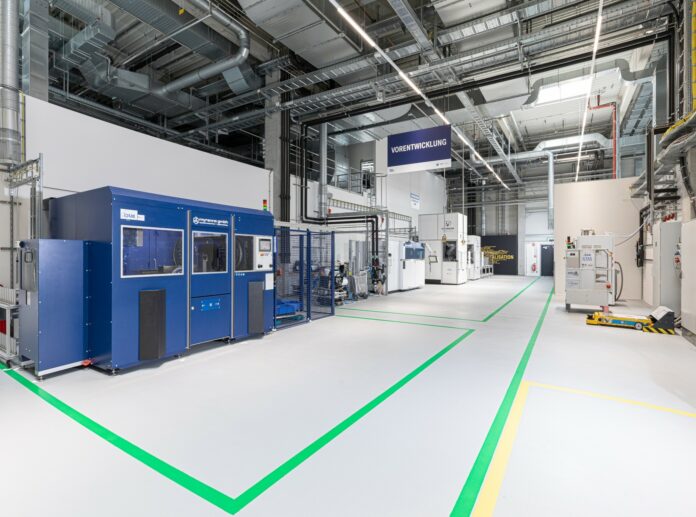
Three years ago, on March 27th, 2019, twelve project partners officially launched IDAM, a project funded by the German Federal Ministry of Education and Research (BMBF) and led by the BMW Group, that aims to promote the “Industrialization and Digitization of Additive Manufacturing (AM) for Automotive Series Processes”.
With the goal of fostering the use of metal 3D printing in standard production of cars, the twelve partners explored several innovative concepts for automated generation of 3D printing construction data.
The year following the launch, GKN Powder Metallurgy shared a first feedback of the project where we learned that creating a digital architecture was one of the most challenging phases.
Their efforts are paying off as the consortium has recently successfully implemented a digitally connected, fully automated 3D printing production line for automotive standard production. An additional line is located at the firm GKN Powder Metallurgy in Bonn.
