Interview exclusive sur une collaboration tripartite entre MSC Software, Markforged et Danfoss qui mène à la livraison d’outils d’optimisation des performances pour les utilisateurs de Markforged.
Bien que personne ne puisse dire avec certitude ce qui se passera dans un avenir (proche ou lointain), les experts en technologie fournissent des certitudes quant à l’avenir de la fabrication – en particulier la fabrication additive (FA). La fabrication additive existe depuis des décennies. Cependant, au cours des cinq dernières années, nous avons vu une vague de fabricants se tourner vers la technologie de FA au même moment que des imprimantes de qualité industrielle abordables faisaient leur entrée sur le marché.
Les imprimantes 3D industrielles peuvent imprimer des pièces complexes avec des matériaux et des procédés reproductibles, cohérents et fournissant des résultats de haute qualité qui reflètent l’intention de l’ingénieur qui les a conçues. Cependant, tout comme les procédés de fabrication ont été affinés et perfectionnés, le savoir-faire et l’expérience sont essentiels pour s’assurer qu’une pièce fonctionne comme il se doit lorsqu’elle est imprimée en 3D.
Cette situation est exacerbée si les fabricants n’ont qu’une connaissance limitée des matériaux en cause. Lorsque le résultat souhaité n’est pas atteint, c’est non seulement frustrant, mais ce qui l’est encore plus, c’est de ne pas en connaître les véritables raisons. De nombreux facteurs peuvent affecter le comportement d’une pièce en production, tels qu’une incompatibilité entre les propriétés du matériau et la technologie de fabrication additive, ou si une topologie de pièce complexe n’est pas bien optimisée pour le processus d’impression utilisé. La différence réside dans le fait que les nouveaux processus de FA sont guidés par les données et que les matériaux peuvent également être codés numériquement, ce qui permet de modéliser et de simuler un dessin avec précision avant qu’une seule pièce ne soit imprimée.
Danfoss, un leader mondial de l’industrie qui fournit des solutions hydrauliques et électroniques pour les équipements mobiles, a été l’un des premiers à adopter cette nouvelle technologie, et ils ont rapidement constaté que même les meilleures conceptions exigeaient des itérations de ces défis. L’un des objectifs de l’entreprise était de tester que les pièces étaient prêtes à être ajoutées à la chaîne de fabrication. L’entreprise a donc entrepris de réduire le nombre d’essais de construction par pièce et de définir un outil d’analyse par éléments finis (FEA – Finite Element Analysis) qui pourrait déboucher sur une approche de « bonne première fois » en utilisant la FA.
La société danoise a donc décidé de s’appuyer sur l’expertise de ses deux partenaires, Markforged & MSC Software, pour relever ces défis.
Nous nous sommes entretenus avec Craig KLOCKE, Tripp BURD & Olivier LIETAER, représentants respectifs de Danfoss, Markforged et MSC Software pour discuter de ces défis et de la solution unique qui sera disponible pour un public plus large dans le futur.
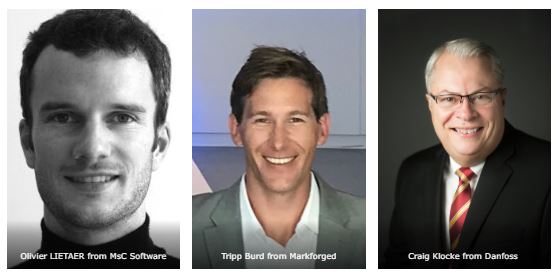
Comment Danfoss a-t-il initié le partenariat entre Markforged et MSC Software ?
Le groupe Danfoss est solidement implanté dans l’industrie de la fabrication additive. L’entreprise est connue pour sa gamme complète de produits et de services dans le domaine du refroidissement des aliments, de la climatisation, du chauffage des bâtiments, des entraînements à fréquence variable, des compresseurs à gaz et de l’alimentation des machines mobiles – en d’autres termes, un large éventail d’industries où ils peuvent explorer diverses applications de la FA.
