Since it had discovered 3D printing can provide a cost-effective approach to making inch-wide pucks used to fill holes in the splitters on the cars, NASCAR Cup Series Team Leavine Family Racing has become a real proponent of additive manufacturing technologies.
At the time, by printing the pucks in-house using a low-cost 3D printer printing with PLA material, the team succeeded to save $20,000-$25,000 a year.
As every user that realizes the savings in terms of cost and time, the team became addicted and started to look for more applications – and obviously for a more advanced technology. That’s where MakerBot comes into play.
“We selected the MakerBot METHOD X for its advanced capabilities. The METHOD X was one of the most advanced products on the market to create better, faster, and lighter parts through prototyping or some of the advanced materials that MakerBot offers,” said Michael Leavine, vice president of Leavine Family Racing. “METHOD is one of the most sophisticated units on the market, from the ease of connectivity––we can run all three of our printers from our laptop––to the advanced materials we were able to use––from ABS to nylon carbon fiber––to the heated build chamber that ensures print accuracy and repeatability every time.”
Let’s remind that, today using a MakerBot METHOD X 3D printer, it’s getting access to a wide range of materials including advanced thermoplastics, as well as unlimited collaboration from anywhere with new CloudPrint™ Software, not to mention the possibility to achieve rapid prototyping and end-use parts.
With three MakerBot METHOD X 3D printers, two for the garage and one that could be set up in Leavine’s office or taken on the road for use on-site at races, the team started to explore applications such as prototyping fitment and fabricating fixtures.
From the fabrication of dummy camera pods to the air intake duct inside the car, 3D printing seemed to be a magic solution for “doing things better, faster, cheaper, and more efficiently”.
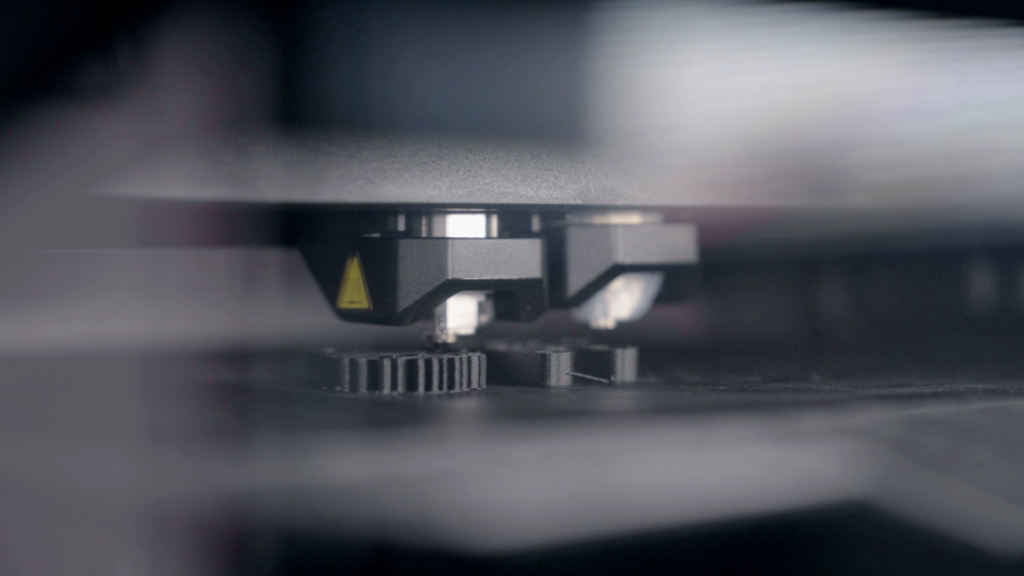
From a technical perspective, to manufacture the air intake duct for instance, a driver cooling system that brings fresh air into the vehicle, the team used MakerBot Nylon Carbon Fiber. The recently unveiled composite material integrates a nylon 12 base polymer and absorbs less moisture than nylon 6/66, therefore, retains more of its performance in the presence of moisture.
Due to its high strength and heat performance capabilities, it’s often considered as a good candidate to print some metal replacement parts.
“We stress tested parts 200% beyond what they were going to see at the racetrack to see what was going to fail and when it was going to fail before it ever goes onto the track. Our process is more quality control and stress testing before it goes on a race car in a performance capability. If it’s a critical part and it fails, it can be the difference between winning and coming in last place. The need to be able to quality control and stress test parts and iterate rapidly is important”, Leavine outlines.
Leavine Family Racing raced the No. 95 Toyota Camry in the NASCAR Cup Series from 2011 to 2020. The team completed the 2020 NASCAR Cup Series season with a top 20 finish, with Rookie of the Year contender Christopher Bell behind the wheel.
With MakerBot as a technological partner, Leavine Family Racing seems to be in good hands to optimize driver performance during races.
Remember, you can post free of charge job opportunities in the AM Industry on 3D ADEPT Media or look for a job via our job board. Make sure to follow us on our social networks and subscribe to our weekly newsletter : Facebook, Twitter, LinkedIn & Instagram ! If you want to be featured in the next issue of our digital magazine or if you hear a story that needs to be heard, make sure to send it to contact@3dadept.com