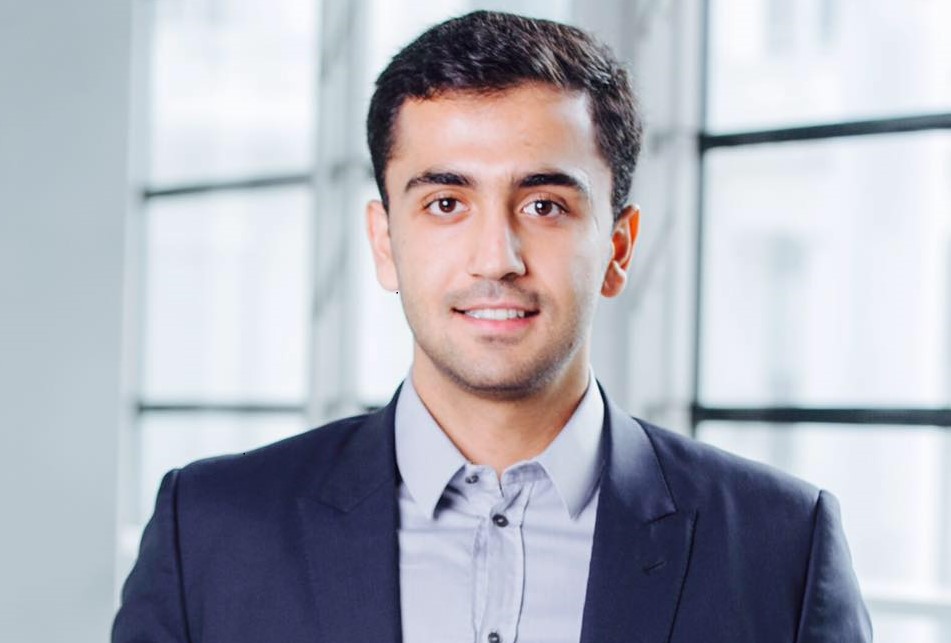
Aslan Shirazian
Providers of SaaS solutions play a vital role in the search of solutions to overcome hurdles faced by additive manufacturing companies. These hurdles often concern design, manufacturing & build validation, and leave many unanswered questions for designers, additive manufacturing (AM) companies, not to mention OEMs, consultants and other third-party companies.
GROW Software Ltd (aka GROW), a London-based company, has reviewed these questions, in order to provide a complete SaaS solution to these professionals. The company is much more than a DRM Security Company. It has showed the market it has a bigger vision than other companies of the same range by providing a solution that is based on three pillars, a solution that would enable companies to save cost and time, and above all, to consider a bright future for additive manufacturing processes.
In order to understand the how and the why of this solution, we have invited Aslan Shirazian, Business Development Manager of GROW in this #OpinionoftheWeek.
What are the challenges that GROW tries to overcome?
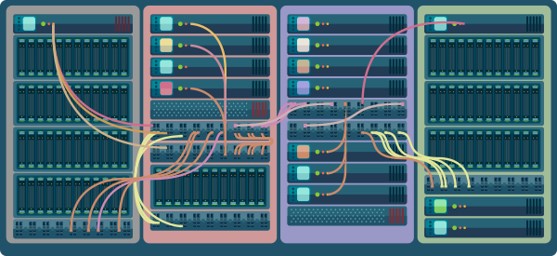
Today, 3 challenges remain and each of them raises several questions:
The first one is design which raises issues about the way one designs, about intellectual property (IP) and the choice of the right equipment: How do you design for AM? How do you protect the IP and know how over a design? How do you pick the right machine, materials, and settings for that specific design?
Manufacturing is considered as one of the most important challenges since it requires manufacturers to know the causes of failures that might occur, to determine how they can control their digital rights inside the machine, and more importantly, to make sure the machine is running fine.
Lastly, once the part is built, manufacturers have to make sure that it is built to the correct specifications. That’s exactly where build validation comes into play and the challenge here is the cost and limitation on quality control, especially for complex structures.
So, these challenges result in a solution that is based on three pillars. What are they?
Those pillars are security, consistency and insights.
Security consists in protectingthe IP of the design. In 2017, we have been granted a patent in the EU and in the US over our process and security. Technically speaking, we have an encryption system where we are able to encrypt the design (.STL, .SLI, .CLI and .3MF file formats) as well as manufacturing process instructions: we are able to send the file directly into the machine, to decide of the way it should be built, to ensure the production of the part with a given material and only on a specific machine or even to order a specific number of prints.

Our second pillar is consistency. We are able to lock down the part on the platform so that no other part can be built on the same platform. Also, we have a total control on the position and build count of the part on that platform. Once the build has started on a machine, a build report is automatically generated and is sent back to the design owner. The good news is that this report is generated automatically, not manually and it provides all the details related to the manufacturing.

And Insights. This part comes into play at the end of the build process. Once the part is built, the next step consists in validating its quality. We are able to ensure the quality and output while collecting the build data of the machine and analyzing them. Indeed, we have developed a tool that can conduct some statistics and analytics in order to determine potential anomalies.
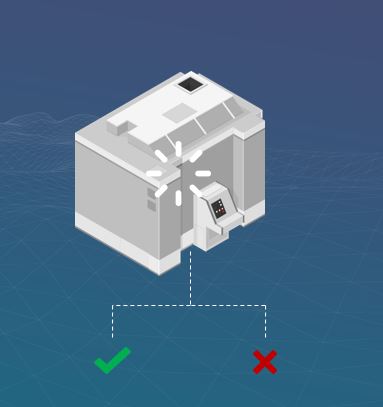
Thanks to the way we apply these pillars, we enable AM companies to save cost and time in production.
Intellectual property remains one of the two main issues tackled at the regulation level. According to you, what concerns does it raise?
IP can be applied in different scenarios: the first one being the design. In the aerospace industry, engineers have spent many years to design a specific part as well as locking down how the part should be built in order to be qualified to fly, therefore, protecting that design is of paramount importance.
Furthermore, IP over how the part should be built is also important because each design and material has its own set of design rules. Therefore, protect that is also very important.
The second scenario is the manufacturing process. As mentioned earlier, both design and the process parameters as well as all other manufacturing instructions should be coupled together on an encrypted format so that the final outcome of the build is successful and qualified.
Is the application process of your software differ from one target (designers) to another (services bureaus)?
For each target, it is similar but we have developed our software in a modular way. Hence, we can easily customize it to fit the needs of each target.
Is there any advice you would like to give to professionals who do not know what to do about the challenges of AM?
One of the main challenges that AM in general is facing is not only about security but above all about manufacturability and lastly, build validation. As well as developing our existing end-to-end additive manufacturing digital rights management solution, we are focused on building artificial intelligence (AI) engines to overcome additive manufacturing adoption challenges surrounding design, manufacturing and build validation. Having launched our first product and de-risked the technology we have identified key targets and are now working closely with key industry stakeholders.
Your last word?
At GROW we are committed to develop cutting edge technology to enable secure distributed additive manufacturing as well as ensuring quality and consistency over each build.
For further information about 3D Printing, follow us on our social networks and subscribe to our newsletter!
Would you like to be featured in the next issue of our digital magazine? Send us an email at contact@3dadept.com
//pagead2.googlesyndication.com/pagead/js/adsbygoogle.js (adsbygoogle = window.adsbygoogle || []).push({});