As part of a research project, ITAMCO (Indiana Technology and Manufacturing Companies), has additively manufactured parts made with EOS 17-4 PH IndustryLine metal powder that exceeded 17-4 PH Stainless Steel in tensile strength.
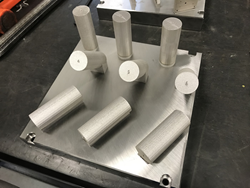
The project aimed to explore the properties of the 3D printed parts for Direct Metal Laser Sintering (DMLS).
The different stages of the project
The build of nine cylinders was prepared with Sunata™ software by Atlas 3D. The software chose the best orientation for the parts and generated the necessary support structures for the build on ITAMCO’s EOSM 290 3D printer.
Three cylinders were therefore built horizontally, three at 45˚ to the horizontal, and three were built vertically. After the build, the cylinders were cut from the build plate and sent for heat treatment.
First, the cylinders were heated to 1040˚ Celsius and kept at that temperature for 0.5 hour. The cylinders were then quenched by argon. After that, the cylinders were reheated to 480˚ Celsius and kept at the temperature for one hour. The cylinders were quenched again by argon. The hardness was between 40 and 47 HRC and the estimated tensile strength was 190 KSI after heat treatment.
After this stage, SGS MSi, a metallurgical testing laboratory, received the cylinders. The tensile strength (PSI) numbers: average tensile strength (PSI) of the nine cylinders was 192,000. The average tensile strength (PSI) of six heat-treated stainless steels (H900, H1025, H1075, H1150, H1150-M, H1150-D) is 144,000. Therefore, the tensile strength of the nine cylinders outperforms the tensile strength of raw material 17-4 PH that had been heat treated.
“We conducted the research so we could compare the wrought properties of metal to parts made through additive manufacturing with the new EOS 17-4 PH Stainless Steel metal powder. It is quite amazing to us that we achieved the wrought properties of metal,” said Joel Neidig, Business Development and Technology Manager with ITAMCO.
For further information about 3D Printing, follow us on our social networks and subscribe to our newsletter!
//pagead2.googlesyndication.com/pagead/js/adsbygoogle.js
(adsbygoogle = window.adsbygoogle || []).push({});