Il y a trois décennies, l’entreprise a commencé à utiliser la fabrication additive. Le Groupe danois a exploré plusieurs types de technologies telles que les imprimantes SLA, FDM, MJF et composites. Il a aussi signé de nombreux partenariats avec des sous-traitants notamment Fast Radius pour accélérer l’adoption de la FA.
De plus, 2017 a été une année décisive pour le fabricant industriel qui a fait un pas de géant dans sa transformation numérique avec l’ouverture du premier des trois centres d’impression 3D mondiaux à Nordborg, au Danemark, puis en Amérique du Nord et en Asie.
A ce jour, le Groupe a enregistré plus de 15 000 pièces imprimées en 3D fabriquées dans le monde. Cependant, malgré le succès actuel – quoique discret – de sa transformation numérique, Danfoss se heurte toujours à des difficultés dans son cheminement vers l’optimisation de l’efficacité de la production.
Optimisation de l’efficacité de la production grâce à la FA métallique et aux outils logiciels appropriés
Tout comme plusieurs fabricants industriels, la multinationale s’est appuyée sur la FA métallique pour accélérer sa transformation numérique. En effet, la FA métallique reste un facteur clé influençant la demande du marché, et l’équipe de Craig Klocke en est parfaitement consciente. Le responsable de la conception et de la fabrication additive a déclaré :
« Tout le monde connaît les avantages de la FA : sa flexibilité, sa valeur ajoutée pour les clients. Le métal est nécessaire dans certaines applications en raison de ses propriétés générales et de sa capacité à répondre aux exigences en termes de résistance et de rigidité, bien que les polymères et les composites aient des capacités incroyables.
De plus, une autre raison pour laquelle nous avons besoin d’imprimantes 3D métal est que nos matériaux actuels sont des métaux. De plus, c’est assez ironique, mais nous avons besoin d’avoir toutes les capacités d’impression 3D métal pour sécuriser la majorité de nos demandes. En effet, nos clients croient que nous en avons besoin, alors nous nous assurons de l’avoir ; autrement, ils ne voudraient pas faire affaire avec nous. En réalité, seul un petit pourcentage de nos demandes résulte en des applications d’impression 3D métal, mais cela augmente avec le temps ! »
L’exploitation des capacités d’impression 3D métallique peut rapidement devenir coûteuse si l’utilisateur ne dispose pas d’outils appropriés, sans parler du temps investi dans les processus de production et les tests, mais l’équipe a été impressionnée par la technologie abordable de Markforged. Danfoss utilise des imprimantes 3D métalliques et composites de Markforged dans ses locaux. L’équipe a découvert que les pièces composites de Markforged étaient aussi solides que l’aluminium lorsqu’elles étaient renforcées avec de la fibre de carbone, mais ils n’avaient aucune expérience en polymère et en pièces composites lorsqu’ils ont commencé. Le responsable de la conception et de la fabrication additive a déclaré : « Sans cette expérience, les cycles d’essais et d’erreurs sont beaucoup plus longs et plus difficiles. Comme nous sommes déjà client de Markforged et MSC Software, il a été facile de connecter nos trois sociétés pour discuter de cette question. Le défi était encore plus grand pour Markforged et MSC Software qui avaient besoin de développer une solution qui améliorerait notre capacité de prédiction, mais aussi d’intégrer le chemin de fibre détaillé de l’imprimante dans le logiciel », poursuit Klocke.
Le partenariat entre Markforged et MSC Software
Markforged est l’un de ces fabricants qui croit fermement qu’une solution robuste de fabrication additive pourrait faire une différence majeure dans la course contre la transformation numérique. Reconnu pour ses imprimantes 3D métal et à fibre de carbone, le fabricant a levé cette année un montant important de nouveaux capitaux (82 millions de dollars dans le cadre d’une ronde de financement de série D, pour un total de 137 millions de dollars depuis 2013) pour mener les innovations.
