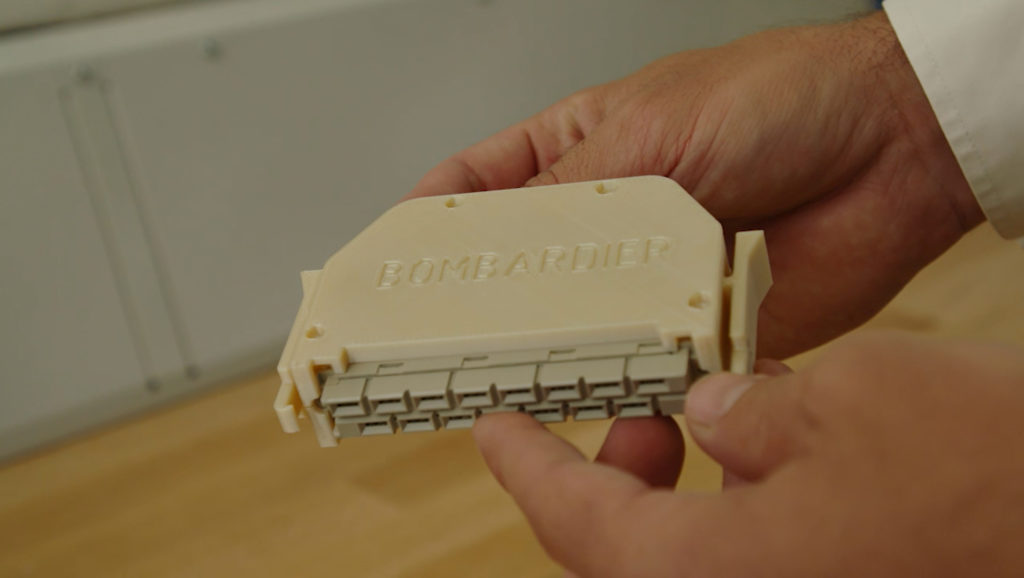
“If five air vents were required for one small fleet of trains, this can only really be achieved with additive manufacturing. Although the individual unit cost will be higher, you can just buy 5 and receive in a couple of weeks, rather than buying 10,000 and getting them in 3 months. The huge positives far outweigh the minor negatives. In fact, we recently teamed up with Angel Trains, one of the big three UK rolling stock providers, and train operator Chiltern Railways, to deploy and successfully trial the first 3D printed parts on UK passenger trains”, Stevens points out.
Speaking of the manufacturing process of interior grab handles for instance, DB ESG leverages Stratasys’ fire, toxicity and smoke compliant ULTEM™ 9085 resin material. The material is even more important as it integrates properties that facilitate the certification of spare parts in compliance with all standards, laws and regulations governing the rail industry.
“Typical certificates contain material properties like fire resistance and elongation at break, as well as part specific strength calculations. As the parts could be safety relevant, an update of the risk analysis for the whole system is often necessary. As such, we are also using ULTEM™ 9085 fire safety compliant material”, completes Kuczmik.
The Head of Additive Manufacturing/Mobility Customer Services –Siemens Mobility is going one step further. Indeed, these transport companies can now address the replacement of spare parts but to maintain low production costs, it is crucial to manufacture these parts only when they are needed, hence the need of a digital inventory. Reality is with digital warehouse, manufacturers can have instant access to design files, facilitating more agile, just-in-time production.
“It’s our belief that switching to virtual stock is essential moving forward – at least for corrective spare parts, where we do not know exactly if, when and how often they will be needed. Siemens Mobility already offers this via our Easy Sparovation concept. This comprises several possible options – standard ordering within the typical delivery times due to conventional production constraints, delivery within twenty-four hours in Europe from our stock, and printing on demand. The maintenance company or operator can decide based on how urgent the requirement is”, notifies the spokesperson of Siemens Mobility.
Moving forward, transport companies will develop new applications in the rail industry and print bigger parts. As local production becomes more and more essential, operators would need to ensure a more solid connection between a digital inventory, AM systems and a 3D printing software, especially MES (manufacturing execution system) software.
Remember, you can post free of charge job opportunities in the AM Industry on 3D ADEPT Media or look for a job via our job board. Make sure to follow us on our social networks and subscribe to our weekly newsletter : Facebook, Twitter, LinkedIn & Instagram ! If you want to be featured in the next issue of our digital magazine or if you hear a story that needs to be heard, make sure to send it to contact@3dadept.com