It all started in 2017 when space technology company Launcher has trusted AMCM, an EOS Group company, for the production of a 3D printed Launcher E-2 engine which was used on the first stage of its orbital launch vehicle. To achieve this goal, the manufacturer of customized additive manufacturing machines had developed the AMCM M 4K, an industrial 3D printer that features a part construction volume of 45x45x100 cm and that processes copper alloy, one of the most complex materials for liquid rocket engine combustion chamber production.
Launcher was certainly satisfied with the results of this collaboration as both companies announce today that Launcher has acquired the M 4K AM system to advance its high performance orbital launch vehicle strategy.
The space company’s ultimate goal is to 3D print the entire 10 ton-force E-2 rocket engine to deliver small satellites to low Earth orbit and according to Max Haot, Founder and CEO of Launcher, “AMCM’s flexibility and openness to customer requirements, both in machine building and process implementation, is remarkable.”
From a technological standpoint, reality shows that space engineers use to design smaller engines or produce multi-part combustion chambers to cope with the limited construction volume constraints of “conventional industrial” 3D printers.
To overcome this challenge and build a high performant liquid rocket engine, Launcher had decided to 3D print its E-2 engine combustion chamber as a single part, to ensure optimal cooling channel design, fewer parts, simpler processes, and lower overall production costs. Furthermore, unlike companies that rely on Inconel alloy as their combustion chamber material, Launcher had decided to bet on copper alloy, which is according to AMCM, “the best material for liquid rocket engine combustion chambers due to its optimal thermal conductivity properties, and to the fact that it enables more effective regenerative cooling.
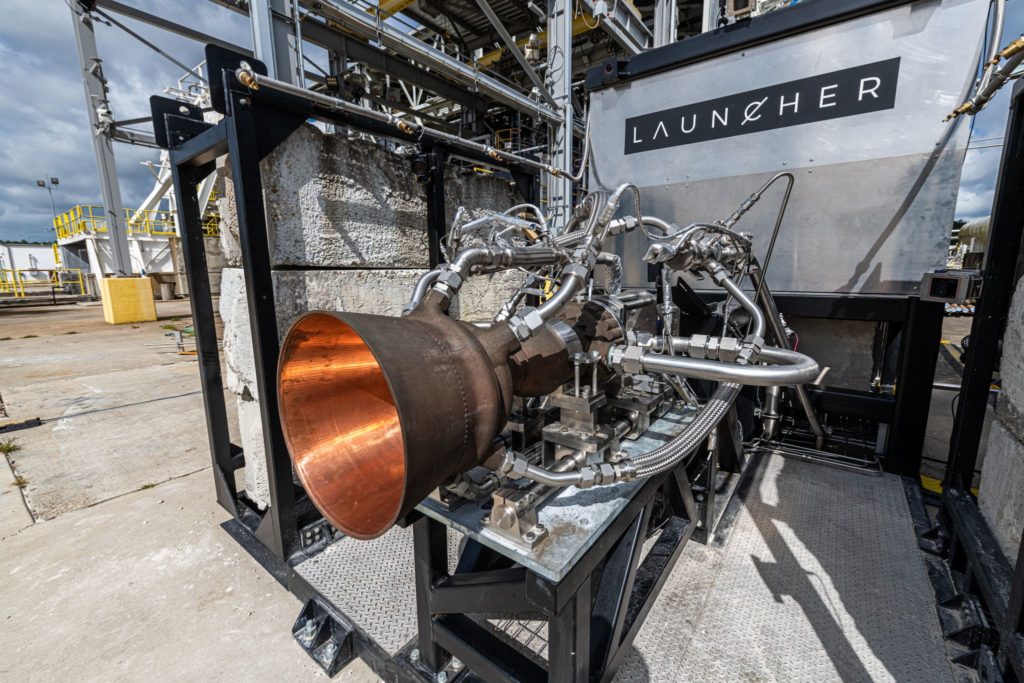
“The major advantages of metal AM in the production of liquid rocket engines is lower cost to manufacture and allow for complexity in design – a common barrier-of-entry with conventional manufacturing technologies. Furthermore the development times are dramatically lessened and design flexibility is expanded. The result of these benefits is improved propulsion systems that use less propellant, carry larger payloads, and enable new ideas and applications to take flight. Additive manufacturing is revolutionizing the space industry and innovative companies like Launcher are taking advantage of this advanced 3D printing technology”, Martin Bullemer, Managing Director of AMCM states.
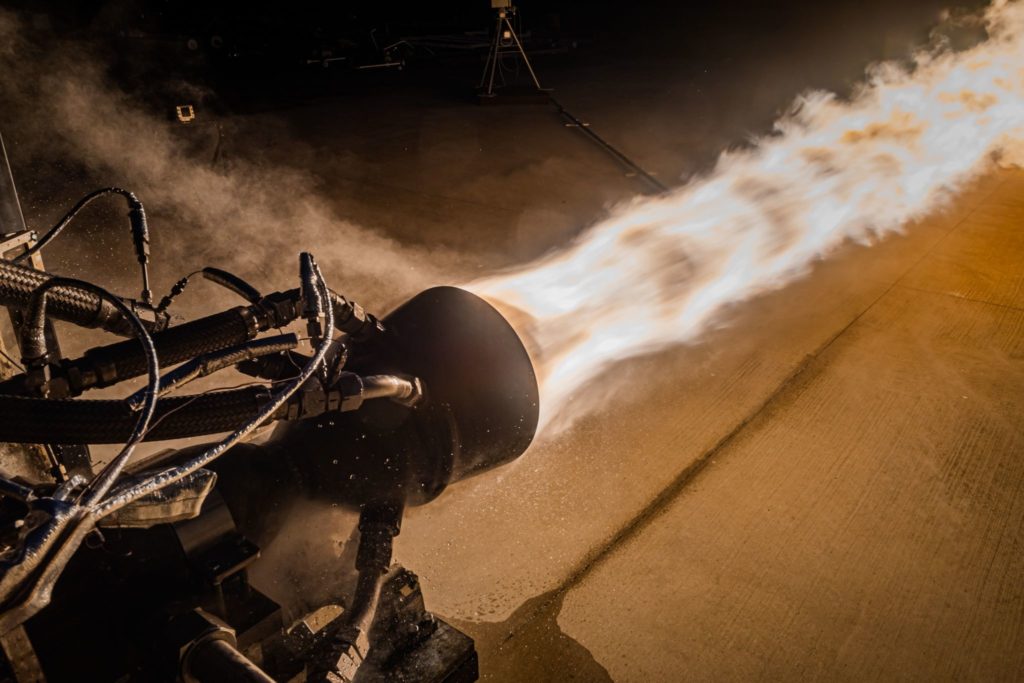
While we can’t wait to see new Launcher’ space applications enabled by AM, we can’t help but think that, AMCM’s recently announced contract with Orbex can make it a 3D printer manufacturer of choice for space applications.
Remember, you can post job opportunities in the AM Industry on 3D ADEPT Media free of charge or look for a job via our job board. Make sure to follow us on our social networks and subscribe to our weekly newsletter : Facebook, Twitter, LinkedIn & Instagram ! If you want to be featured in the next issue of our digital magazine or if you hear a story that needs to be heard, make sure to send it to contact@3dadept.com