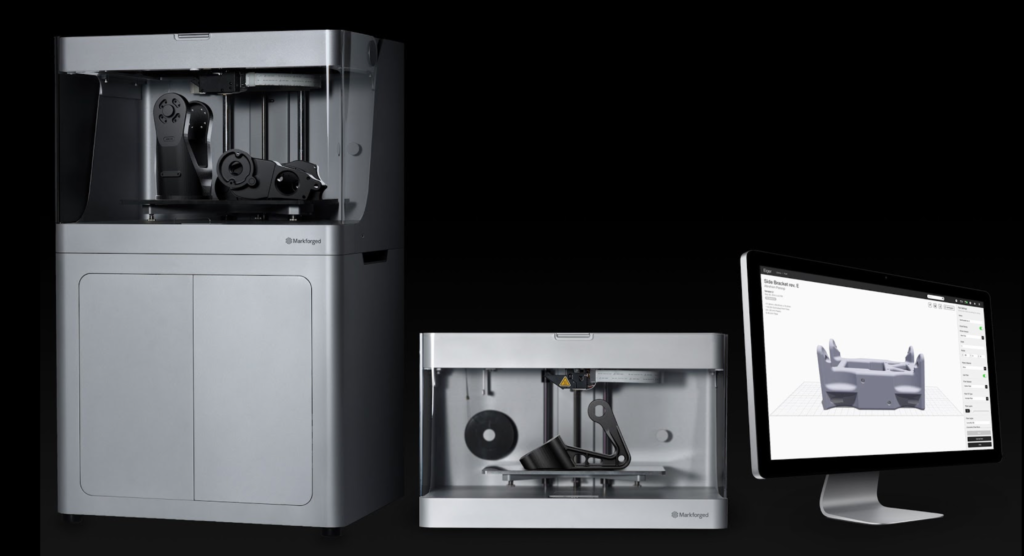
MSC Software, en revanche, fait partie d’une grande famille, dont le fonctionnement est crucial à comprendre pour pouvoir en tirer le meilleur parti. L’entreprise développe une technologie logicielle de simulation qui permet aux ingénieurs d’améliorer la qualité, de gagner du temps et de réduire les coûts associés à la conception et aux essais des produits fabriqués. Simufact Engineering simule les processus de fabrication des métaux, tandis qu’e-Xstream Engineering fournit la plate-forme de modélisation des matériaux composites et avancés appelée DIGIMAT. Toutes les sociétés font partie d’Hexagon, un fournisseur mondial de capteurs et de technologies de l’information dans de nombreuses industries (aéronautique, automobile, santé et bien d’autres).
Pour répondre aux besoins de Danfoss, Markforged et MSC Software ont décidé de travailler ensemble sur la validation et l’optimisation des designs avant de les imprimer sur des imprimantes 3D Markforged.
Tout ceci semble très simple à dire, mais il s’agit d’un long processus qui exige une compréhension complète du processus d’impression et l’intégration dans un flux de travail de simulation numérique tel qu’une solution de FA d’Hexagon.
Développer une solution de fabrication additive
Images via Danfoss
Le développement de Digimat pour la fabrication additive a commencé il y a quelques années. Au fur et à mesure de l’expansion de la technologie et du marché, l’entreprise a développé une solution dédiée à la FA. « Il y a cinq ans, nous avons commencé à discuter avec des clients clés pour Digimat Additive Manufacturing. Ils voulaient bénéficier de la même chaîne numérique que celle que nous proposons pour le moulage par injection, mais en l’occurrence dédiée à la FA », explique Olivier Lietaer, Business Development Engineer chez e-Xstream Engineering.
MaterialCenter est donc une plate-forme de gestion du cycle de vie des matériaux développée par e-Xstream Engineering, connue pour son produit Digimat, qui vise à suivre, collecter et stocker toutes les données relatives aux matériaux.