The partners have first developed fully automated driverless transport systems (FTS) that can carry the 3D printers’ mobile build chambers between modules in the IDAM production lines. The machines are orchestrated by a central control unit that consolidates all production data from individual line modules to ensure maximum productivity and quality. During the preparation process, the processed metal powder is transported to workstations where the material can be prepared independently. Post-processing of the fabricated components takes place at specially designed stations that are also fully automated.
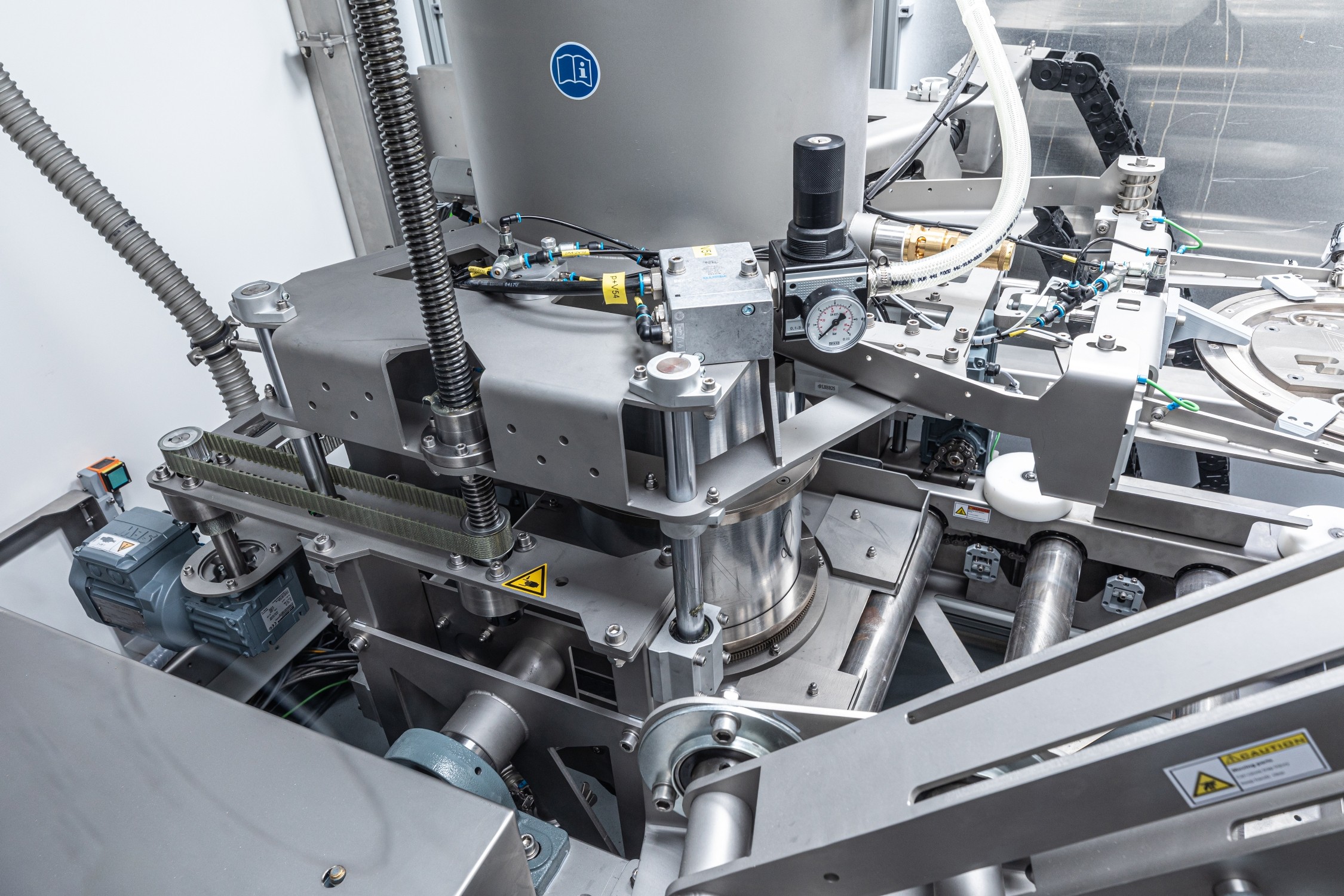
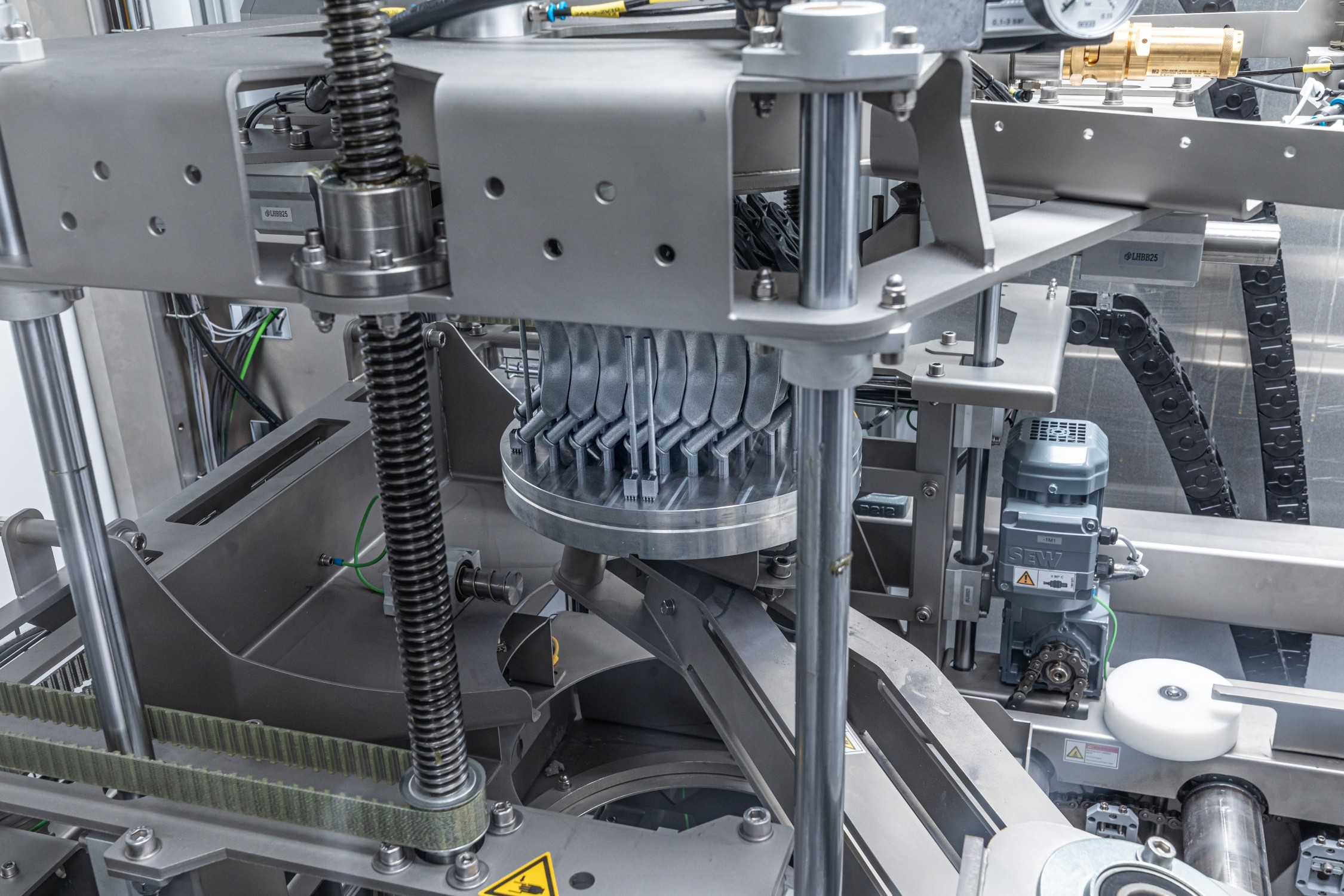
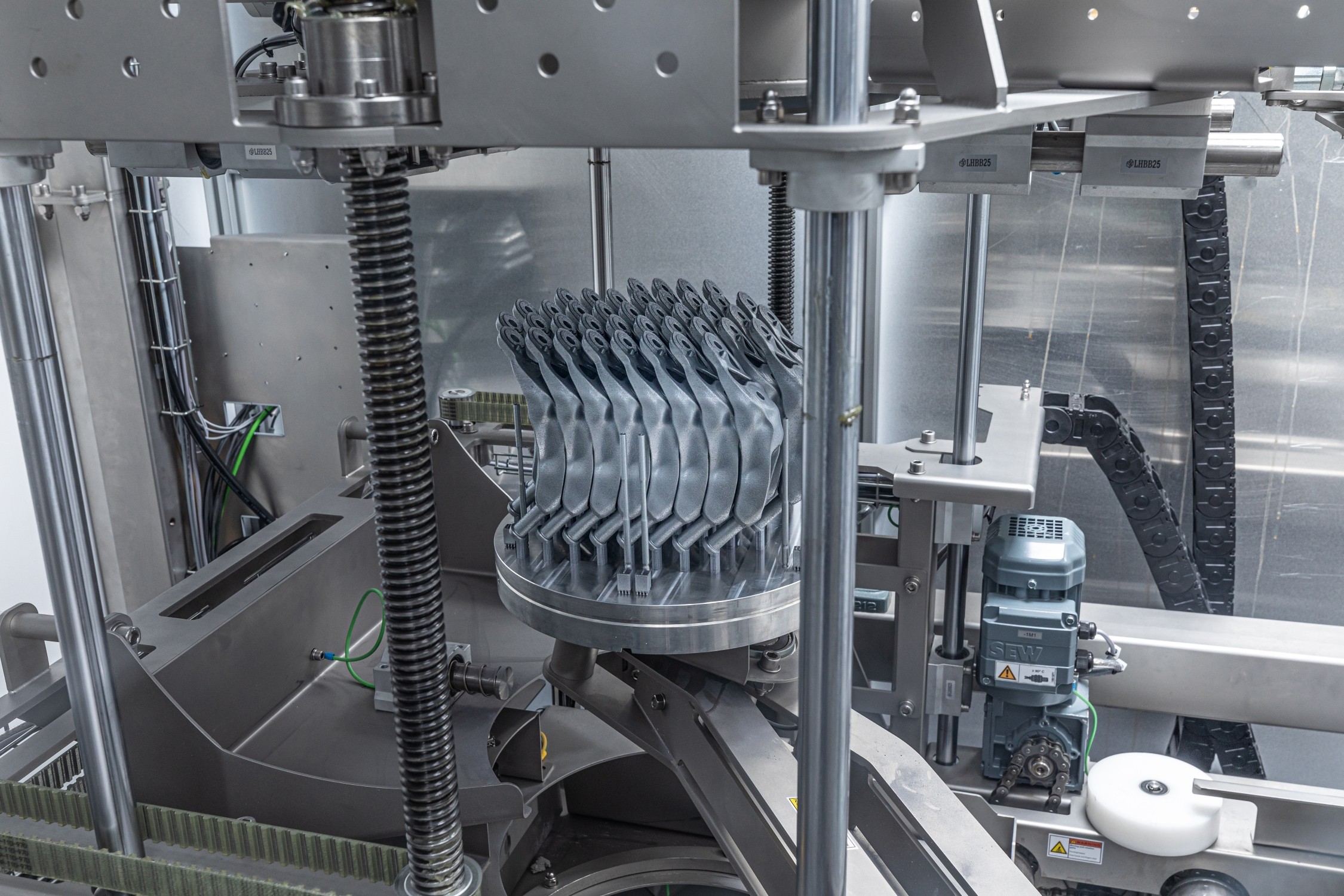
Quality assurance of the finished parts takes place in-line, during the laser melting process, using sensors. This includes checking emissions from the molten pool with a CMOS camera and pyrometer. AI algorithms are used to correlate the data collected with actual component quality. This means process deviations can already be identified during production and component quality evaluated, a press release reads.
Around 50,000 components per year can be manufactured cost-effectively in common part production, as well as more than 10,000 individual and new parts, by means of 3D printing using Laser Powder Bed Fusion (LPBF): The starting material, metal powder, is remelted with a laser, layer by layer, at the site where the solid component needs to be created at each level. Using this 3D printing process means certain tools are no longer required and new design possibilities can be realised – which greatly increases flexibility, the partners explains.
“From the very first day of the project, you could feel the team spirit among the partners. Learning from one another, developing innovative solutions together and making the best use of each partner's individual strengths – those were key to successful industrialisation and digitalisation of additive manufacturing,” according to Felix Haeckel, consortium leader and BMW Group project manager.
Remember, you can post job opportunities in the AM Industry on 3D ADEPT Media free of charge or look for a job via our job board. Make sure to follow us on our social networks and subscribe to our weekly newsletter : Facebook, Twitter, LinkedIn & Instagram ! If you want to be featured in the next issue of our digital magazine or if you hear a story that needs to be heard, make sure you send it to contact@3dadept.com