The Naddcon research and development centre has recently integrated an ExAM 255 3D printer from AIM3D into Siemens’ NX design software.
The NX tool contains extensive CAD, CAM and CAE solutions, as already used for the conventional manufacturing of components in the machining industry. This integration of NX is just one of many options though in the open machine concept of AIM3D’s multi-material 3D printers.
So, how did they proceed and most importantly, why?
Here is why.
Naddcon opens up a new possibility for the operation of 3D printers and the generation of G-code. The team ambitions to map a 3D printing process as a continuous digital process chain from the component design to the production and post-processing.
The bridge between the machine firmware of AIM3D and the CAD/CAM environment of Siemens NX integrates the 3D printer as a CAM processing machine. With CAD, CAM and CAE approaches provided by NX, the 3D components can be optimised in terms of bionics, free-form surfaces, selective densities (variable filling strategies) and weight reductions (for example, grid structures).
The fibres can also be laid down in an optimised manner with respect to the force flow, which defines the stiffness or elasticity and the mechanical load capacity. In addition, a database system and powerful simulation models are available. This means that the entire 3D printing process from the design to the production can be better controlled, components can be optimally designed and at the same time a very high reproducibility can be achieved. In general, it can be said that NX enables an exact machine simulation. More precisely, this means that traversing speeds, extruder performance and temperatures can be controlled with pinpoint accuracy depending on the component geometry.
A key example of opportunity that is now possible: free-form surface machining in 3D CEM printing
A keyword in free-form surface machining is Multi-Axis Deposition. Originally developed for laser beam build-up welding by DMG Mori, the tool has since been extended to FDM/FFF. In fused deposition modelling, strands of material are deposited onto a surface. These strands are obtained by melting a polymer and continuously extruding it through a nozzle, followed by the material hardening due to cooling at the desired position of the working plane. The build-up of a component is usually done by repeatedly creating one working plane at a time, line by line, and then moving the working plane upwards in a ‘stacking’ manner so that a shape is created layer by layer. NX allows for the generation of toolpaths along curved surfaces. This way, true 3D paths, that create planes independently, can be generated. Using this technology in process development can eliminate the staircase effect typical of AM processes. The result is a true 3D contour of a solid body.
Here is how.
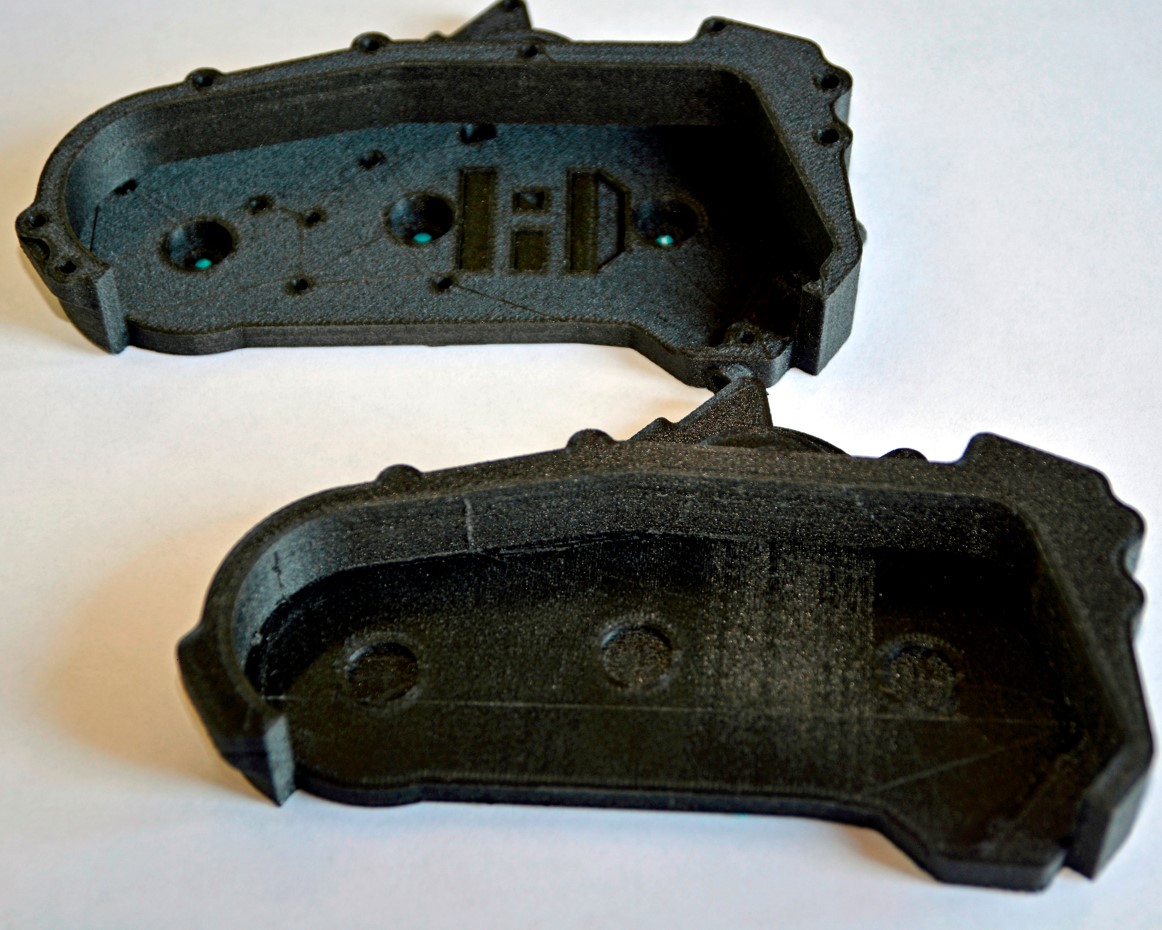
Sebastian Kallenberg from Naddcon designed the required steps for the integration based on a standardised component made of PA6 GF30 (demonstrator), the design of which was to be optimised using NX.
The first step was to build a kinematic model of the 3D printer by integrating the CAD model of the ExAM 255 into NX, as well as defining the kinematic axes and determining the machine zero point. The kinematic model enables a machine simulation of the tool paths before the actual production process takes place.
The next step was the generation of the tool path for the extruder of the AM system. This involves generating trajectories based on machining operations and the component geometry.
The third step was the machine simulation of the ExAM 255, that is, the simulation of the tool path with the associated axis movements of the machine model. The application of the material as well as potential machine collisions can also be simulated. The main aspect here is the programming of a post-processor to translate the NX tool paths into a numerical G-code that the 3D printer can interpret.
A G-code consists of path conditions (G-word) and additional functions (M-word), each of which is assigned either a movement or an action. The combination of these commands allows the 3D printer to understand the pattern it must follow to produce the part. A G-code is a programming language used to program numerically controlled machine tools.
In 3D printing, it is usually generated automatically by the slicer software when the design is converted to an STL file. Post-processor programming allows for machine-specific adjustments for an improved process control. When using NX, however, an STL format is no longer necessary, as the process makes use of solids that are either directly generated within NX or can be imported from a different CAD system.
Remember, you can post job opportunities in the AM Industry on 3D ADEPT Media or look for a job via our job board. Make sure to follow us on our social networks and subscribe to our weekly newsletter : Facebook, Twitter, LinkedIn & Instagram ! If you want to be featured in the next issue of our digital magazine or if you hear a story that needs to be heard, make sure you send it to contact@3dadept.com