« Conçue pour la FA, MaterialCenter permet aux fabricants d’améliorer la qualité d’impression et d’assurer la traçabilité en capturant toutes les données de FA. Ces données peuvent être liées au matériau (le numéro de lot), à la machine (le type d’imprimante 3D utilisée pour la production, son numéro de série), aux réglages du process, au nombre de pièces dans la construction ou dans le test », poursuit l’Ingénieur en Business Development.
En d’autres termes, ce système centralisé de gestion des données permettrait à tout utilisateur de trouver en quelques minutes des données pertinentes, entièrement connectées et traçables dans toute l’entreprise.
« Si l’utilisateur veut comparer différentes constructions, ou s’il y a un problème avec la production d’une pièce donnée, il peut facilement retourner aux données de fabrication de la pièce et découvrir la cause du problème », a déclaré Lietaer.
Avec l’acquisition récente d’AMendate, une société allemande spécialisée dans l’optimisation topologique, MSC Software est maintenant en mesure de fournir une solution logicielle de conception générative holistique appelée Apex Generative Design qui automatise la conception de dessins imprimables en 3D. De plus, avec l’appui de sa société mère Hexagon, MSC Software est de plus en plus en mesure de fournir aux fabricants industriels des solutions de bout en bout qui intègrent des scanners et des logiciels de métrologie pour boucler la boucle du processus de conception par l’inspection de la pièce produite et sa finition.
« Avec l’acquisition récente d’AMendate, nous sommes maintenant en mesure de proposer des capacités d’optimisation topologique. Quelle que soit la technologie utilisée pour créer la pièce (métal, polymère ou composite), nous sommes bien placés pour aider l’ingénieur à faire les bons choix grâce à l’utilisation du système de gestion des données, la simulation de processus avec Digimat ou Simufact et la performance des pièces telles qu’imprimées. La raison pour laquelle nous avons différentes solutions est plus historique : nous venons du monde de l’ingénierie des matériaux et Simufact vient du monde de la fabrication métallique. Il est logique que chacune de ces entreprises développe des solutions dédiées. De plus, nous devons absolument voir les choses à un niveau plus élevé : que l’utilisateur utilise Digimat ou Simufact, ils font partie de notre solution de bout en bout, le plus important est que nous aidons les ingénieurs à produire leurs pièces avec plus d’efficacité, en réduisant leur coût et la quantité de matériaux habituellement utilisés », déclare le porte-parole d’e-Xstream Engineering.
Le potentiel de la simulation numérique : l’ingénierie des matériaux, la simulation des procédés et la performance des pièces
Images Digimat
Pour aider Danfoss à prévoir ce qui se passera pendant le processus de production avec les imprimantes 3D de Markforged, MSC Software et Markforged travaillent actuellement sur trois étapes importantes : l’ingénierie des matériaux, la simulation des procédés et la performance des pièces.
La simulation de processus a également été une question clé soulevée par Danfoss. Leur équipe d’ingénieurs voudrait savoir comment la pièce sera imprimée exactement – s’il y a un risque de décollement par exemple – et tout autre problème qui pourrait empêcher un échec de fabrication. En ce qui concerne la performance des pièces, les ingénieurs de Danfoss doivent savoir comment optimiser la performance des pièces pour une quantité donnée de matériau. Les matériaux Onyx et fibre de carbone continue sont les deux matériaux dont les données ont été analysées dans le cadre de ce partenariat.
