HP has added the Polypropylene (PP) material to its portfolio of additive manufacturing materials.
Developed in collaboration with BASF, the High Reusability PP is versatile, durable, and chemically resistant. It is suitable for applications in the automotive, consumer, industrial, and medical sectors where an optimal balance between performance and cost is desired. In addition to performance, the PP helps reduce wasteby enabling up to 100% reusability of surplus powder4
The new HP 3D High Reusability PP enabled by BASF provides customers with a genuine new additive manufacturing material offering the same properties as commonly used PPs in injection molding, which has proven to have nearly unlimited use. With its excellent chemical resistance, low moisture absorption, and long-term durability, PP is ideal for piping, fluid systems, and containers. For example, automakers will be able to use the same PP for prototyping and production of final parts found in vehicles’ interior, exterior, and under-the-hood.
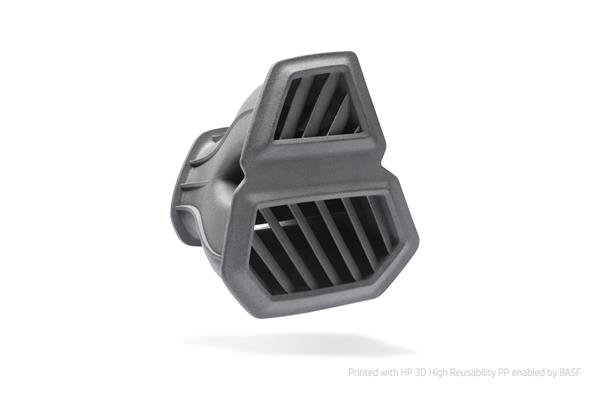
This is not the first collaboration between HP and BASF. Their latest collaboration led to the development of TPU material, which is used today across the world in HP partners’ facilities. Both partners have decided to extend their partnership to the development of new applications with market leading customers in the automotive, consumer, industrial and medical industries.
“The response to the COVID-19 crisis is a watershed moment for the industry. HP and its partners have 3D printed more than 2.3 million parts to bridge supply chain gaps, enable local production, and help healthcare professionals on the front lines,” said Ramon Pastor, Interim President of 3D Printing and Digital Manufacturing, HP Inc. “As we navigate this new landscape, we continue to execute on our strategy and push innovative new 3D printing materials, solutions, and partnerships forward to help our customers re-open manufacturing and deliver disruptive innovation for the world’s industries.”
Other partnerships and clients
In order to develop new PP applications, HP collaborates with new partners, parts suppliers and customers. In addition to GKN Powder Metallurgy/Forecast 3D, Henkel, the company is signing new partnerships with Extol, a specialist in plastic assembly technology, custom automation, and engineering services, Oechsler, a supplier of 3D printed parts, and Fast Radius, a service provider that is now joining its HP Digital Manufacturing Network.
Cobra Golf has decided to debut in the 3D printing industry with HP MJF. The company operates in the golf world. In order to elevate the game, Cobra is committed to advancing engineering first-of-its kind clubs and equipment.
“Cobra Golf strives to deliver high-performance products that help golfers of all levels play their best and enjoy the game,” said Jose Miraflor, Vice President of Marketing, Cobra Golf. “To do that, it’s critical to use the most effective manufacturing processes to design, develop, and achieve optimal results. To continue innovating and transforming the way equipment is manufactured, we are working with HP and Parmatech to take advantage of the benefits of Metal Jet. We are seeing immediate benefits including design freedom, rapid design iteration, and high quality parts that meet our economic demands.”
Remember, you can post free of charge job opportunities in the AM Industry on 3D ADEPT Media or look for a job via our job board. Make sure to follow us on our social networks and subscribe to our weekly newsletter : Facebook, Twitter, LinkedIn & Instagram ! If you want to be featured in the next issue of our digital magazine or if you hear a story that needs to be heard, make sure to send it to contact@3dadept.com