La stratégie de MSC Software est donc de s’appuyer sur une technologie de jumeau numérique (Digital Twin) pour collecter et analyser des données produits réelles en cours d’exploitation. Selon les mots de Lietaer, ils développent la « Digital Twin (DT) de matériaux en créant des modèles de matériaux qui peuvent être utilisés pour la simulation ». Il est également possible de créer un DT de l’imprimante. « Avec ce jumeau numérique, [il sera possible pour Danfoss] d’étudier et de comprendre virtuellement le processus, de définir quel est le meilleur flux de travail, quel est l’impact de tout changement dans le processus de conception, avant d’évaluer et tester physiquement la pièce. »
Markforged et MSC Software ne travaillent ensemble que depuis quelques mois. « Nous avons déjà fait des efforts et des progrès considérables en termes d’étapes à franchir pour obtenir les bons outils de simulation numérique. Nous avons commencé par tester mécaniquement les matériaux, l’Onyx et la fibre de carbone continue. La période de test comprend différentes configurations, en ce qui concerne l’orientation du parcours d’outils », explique e-Xstream, bien qu’ils n’aient pas pu en dire plus sur les détails du test.
Cependant, la société a affirmé que les modèles de matériaux ont été intégrés dans la nouvelle version de Digimat sortie le 24 octobre 2019 (la première étape), permettant ainsi aux utilisateurs avancés de bénéficier de la technologie.
« Nous travaillons actuellement sur une interface qui permet aux utilisateurs d’échanger des données de parcours entre le logiciel Markforged et Digimat. La prise en compte du comportement des matériaux et des données de parcours sont les deux éléments clés pour prédire les performances structurelles des pièces et valider que la pièce composite peut remplacer le métal. Enfin, les imprimantes et les processus Markforged seront intégrés dans nos outils standard de validation FEA qui sont faciles et efficaces à utiliser pour tous », poursuit Lietaer.
Réflexions finales
Bien que la simulation numérique MSC évoquée présente des avantages lorsqu’il s’agit de déterminer le poids idéal ou de définir la meilleure disposition des pièces pour réduire le temps d’impression et l’utilisation du matériau, elle ne sera pas une exigence pour les clients actuels ou futurs de Markforged.
« Le partenariat avec MSC Software est très excitant », a déclaré Tripp Burd – Directeur, Ingénierie d’application stratégique chez Markforged, qui est heureux qu’une demande de leur client commun leur ait permis de travailler ensemble. « Le partenariat avec des technologies comme Digimat permet à nos clients de mieux comprendre et d’accroître leur confiance dans la performance des pièces imprimées. La FA est une toute nouvelle technologie, et il y a encore beaucoup à apprendre dans ce domaine. L’application de la simulation logicielle pour la production de composants est un excellent ajout à notre technologie qui fournit des pièces qu’il n’était pas possible de livrer avec d’autres technologies. »
« Les matériaux de Markforged sont avancés et assez difficiles à modéliser. Il y aura donc un effort continu pour améliorer la précision de la solution. Avec le temps, nous serons en mesure d’atteindre le même niveau de précision que pour les autres techniques traditionnelles. Notre objectif est d’accélérer l’adoption de la FA en aidant les ingénieurs à faire les bons choix de conception et à augmenter l’ouverture des applications de FA. Nous sommes convaincus que la simulation numérique, et de tels partenariats sont essentiels pour y parvenir », conclut Olivier Lietaer.
« Ma vision et mon espoir sont que la FEA, la FA et les composites deviennent des activités automatiques comme c’est le cas aujourd’hui pour la fabrication traditionnelle. Avec l’analyse par éléments finis traditionnelle, nous avons éliminé le cycle d’essai, construisons les cycles en utilisant l’analyse numérique. Et je suis persuadé que nous y parviendrons très rapidement avec la FA également. Cela signifie que, dans le cadre de notre développement, nous réduisons les coûts et les risques. C’est vert et efficace. Je suis très heureux que Markforged et MSC Software aient conclu un partenariat et que nous ayons pu l’initier. Je suis très enthousiaste à l’idée de poursuivre le partenariat que nous entretenons avec les deux entreprises. Je ne peux pas prédire où nous en serons dans cinq ans pour l’instant, mais je sais que ce sera un endroit meilleur et plus excitant que celui où nous sommes aujourd’hui », a conclu Klocke.0
Cet interview a d’abord été publié dans le numéro de novembre 2019 de 3D ADEPT Mag.